In this article
When 'Right First Time' is The Only Option
Reduced inventory, improved supplier network
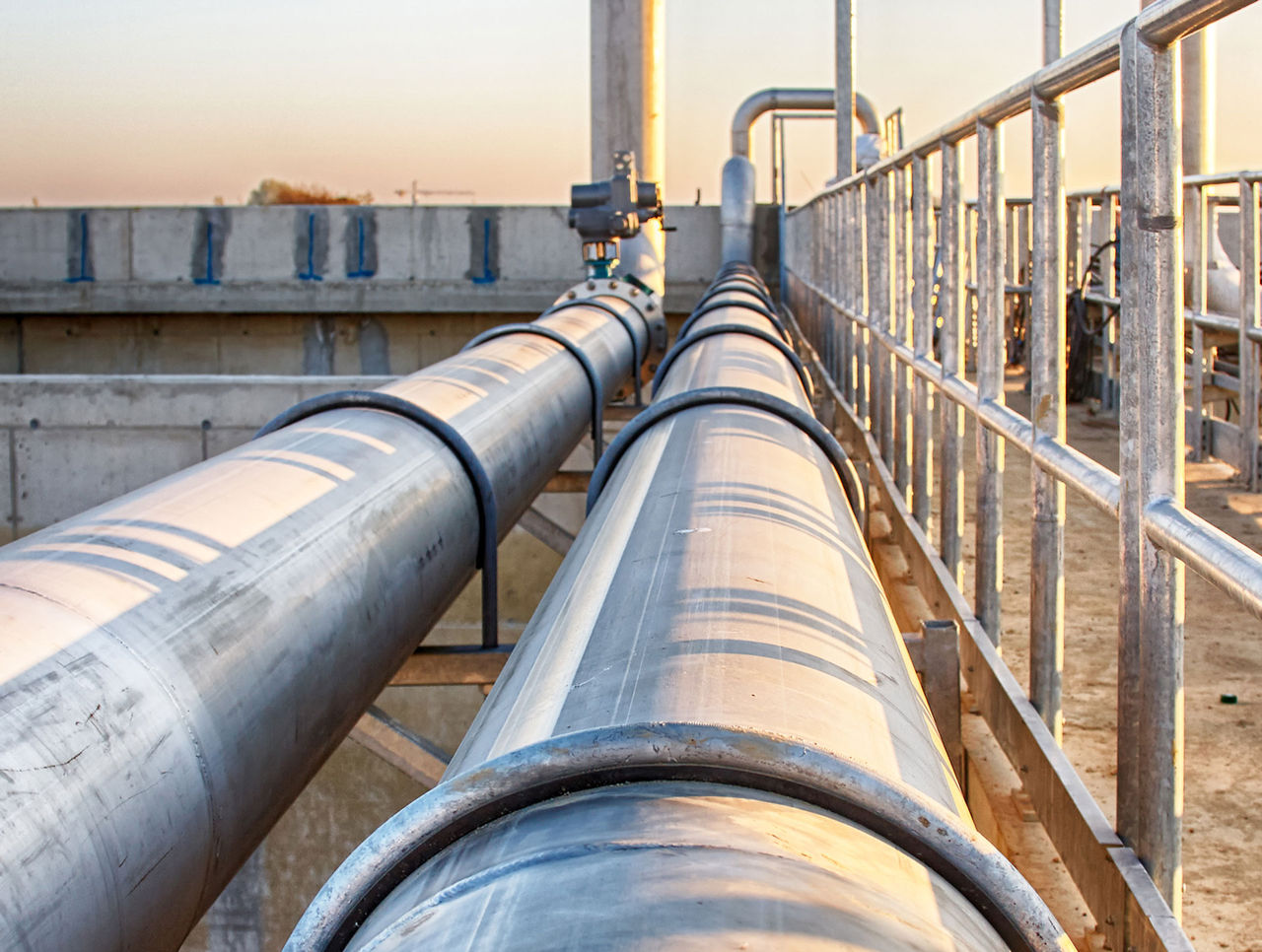
Industry Sector:
Water & Wastewater
Application:
River Intake Pumps
Actual Saving:
£100,000
Payback period:
8 Years (full)
Product/Service:
- Power Transmission
- Specialist Engineering
- 3D Printing
Customer Benefits:
- Reduced maintenance
- Improved uptime
- Increased productivity
- Reduced inventory
- Easier access to spares
- Lower lead-times
- New component database
Large-scale projects leave very little room for error. Customers are looking for a swift solution as downtime often leads to unnecessary expenditure and reputation is at risk. As an engineering service provider, customers are putting full trust in your capabilities to deliver, so right first time is the only option.
Challenge
One water authority was under immense pressure when Pump No.2 of their three river supply pumps was showing excessive vibration through the pump which was being transferred into the locaring bolts.
Pump No.1 had been with the OEM for more than a year, and now, and Pump No.3 had recently been overhauled and was running smoothly.
ERIKS were called and were requested to remove Pump No.2 and the associated high voltage motor for complete overhaul and repair in an efficient turnaround. The site would be down to only one pump for the duration of the remedial work without any duty/standby. Timing was of the essence.
On reaching the work shop the complete pump was stripped and cleaned, during the inspection, a number of critical issues were identified by the ERIKS engineering team.
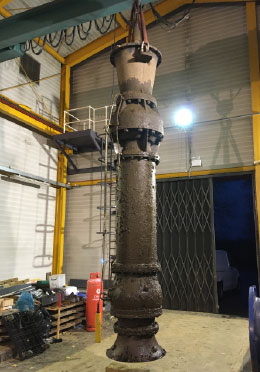
Old river intake pump in-situ
During the inspection, it was also evident that another party had previously repaired the pump. All the shafts were found to be ceased in the taper and collet couplings. One shaft had sheared and broken within the coupling arrangement. The taper on the end of this shaft was found to be inconsistent with the rest of the couplings and shafts.
This inconsistency meant the coupling and shaft were not located correctly, which had allowed excessive movement on the shaft and coupling arrangement, and ultimately led to the failure of the pump.
Solution
The ERIKS engineering team after completely stripping down and cleaning the pump, undertook NDT crack testing. All items were 3D scanned to provide a permanent database of all components, The database will enable ERIKS to manufacture spares prior to extracting the pumps and motors from this plant room in the future, therefore reducing the time these critical assets are off the application. There is the added benefit of maintaining control on quality and consistency on all future repairs too.
All wear items were replaced including, shaft sleeves, rubber cutlass bearing bushes, wear rings and shafts. In order to meet industry defined Regulation 31 and WRAS approval, all areas in contact with the pumped water were either coated with an approved coating or were manufactured using industry and OEM compliant materials.
In addition, ERIKS put forward a proposal to supply extra components for the customer enabling them to hold critical spares, including all wear items such as shaft sleeves, rubber cutlass bearing bushes, wear rings and shafts. Thus, reducing future lead-times.
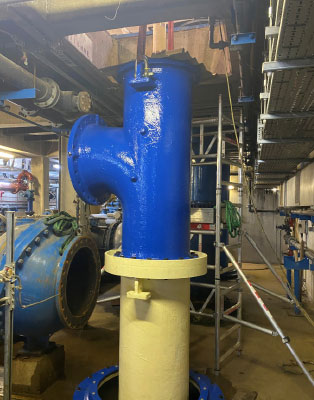
Refurbished and repainted pipework
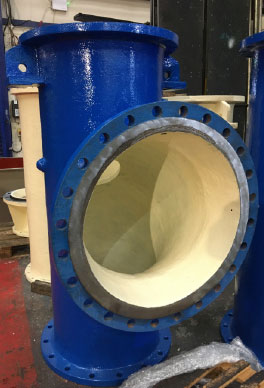
Refurbished pipework with WRAS-approved coating
Result
ERIKS were able to identify the root cause of failure, engineer a solution, and return both the pump and high voltage motor back into full service – within the agreed schedule.
The client now has a duty/standby pump arrangement for this specific application, as well as all the necessary information for ERIKS to supply previously long lead-time spares quickly in the future.
With spares and castings for many of the older pumps no longer readily available from the OEM, reverse engineering is now essential. Utilising modern technologies such as 3D scanning and printing, ERIKS can now confidently and consistently produce spares for the customer as and when requested on significantly reduced lead times, displaying, in this case, that repairs are far more cost-effective than replacement.
It is anticipated that the overhauled motor and pump will last at least 50% longer than the previous repair, saving the customer £90,000 and reducing the customers need to attend site to perform maintenance, which would total an additional £10,000 over an eight year period.