In this article
Food industry needs a wake-up call
Food safety is of enormous importance in the food processing industry. End users must be able to rely on it blindly. Every day, manufacturers of both food products and machines have to deal with a maze of rules, requirements and legislation. Many manufacturers are therefore increasingly leaning on the knowledge of their suppliers to deal with this complex subject. Is this fair?
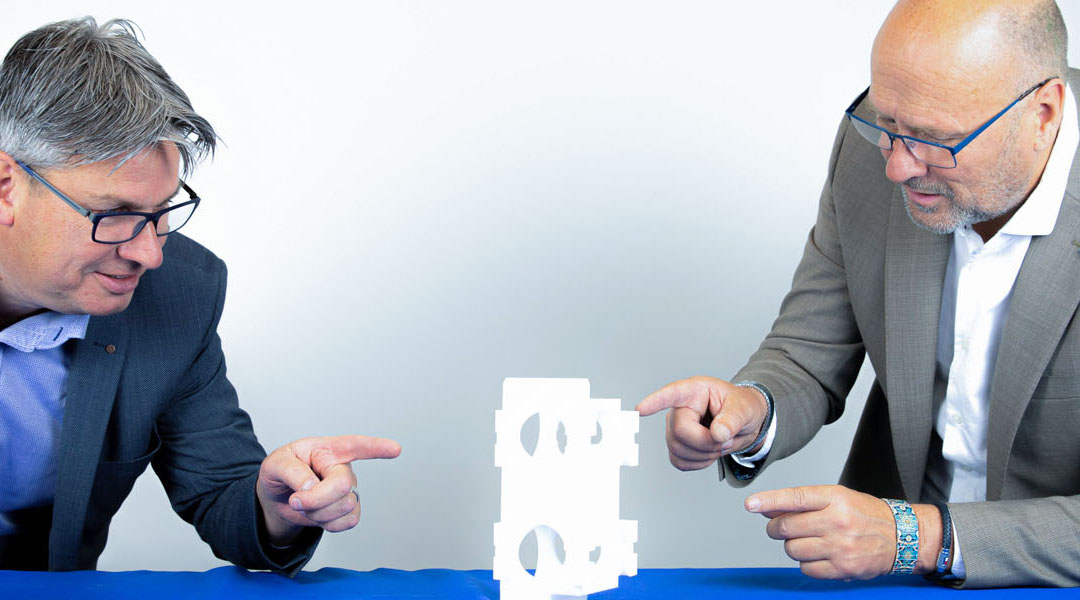
FACT! Traceability is hard to implement. ERIKS specialists Berry Kragt and Edwin van Nieuwenhoven - champions of food safety - see many companies struggling with this issue. What do they have to deal with when it comes to traceability conform EC1935/2004 standards? Read their story below.
We have lost count on the number of times we get asked "Where does this material come from?" or "Show me your certificate!". It’s similar to meat: the steak on your plate must be traceable to a specific cow. Where did the cow reside? In what pasture? And with which farmer? Traceability goes a long way, and is just as relevant in 'plastics land'.
As far as plastics are concerned, products or raw materials must be traceable. This is carried out according to agreed guidelines and only possible when the entire chain complies. EC1935/2004 is not optional. It is legislation.
When solutions are made with non-traceable materials, Food Grade guarantees are not a 100%. That’s also a big part of traceability: 'hedging' against major problems or liability. Contaminated goods may result in a claim. Traceability is vital to find out whether the source was Food Grade or not.
We occasionally worry about the unfamiliarity with EC1935/2004 legislation, even among big players from whom you would not expect this lack of knowledge. In that respect, the food industry really needs a wake-up call.
ERIKS: fully certified
ERIKS holds the ISO 22000-2018 certificate. This is unique, as we are not a food processing company. The certificate guarantees GMP EC2023/2006 requirements.
- Certified production according to ISO22000
- Contaminants legislation - EC1935/2004
- Material requirements - EC10/2011
- Quality requirements - EC2023/2006
- 100% traceability
- Declaration of Compliance
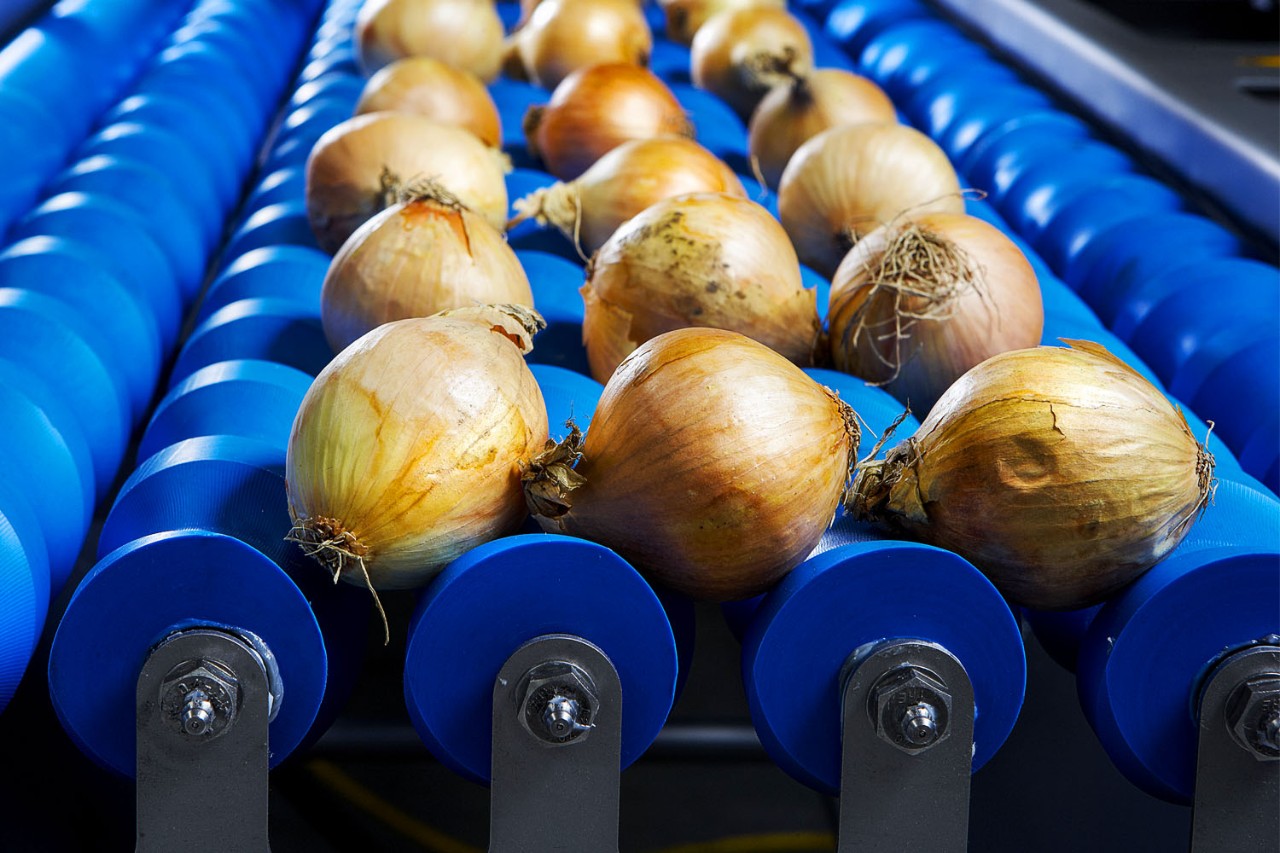
Raising awareness through education
At ERIKS, we are dedicated to convince manufacturers and machine builders of the importance (and compliance) of current legislation. This is the only way to avoid major food safety problems.
Fortunately, some manufacturers are very progressive. When we visited an American pharmaceutical company, everyone was called together. The buyer, the technical department, the quality manager - anyone who had anything to do with the topic of traceability.
After a session like this, you notice that people 'wake up'. Immediately, employees realise the importance of the issue and start acting on it: a mechanism of alertness and pro-activity comes into play. As a result, a quality manager would comment: "Hey, what's happening here should not happen in our production line". Due to the processes that have been discussed and established in the session, everyone is alert and observant. This is just one of the ways in which we help companies become aware of the issue of traceability in the chain.
In large companies, however, we also experience the opposite. For example, when the technical department needs parts quickly and because of the rush is not interested in a certificate or traceability. That's a risk.
Hands-on support
ERIKS offers in-depth support. We notice that companies struggle with issues concerning the implementation or further improvement of the EC1935/2004 legislation within their own processes. ERIKS offers companies tangible support, such as:
- Presentations to boost your knowledge on EC1935/2004
- Practical help with EC1935/2004 approval of installations
- Production methods according to GMP2023/2006
- A growing range of EC1935/2004 and EU10/2011 approved components
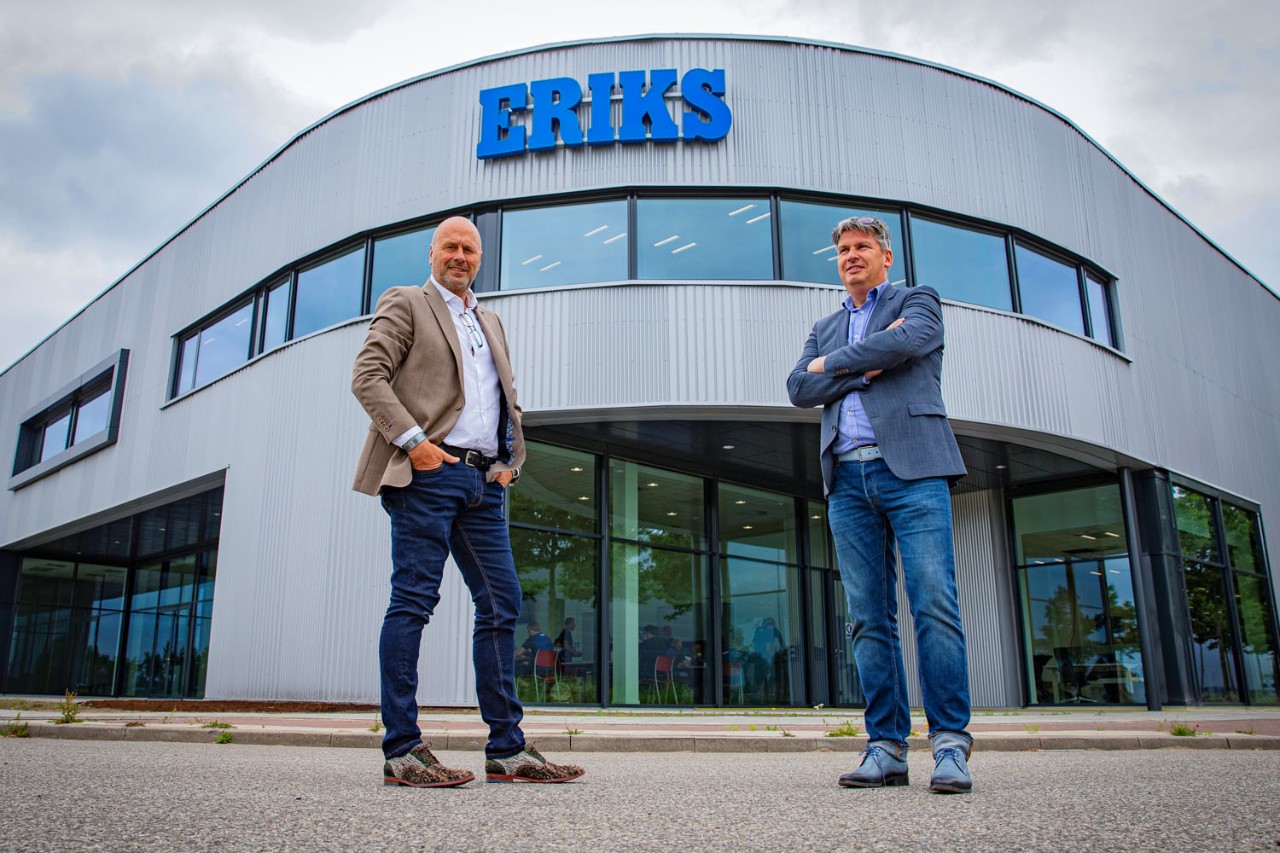
Recalls
There are many recalls in the food chain, especially when it comes to nuts, legumes, fruits and fish. What Mars experienced in 2016, when they dropped a cap in their production line, doesn’t have much to do with traceability per se. What is does show is the enormous impact of a recall. You can imagine the expenses of recalling your product across 60 countries because your processes were not in order.
Another example is the case of a well-known cornflakes producer. The smell and taste of the cornflakes were affected due to package migration. The impact of these events on smaller companies might lead to bankruptcy due to having millions of boxes taken out of circulation. When companies do not take responsibility, consequences of a claim are immense.
During an inspection, companies will sometimes show a slip of paper, marked EC1935/2004, stating: "This is a certificate that my supplier gave me." But you don't get away with it that easily. Traceability is just one piece of the puzzle you have to complete. What about correct migration values? You need a certificate, a DOC (document of compliance) that contains a reference to your technical drawing (number), specifically linked to an order. A scrap of paper stating that a specific material complies with 'something' is not enough for an audit.
Certified end products
A Food Grade processed product is traced internally by batch- and production order number. When our production is finished with the plastic end product, we tick all of the boxes on our checklist. The EC1935/2004 certificate is linked to the finished product.
Certificate requirement according to EC1935/2004:
- Material batch number
- Order number
- ERIKS Order number
- At line level
- Correct migration values
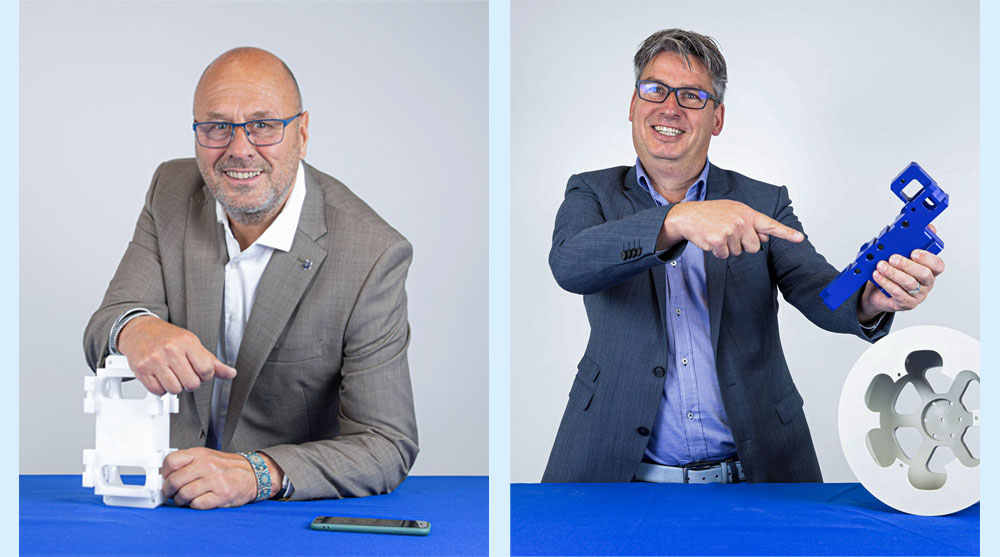
“We worry sometimes, even about big players you don't expect it from”
All these data are vital to ensure traceability. Using this method, we are able to trace your order back to the supplier's granulate.
Simplifying the hard stuff
When a company asks for our help, we have all of their departments come together: purchasing, sales and production, but especially quality control (as they have a mandate). Quality control decides what will or will not happen in the production process. This department also understands the importance of traceability. We make all these steps transparent and verifiable.
Sometimes it is even used against us, that we ‘overcomplicate’ matters. This is not the case. Our method ensures that your business complies with current legislation. The legislation-standard has been in force since 2004, and may be fined since. We are not overcomplicating, we are simplifying the hard stuff.
This applies not only to our industrial plastics, but also to piping systems, seals, hoses and all components that come into contact with food. And, we practice what we preach. ERIKS is itself audited by Lloyds. Within our facilities, we keep our stocks separated between Food Grade and standard assortment to avoid contamination. In turn, we audit our suppliers. This way, we can guarantee complete traceability.
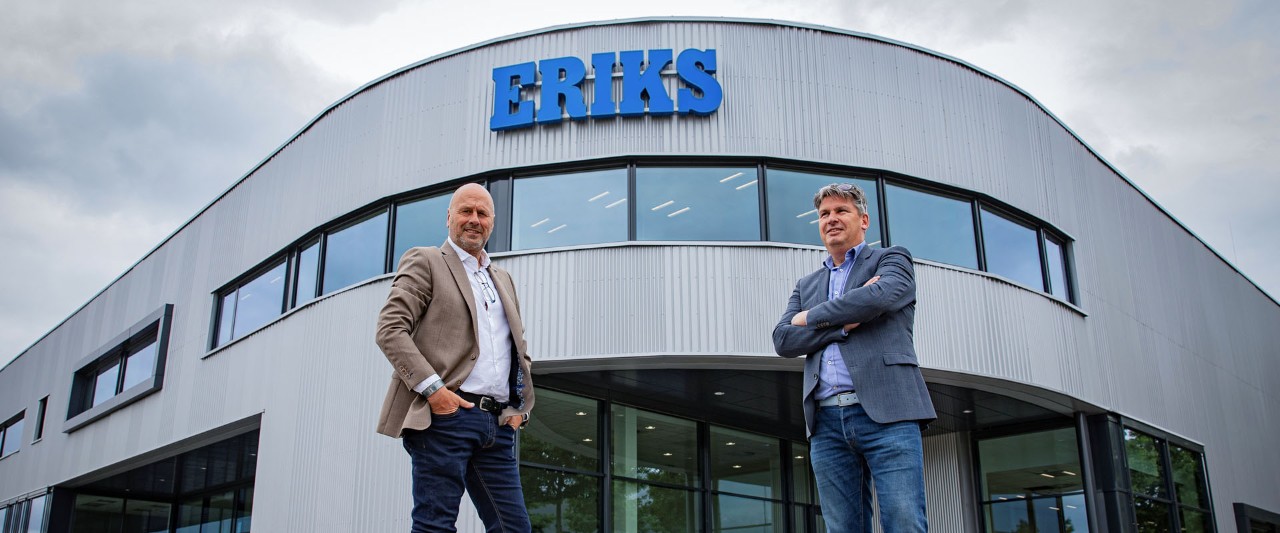
Berry and Edwin at the Industrial Plastics Centre of Expertise in Ede.
Not just a 'story', but a way of working
Our message to the market is: look at your process and make sure it’s up-to-date. Do you need help? ERIKS Application Engineers are happy to assist. Our many years of experience and countless insights with clients in the food sector will guide you through the maze of the EC1935/2004 legislation.
To be fair: if you want to get this sorted out, you need to get cracking. Fortunately, we can support you. We’ll set up traceability, right up to the raw materials producers. Customers will need to set up their own registration systems. Traceability and EC1935/2004 legislation is not just a 'story' that we come and tell you - it is a way of working.
One final example from our day-to-day practice: a company has a lot of plastics stored in bins. No one knows where they come from or what they are suitable for. They have to dispose of the items and reorder them with a certificate. Of course, we think this is a nice order, but does it really help the company? If management and registration are not adjusted, you will have the same problem again in no time: materials will get mixed up. We are here to help you implement traceability.
We document the entire flow meticulously; from granulate to end product. That’s why companies like to do business with us.
Invitation
Get in touch! Visit our brand new Industrial Plastics Centre of Expertise in Ede, where we can physically show you all aspects of traceability in the chain. Take a look behind the scenes, and together we will discuss the major issues around traceability. Want to know more or make an appointment?
For more information on traceability or to get in touch with a dedicated Application Engineer, please contact your local ERIKS Service Centre, who will be happy to discuss your options.
#ERIKS #LetsMakeIndustryWorkBetter #Food #Traceability #Legislation #FoodSolutions
Solutions for the food industry
About the food industry
Our blogs on food safety
Consult our Food Experts
Top Tips Whitepaper
ERIKS will handle this - let us know how we can help...
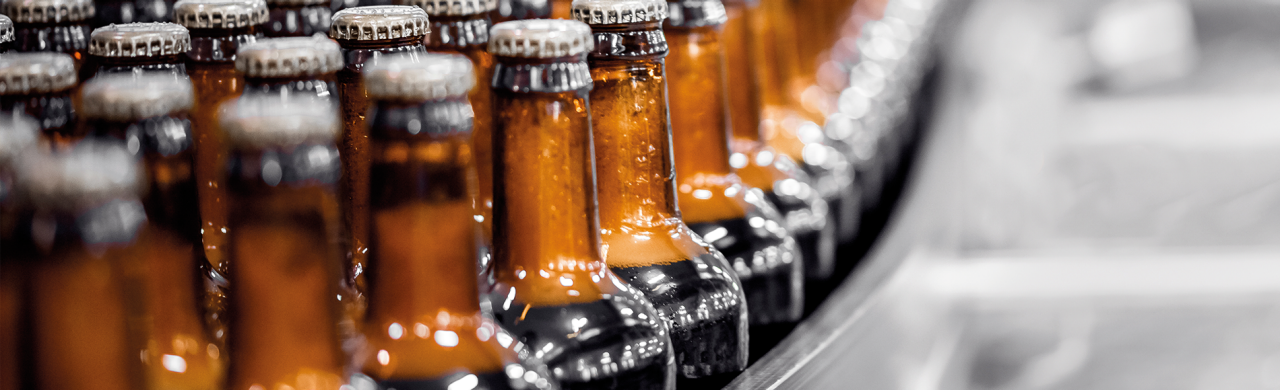