In this article
Time for a new air style?
It only takes a quick comb through your energy bills to spot rapidly rising costs. One way to trim them is to reduce leaks in your compressed air system. But a more effective way to save more – a buzz-cut to your costs, if you like – is simply to use less compressed air. An ERIKS Air Optimisation Program will help you to do exactly that.
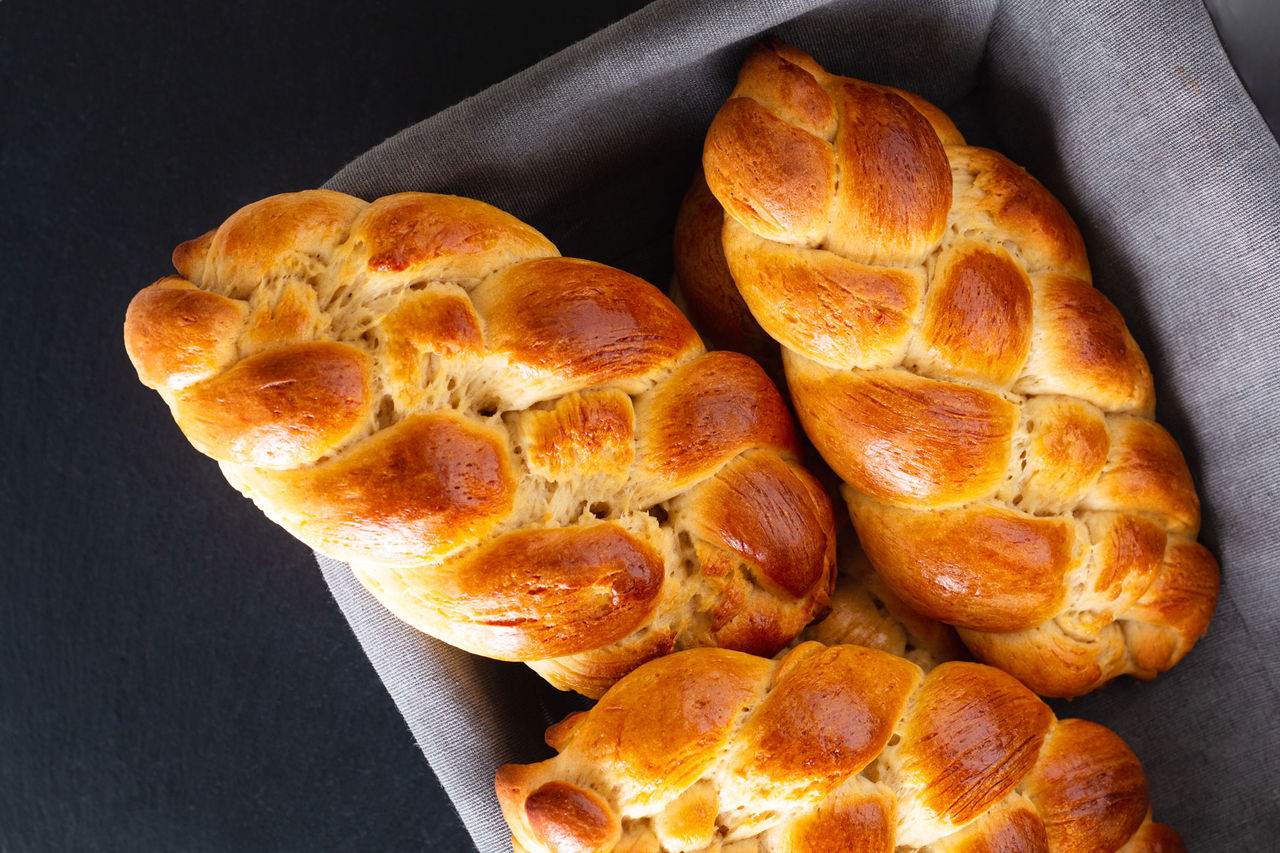
Compressed air is the only resource that’s generated to be wasted. Once it has been used, the open nature of compressed air systems means that the air is simply dumped into the atmosphere, and more has to be generated as required. If it leaks from the system before use, that’s a waste. But if you’re generating more than you need in the first place, that’s an even bigger waste, and an unnecessary cost for the energy to produce it.
The solution is a new compressed air style of energy-saving.
An ERIKS Air Optimisation Program doesn’t just reduce compressed air loss, but reduces compressed air generation too. And the less you generate, the less you pay for the energy to do it.
Slicing costs for a bread baker
A leading national bread baker wanted not only to reduce their energy costs, but also to shrink their carbon footprint. Realising compressed air usage was a significant factor in their rising bills, they contacted ERIKS for help.
ERIKS offered the baker an Air Optimisation Program, in five slices.
The first ‘slice’, an Air System Audit, looks at the customer’s compressed air system: its layout, condition, working pressure and types of compressor employed. This provides a clear picture of the current design and state of the system, and highlights any potential improvements for later consideration.
The second slice is an Air Leak Survey. Air leaks are a common problem with compressed air systems. But because they don’t directly affect compressed air end-use, they’re a problem which is often overlooked or ignored. Rather than air pressure being reduced at the point of use due to the leak, the compressor simply works harder to generate more pressure to compensate for the leak.
Which of course uses more energy.
Under pressure to save
The third slice of the Program is Repair.
Stopping leaks delivers immediate savings by reducing the volume of air required. This stage also assesses the opportunity for turning down the system supply pressure.
Although many systems operate at a higher pressure, most pneumatic equipment will operate effectively at just 5 bar. Reducing the pressure not only reduces the amount of energy required to generate it, but may even enable a reduction in the number of compressors required.
In this customer’s case, reducing the pressure has cut the number of operating compressors from three to two. But with three compressors still available, their use can be rotated, which reduces maintenance and extends their service life.
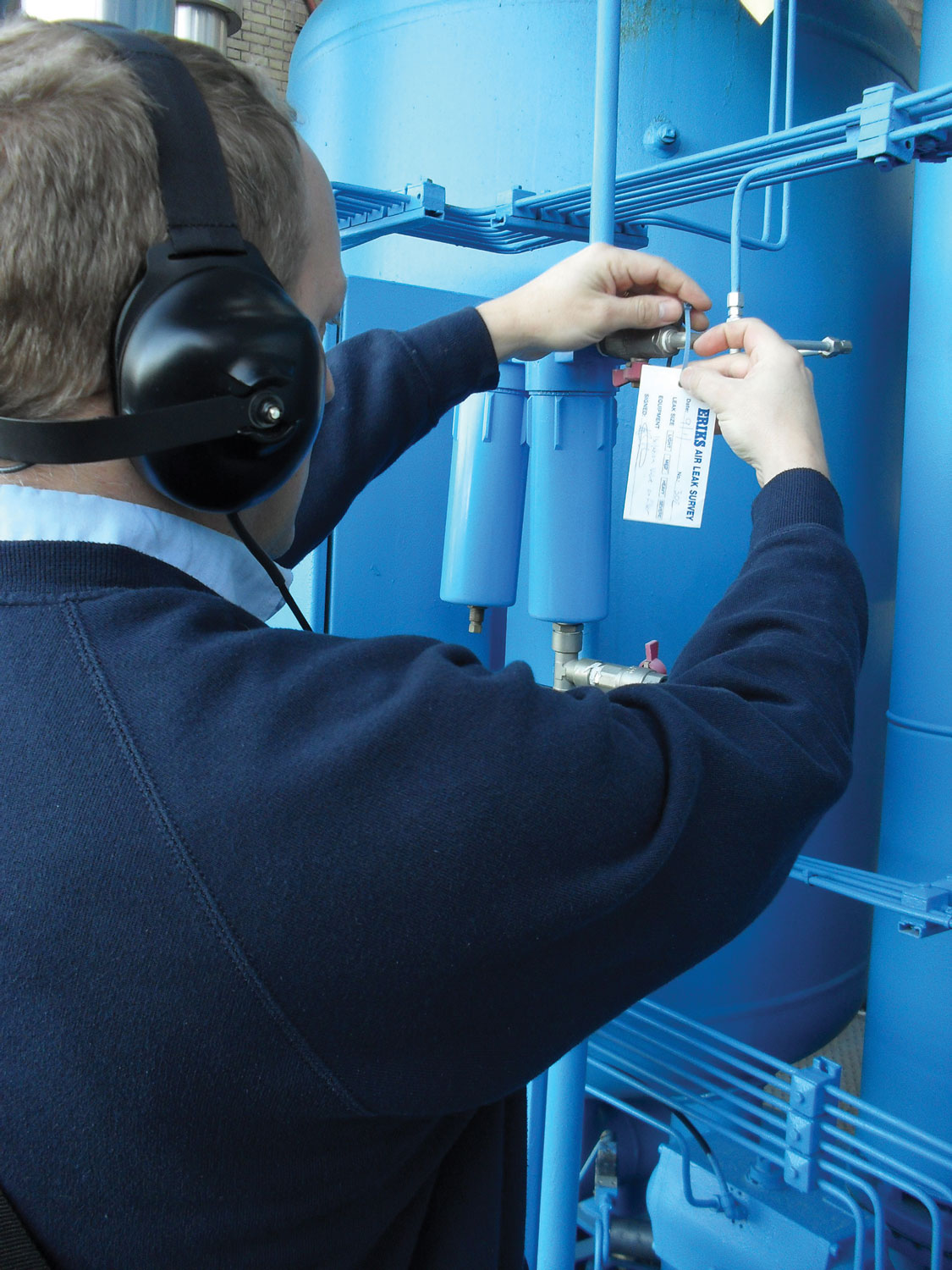
Bread and butter
With all three ‘slices’ now complete, the customer has realised annual savings of £112,560 [see box-out for details] and is planning to move on to the third and fourth stages of the program:
- Monitoring Ongoing Consumption – involves installation of flow meters to identify real-time consumption, highlight unexpected increases, and provide warning of leaks
- Introducing Innovations – together with the customer, ERIKS will consider and assess equipment and installations which can reduce compressed air consumption and help achieve additional savings. These are likely to include pressure boosters, reduced pipe sizes, and moving valves closer to cylinders.
Helping customers to save energy and costs – and to reduce their carbon footprint – through compressed air optimisation. That’s ERIKS bread and butter. So why not use your loaf and get in touch?
Air Optimisation for optimum savings
Following the first three stages of the ERIKS Air Optimisation Program, the customer is already saving £112,560 p.a., calculated as follows (based on an average energy cost of £0.27 per kW/hr):
Original system
- System pressure: 7.7 bar
- 3 operating compressors with 65% average use
- Running at 85% efficiency
- [Based on 2 compressors running 24/7/365, and 1 back-up compressor cutting-in several times a day]
Optimised system
- System pressure: 6 bar
- 2 operating compressors – cost-saving: £29,760 p.a.
- 1 back-up unit, 40% average use (Now not required) – cost-saving: £82,800 p.a.
- TOTAL COST-SAVING: £112,560 p.a.
For more information on Flow Control solutions and to get in touch with one of our ERIKS Pumps Specialists or Valve/Flow Control Engineers, please contact your local ERIKS Service Centre, who will be happy to discuss your options.
#ERIKS #LetsMakeIndustryWorkBetter #CompressedAir #AirOptimisation #EnergySavings