In this article
Clearing compressed airways!
A completely new way to tackle air filtration
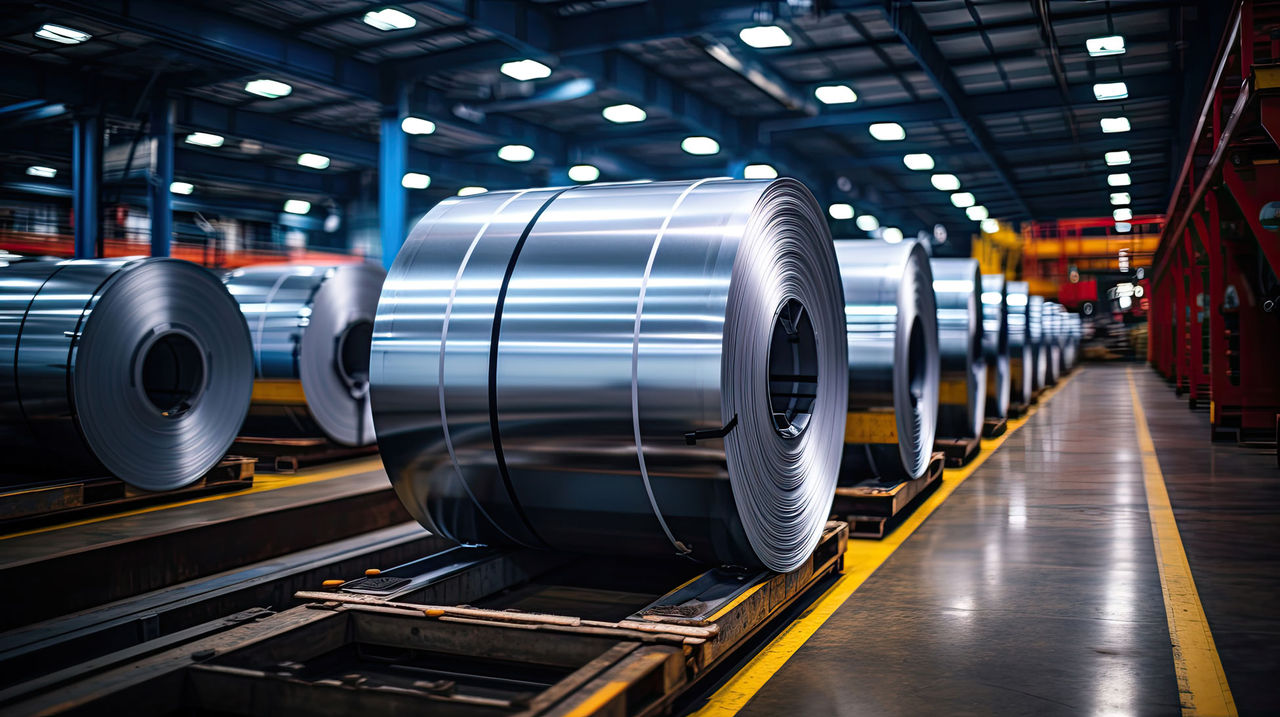
Industry Sector:
Primary Industries
Application:
Baghouse dust collection / Powder blowing machines
Actual Saving:
£72,260
Payback period:
12 months
Product/Service:
- System inspection and upgrade
- Filter supply and installation
Customer Benefits:
- System improvement
- Reduced maintenance
- Increased productivity
- Improved reliability
The oil emulsion, moisture and solid particulates found in compressed air cause damage and wear to pneumatic equipment. Filtration is essential but, until recently, the technology to deal with it was remarkably primitive.
A radical new alternative to traditional membrane filtration has saved a major manufacturer tens of thousands of pounds in replacement costs, increased the life of the equipment and drastically reduced the likelihood of unplanned shutdowns, thanks to ERIKS problem-solving expertise.
Challenge
Moisture in the air lines was causing extensive damage to pneumatic equipment at a major UK steel manufacturers plant. The manufacturer operated a baghouse dust collection system, but the baghouse filter socks would frequently clog and tear, requiring replacement on a regular basis and occasionally leading to unplanned site shutdowns when harmful emissions were detected in the dust pollution caused by torn socks.
In addition, the socks would clog due to moist particles, leading to frequent time-consuming air purges. Airline moisture was also affecting the manufacturers powder blowing machines. Resulting in damaged solenoid valves, leading to uncontrolled application of powder, which would then have to be applied manually — again, extremely time consuming and costly.
Traditional air filtration equipment is essentially as primitive as a sponge on a stick, which is only up to 80% efficient at soaking up contaminants. As it becomes more saturated, the sponge becomes even less efficient and even more damage can be caused.
Solution
An ERIKS engineer reviewed the problem and determined that AVG’s EXPEL compressed air filter was the answer. Unlike traditional membrane systems, EXPEL is engineered using computational fluid dynamics and works by manipulating the flow of compressed air so that moisture and particles are removed before they can do any harm.
Compressed air entering the unit is directed downwards towards angled vanes which create eddy currents, forcing contaminants to the sidewall of the bowl where they are automatically discharged. Next, the air is forced up through the unitary vertical bodies where the <5% of remaining contamination down to one micron falls to the base and is also discharged.
Installation is simple. There are no holes to become blocked and no moving parts to fail. The EXPEL is reusable and easily cleanable if required.
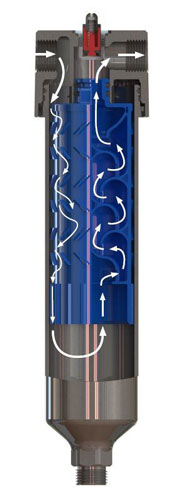
Cutaway of AVG EXPEL Compressed Air Filter
Result
Once installed, EXPEL was removing 250ml water every two days, a volume that indicated the need for a well above average frequency of refurbishment of the baghouse with the previous system.
The more efficient removal of water and contaminants means that baghouse refurbishment requirements have been reduced, with a lesser impact on planned maintenance time and costs. And the cost of replacement filter socks has been eliminated, because they no longer clog.
Following this a second EXPEL unit was installed near the powder blowing machines, to eliminate damage to the solenoid valves and to prevent them from malfunctioning, so time is no longer wasted applying powder manually.
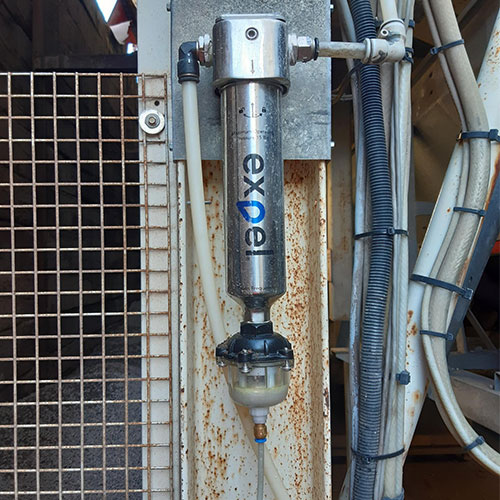
AVG EXPEL Compressed Air Filter installed
Financially, this has saved a cumulative £72,260, comprising £11,000 saved on sock replacement, £27,000 on sock cages and spares, £6,000 on pulse control panel and £28,260 on labour costs.
Energy use has reduced as the site is no longer having to purge the clogged socks and wasting compressed air. The equipment will last longer, too, thanks to the reduction of contaminants down to 1 micron. Maintenance costs and downtime are reduced and productivity has increased.
ERIKS diagnostic expertise, speedy response and delivery of the EXPEL unit meant that the problem was solved quickly and efficiently, with as little disruption to normal production as possible.