In this article
FrieslandCampina - Efficient tool carts
Have you ever gone into the factory for a maintenance job and then forgotten that crucial spanner, did you have to go back, with all the delays (and costs) that entails. Have you accidentally left a pair of pliers behind afterwards and had to return and search for them? This no longer happens at FrieslandCampina in Veghel thanks to well-prepared and carefully equipped tool carts. The result: satisfied mechanics, no loss of time and savings of around 170,000 euros.
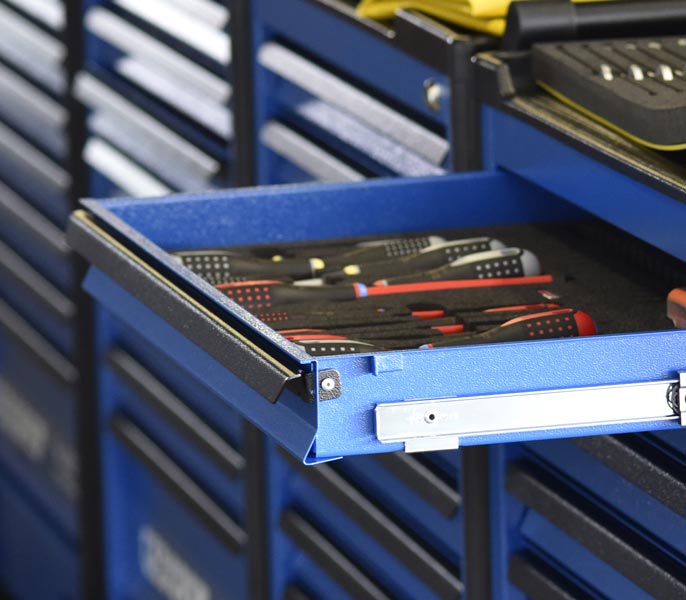
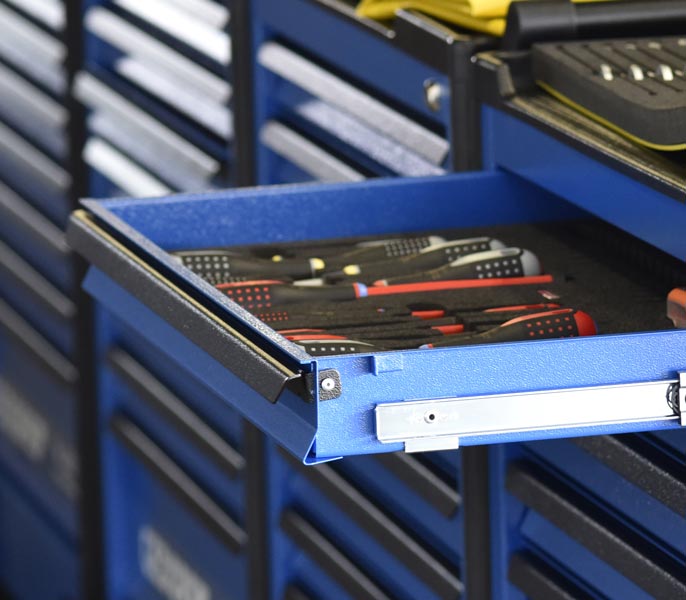
Structural time savings through less misshaping
Royal FrieslandCampina is one of the world's largest dairy companies, with 23,800 employees, branches in 34 countries and an annual turnover of almost EUR 12 billion. The company is a cooperative, which means that the more than 12,000 dairy farms in the Netherlands, Germany and Belgium that supply the company are controlled by the cooperative. In the Veghel branch of the international, lactose and proteins, among other things, are extracted from raw milk for the food industry. Every day, the 400 employees see thirty large trucks entering the site, which together deliver one million litres of milk.
Quality improvement programme
In the first production hall in Veghel, there are four man-high centrifuges. Here, the cream is extracted from the milk, after which the remainder is further processed to extract everything that can be used from it. It is the start of a production process that must, of course, continue without hitches and delays. This was also one of the reasons why the management set up a quality improvement programme called WCOM. Within the programme, projects are started at all the company's sites, with which concrete improvements (e.g. in the field of efficiency, quality and safety) can be implemented in fourteen to fifteen weeks.
Between those man-sized centrifuges is a blue tool cart. A beautiful, sleek cart with eight drawers and castors. The cart contains all the tools the mechanics need for maintenance. General operator Kevin Emons and WCOM quality manager Harrie van Herpen look at it with satisfaction. The carts are the outcome of such a WCOM project. And they are literally a godsend too, the two say. "The mechanics always have the right tools with them. As a result, they work better and faster and we have less downtime in our production process."
Back to the workshop
Let's go back to the beginning of 2018. Harrie van Herpen was asked to take a look at tool use in the production location. Because what was the case? In the past, every mechanic had his own tool trolley, containing his own set of tools based on his own needs and his favourite brands. In that way, he almost always took too much with him, or during the day he often needed that one spanner he didn't have with him. Kevin Emons: "Then he would have to put down his work, walk back to the workshop and return via the cleaning line. All in all, this resulted in a lot of lost time. What's more, not all the tools were taken back afterwards. All of which adds up to extra costs.
The question to Harrie van Herpen: can't that be done better? He discovered that it could indeed be much better. "In various brainstorming sessions, we quickly came up with a solution: standardised tool carts, which stay in the department, containing all the necessary tools in a well-organised manner at fixed positions in foam or hard plastic."
The brainstorming sessions were organised by and with ERIKS, Friesland Campina's preferred supplier for many years. ERIKS was brought in at the early stages to help think things through and - ultimately - to supply both the carts and the tools. Application Engineer Tools Remco Dijkmann and Account Manager Jack Peek were involved in the whole process on behalf of ERIKS.
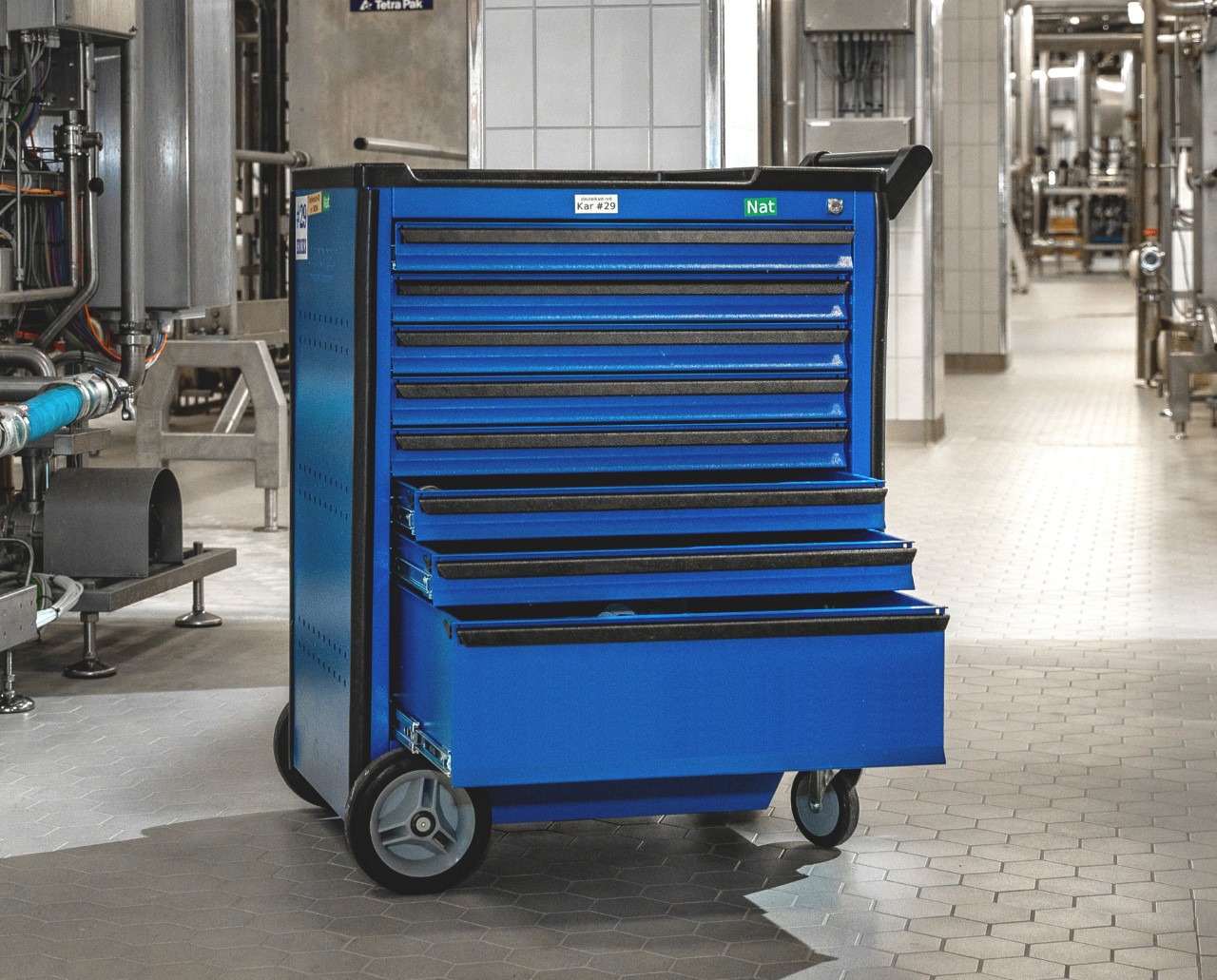
What tools?
That was step 1: choosing the cart. But how and which tools should the carts contain? That was one of the most fun parts, according to Van Herpen. "ERIKS organised a so-called tool meeting here, where all the required tools were displayed on tables. Then we asked the mechanics: which tools do you use and what do you need? And made it clear: we can't fit everything in the carts, so make a choice. We really let the mechanics choose and decide for themselves. That was good for support and for the acceptance of the new working method.
The outcome of this session: the number of different tools was reduced by fifty per cent. And so the fifty carts required - for as many departments - could be filled with a total of 211 tools. This led to an initial procurement reduction, because ERIKS was also able to significantly reduce the number of different tool brands.
Each tool now has its own place in the various drawers, enclosed in inlays that ERIKS has developed and manufactured especially for the carts. The great advantage of this is that when a drawer is opened it is immediately clear whether all the tools are present. That makes inspection easier and safer. And, not unimportantly, the inlays mean that more tools fit in the cart.
FrieslandCampina works in Veghel with three different safety zones: Low Care (Green Zone), Medium Care (Yellow Zone) and High Care (Red Zone). What is unique is that the content of the carts is adapted to the different zones by ERIKS. This applies to the tools in the drawers, but also to the inlays. Because the Red Zone is where we work with the highest hygiene standards, ERIKS had special plastic inlays developed for this zone according to EC1935/2004, which are easier to clean and keep clean than the foam inlays in the carts for the Green and Yellow Zone. By the way, says Van Herpen, the tool sets in the different carts are 95 per cent the same.
New work implementation
And then the final step: putting the new work implementation on paper and letting the people work with it. Van Herpen: "We no longer wanted everyone to just take their own cart. So each zone in the production location has its own numbered cart. When a mechanic starts work at his place, he gets the key to the cart and signs for the completeness of its contents. When he has finished, he signs off again. When he has finished, he signs off again, thereby letting it be known that he is also leaving the cart behind in its entirety. If his colleague after him sees that something is missing, it is always possible to find out who used the trolley. That also ensures that people work more carefully."
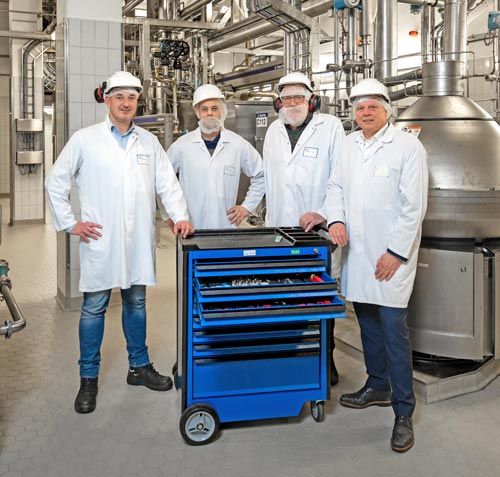
Order less
Van Herpen and Emons managed to complete the project within the planned fifteen weeks. And with success: the mechanics are satisfied and the quality of cleanliness and speed has improved. "Moreover, we have noticed that far fewer tools go missing. The purchasing department is ordering less than it used to."
The fifty carts and the accompanying tools required a substantial investment, but ultimately yielded good returns. Van Herpen's calculations show that FrieslandCampina will save around 170,000 euros as a result of the project. The biggest saving comes from the fact that the carts and tools no longer need to be moved, checked and cleaned each time they are used, as they remain in the department. That used to take at least half an hour per technician per day.
"And that amounts to a total of 250 working days per year, or more than €160,000. And the work doesn't have to be stopped as often because, for example, a spanner needs to be fetched. The mechanic then has to go through the cleaning line again. That also takes a lot of time, and therefore money.
Also at other locations
The management is happy with the results, says Van Herpen. "Not only because of the savings and the improved way of working, but also because of the satisfied shop floor." And so the question is: will this way of working also be implemented at other branches of the dairy giant? "It has already been picked up at other branches," says Van Herpen. "But I can imagine that this success leaves you wanting more. I have presented the project and its results to the MT, which was very pleased. The central office in Amersfoort must now give it a whirl."
Van Herpen himself is happy and satisfied with ERIKS' contribution and work. "They have a lot of knowledge and expertise, and think along well and constructively. Of course, they are not preffered supplier for nothing. Nothing was too crazy for Remco and Jack. I think that the thinking and cooperation of ERIKS has played a major role in the success of the project."
Deliver more than requested
Remco Dijkmann and Jack Peek also look back with a good feeling. "We are proud to work as a partner with FrieslandCampina on a good result. It's nice to hear and see that the customers and mechanics are so satisfied. These are, of course, compliments we are pleased to hear," says Jack. "And it was great to work together. We tried to deliver more than was asked of us. And I think we succeeded. In terms of ease of ordering, reduced stock levels, fewer misguided orders and finding the tools more quickly, we've been able to make some great strides for FrieslandCampina."
Both Jack and Remco see opportunities in other companies for the concept. "It works well, that has now been proven. I think there are enough other customers and companies that could benefit from such a system. I would love to show what the possibilities are."
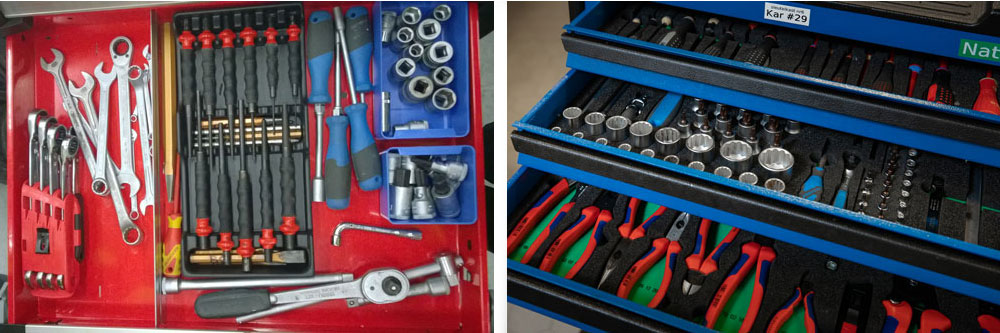
Left: old situation, tool trolley contents
Right: new situation, numbered trolley with standard contents
For more information on Tool solutions and to get in touch with one of our ERIKS Industrial MRO and Safety Specialists, please contact your local ERIKS Service Centre, who will be happy to discuss your options.
#FrieslandCampina #ERIKS #LetsMakeIndustryWorkBetter #Food #Tools #CostSavings
Want to know more about our Tool Control concept?
Solutions for the food industry
About the food industry
Our blogs on food safety
Consult our Food Experts
Top Tips Whitepaper
ERIKS will handle this - let us know how we can help...
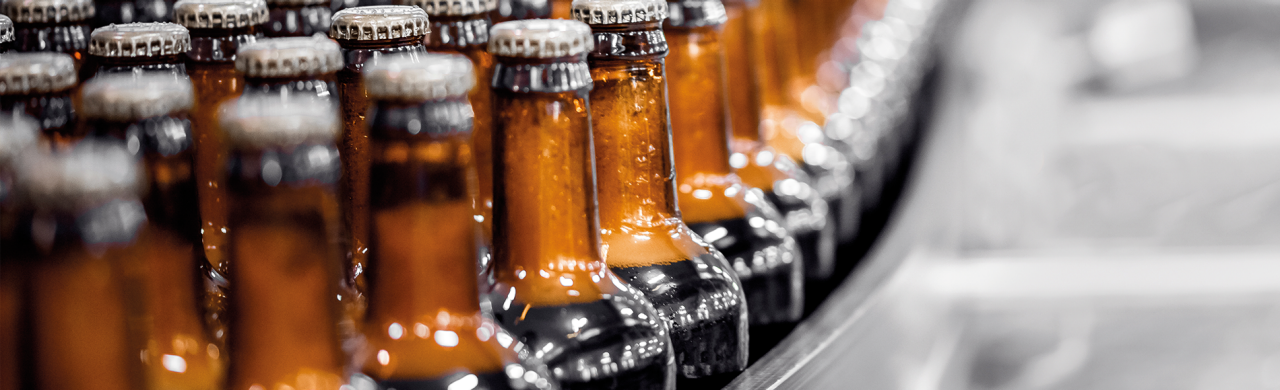