In this article
Engineering the perfect working environment
The speed with which customer orders can be fulfilled is an essential criterion when measuring the success of most warehouse operations. What is often overlooked, especially in major retail warehouses, is the impact that this can have on staff. Many of them walk ten or more miles every day, are expected to meet tough pick/hour targets and often have to work in conditions that are generally considered as being far from ideal.
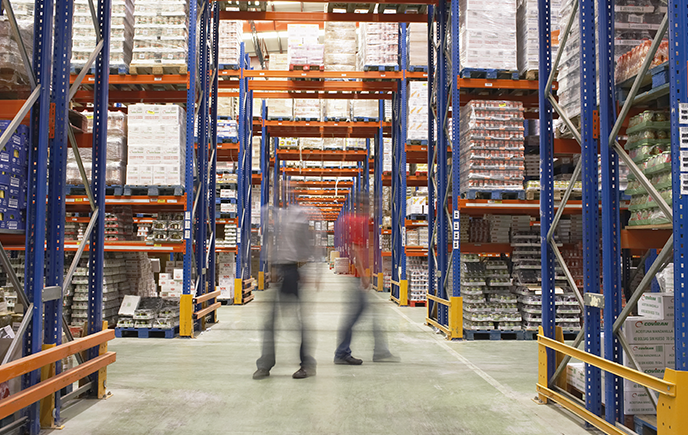
At ERIKS, with our long experience of managing industrial warehouses and supply chain operations, we have an excellent understanding of the challenges of balancing employee safety and job satisfaction with the demands of customers for fast, accurate and reliable deliveries.
That’s why, when designing our new Oldbury Fulfilment Centre of Expertise, we gave careful consideration to ways in which we can use the latest technologies to create a perfect blend of working environment and an exceptional customer experience.
Pick-times, storage locations and building amenities
It may sound obvious but one of the most effective ways of reducing the distance that staff walk each day is simply to build the stock control system around them. At our new centre, we’ve installed 21 vertical lifts and storage towers, linked to a network of over 400m of high-speed conveyors. This fully automated system allows the correct products to be selected and delivered to team members waiting at centralised packing stations; staff fatigue and stress is significantly reduced, while allowing us to pick up to xxx items per hour with a dramatic 30% improvement in pick-speeds.
Fulfliment Centre of Expertise image gallery
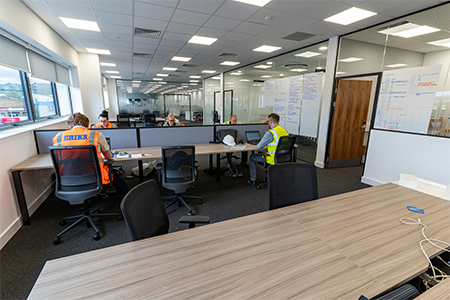
FCE Office Space
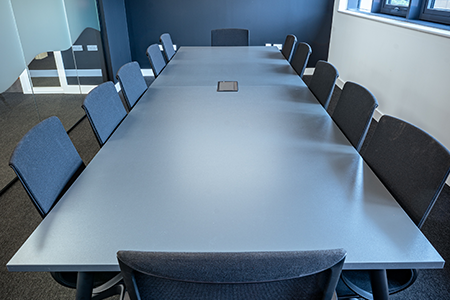
FCE Meeting Room
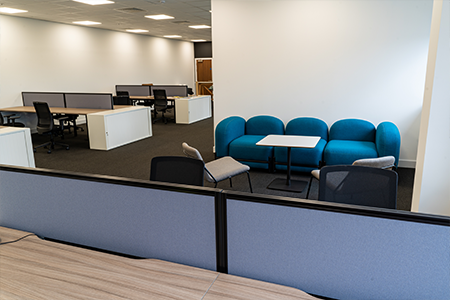
FCE Breakaway Area
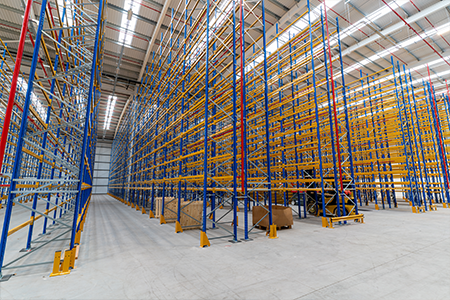
Warehouse Vertical Storage
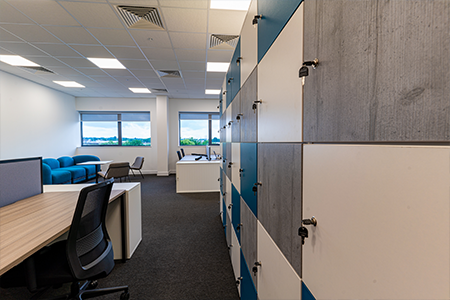
FCE Personal Storage Area
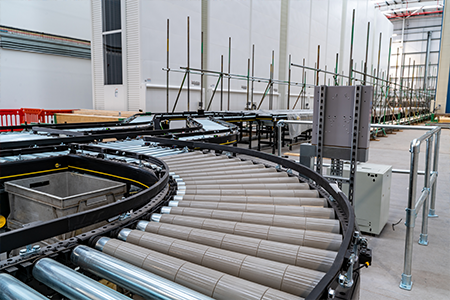
High Speed Conveyor System
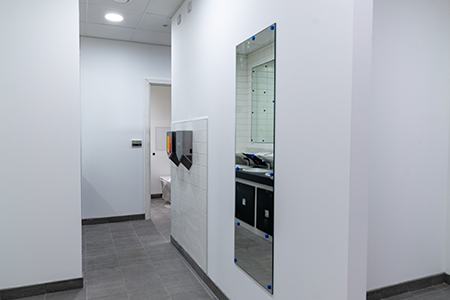
FCE Restroom Facilities
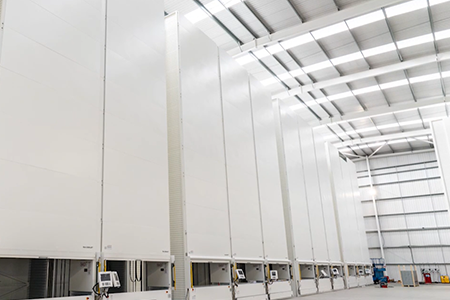
Vertical Lean Lifts
One of the frustrations for both customers and fulfilment centre teams are incorrectly picked and delivered orders. It is generally considered that a good error-picking rate is less than 0.2%. Although this may sound low, in means that for every 1,000 orders there will be two that result in unhappy customers and consequently frustrated fulfilment centre staff. In our view, that’s two too many.
Our goal at our new Oldbury Fulfilment Centre of Expertise is consistently to reach 100% pick-accuracy. To achieve this, we’re using the latest Industry 4.0 technologies, integrated with advanced warehouse management software that in turn is linked to our company-wide ERP platform.
Vital to the system is the extensive use of tools such as pick-to-light, barcode scanning and check-weighing devices. These are, for example, used as part of our goods-in inspection and quality control process and then again at the picking and packing, and final despatch stations. The combined technologies ensure that only the products ordered through our supply chain enter our fulfilment centre, and that these match the required quality and quantity. By checking and monitoring each product at every stage we’re able to ensure that exactly the products ordered by customers are picked, packed and despatched.
One of the key advantages of our investment in advanced technologies is that it has allowed us to reduce pick times, with most products now being picked within an hour of order; with end-to-end traceability we’re able to ensure that each pick is both fast and accurate. This makes our Fulfilment Centre teams more productive and reduces their stress levels as they no longer have to deal with incorrect orders, picks or urgent returns. It also gives them more time, empowering them, for example, to be part of our continuous improvement process considering methods of improving our systems and customer-facing services still further.
The Oldbury Fulfilment Centre of Expertise is much more than just our latest and most advanced fulfilment hub. It is also our new UK headquarters, with over 1,100 m2 of light, open and energy-efficient workspaces, designed using the latest architectural and behavioural insights. Our goal is to create an environment where our specialist teams can develop novel ideas and innovative solutions that strengthen our support for customers, while bringing a fresh approach that resolves complex supply chain and manufacturing challenges.
Our new Oldbury Centre represents a significant investment for ERIKS. It makes a strong statement of intent about the importance and value that we place on all our customers, employees and stakeholders, and provides the critical foundations that will support future success and prosperity.
For more information or to place an order please contact your local ERIKS Service Centre today or alternatively, CLICK HERE to buy directly from the ERIKS Webshop.
#FCE #Fulfilment #FulfilmentCentreofExpertise #Engineering #Technical #Warehouse #Automation #Smart #Digital #Technology