In this article
Sensus saves money with smart butterfly valves
Disruptions in your production process, or even total failure: nobody wants that. Inulin manufacturer Sensus was suffering a lot of this until ERIKS came up with a structural solution: the installation of 900 special butterfly valves. The result: a much improved production process, minimal downtime and total savings of EUR 800,000.
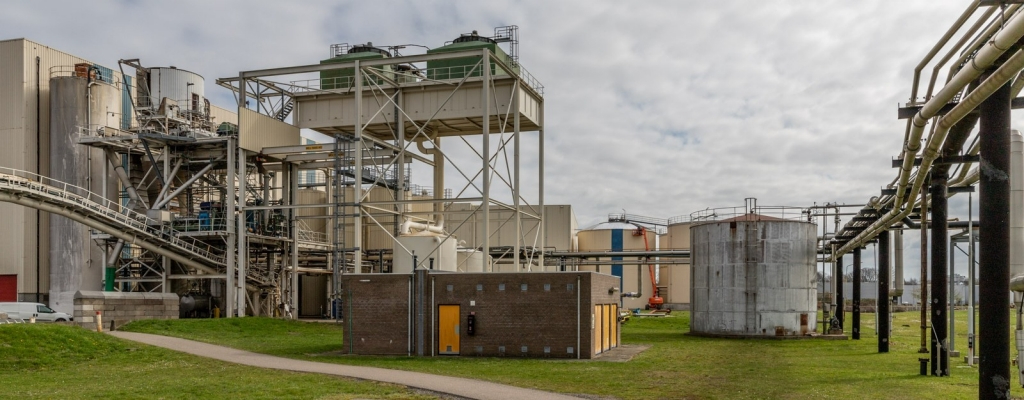
Worldwide, there are only three factories that produce it: inulin from chicory, suitable as a sugar and fat substitute and widely used, for example, in breakfast cereals, bars, bread, pastries, dairy products and baby food. One of these factories is in the Netherlands: Sensus, in Roosendaal. Sensus was experiencing many problems in the sixteen silos where the semi-finished product for inulin is demineralised: the demineralisation plant, the most critical part of the entire process.
Failures due to breakdowns and leaks
"The butterfly valves there often failed or suffered leaks," says Martin Geuke, Sensus purchasing manager. "We carried out various activities that reduced the number of faults. But our engineers still had to work regularly to get things working again. And we couldn't operate at full capacity during that time."
Far less unexpected maintenance
Sensus asked three regular suppliers to help it find a solution to prevent breakdowns and failures. "We set the same tough conditions for all three: we wanted valves that could give us operational reliability, that were guaranteed to last ten years," says Geuke. "So that we would have much less unexpected maintenance and the plant could just keep running."
800,000 less in unforeseen maintenance costs and breakdowns
The new butterfly valves have now been installed in one of the four lines of the Demi plant. "It turns out that ERIKS supplied the right valves. There are no malfunctions and no leaks. The people at ERIKS handled it well and helped us enormously." This is also reflected in the expected savings: Over the next ten years, Sensus will spend around EUR 800,000 less on unforeseen mechanic costs and costs due to operational downtime, or EUR 80,000 a year.
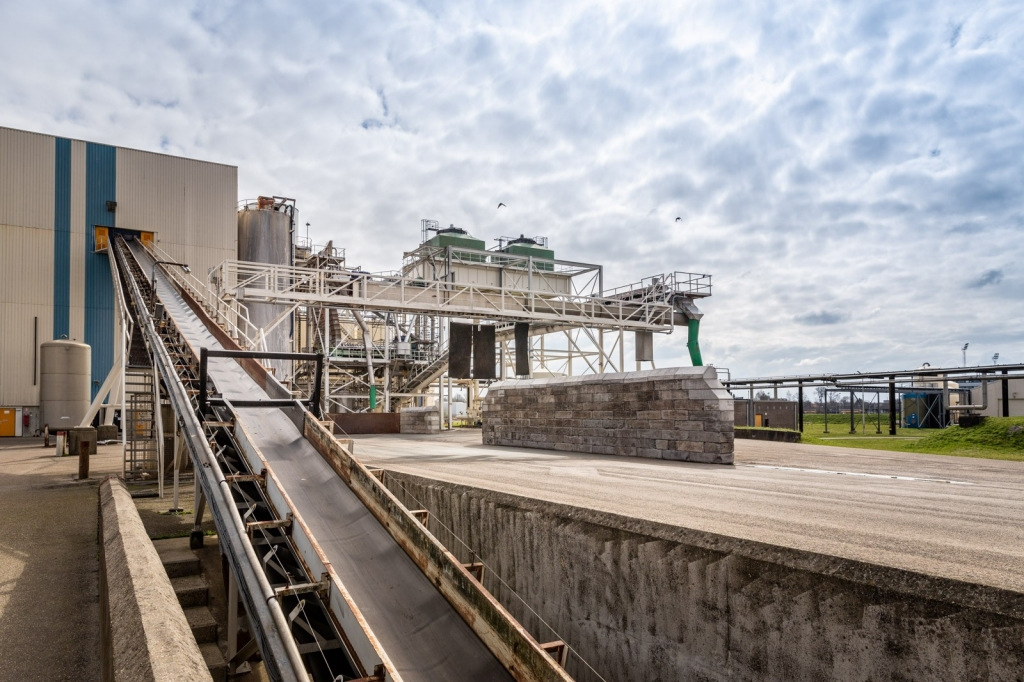
Sensus's Inulin factory in Roosendaal
Confidence in a successful outcome
Doing business is about having trust in each other, Geuke emphasises. "We certainly already had that trust and now with this result ERIKS has definitely added another excellent product group. Our factory will be even more stable thanks to ERIKS. And that is what it is all about for us.
5 advantages of ERIKS butterfly valve solutions:
- think proactively about optimising the production process
- minimise failures
- prevent leakage
- reduce downtime
- structurally reduce unforeseen maintenance costs
Pro-actively working together on a successful solution
The solution that ERIKS developed especially for Sensus was chosen. "ERIKS simply understood our question best," says Geuke. "It was more than giving a ten-year warranty on your product; it was proactively working with us to find a good solution to the problem."
We were naturally keen to help optimise the process," says Ron van der Velden of ERIKS, a supplier to Sensus since 1999. First, ERIKS specialists investigated which butterfly valves were most suitable for Sensus's demi-plant. ERIKS and Sensus then carried out extensive tests for two months to ensure that the butterfly valves worked properly and without leakage. "We now have a valve that we know will work without any problems for ten years, or 10,000 switching operations."
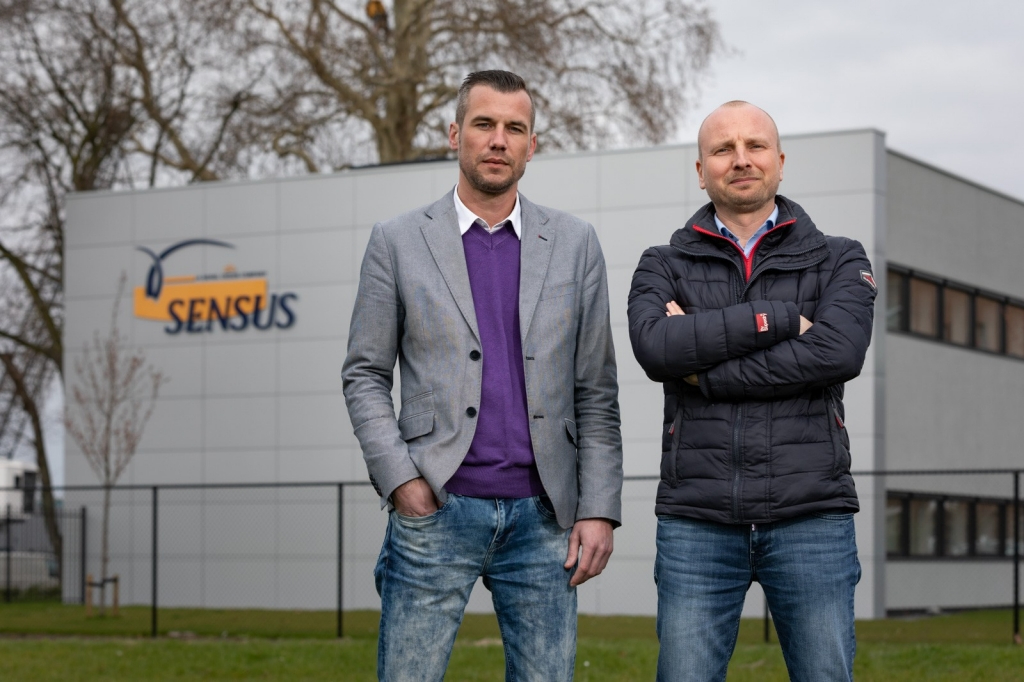
Ron van der Velden (L) and Mark de Jong of ERIKS.
Thinking along
ERIKS specialists will replace the valves in the other three lines step by step over the next few years. "This is a great joint result", says Geuke. "It was nice to see how ERIKS always thought along and selected the right product. We have come a long way in good cooperation."
"It is nice to see that this business unit can run carefree," says Van der Velden of ERIKS. "That is actually worth even more than the ten-year guarantee that we give on the valves: the idea that you, as a manufacturer, can rely on the machines and installations just to keep on running."
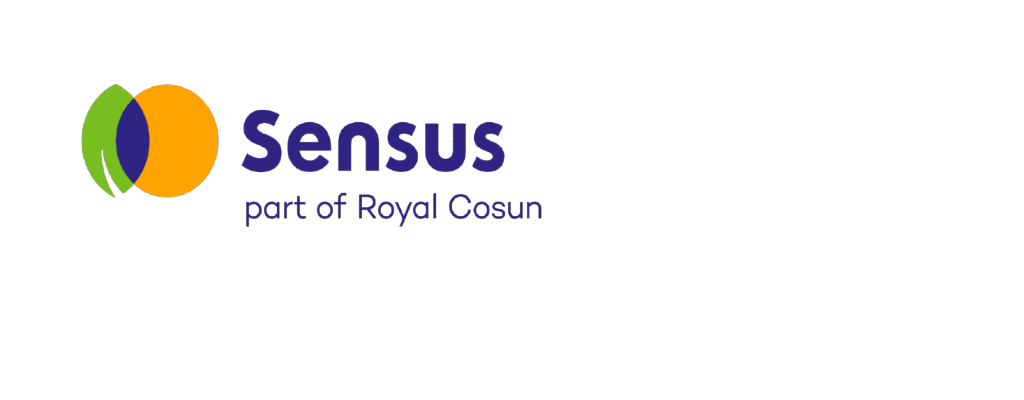
For more information on Valve solutions and to get in touch with one of our ERIKS Flow Control Specialists, please contact your local ERIKS Service Centre, who will be happy to discuss your options.
#Sensus #ERIKS #LetsMakeIndustryWorkBetter #Food #FlowTechnology #Valves #CostSavings
Solutions for the food industry
About the food industry
Our blogs on food safety
Consult our Food Experts
Top Tips Whitepaper
ERIKS will handle this - let us know how we can help...
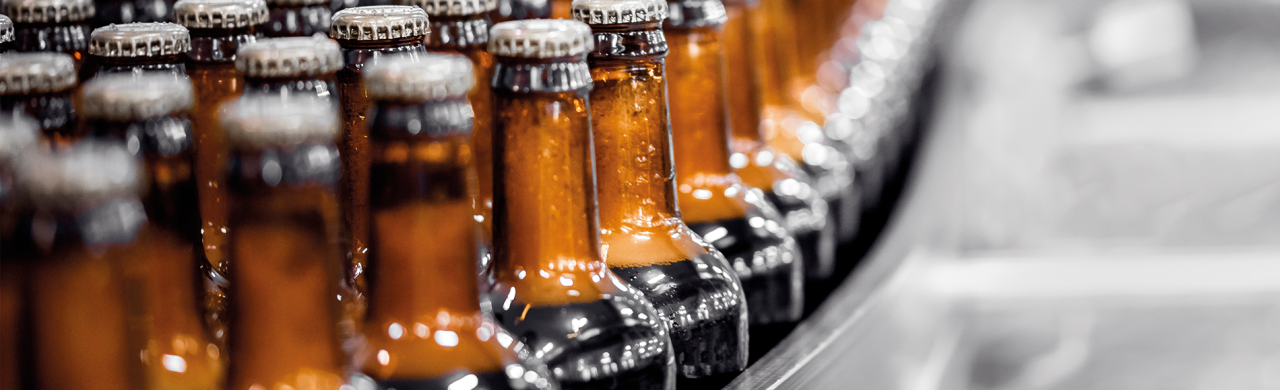