In this article
A record rewind for ERIKS Chesterfield
When a complex alternator stator at a major refinery required a rewind, the customer didn’t pause. They wanted a partner with the experience, expertise and resources to meet the challenge. And that’s where ERIKS know-how came into play, to complete the project in record time.

The stator is part of a customer’s generator, driven by steam from the refining process. After several decades service it was at the end of its life, and at risk of failure. It was already producing high partial discharge in service. To rewind it would be a 3-month project, but manufacturing new coils beforehand would normally take an additional 6 weeks. With the generator out of action for so long, the customer would have to buy-in their energy, with significant cost implications.
Fortunately, ERIKS’ forward-planning and rewind capabilities helped to save the client time and money.
Here’s one we made earlier…
The customer’s stator is not a standard design. It incorporates unconventional coils of a complicated shape, that demand special tooling and jigging for their manufacture. This all helps to increase the cost and the lead time.
Fortunately, ERIKS had manufactured replacement coils for the customer several years before. They were stored in special crates, inside sealed foil bags with a desiccant, and all ready to be used immediately.
ERIKS’ understanding of the stator, gained during the manufacture of the coils, made them the obvious choice for the rewind. But it was a rewind with nothing obvious about it.
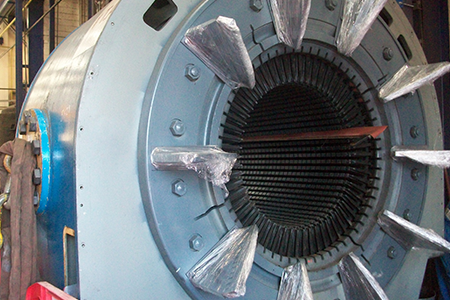
Stator stats.
A typical stator has a diamond coil winding which is relatively straightforward to rewind. This one was far from typical and far from straightforward.
The individual coil bars forming the winding are fanned out at the end winding, with each bar end required to be manually formed, joined and connected, to complete the winding and create the 3-phase, 2-pole circuit.
The stator consists of 60 slots, with a top and bottom bar in each slot. Each of those bars has 2 conductor turns, and each conductor turn comprises 10 parallel copper sectional strips. That’s a total of 2,400 individual sectional strips running through the stator and protruding at each end – making 4,800 copper strip ends in all.
Each of these ends has to be individually shaped – a process requiring care, precision and skill – then cut to size, braze joined, insulated by hand, and formed into the individual conductor turn. The completed and formed noses then have to be over-insulated, and all the associated end-winding supporting and bracing structure also has to be formed and secured.
It’s clear why the whole rewinding process took even ERIKS’ experienced engineers 10 weeks of round-the-clock working.
Rewind re-think
When the alternator stator had last been rewound, the only insulation available was Class B rated. Many years on, the availability of Class F insulation enabled ERIKS to propose an upgrade.
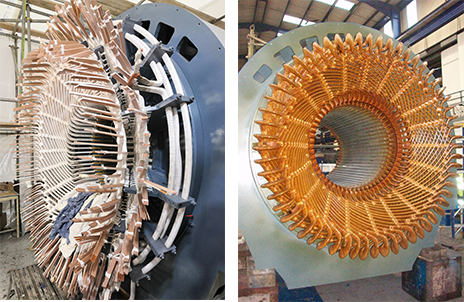
The thinner insulating material meant there would be enough space to accommodate conductive ripple spring side packing to secure the coils in their slots. This ensures more effective prevention of partial discharge in service and securing of the coils.
The customer agreed, and the stator was rewound to the new, higher standard, for even more effective performance. But even so, nothing was left to chance.
A test at every turn
A battery of tests was carried out throughout the rewind process, and once it was completed, to eliminate any potential mistakes and guarantee the quality of the operation.
These tests included:
- low resistance tests to check for poor joints
- circuit resistance balance tests
- polarity tests
- inter-turn tests
- a variety of insulation tests.
Lastly, before the rewound stator was approved to leave ERIKS’ workshop, it was subjected to a one-minute HV withstand test at 23,000V, followed by partial discharge and tan delta tests.
Put on the spot
The customer’s operating environment – a major oil refinery – is clearly a volatile one, with numerous associated health and safety risks. So to carry out the rewind, the alternator stator was transported from the customer’s site to the ERIKS workshop, where it was stripped and rewound before being returned to the refinery for installation.
However the customer was sufficiently impressed by the conduct and capabilities of ERIKS’ engineers in the workshop that a second job has now been booked. And to eliminate the time, complexity and cost of transportation, this time ERIKS will be working on-site.
Meanwhile, the successfully rewound and generator alternator stator with its upgraded insulation is back in operation, with a service life confidently expected to equal that of the plant.
With few suppliers able to match their experience, expertise or resources, it’s clear that ERIKS should be the first choice for a rewind of this scale and complexity. And you can put that on record.
For more information on Engineering, Repair and Replace solutions please contact your local ERIKS Service Centre, who will be happy to discuss your options.
#ERIKS #LetsMakeIndustryWorkBetter #OilRefinery #Engineering #Insulation