In this article
When a hammer's not enough - there is another solution
To the person with only a hammer, everything is a nail. But to the person with every option open, the solution is whatever’s best for the job. That’s why ERIKS’ repair/replace neutrality means customers are never pressured to make a choice. With all the options and costs presented to them, it’s their decision. And when one option offers significant savings, as it did for a UK power station operator, that decision isn’t difficult.
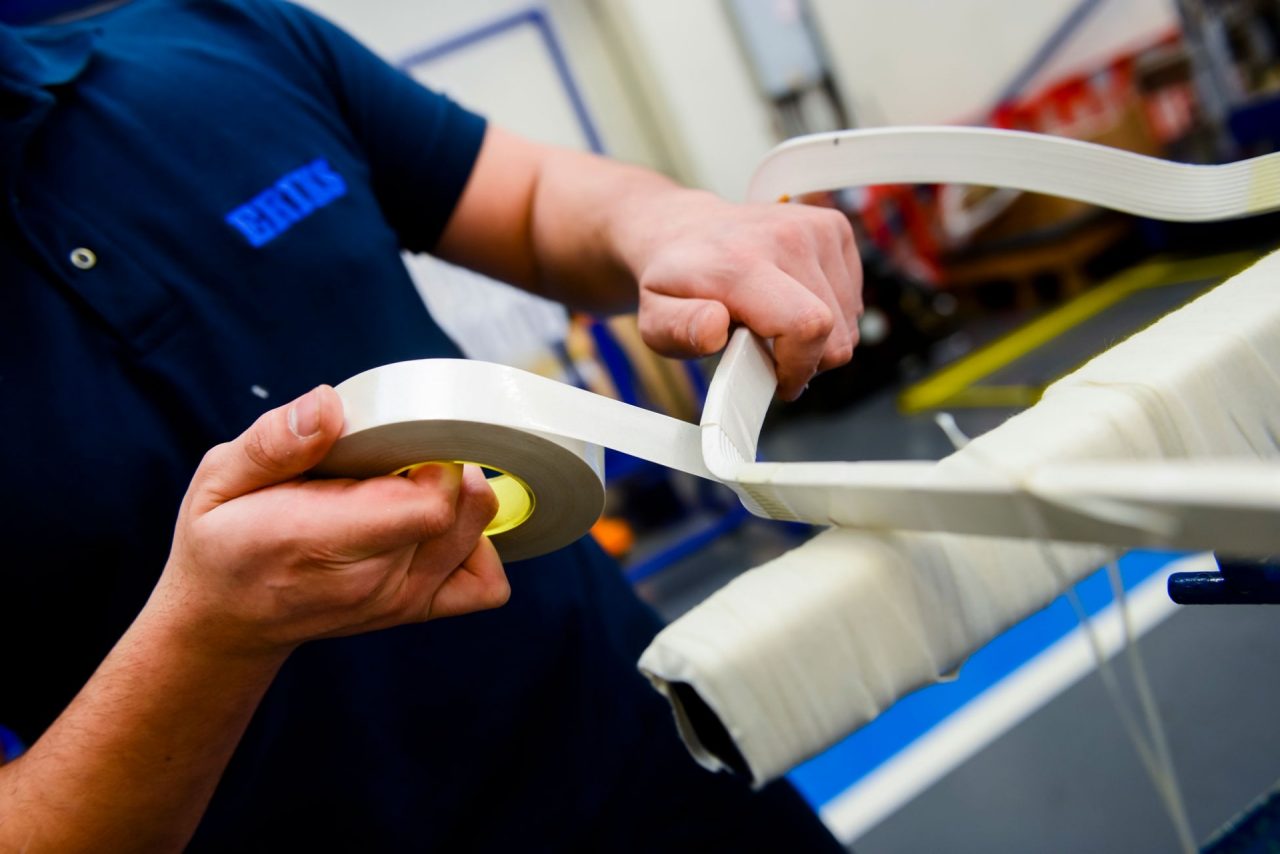
The customer’s original supplier was keen to replace a failed 10 year-old boiler feed pump motor with a like-for-like new one. Perhaps to ‘help’ the customer with their decision, the new 11kV 630kW motor was priced at £94,000, and a rewind at £98,000. With no sales axe to grind, ERIKS’ rewind cost came in at £10,000 less than a new motor. But it was no cut-price solution.
Back to basics
Firstly, ERIKS’ engineers at the Chesterfield HV Motor Centre of Excellence, carried out a complete strip-down inspection of the motor, to identify the root cause of failure. This revealed the motor core was undamaged, but also that the specification was far from standard.
The stator slot thickness was more suited to a 6.6kV motor, and the insulation tape was correspondingly thinner. As a result, the windings had less than optimum protection in the slots and deteriorated prematurely – drastically shortening the motor’s lifespan.
Changing the slot width or the copper thickness weren’t viable options. But ERIKS could engineer a solution to offer more protection within the existing slots.
Got it taped
ERIKS’ motor rewind know-how made it easy for the engineers to find a far higher-quality replacement insulation tape, of the same thickness.
To further enhance its insulating properties, ERIKS used a high-grade epoxy resin pressed cell insulation system, to impregnate the tape and give the windings greater protection in the slots. Many repairers use alcohol- or ethanol-based resins, which evaporate at higher temperatures, leaving a void in the insulation.
ERIKS Chesterfield is one of the few UK repairers with its own vacuum pressure impregnation (VPI) facility. This gave ERIKS the flexibility to use a longer, lower-temperature process, to ensure the resin fully impregnated the tape.
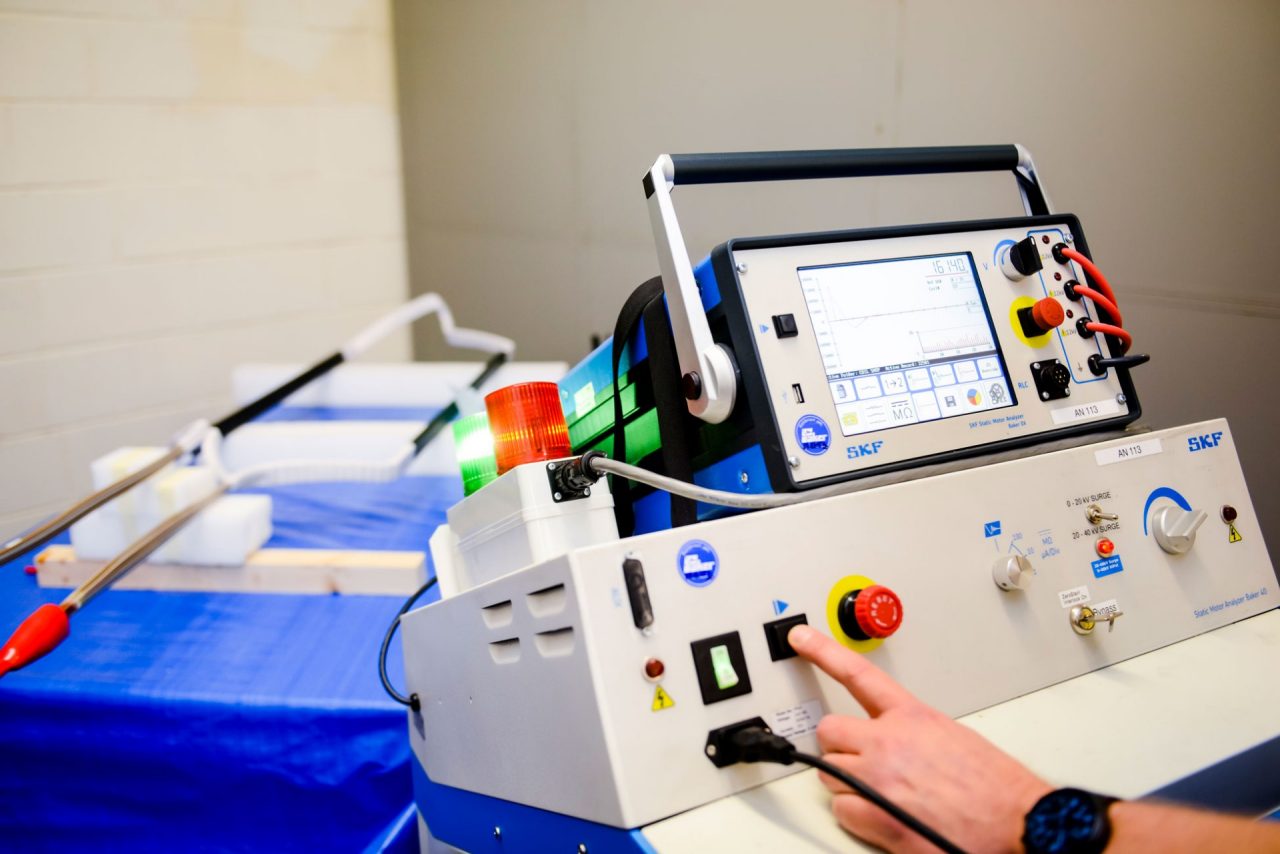
The tape thickness on the end windings was also restored to the thicker, standard 11kV specification, giving the motor the best possible protection.
With the new coils manufactured and fully tested, the motor was rewound incorporating the new insulating tape, and tested again, all on-site at Chesterfield. Then it was returned to the customer 17 weeks early and £10,000 cheaper than a new motor would have been.
All things considered
That’s one cost-effective rewind completed. But the customer has four more identical motors of the same age, potentially in the same condition, and all possibly prone to a reduced lifespan.
Using the Chesterfield Centre’s Partial Discharge and Tan Delta testing facilities, ERIKS can carry out a health check on all four motors. If the results indicate it’s feasible, a dip in the VPI tank would re-cover the insulation system – avoiding a potential rewind and saving around £70,000 per motor (or £80,000 for a replacement).
Alternatively, if the tests show a full rewind is required, ERIKS can upgrade all four motors in line with the first, to provide a similar extended in-service lifetime and more cost savings.
It’s the customer’s decision, of course. But when all the options are available – and all in one place – it’s much easier to make the right decision every time.
Chesterfield HV Scope of Service
- ERIKS Chesterfield HV Motor Centre of Excellence. A comprehensive range of HV and DC motor, transformer, generator and traction engine repair facilities and capabilities, all in one place.
- All coils manufactured on-site. Boughtin coils all arrive together, meaning a longer lead time and no chance to make changes before the full set has been manufactured. On-site manufacture means one coil can be fit-tested and installed while the next is still being made.
- In-house technical expertise and manufacture make upgrades easier to identify, propose, test and build.
- Motors: 3.3, 6.6 and 11kV. Up to 30 tonnes, 20MW (approx.) and 4.95m height.
- Generators: 3.3, 6.6 and 11kV. Up to 30 tonnes, 20MW (approx.). 4 pole.
- Transformers: 415V – 11kV. Up to 30 tonnes and 2.5m height.
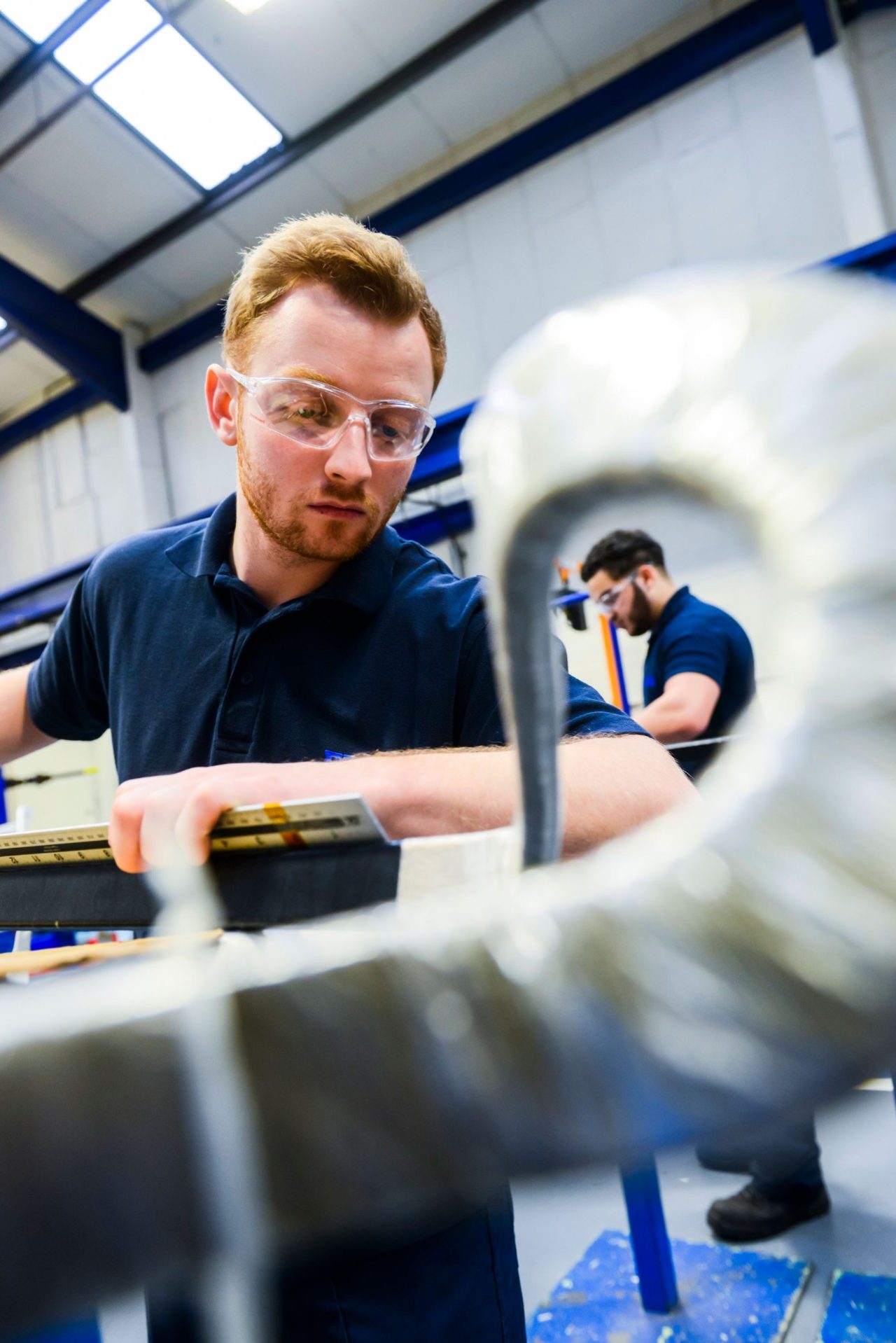
For more information on HV Motor solutions and to get in touch with one of our ERIKS Motor Specialists, please contact your local ERIKS Service Centre, who will be happy to discuss your options.
#ERIKS #LetsMakeIndustryWorkBetter #Motors #Maintenance #Solution #Engineering #Chesterfield