In this article
Full steam ahead
How can steam system users achieve their decarbonisation and sustainability goals? One way is by working with ERIKS and partner supplier Spirax Sarco. In this article, Spirax Sarco Channel Manager Paul Pugh looks at the opportunities for pharmaceutical companies in particular to utilise new infrastructure methodology and continuous assessment and monitoring.
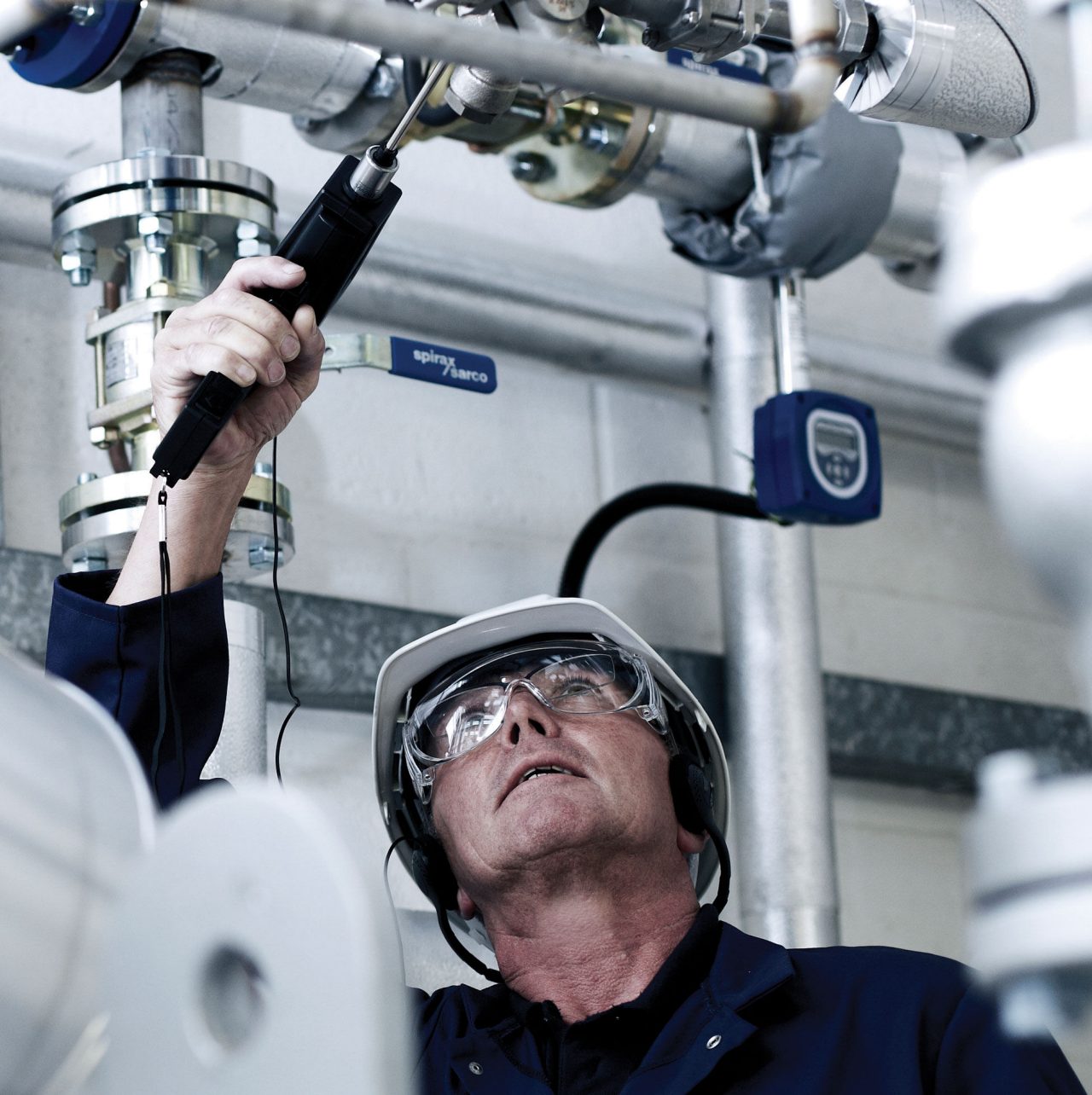
Will a mechanically correct, appropriately maintained steam system contain potentially harmful volatile substances or biological contaminants? It’s highly unlikely – which is what makes that system the very definition of sustainable. And with Spirax Sarco’s help to improve steam quality management, customers can further enhance the potential of their existing steam system, plant and process – to do more with their current infrastructure, or to do more with less through effective demand reduction.
The first steps are to understand the customer’s needs, and to benchmark their existing steam systems.
Giving substance to steam
Because every manufacturing site is different, an initial assessment is essential. This uses steam quality testing (SQT) and steam trap surveys (STS) as a benchmark diagnostic, followed by a steam system audit.
Now the scene is set for Spirax Sarco’s steam quality management approach, addressing three main points: safety, mitigation of contamination risk in the steam system, and efficient thermal energy transfer management (i.e. sustainability / decarbonisation).
Focussing on these helps us to achieve our aim for our customers of safe, compliant and thermally-efficient plant and process steam systems, with steam of the correct quality and quantity, arriving when required at every plant and process point of use.
Focussed on Pharmaceutical
Our approach for the pharmaceutical industry has been developed with the support of the International Society of Pharmaceutical Engineering (ISPE).
Using steam system audits, we evaluate and address potential and known issues – including maintenance, expansion, refurbishment, sustainability and energy efficiency / process productivity. Within a typical pharmaceutical manufacturing facility we pay particular attention to the utilities and facilities functions (water, plant and process steam utilities), with a view to improving not only process but also steam quality.
While the steam system audit details how the current system is working, operator feedback highlights their main steam system concerns.
This provides for further engagement relating to decarbonisation, sustainability and energy saving – all supported by payback calculations for any proposed improvements.
The keys to the system
As part of developing a better understanding of the steam system, it is essential to consider Best Practice engineering, and to explore key areas including:
- type of products being manufactured
- number of process steam points
- how steam quality is currently managed
- steam generation and distribution methods
Survey and audit results then support further discussions around infrastructure and steam quality improvements, as well as helping to identify solutions to site issues and pain points. This is particularly important when considering overall sustainability goals, energy footprints and decarbonisation.
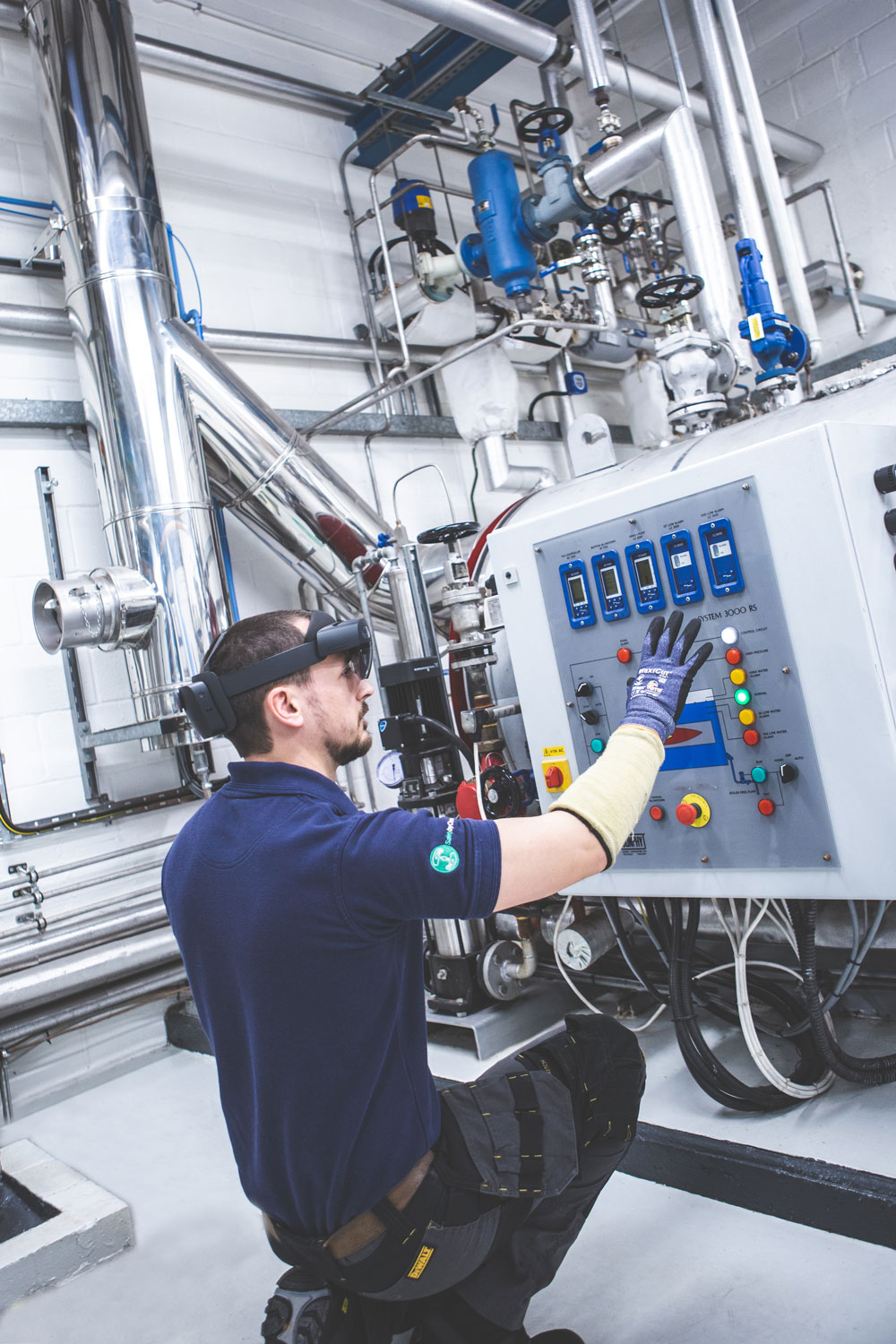
We deploy steam quality management tools (underpinning steam system engineering Best Practice) to achieve a mechanically correct and appropriately maintained steam system. One which raises, distributes and delivers steam of the correct quality and quantity to all points of use. Then, once a robust baseline has been established, the focus turns to steam system optimisation and – where appropriate – demand reduction.
Maintaining these steam quality management principles enables each site to gain the very best performance from its existing steam system infrastructure, and so to optimise energy use.
A solid foundation
The Spirax Sarco approach is to keep things simple. By working closely with individual sites we allow customers to learn, and build on their own knowledge and understanding – creating the solid foundation for a quality steam system.
This may involve, for example, establishing which points of use will benefit from monitoring (e.g. steam dryness or flow metering). Or where digital solutions will maximise value within the steam system – supporting cost centre analysis and allowing users to ‘walk the critical data’.
This partnering approach also enables seamless integration of Green-Tec solutions, ensuring our customers can do more with less in their existing infrastructure.
In summary, Spirax Sarco’s focus is on enabling customers to improve and maintain clean steam generation. This can be through both Best Practice engineering and by delivering more with their existing steam system infrastructure – leading to cost savings and increased productivity.
Ultimately, the goal is to raise and distribute steam more efficiently, and deliver steam of the correct quality to its point of use. All while delivering innovative solutions in support of process improvement, energy saving and decarbonisation.
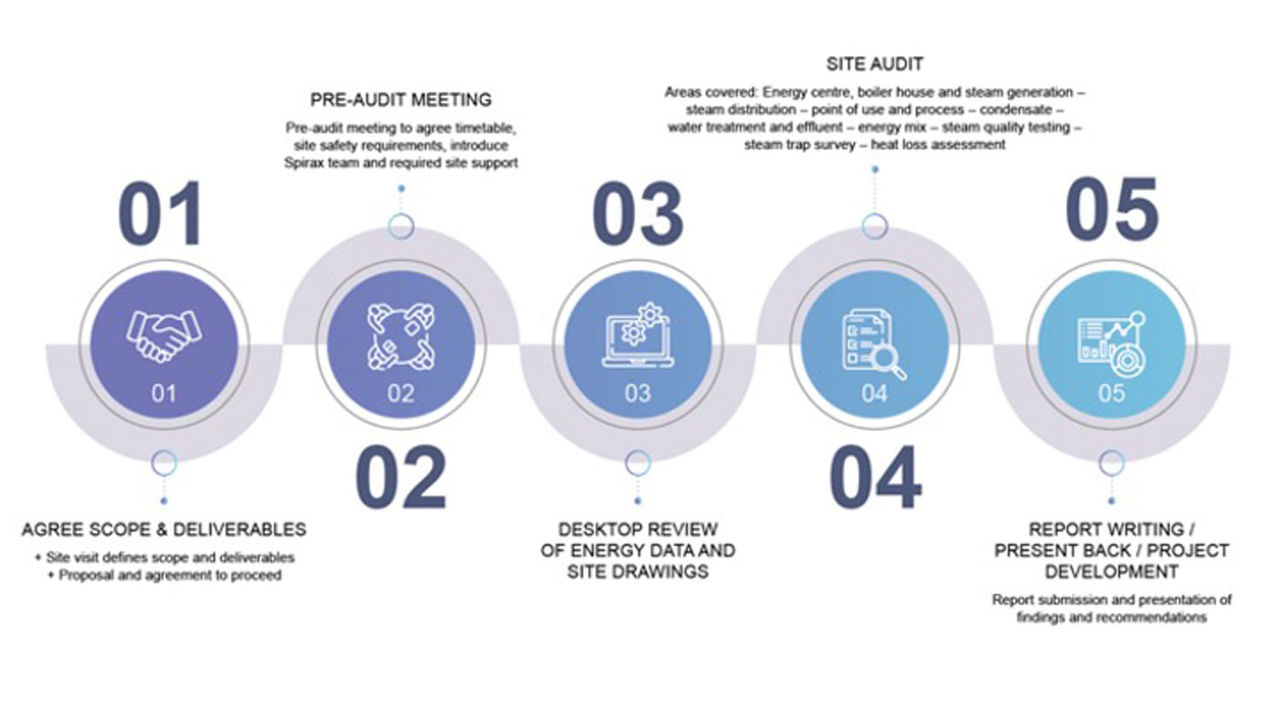
For more information on Flow Control solutions and to get in touch with one of our ERIKS Pumps Specialists or Valve/Flow Control Engineers, please contact your local ERIKS Service Centre, who will be happy to discuss your options.
#SpiraxSarco #ERIKS #LetsMakeIndustryWorkBetter #SteamSystems #Pharmaceutical