In this article
The energy crisis and supply chain disruption
In recent months, the cost of energy for manufacturing and process companies has risen significantly. As recently as April, the cost of gas per therm, which had been stable for some time, was under £0.50; by October, however, the cost had jumped to over £2.50 per therm. That’s a staggering 400% increase in gas prices in just six months; a similar, although not quite so dramatic, situation is now taking place with oil prices, which have topped $80 a barrel for the first time in three years.
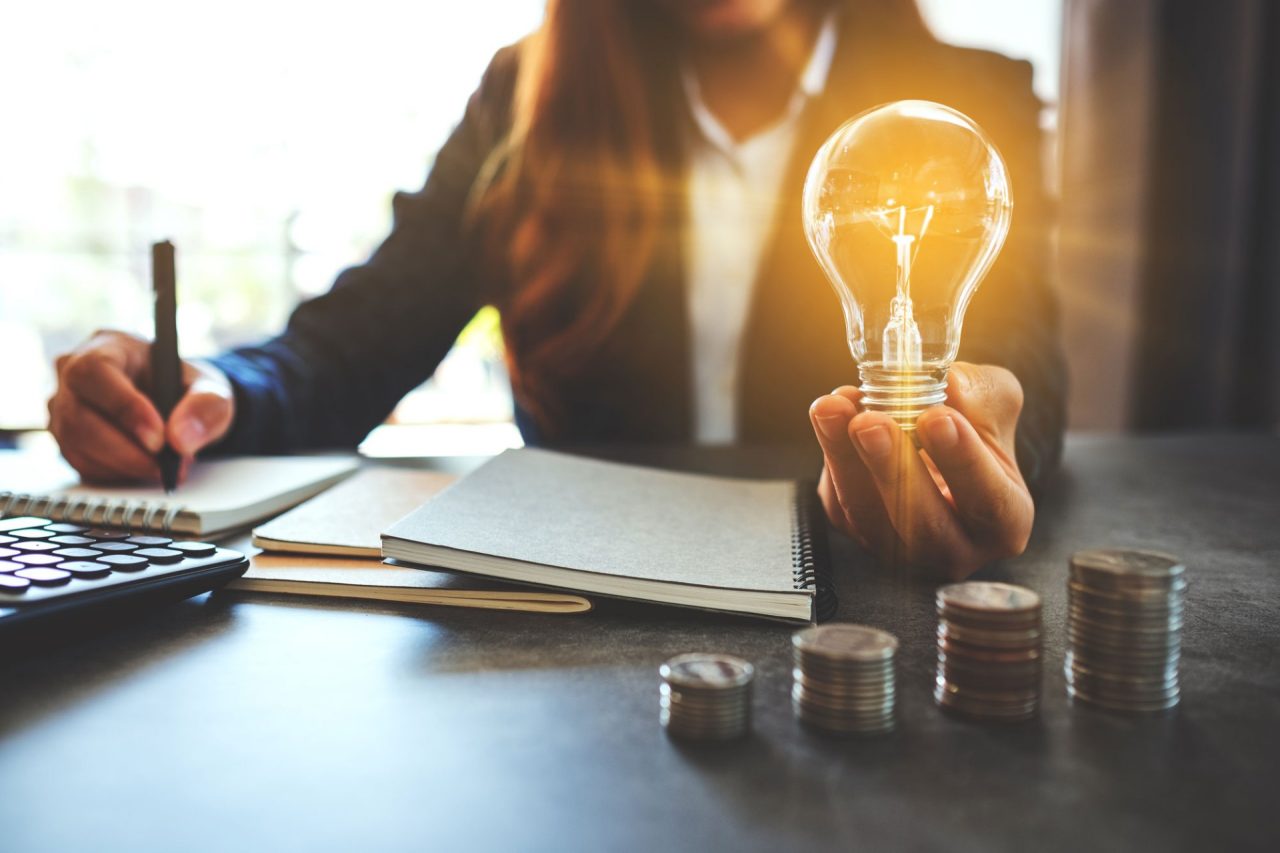
As a result, industrial companies that are dependent on gas or electricity for powering their manufacturing operations find themselves in a situation where their operating margins are being increasingly squeezed. We’ve already seen factories being forced temporarily to close or reduce their output. These include the fertiliser manufacturer, CF Industries, which halted production at its two plants in the UK for several weeks, while steelmakers have had to pause production during hours of peak electricity demand.
Predictions from industry analysts are that costs will rise still further in the coming months, as seasonal demand from consumers and industry starts to take effect. Longer term, with the collapse in a growing number of UK energy suppliers, rising global demand for gas and oil resources, an increasingly unstable geo-political environment and a growing climate crisis, the halcyon days of cheap energy may be long gone.
The need for energy efficiency in manufacturing
Although it’s the big energy users – chemicals, steel and glass – that are making the headlines, the rapidly rising cost of energy is hitting all manufacturing companies. Although few companies can do much to mitigate these supply costs – especially as they do not share the same price-cap protection enjoyed by consumers – there are ways of reducing energy consumption, which can offset much of the pain and protect businesses against higher energy costs in the future.
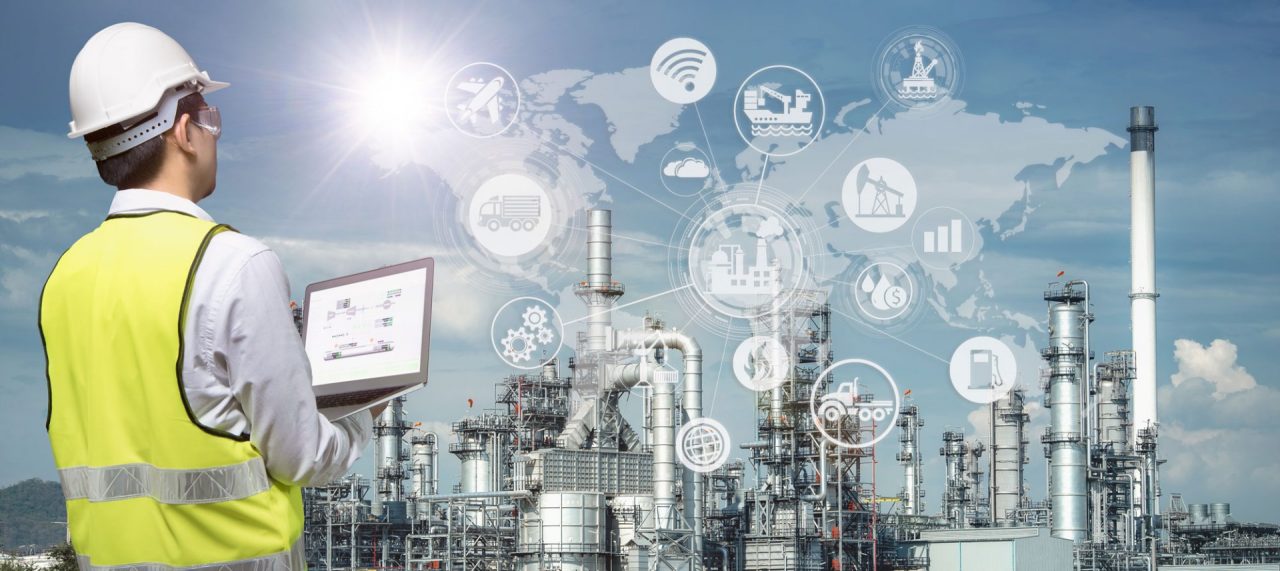
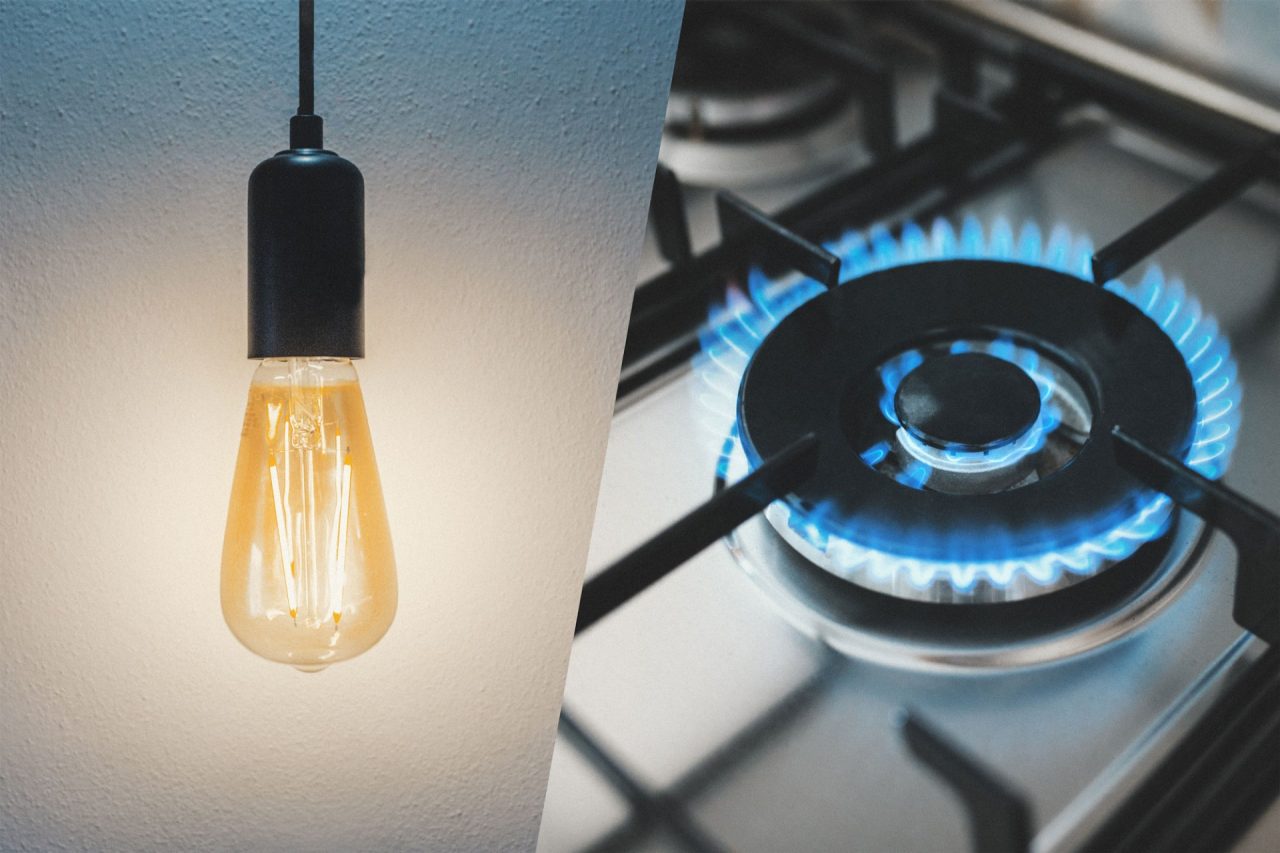
It has become common practice to specify energy efficient equipment whenever new plant and machinery is required. Similarly, there has been growth in the adoption of devices such as variable speed drives for motors, fans and pumps, of heat recovery systems for large air compressors, and in measures that minimise heat losses from industrial buildings.
In many respects, however, the easy steps have been taken. Realising further significant savings requires a far more radical approach to the way in which energy-intensive production and process operations are carried out.
For example, most factories use large electric motors, many of which have been in place for anything up to thirty years. It’s worth noting that motors account for around 65% of all energy consumed in the manufacturing sector and although older motors may have been considered state of the art at the time they were installed, technology (and legislation) has advanced considerably in recent years. This is especially true in terms of energy efficiency, so that replacing a typical 30-year-old 110kW motor with a modern equivalent will save you around £5,000 a year – and as energy prices rise, so too will the potential saving.
However, it is important to look at individual plant assets in isolation and as a system, older ancillary equipment such as pumps, drives and controls are often forced to operate beyond their optimum efficiency rate as other parts of your operation are upgraded or reconfigured. This can have a significant impact on performance and energy efficiency pushing up operating costs. Reviewing their operation with a holistic view of the complete manufacturing cycle is therefore important when identifying opportunities for process optimisation.
This is where the experience of an external industrial specialist such as ERIKS can be beneficial, as we can bring a fresh perspective and dedicated skills that can help both to identify aging inefficient assets that need replacing and ways in which process operations can be optimised.
This might be something as simple as checking the lagging on heating systems – even a small area of failed insulation can result in a significant energy saving over time – or require a deeper dive into the configuration of automation and control platforms that with simple changes can provide savings. We have saved significant amounts of energy and improved productivity by evaluating and updating these systems.
Building a resilient supply chain
Reaching the goal of true energy efficiency requires time, resources and investment. Nonetheless, the goal is worth reaching as the savings can be significant and will contribute directly to your bottom-line profits.
A critical aspect that can often be overlooked is the need for a resilient supply chain. At a time when most industrial companies are struggling to recruit skilled staff, or have adopted a policy of outsourcing non-core production activities and services, the need for dedicated supply relationships with specialised external partner organisations has never been greater if real efficiencies and savings are to be made.
At ERIKS, we provide a range of dedicated engineering, maintenance and customer support services. These range from condition monitoring and predictive maintenance to asset repair and upgrade with impartial advice, and are designed to help customers improve productivity and profitability, by extending the product lifecycles and decreasing total cost of ownership, especially through improved energy efficiencies; we typically deliver £2 million worth of savings for our customers each and every month.
Just as important is our ability to provide supplies of critical parts and components, even at times when global supply chains are facing severe dislocation. This has been especially true in the last few years, when we’ve seen considerable disruption from the Covid pandemic, geo-political instability, severe weather events and chaos originating from specific events such as the blocking of the Suez Canal by the container ship the Ever Given. Throughout, we’ve maintained a robust and resilient supply of critical parts and equipment to our customers in the UK and Europe.
Building a resilient supply chain
Reaching the goal of true energy efficiency requires time, resources and investment. Nonetheless, the goal is worth reaching as the savings can be significant and will contribute directly to your bottom-line profits.
A critical aspect that can often be overlooked is the need for a resilient supply chain. At a time when most industrial companies are struggling to recruit skilled staff, or have adopted a policy of outsourcing non-core production activities and services, the need for dedicated supply relationships with specialised external partner organisations has never been greater if real efficiencies and savings are to be made.
At ERIKS, we provide a range of dedicated engineering, maintenance and customer support services. These range from condition monitoring and predictive maintenance to asset repair and upgrade with impartial advice, and are designed to help customers improve productivity and profitability, by extending the product lifecycles and decreasing total cost of ownership, especially through improved energy efficiencies; we typically deliver £2 million worth of savings for our customers each and every month.
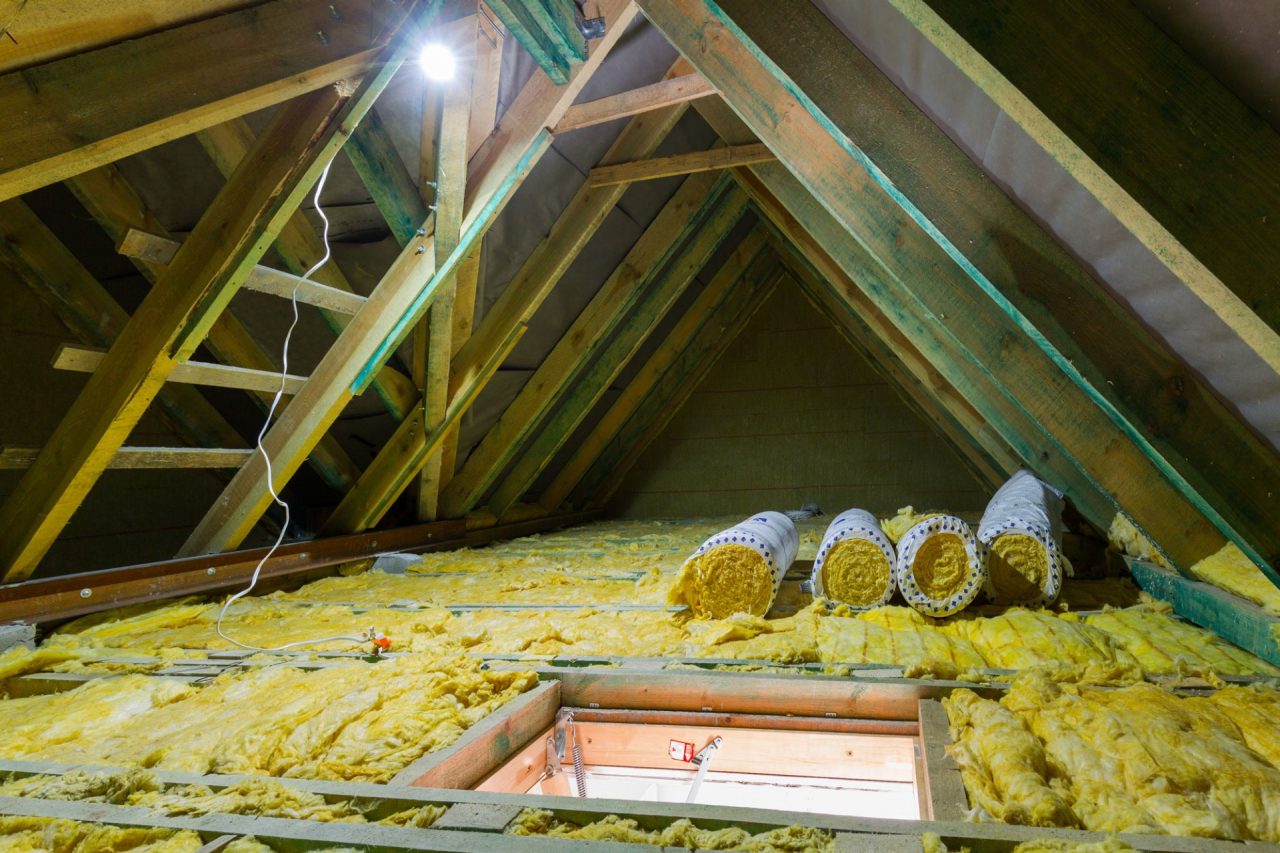
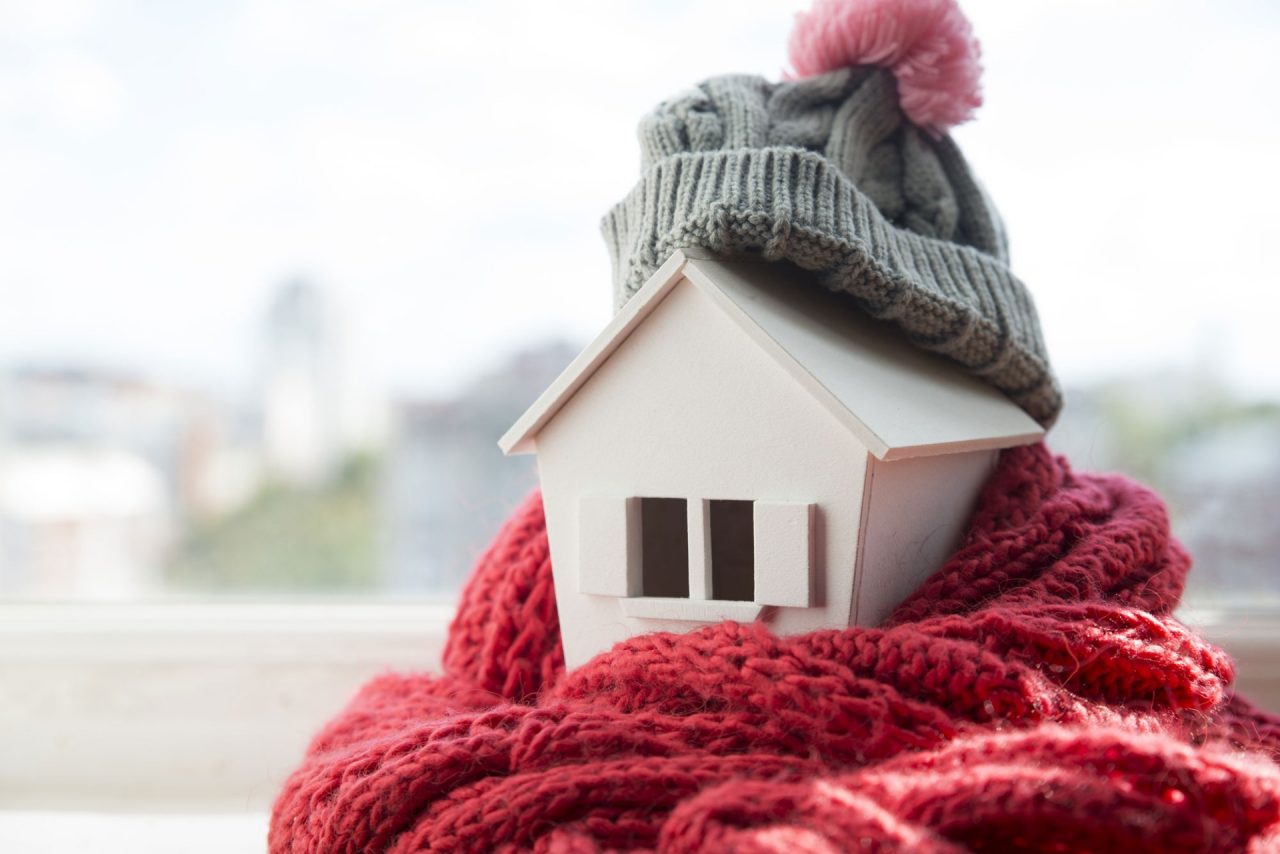
Just as important is our ability to provide supplies of critical parts and components, even at times when global supply chains are facing severe dislocation.
This has been especially true in the last few years, when we’ve seen considerable disruption from the Covid pandemic, geo-political instability, severe weather events and chaos originating from specific events such as the blocking of the Suez Canal by the container ship the Ever Given. Throughout, we’ve maintained a robust and resilient supply of critical parts and equipment to our customers in the UK and Europe.
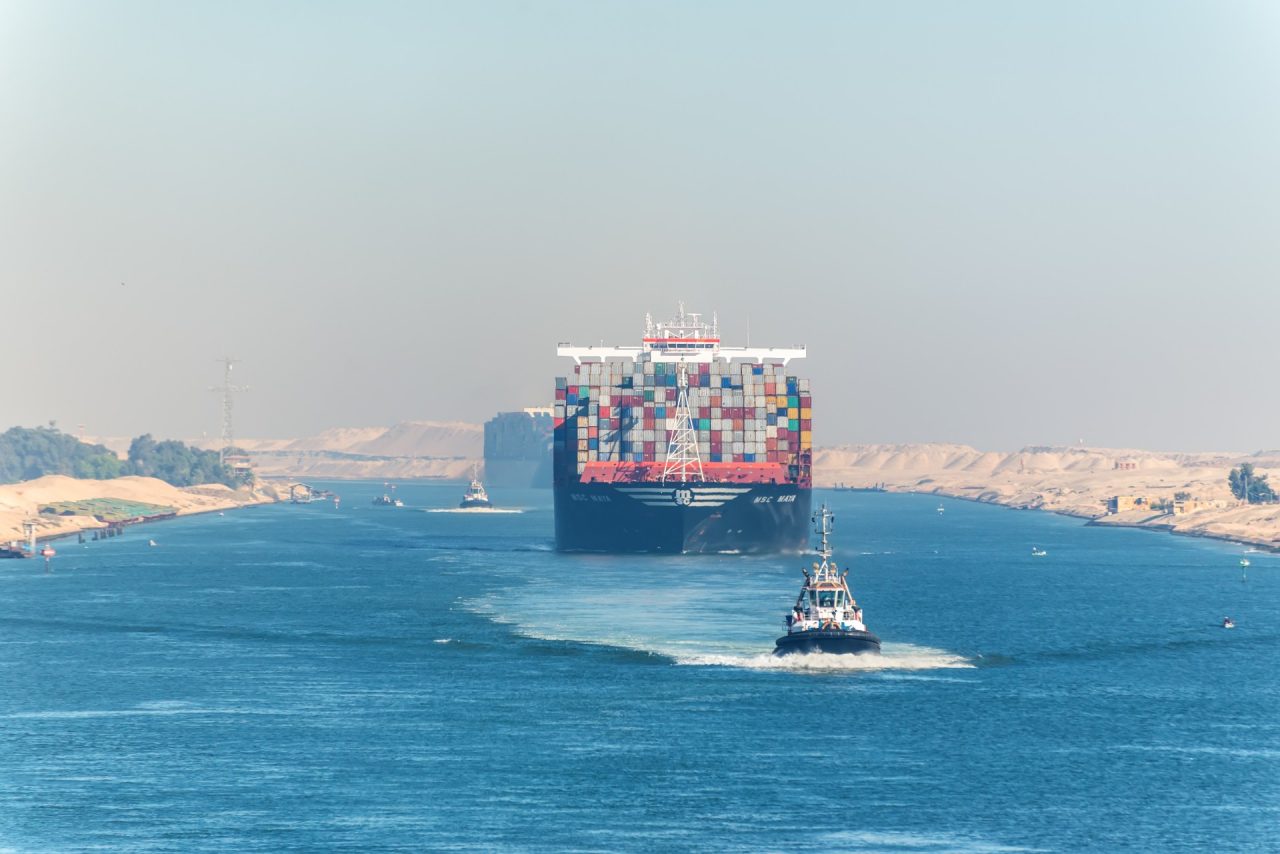
Minimising industrial risk
As Benjamin famously said, only two things are certain in life: death and taxes. We can perhaps add to this, certainly for the foreseeable future, as it seems highly likely that both energy prices and supply chain shocks will continue to be an ever-present factor in our lives.
As business leaders we need to do everything we can to mitigate risk. Partnering with a specialised industrial services provider can be a key aspect to this process, helping to eliminate uncertainty and minimise risks, especially in the business-critical areas of energy and supply chain management.
To learn more talk to one of our industry specialists today.
More about the Energy Crisis...
We have more insights and information we can offer:
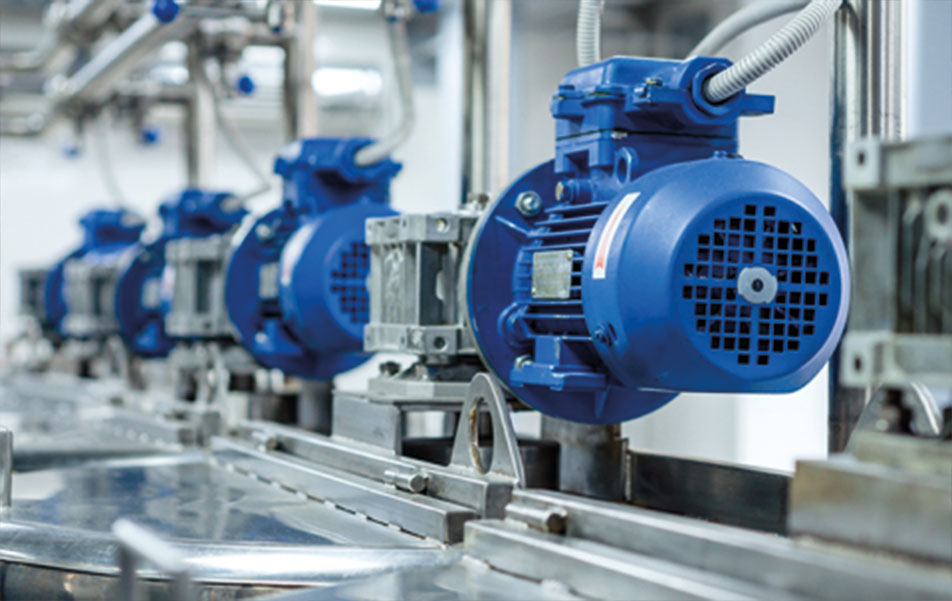
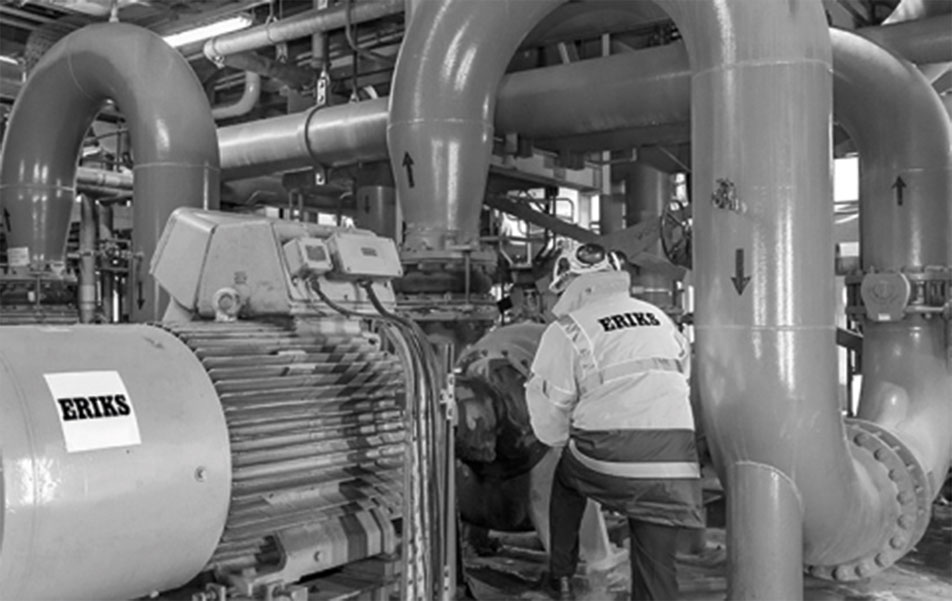
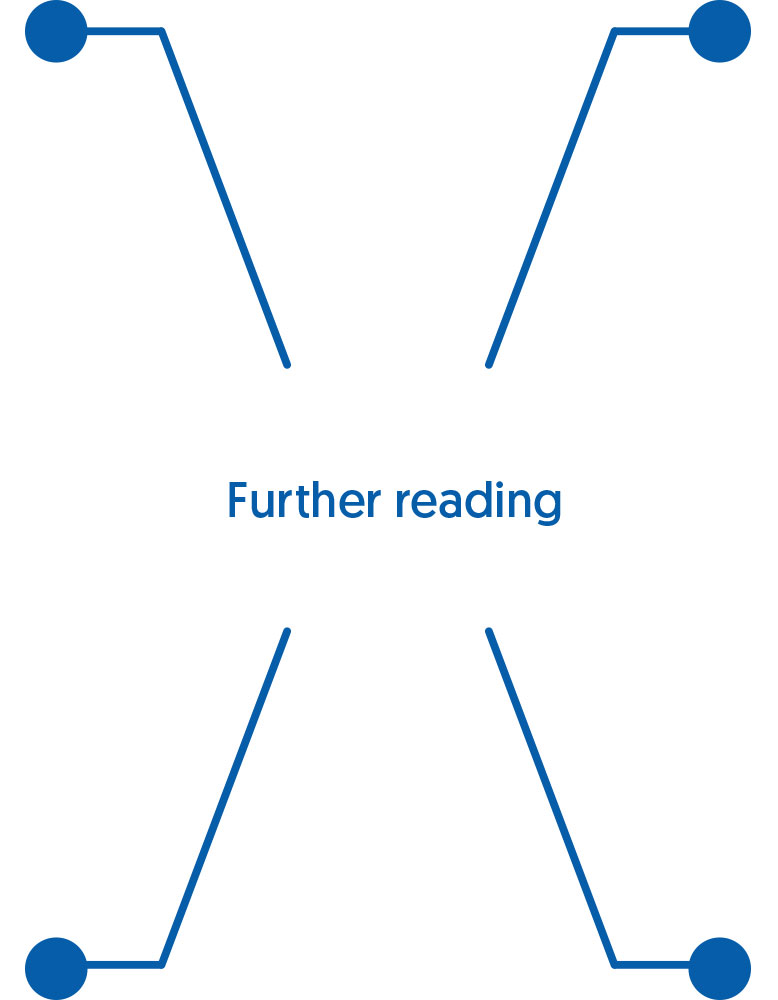
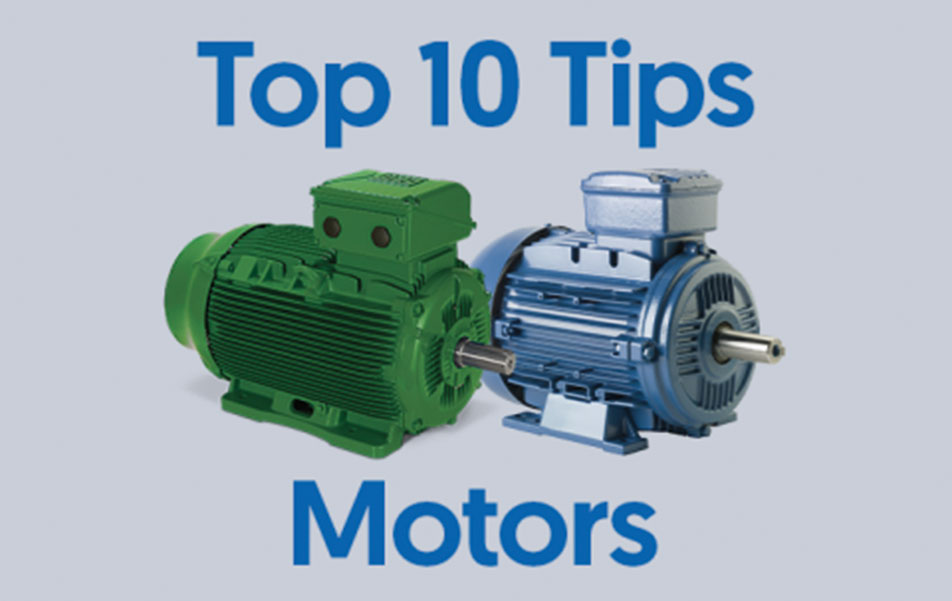
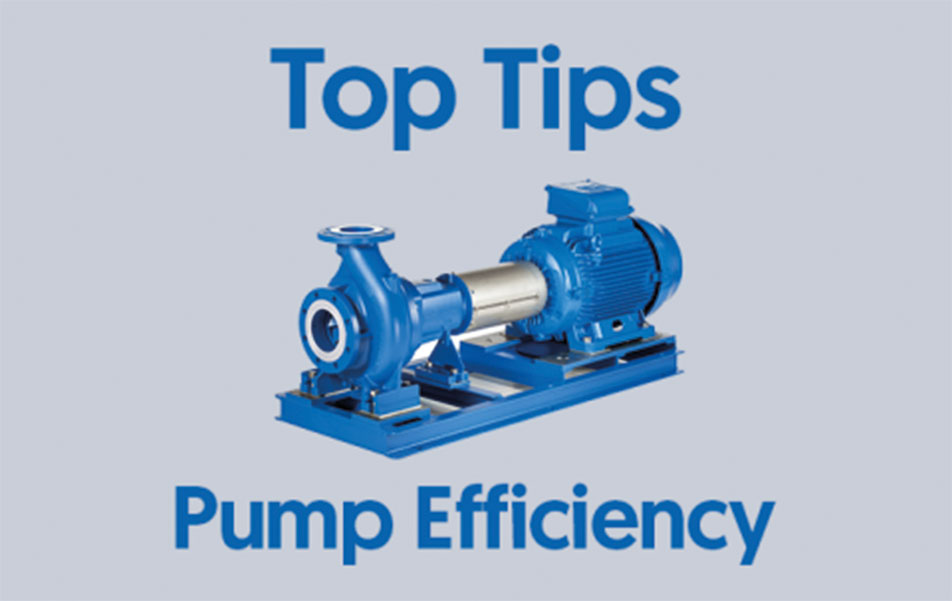
For more information on Power Transmission solutions, get in touch with one of our ERIKS Pump Specialists or Application Engineers, please contact your local ERIKS Service Centre, who will be happy to discuss your options.
#ERIKS #LetsMakeIndustryWorkBetter #Engineering #SupplyChain #EnergyCrisis