In this article
Efficiency or functionality? Why it's no longer Jekyll or Hyde
Good or bad? Left or right? Either/or? Would you prefer a premium energy-efficient motor in your production plant – incurring an extra cost? Or a standard motor that gets the job done and no more? The good news is, combining efficient motors and drives with digital solutions, can give you sustainability and an improved total cost of ownership (TCO).
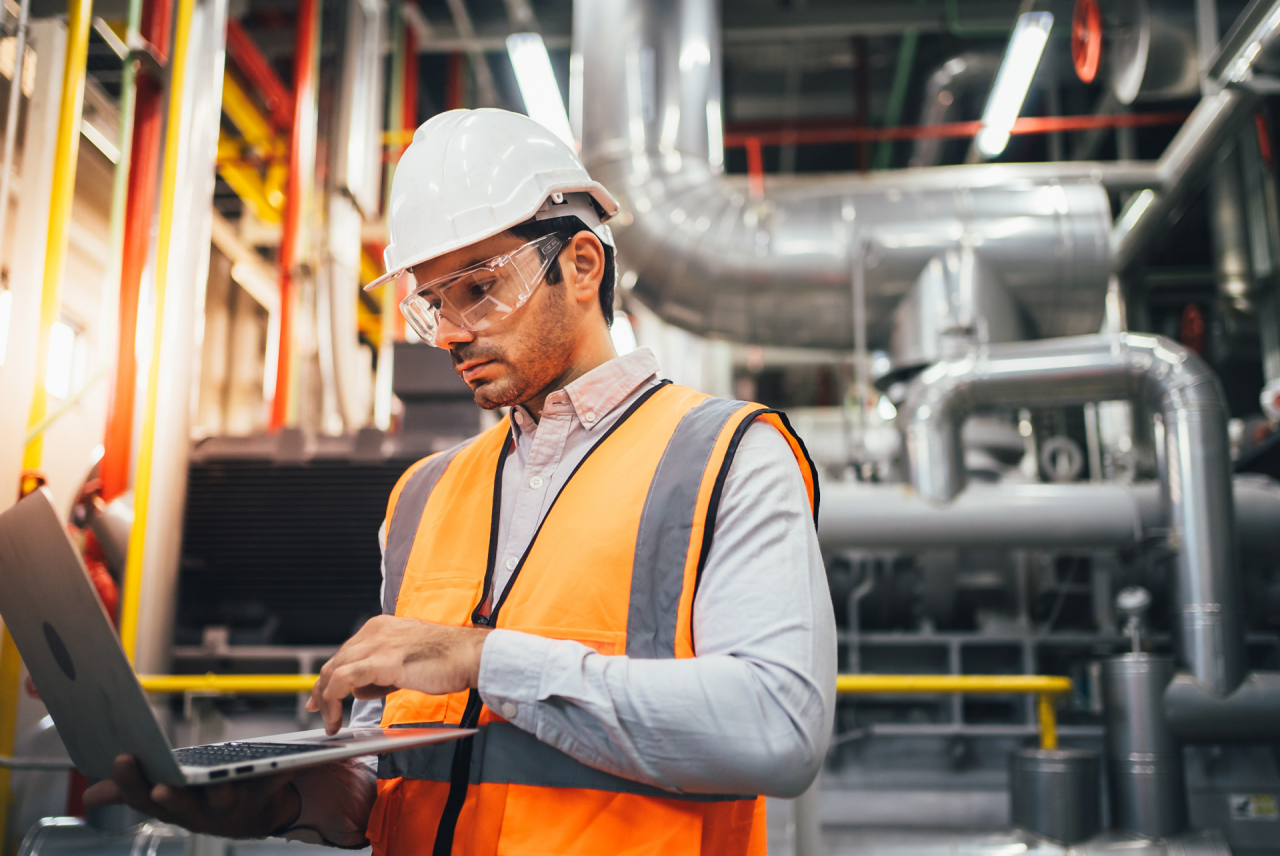
Maintenance engineers and plant managers have traditionally been on opposing sides in an efficiency v. functionality battle. While the engineers’ priority has been to keep the plant running, managers’ have been trying to balance functionality with energy efficiency. But now that it’s every plant employee’s responsibility to seek sustainability, maintenance has an integral part to play.
The question is: how?
Electric motors, for example, represent around 50% of global electricity consumption. So reducing this will be vital to achieving sustainability goals. Reduced power consumption and energy costs will, of course, result from increasing plant efficiency and environmental compliance – and inevitably, a reduced TCO will follow.
How efficient is ‘efficient’?
The energy efficiency level of an electric motor is calculated as the ratio of mechanical output power to electrical input power, and expressed in International Energy (IE) efficiency classes.
IE1 is the lowest classification level, and IE5 the highest. Since July 2023, European legislation adopted by the UK states that 75-200kW motors must meet the IE4 level. The EC predicts this new legislation will save 110 Terawatt-hours (TWh) by 2030 – equivalent to the electricity consumption of the Netherlands.
Efficiency in action
WEG’s extensive range of energy efficient electric motors for safe and hazardous applications is rated at IE4 and IE5, and offers significant energy savings.
The W22 Permanent Magnet (W22 Magnet) electric motor, for example, is highly effective in reducing motor temperatures and maintaining consistent torque, particularly at lower speeds. It enhances motor productivity, minimises electric losses and temperature and, when controlled by an inverter, gives impressive energy savings and application versatility.
One of Brazil’s leading packaging and disposable plastic manufacturers, Orleplast, deployed multiple W22 Magnet motors at its Santa Catarina facility, ranging from 200 to 250kW. A WEG CFW11 VSD was incorporated for added energy efficiency. The result was energy savings of 286,416kWh per annum: equivalent to powering 85 homes for a year.
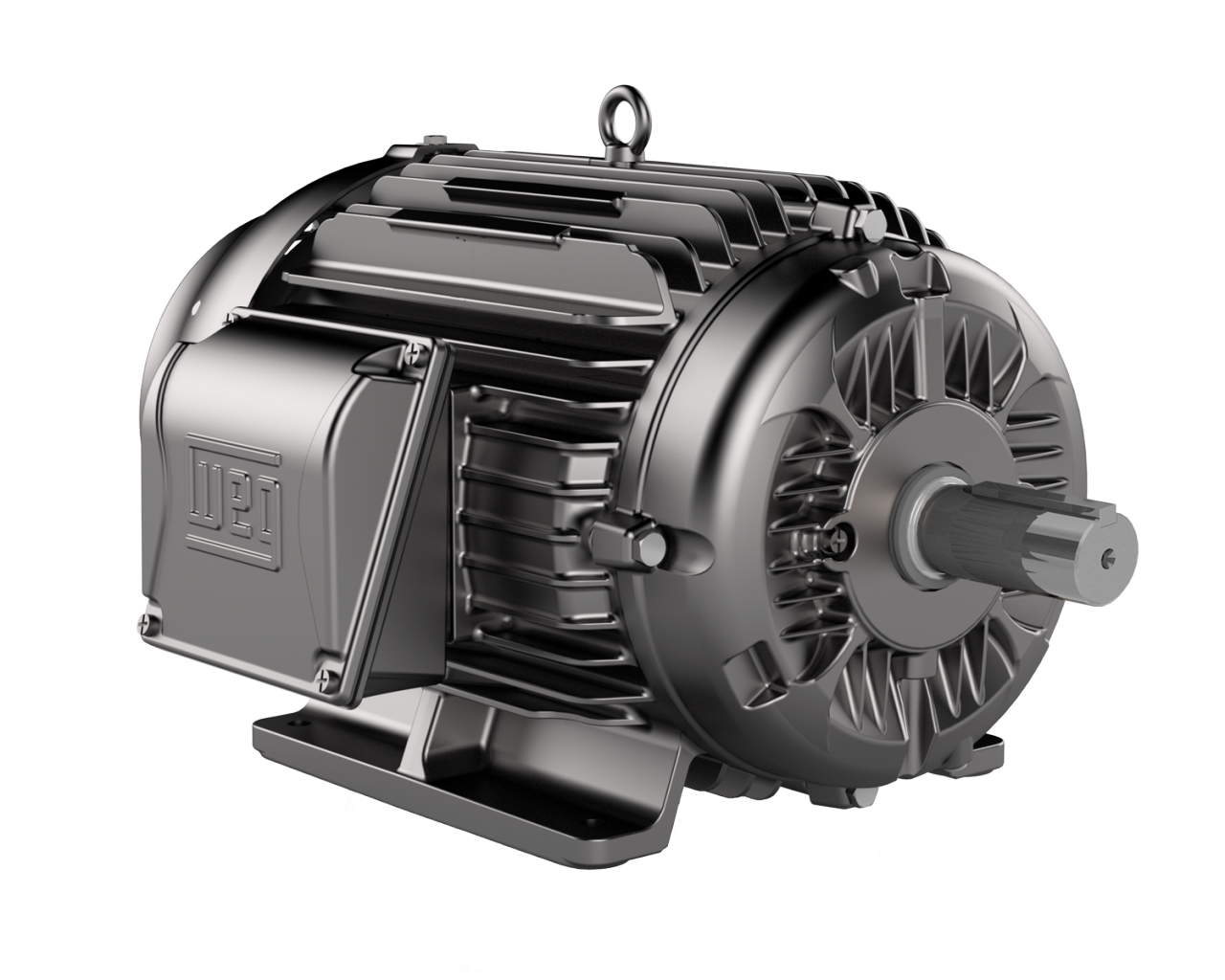
Higher with hybrid
If IE4 efficiency delivers such impressive results, what can be achieved with an even higher efficiency motor?
The WEG W23 Sync+ motors are a hybrid innovation combining permanent magnet (PM), ferrite or neodymium magnets and synchronous reluctance (SynRM) motor technologies. This offers a higher level of efficiency for the entire speed range compared with conventional induction motors – up to IE6 – and a higher power factor than SynRM motors.
The W23 Sync+ motor line unlocks energy savings that have a direct impact on CO2 reductions for production facilities. In fact, WEG has calculated that replacing an IE3 induction 75kW 4 pole with an IE6 W23 Sync+ motor variety may result in a reduction of 126 tons of CO2 during its expected 25-year lifetime.
Making maintenance work sustainable
The sustainability of these more efficient motors and drives cannot be denied. But how can it be combined with the pragmatism of maintenance work? One answer is to introduce digital software such as WEG’s Motion Fleet Management (MFM) into the equation.
That was the solution for a petrochemical manufacturer experiencing at least one motor failure a month. Seeking to enhance Overall Equipment Effectiveness (OEE), the company chose the WEG MFM digital platform to handle remote monitoring and maintenance.
Data gathered by MFM from sensors fixed to the motors was translated into user-friendly indicators, graphics and a historical dataset, making analysis straightforward. The plant’s maintenance team used this data for its own predictive maintenance strategy, resulting in a full six-months with no motor failures.
WEG also employs the MFM platform at its own electric motors plant in Brazil. As a result, OEE rose from 76% before implementation in 2018, to 84% by 2020.
So efficiency v functionality is still an either/or situation. But now it’s either talk to WEG about energy-efficient motors, or miss out on sustainability and a lower TCO.
For more information on Power Transmission and to get in touch with one of our ERIKS Specialists, please contact your local ERIKS Service Centre, who will be happy to discuss your options.
#WEG #ERIKS #LetsMakeIndustryWorkBetter #Motors #IE4 #TCO #Sustainability