In this article
When what goes around doesn't come around
Bearing failures on a water company’s rotary aerators were coming around far too often. So they asked ERIKS for help to stop their maintenance engineers going round in circles.
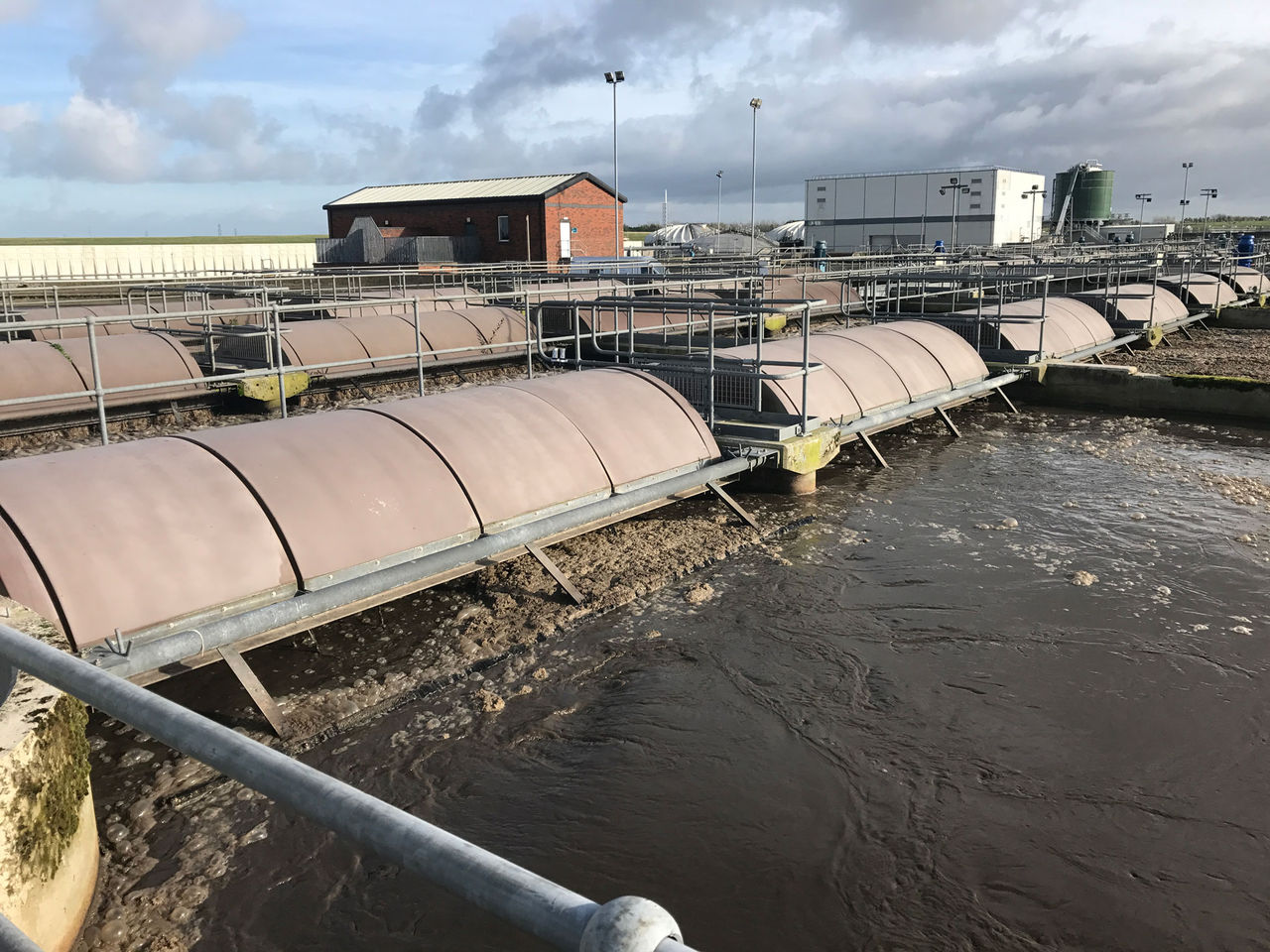
Rotary aerators are a key element of the wastewater treatment process. By continually and slowly stirring the sludge in the aeration tanks, they introduce oxygen to start the aerobic biodegradation process. Most treatment sites have several aeration tanks, but even if just one is out of action then the site’s capacity for effluent treatment is reduced. In the worst case, the site can be overwhelmed, leading to the release of untreated effluent into watercourses.
One site in the North-West was experiencing unacceptable levels of downtime due to repeated shaft bearing failures that support the rotating blades.
In addition, each time the bearings were replaced, the need for a large mobile crane to lift the heavy shaft meant lengthy advance planning was required – extending the downtime and creating a significant Health & Safety challenge.
ERIKS, together with supplier partner Timken, decided the sludge wasn’t the only thing that needed stirring up.
The same but different
Each time a bearing failed, the maintenance team installed a like-for-like replacement. This kept the initial price of the bearings down but – with failures as frequent as every six months – the Total Cost of Ownership was frighteningly high.
ERIKS’ first step was to investigate all potential failure modes, to discover whether a different type of bearing might achieve a longer service life.
It quickly became clear that bearing contamination with water and solids was the cause of failure. In the tough operating environment of the aeration tanks, the bearings’ standard sealing arrangement was simply not up to the job.
In consultation with Timken, ERIKS proposed replacing the standard bearings with the Timken® Split Cylindrical Roller Bearing Housed Unit – to solve not just one problem for the customer, but two.
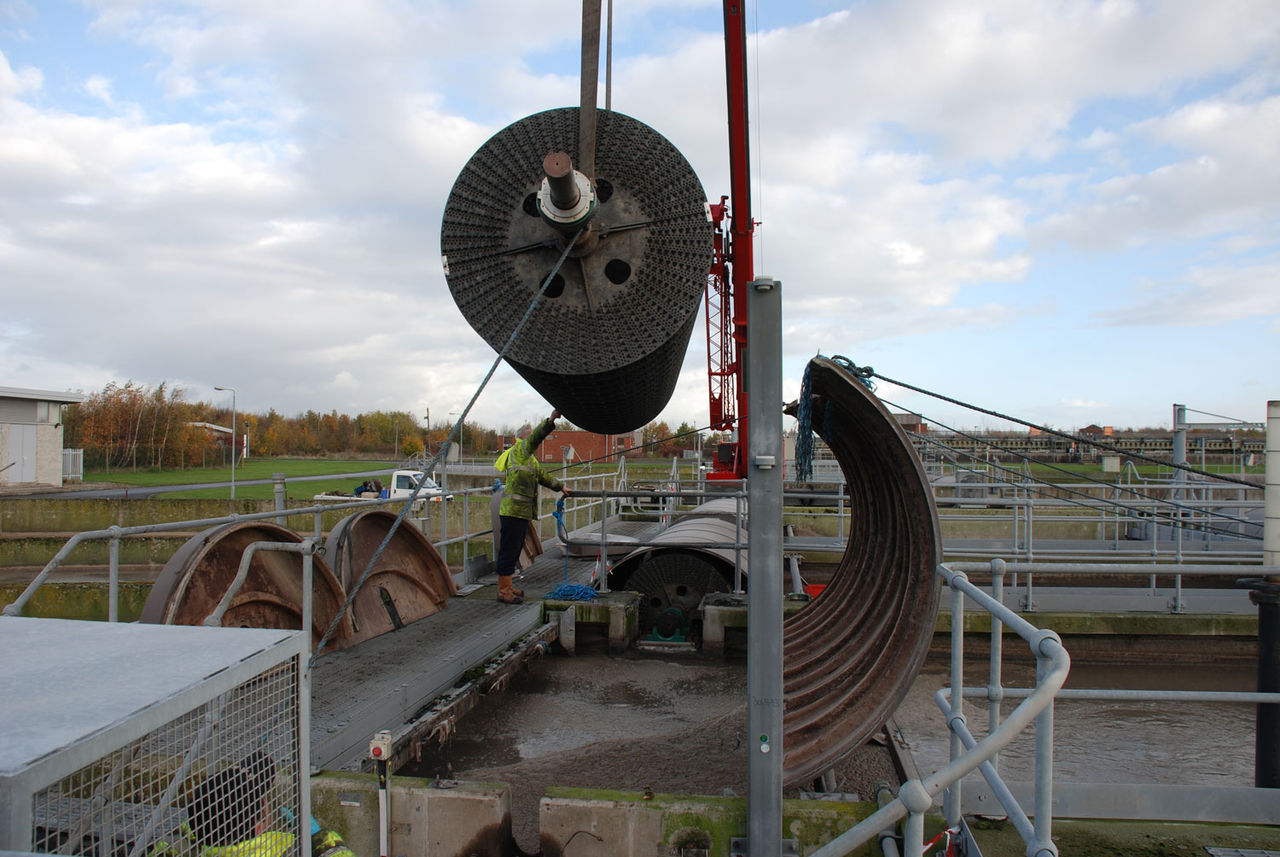
The seal that can swim
Timken’s sealing solution provides the customer with a superior seal arrangement. A single lip seal with a garter spring and retaining plate ensures optimum protection against water and solids ingress, for reduced bearing failure and a longer service life. In fact, the Split Cylindrical Roller Bearing Housed Unit can run fully submerged at a depth of up to 1m its entire lifetime. And while the standard bearings used previously by the customer were failing in as little as six-monthly intervals, the Timken solution has been operating in identical applications for as long as 15 years without any failures.
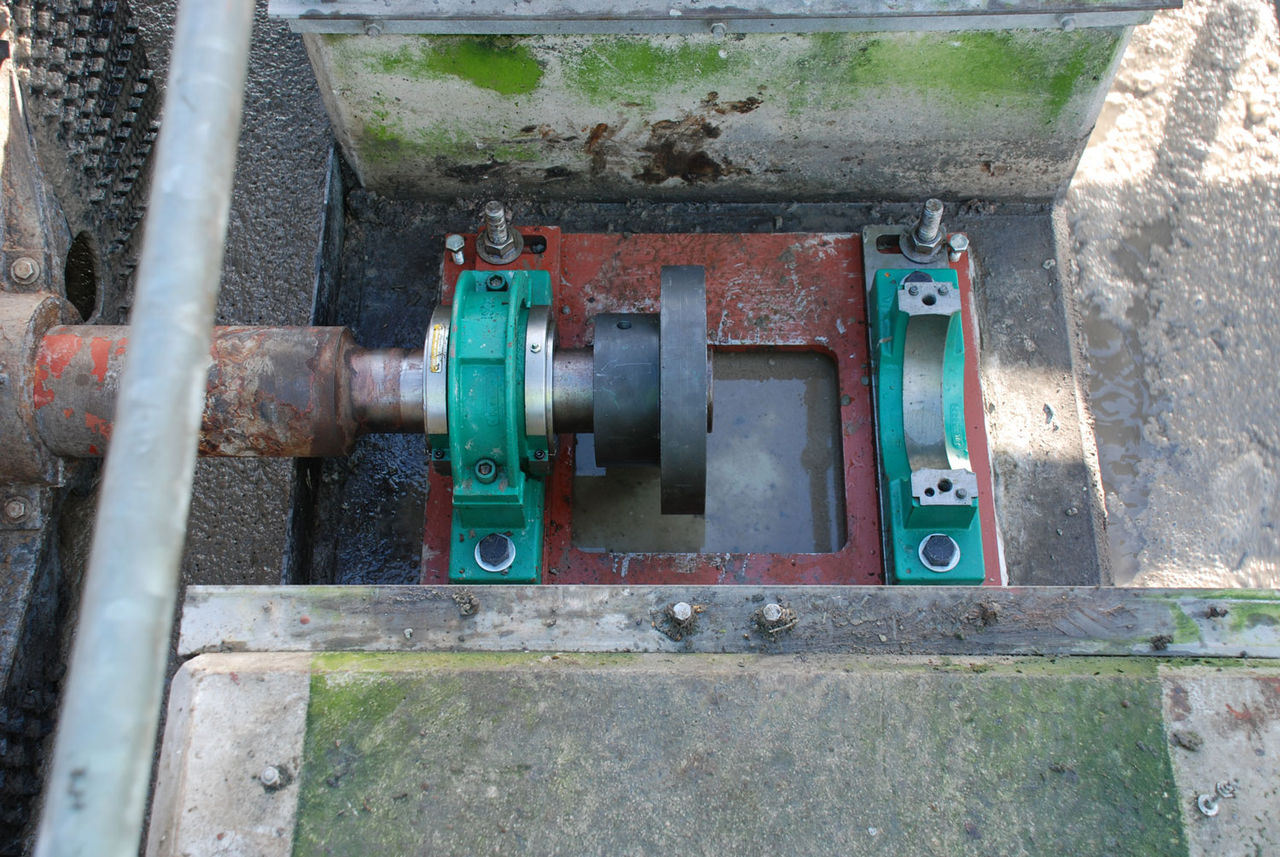
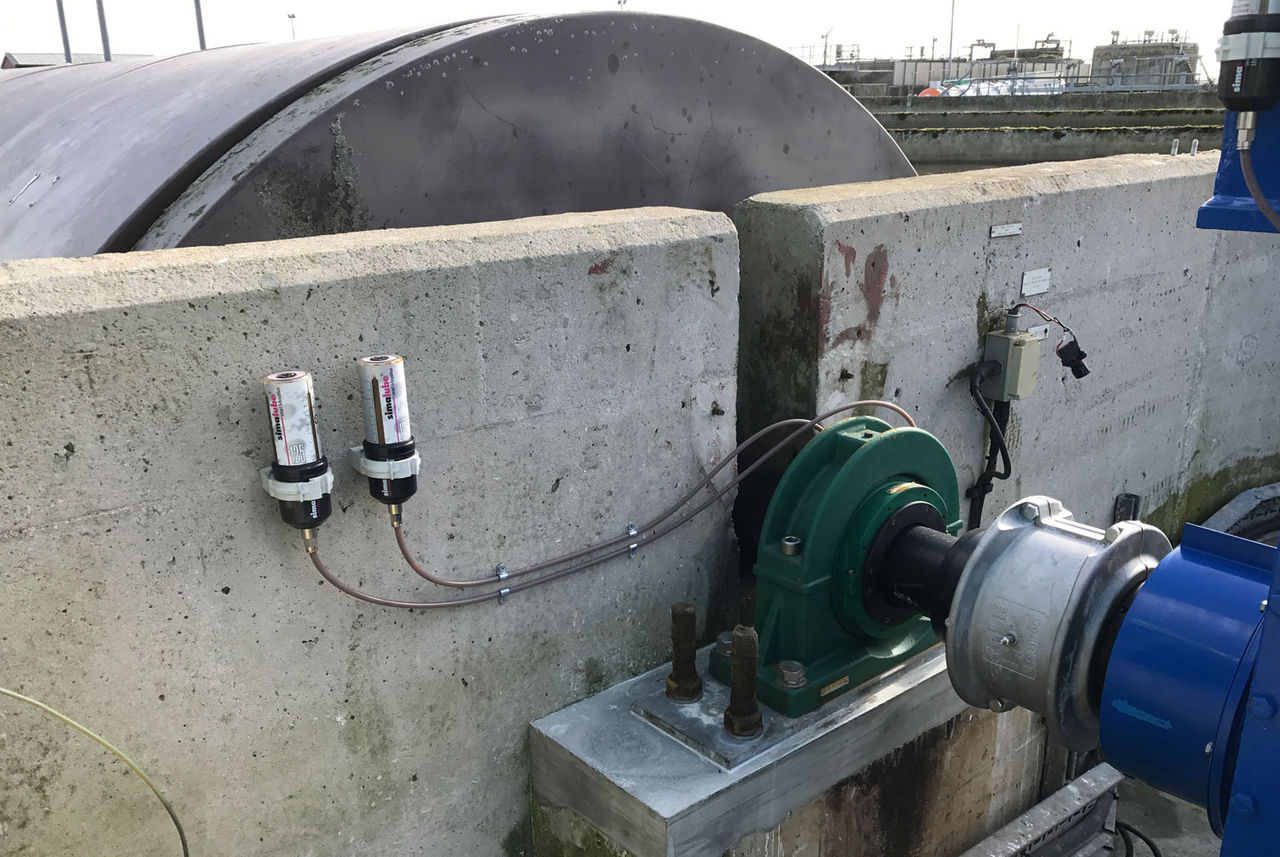
A split decision
It wasn’t only the bearing failures which were causing problems for the customer. It was also the difficulty of removing the failed bearing and fitting a replacement.
Removing a standard bearing requires lifting the whole aerator shaft assembly out of the aeration tank, requiring the shaft to be disconnected from the drive so the bearing can be slid off the shaft. With a complete unit weighing around 25 tonnes, that’s not an easy task.
The Timken split bearing eliminates the problem by making it easier, quicker and safer to remove the bearing. Even some so-called split bearings have only a split housing, which doesn’t solve the problem. But the Timken split bearing is split all the way to the shaft – so it can be removed and replaced with the shaft still in place. All that’s required is a jack to support the shaft while the work is carried out.
The result is a bearing swap-out that takes 1-2 hours rather than several days.
Seal of approval
Damaged or out-of-specification bearings With the standard, failure-prone bearing now replaced with the new Timken Split Cylindrical Roller Bearing Housed Unit, the customer is already seeing significant benefits.
The improved sealing arrangement means contamination has been virtually eliminated, leading to a significant reduction in downtime. This in turn reduces the risk of untreated effluent having to be released.
Long-term maintenance costs have also been reduced, thanks to the much longer service life of the new bearing.
And if and when a bearing does need to be replaced, the customer can expect a far faster, simpler and safer operation overall.
So they’ve quickly come round to Timken’s and ERIKS’ way of thinking.
For more information on Bearing Solutions and to get in touch with one of our ERIKS Specialists, please contact your local ERIKS Service Centre, who will be happy to discuss your options.
#Timken #ERIKS #LetsMakeIndustryWorkBetter #Bearings #WasteWater #TCO