Lubrication solutions with ERIKS and ROCOL®
Performance you can trust for the Food & Beverage Industry
Offering uncomplicated solutions to everyday problems
With lubrication and maintenance solutions tailored to the bakery industry's needs, ROCOL® can ensure that customers' equipment is cared for, and production lines remain operational.
There are many challenges of running machinery in any food manufacturing or bakery environment. Choosing the right lubricants is critical in ensuring the longevity and efficiency of your machinery.
In the food industry, it’s equally important to understand the specific lubricant requirements of each operational and maintenance process in your factory. Here we highlight five problems with one simple solution – ROCOL® Lubricants.
- Risk of Contamination
- High Temperatures
- Low Tempertatures
- Water Resistance
- Process Control
With so many products to choose from, so many food and hygiene regulations to consider – and so much at stake if you get it wrong – don’t take any risks.
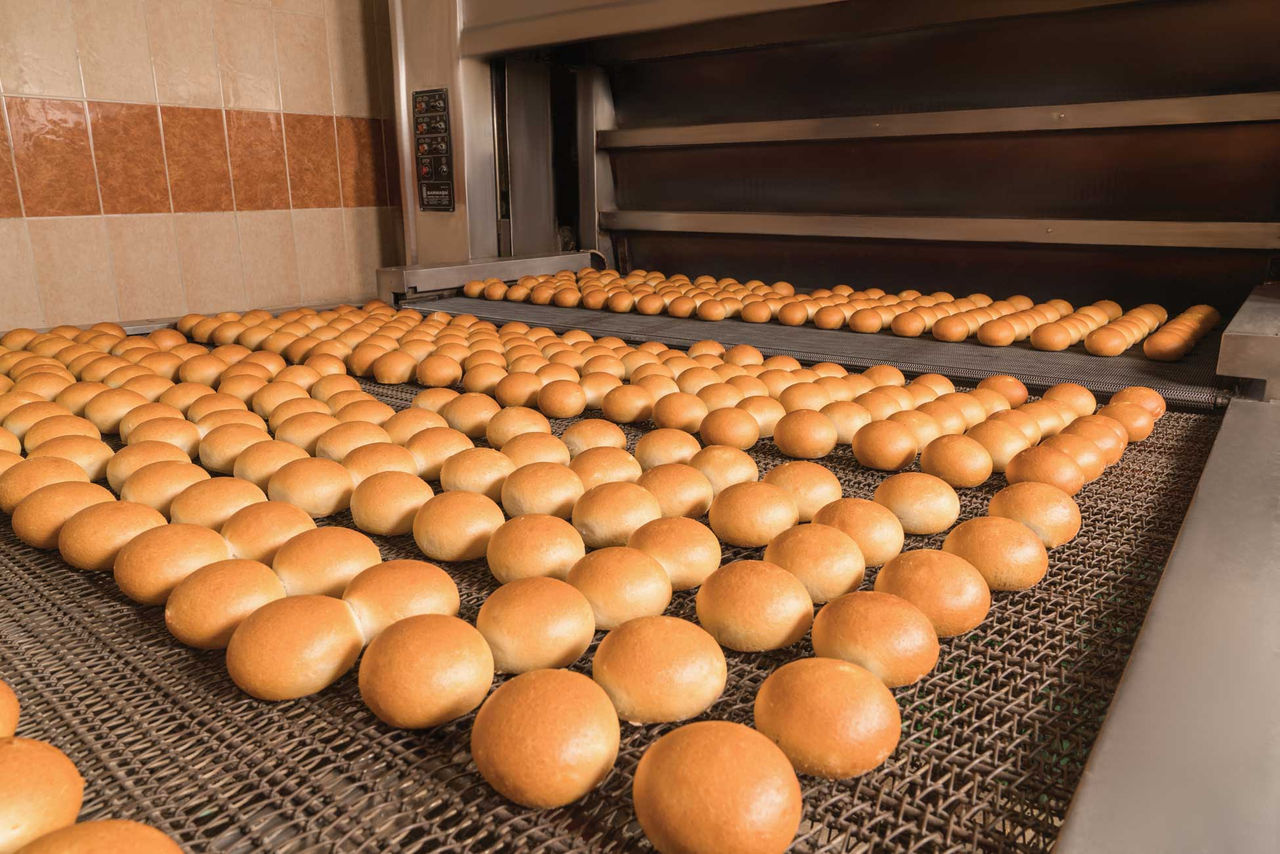
Rocol® Bakery Solutions
Let ERIKS and Rocol® help you select the best product for your needs, and keep your bakery running smoothly.
With so many products on the market, it can be tough to choose which is the right solution to your problem.
Download your copy of ROCOL® Bakery Brochure which will provide all the information you need to assist in your manufacturing decisions.
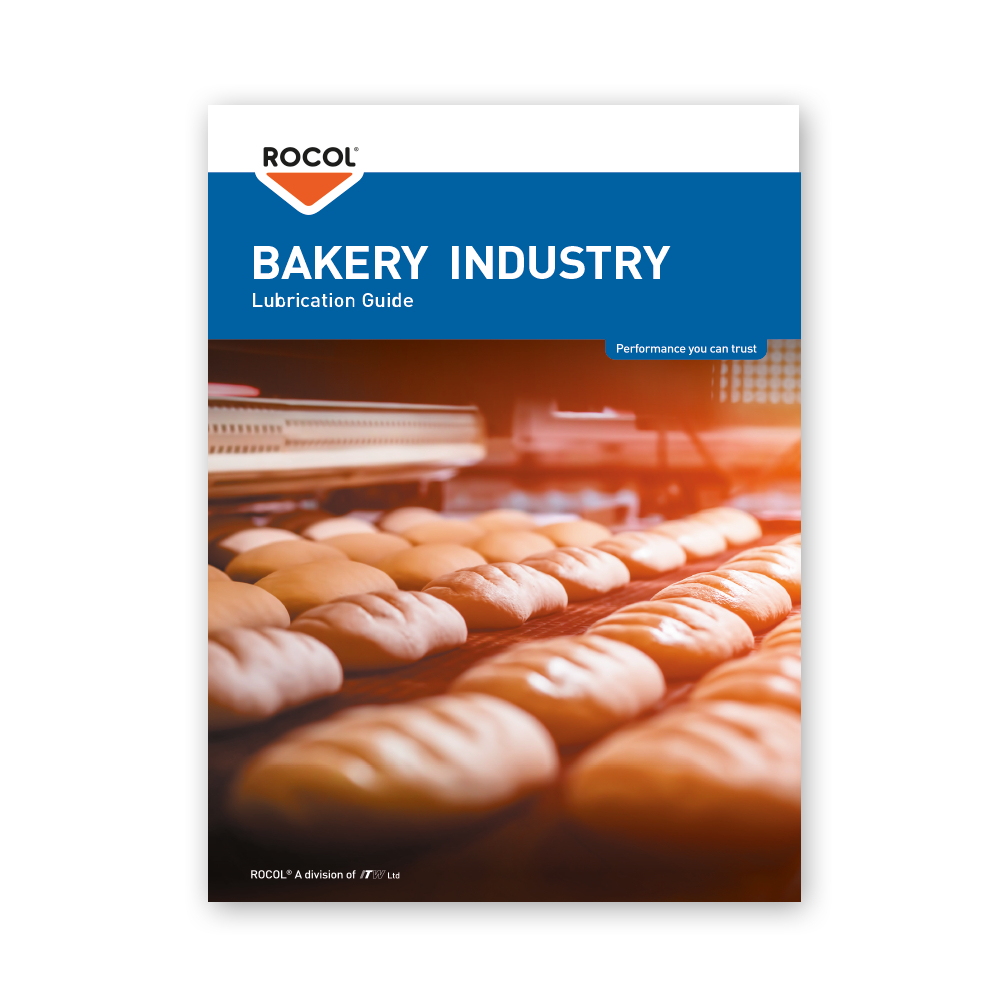
Five common problems in the Bakery
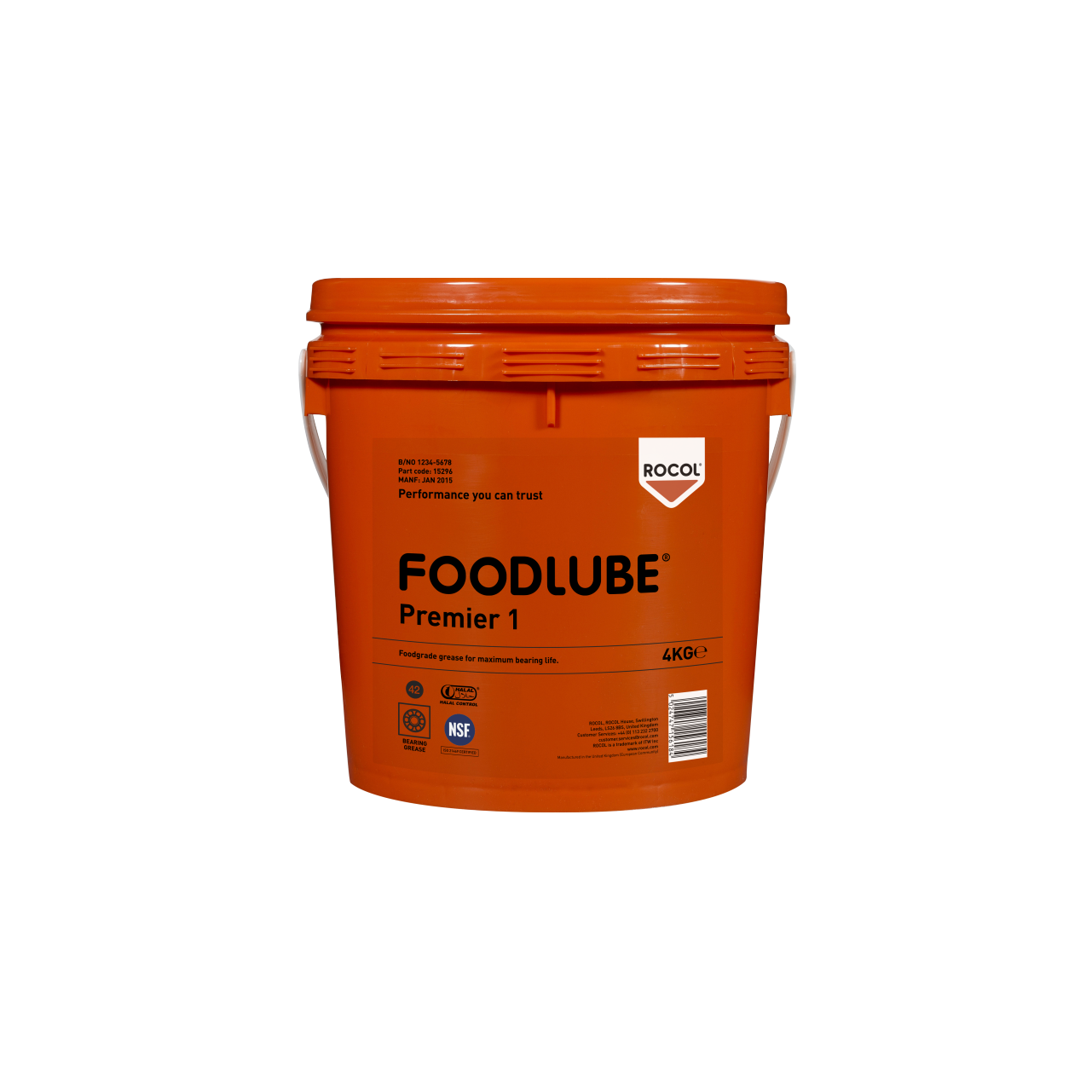
1. Risk of Contamination
Foreign bodies are a common issue that may arise in various stages of food production, including mixing, moulding, chilling, rollers, slicers, baggers, and ovens that require lubrication. These foreign bodies can cause serious problems, leading to product contamination and potential harm to consumers.
To solve this problem, ROCOL has developed high-quality lubricants that are specially designed to prevent foreign bodies from becoming an issue during the food production process. One being ROCOL® FOODLUBE Premier 1 - a high-performance EP grease, designed for enhanced lubrication to significantly extend bearing life.
A non-toxic lubricant containing PTFE, it provides effective lubrication and protection of ball, roller, and plain bearings, slides, and bushes that are used in food, pharmaceutical, and other clean environments.
2. Process Control
Maintaining a safe environment is of utmost importance in any industrial facility, and this is typically achieved through rigorous internal and external audits, as well as the implementation of Hazard Analysis and Critical Control Points (HACCP) procedures. However, these procedures can be quite demanding, and require significant resources to ensure compliance. Unfortunately, this can often mean that resources that could be used for other purposes, such as plant lubrication, are diverted to these safety efforts.
ROCOL® Foodlube Spray Grease is a food grade, multi-purpose EP grease, fortified with PTFE in aerosol spray. With the demands of internal and external audits and HACCP procedures being resource-intensive, it is important to prioritize safety above all else and this is the perfect lubrication for such purpose.
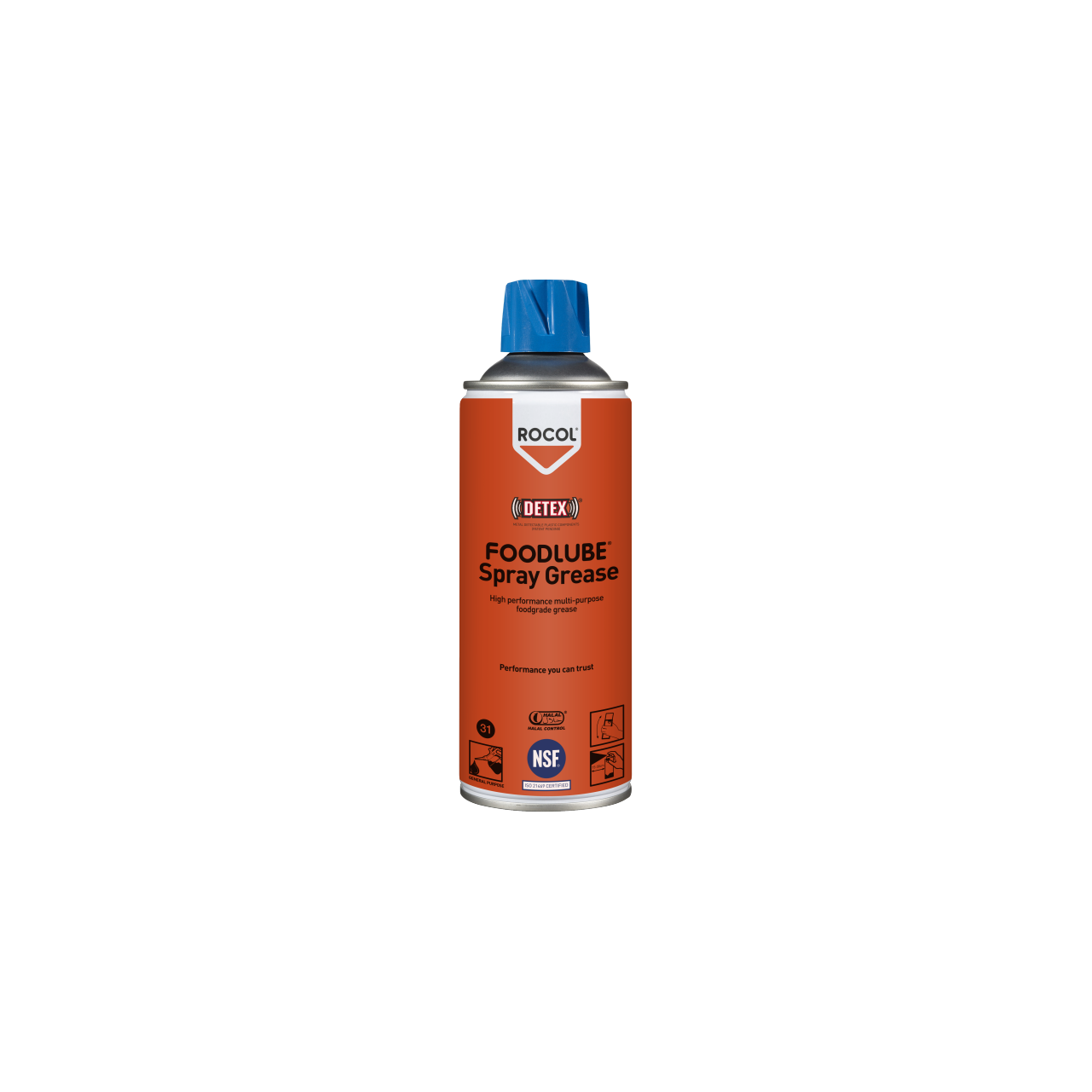
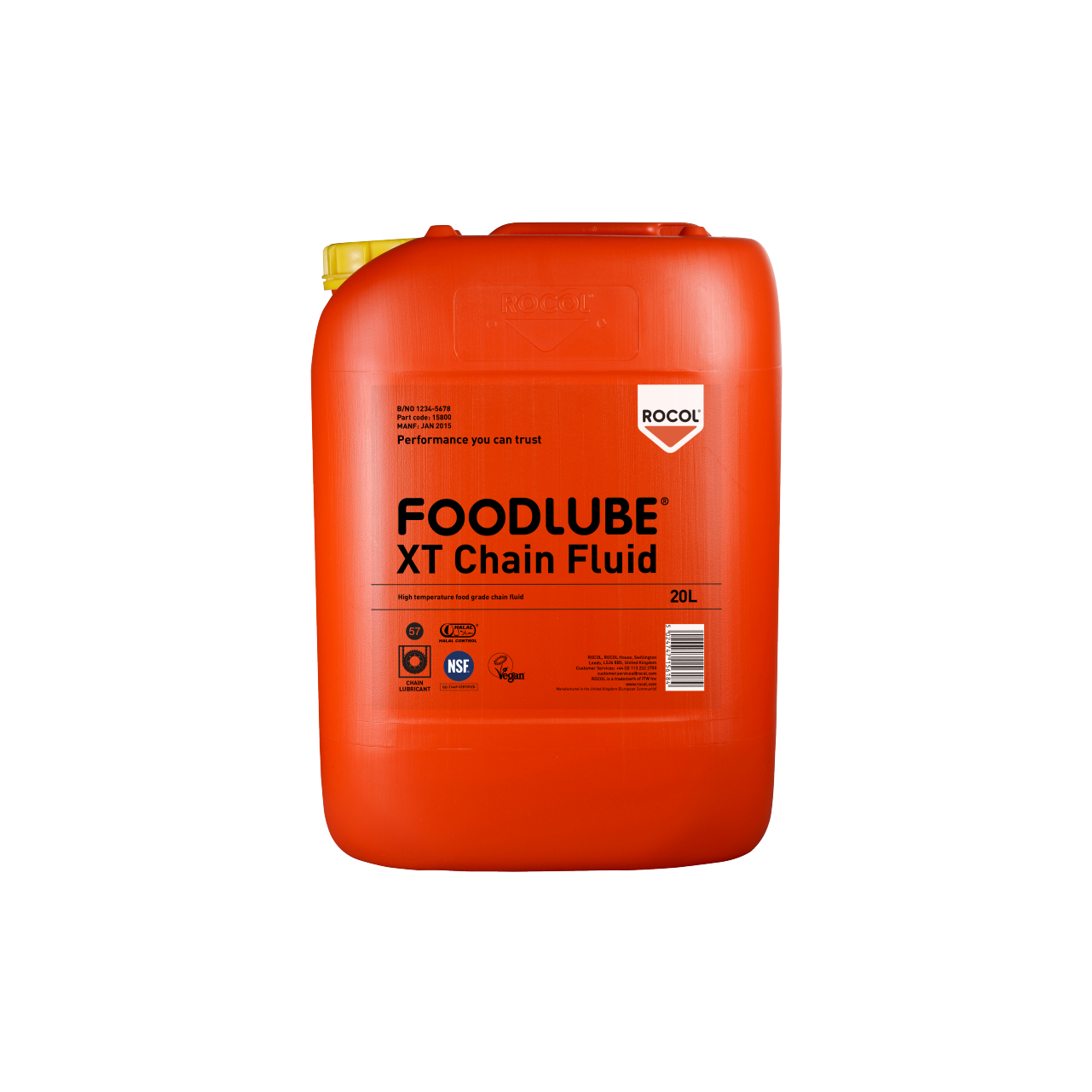
3. High Temperatures
Bakeries are famous for their delicious baked goods, ranging from bread to cakes and other sweet treats. However, behind the scenes, there are a lot of challenges faced by bakers that can affect the quality of their products. One such challenge is the extreme temperature that bakery ovens operate at, which can reach up to 600°C. This high temperature can cause various problems such as excessive solids buildup, chain climb, screeching, and contamination of the baked goods.
To avoid these issues, it is essential to maintain the correct lubrication solution for your bakery oven.
Formulated from a combination of synthetic esters and a special antioxidant package, FOODLUBE XT Chain Fluid ensures the highest performance in terms of thermal stability, low evaporation loss and minimal deposit formation.
Effective for chains operating in food, pharmaceutical and other clean environments, its anti-oxidant package reduces deposit and varnish formation, and its low evaporation properties increase re-lubrication intervals.
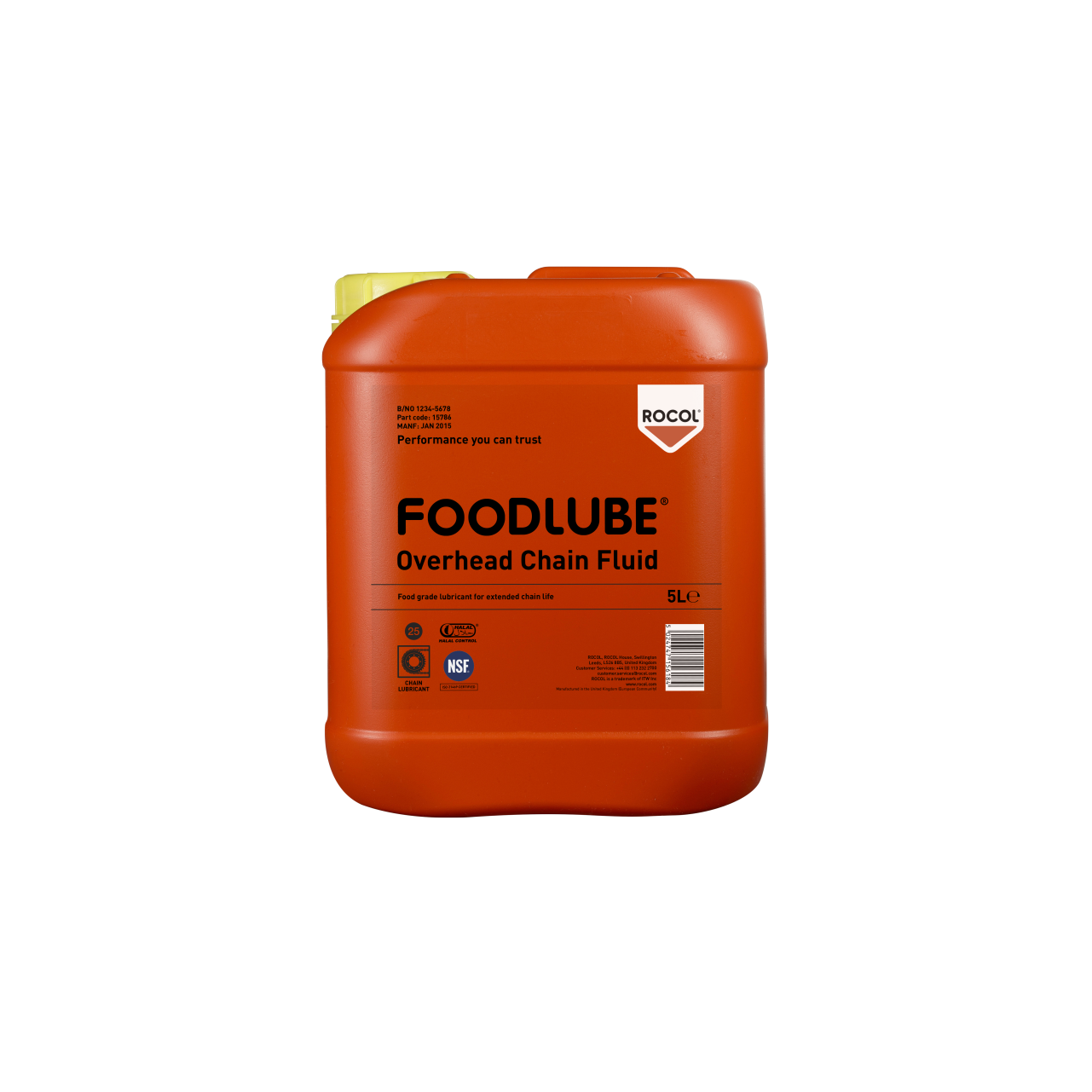
4. Low Temperatures
Chiller drive trains operating at extremely low temperatures such as -50°C can be prone to chatter and shudder. This can lead to drag and a consequent increase in power consumption, which can be a cause for concern.
Proper maintenance and regular inspections can also help prevent these problems from occurring. Finally, it is important to work with experienced professionals with the correct lubrication options, to ensure that your chiller system is operating effectively and efficiently.
FOODLUBE® OVERHEAD CHAIN Fluid is a water-resistant and non-toxic chain lubricant, expertly formulated for optimal performance in environments where dripping lubricants are not acceptable. This is particularly important in abattoirs and processing plants, where maintaining a clean working environment is paramount.
It offers excellent water wash off resistance and corrosion protection, making it ideal for use in clean environments such as the food and pharmaceutical industries.
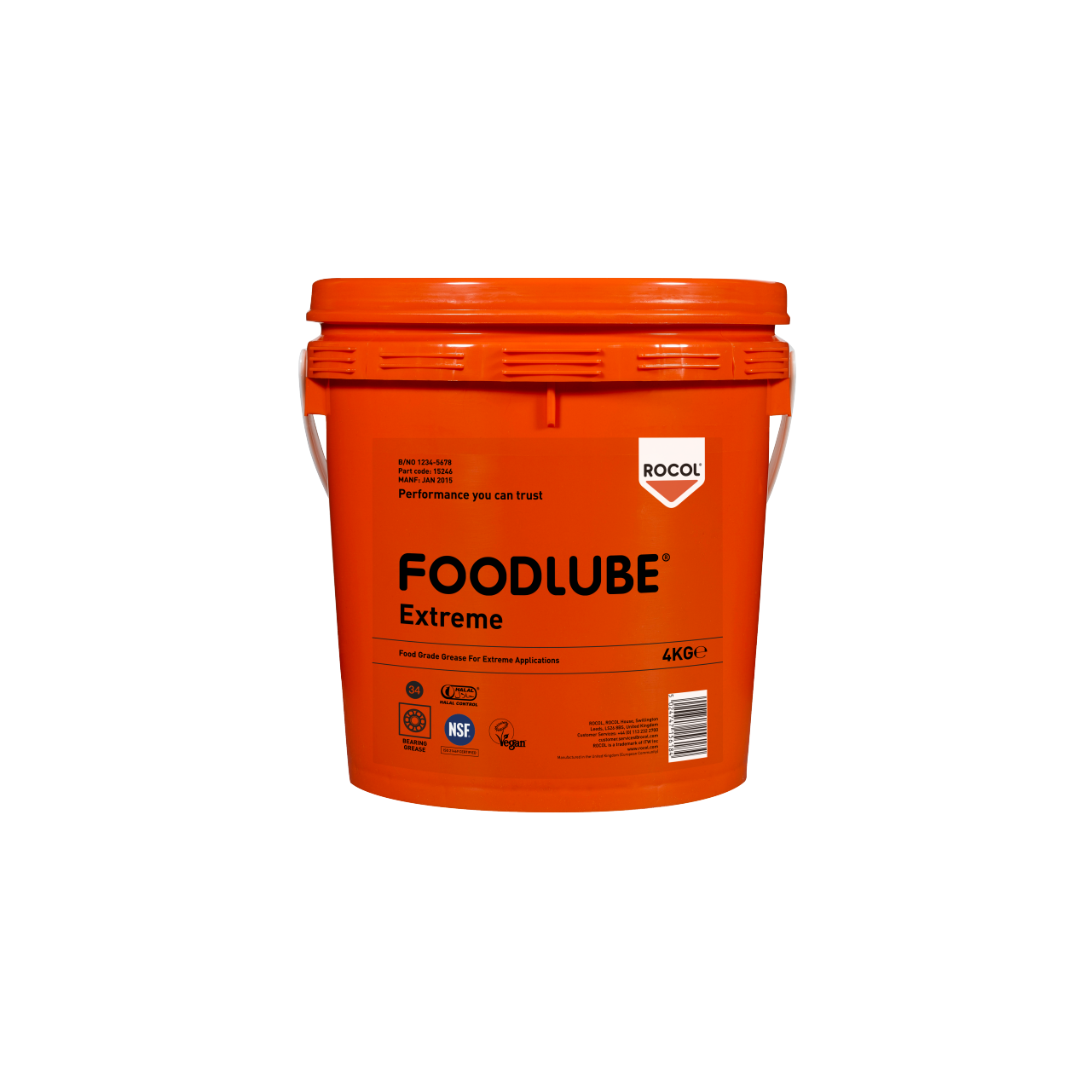
5. Water Resistant
Cleaning is an essential aspect of maintaining hygiene and safety in any food processing facility. Regular wash downs are crucial to prevent contamination and maintain high-quality standards. In particular, areas around mixers, dividers, and moulders require strict cleaning regimes to prevent the build-up of harmful bacteria and other contaminants.
To protect against lubricant deterioration from microbial activity, FOODLUBE Extreme contains an anti-microbial compound, which along with the anti-oxidant additive package greatly extends the life of the grease – reducing re-lubrication frequency and total cost of ownership.
The DETEX technology metal detectable cap on grease cartridge reduces risk of plastic contamination, and FOODLUBE Extreme is NSF H1, ISO 21469 and Halal certified for full audit compliance and peace of mind.
Case Study: Hovis and DETEX®
Find out how Rocol® helped one the leading manufacturer of bread and bakery products in the UK.
A number of DETEX® metal and X-ray detectable caps and actuators were sent through the production process, to test in-line metal detection equipment.
Download your copy of the Rocol® DETEX® Case Study for more information on how reducing the risk of plastic contamination-related recalls.
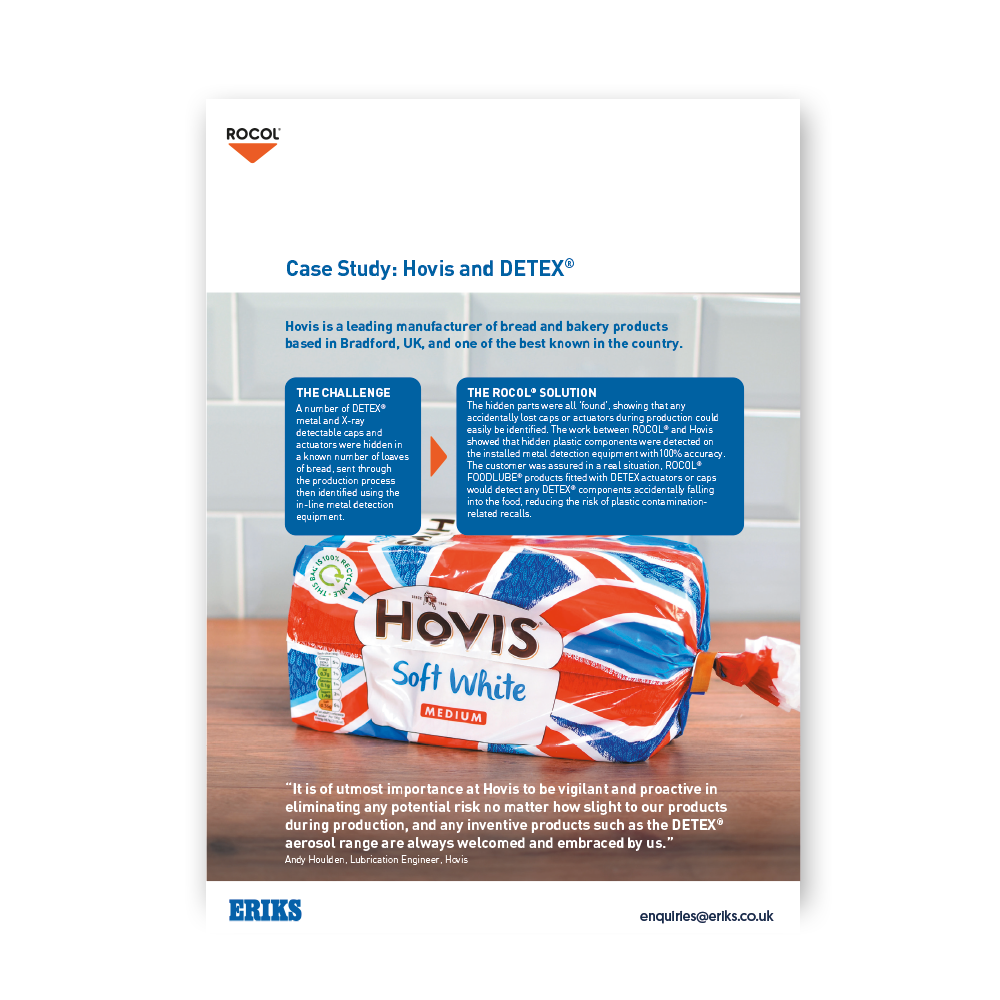
Choosing bakery lubricants? Use your loaf...
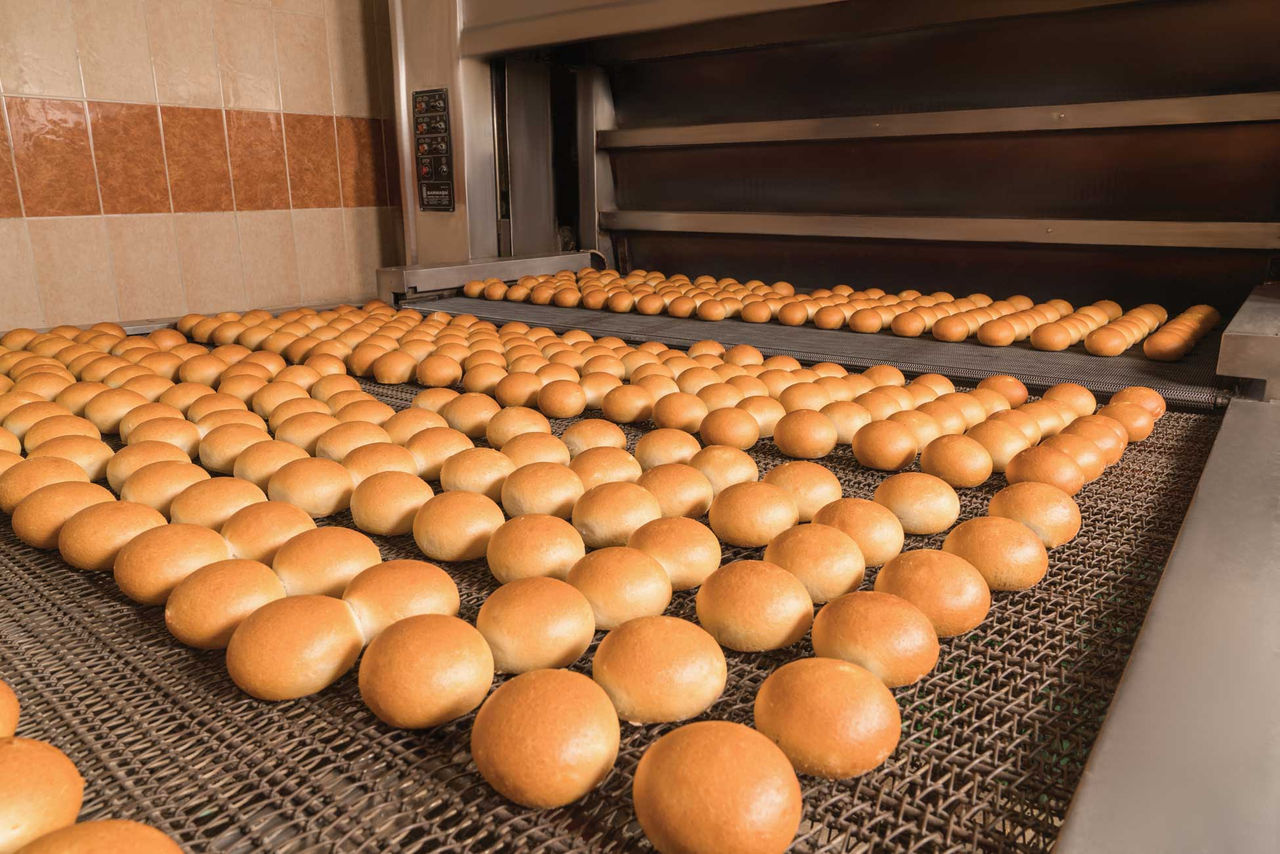
Like many food production sites, a bakery is a challenging environment for processing machinery, and for the lubricants needed to keep it running.
High-speed operating and regular washdowns can take their toll, and strict hygiene and food safety regulations are always there to catch out the unprepared.
A regular maintenance schedule is the first step to reducing unplanned downtime and staying on the right side of the regulations. Careful lubricant choice does the rest.
How can ROCOL® FOODLUBE help you?
Our comprehensive range of products is designed to lubricate and protect operating systems in the food and clean industries.
Whatever the type of drive or conveyor chain etc. in use, we can provide a lubricant to ensure trouble free operation.
Why not take a moment to look at the FOODLUBE brochure and see how we can help solve every day problems simply by using the right lubrication solution.
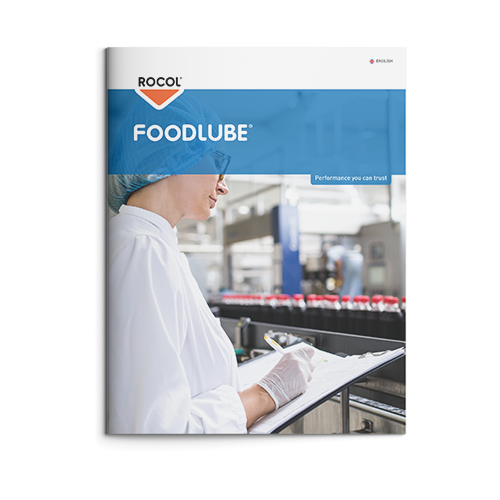
ERIKS Lubrication Essentials Guide
If you can't decide which lubricant is best for you, why not take a look at our Lubrication Guide? Which lubricant is used for Hygienic Environments? What oil should I be using for Gearboxes or Corrosion Products? Our range of carefully curated lubrication solutions will cover 80% of all your lubrication needs. Download your Lubrication Essentials Guide today:
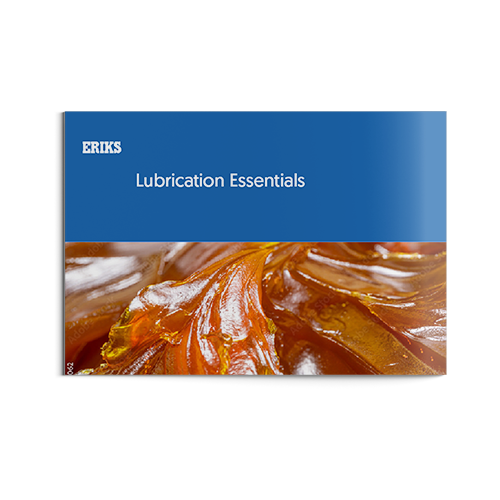
Solutions for the food industry
About the food industry
Our blogs on food safety
Consult our Food Experts
Top Tips Whitepaper
How to Contact ERIKS
Get in Touch
Looking for a custom Product quote? Need an answer to a Technical question? Looking for Careers/HR support? Want to work with us? Interested in our Digital Trading solutions? Have a finance question? Send us your enquiry and a member of the ERIKS team will be with you quickly.
How are we doing?
We strive to deliver exceptional quality service and products. As part of this goal, we encourage customers to submit feedback on their experiences so we can resolve any issues and concerns.
Call us or find your local Branch
At ERIKS we strive to deliver the best quality service and products. As part of this goal we encourage customers to submit feedback on their experiences so we can resolve any issues and concerns.
Call us: +441215086000
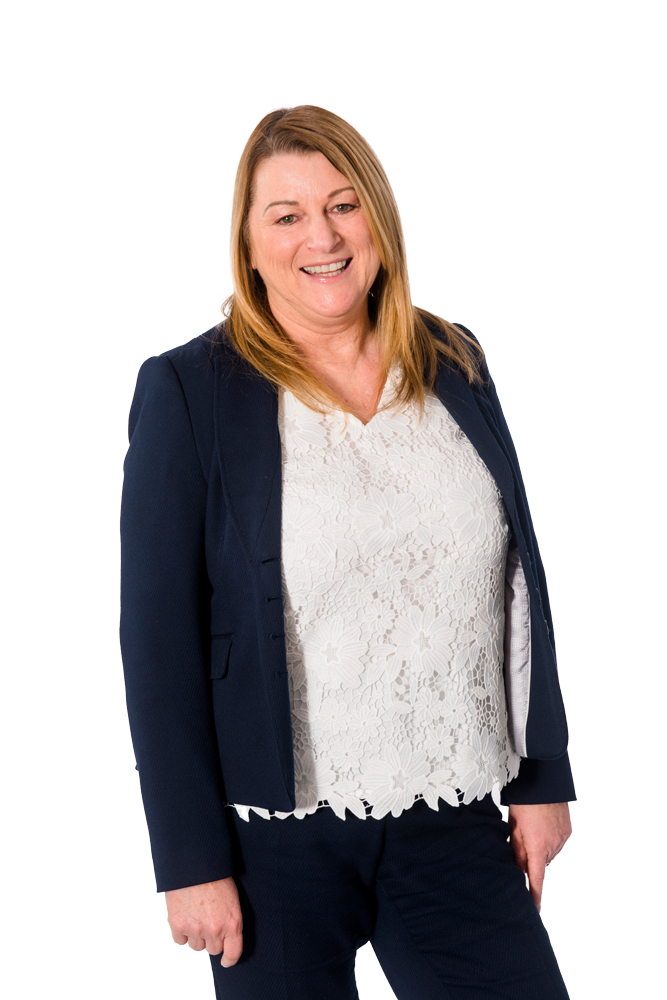