In this article
Rocol make lubrication PFPEasy
Did you know that 70% of bearing failures are due to lubrication errors? And did you know that, surprisingly, it’s not always too little grease that’s the problem, but sometimes too much? Using a grease that’s unsuited to the operating conditions can be an issue too. Especially in more extreme operating environments. But whatever the initial issue, it’s almost always going to lead on to a much bigger and much more expensive problem – like bearing failure, unscheduled downtime, lost production, and bearing replacement. One way to make life easier is to change to PFPE greases – such as Sapphire Endure and new Sapphire Ultra from ROCOL.
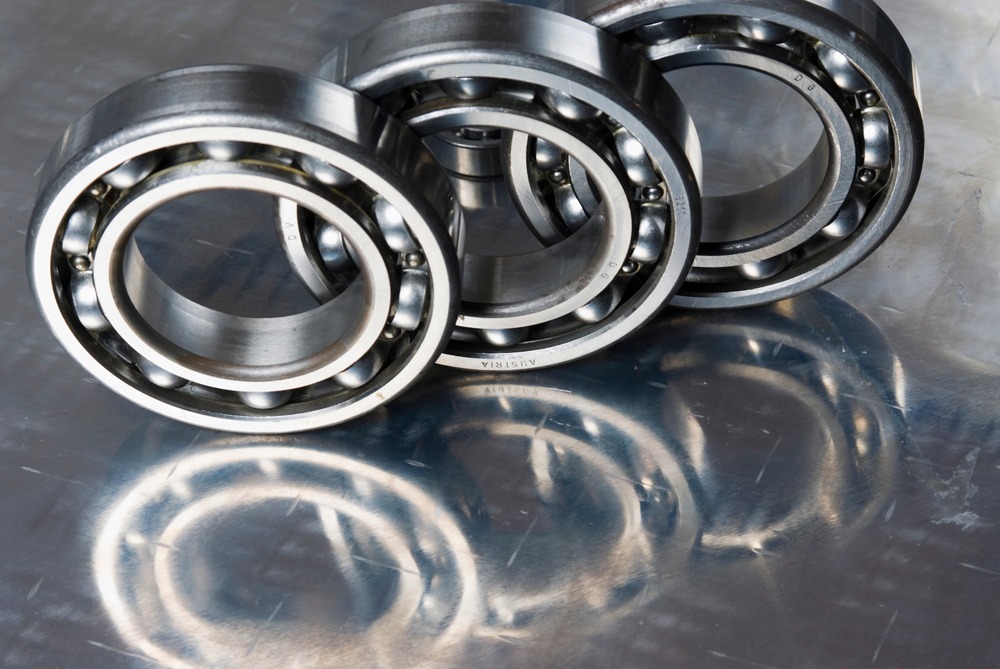
PFPEs – known as perfluoropolyethers if you want to impress people – are highly inert. When they’re used as the basis for a grease, this helps to make them highly resistant to things which can cause problems for non-PFPE lubricants. It also makes them less likely to cause problems for whatever they come into contact with, unlike more aggressive conventional lubricants.
ROCOL Sapphire Endure has been a great success with many customers in the food industry. They need an NSF-registered lubricant which can not only cope with very high temperatures, but also with wet conditions resulting from frequent washdowns.
Now, for customers in other, non-food industry sectors, there’s a new ROCOL grease available with similar qualities. But without the NSF certification and price premium.
The choice is yours
With two ROCOL PFPE greases to choose from, you can select the optimum lubricating solution for your application, your operating environment and your budget. And you’ll be safe in the knowledge that whichever lubricant you choose, you’ll be choosing all kinds of advantages over standard greases. Both ROCOL Sapphire Endure and new Sapphire Ultra are PFPE-based chemically inert greases.
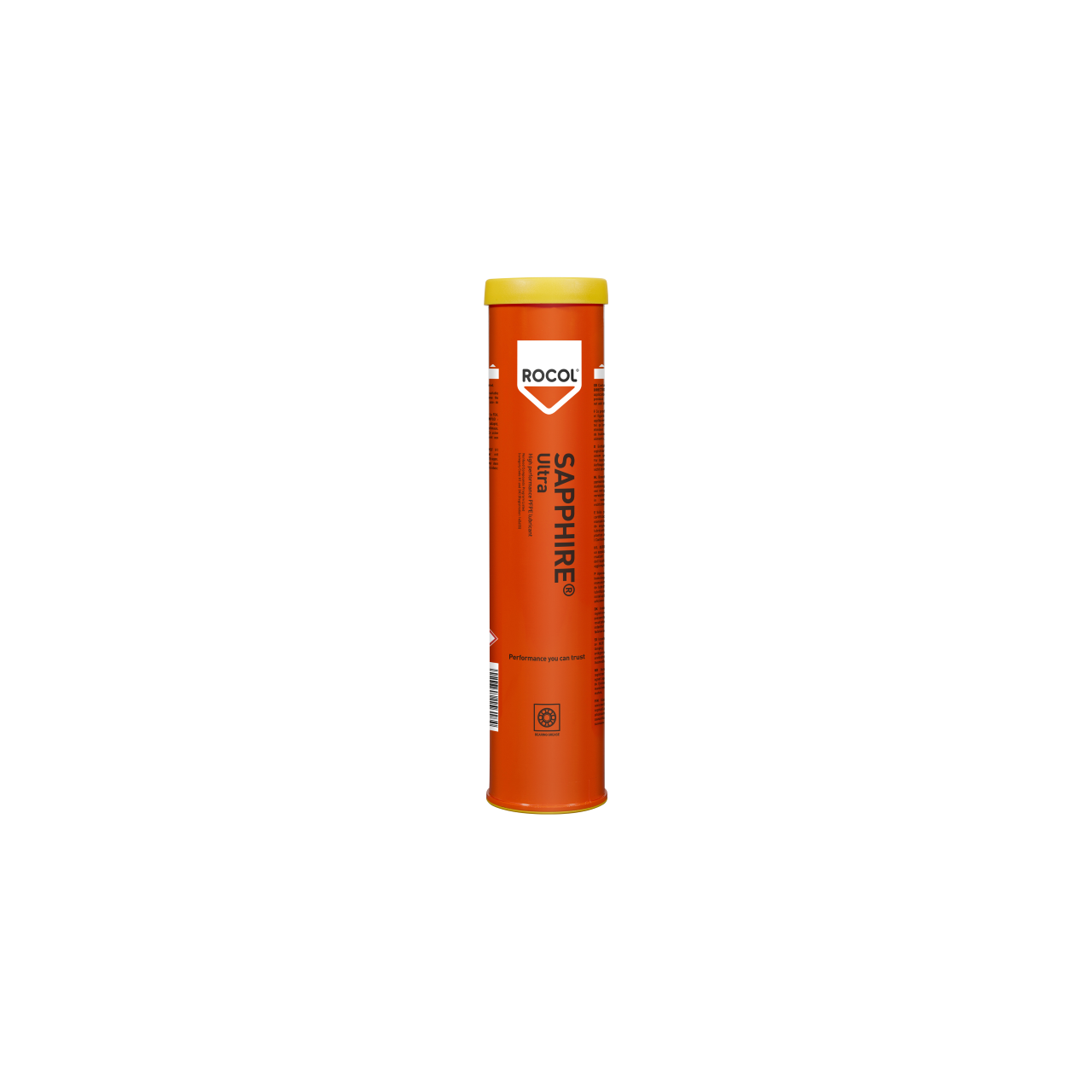
They’re also both far more resistant to washdowns than standard greases, which means grease has to be topped-up far less often. When a bearing does eventually need re-lubricating, it needs far less of Sapphire Endure or Sapphire Ultra than it would need of a standard grease.
Where around a third of a bearing needs to be filled with conventional grease for effective lubrication, only approximately a fifth needs to be filled when using one of the ROCOL Sapphire greases. That not only saves on the cost of lubricant, but – because the grease is less likely to be washed out (and there’s less to be washed out) – also reduces the likelihood and level of potential environmental contamination.
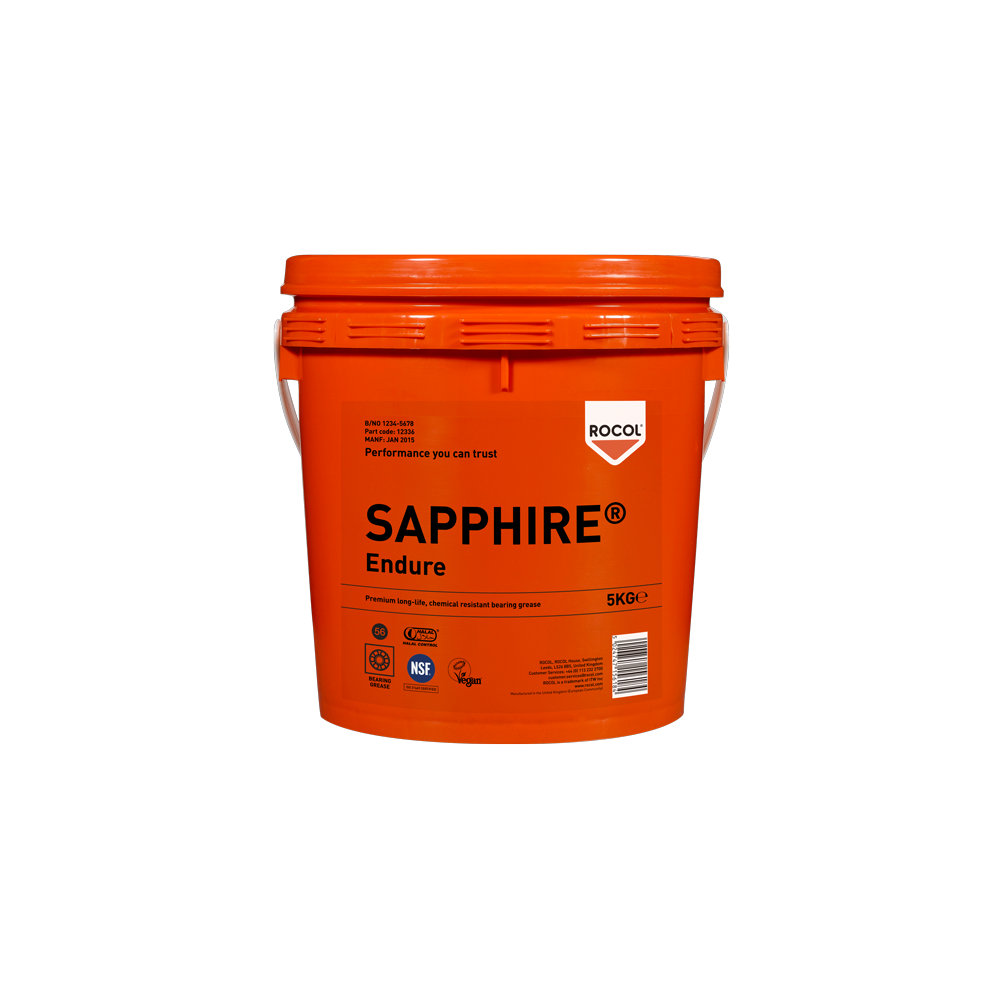
Baked-in temperature resistance
High temperatures aren’t found only in the food industry. For example, bricks get baked. And paint is dried in stoves. So across a wide range of industry sectors, lubricants can be subjected to very high temperatures.
Which means Sapphire Ultra doesn’t need NSF registration to be invaluable. Instead, it can be the go-to grease wherever operating temperatures rise as high as +280°C (or drop as low as -25°C), and where water, chemicals and steam are present.
For anti-friction and plain bearings, small gears, slides, pins, valves, plungers and screws, ROCOL Sapphire Ultra offers high temperature-, water-, chemical- and oxidation resistance, and all while using less lubricant.
That’s food for thought for more than just the food industry.
When problems melt away
A leading automotive component manufacturer was facing issues with rejection of components. Their powder-coating conveyor was operating almost continually, in temperatures of 240°C. The high temperature was causing base oil to separate from the lubricating grease used on trolley bearings, and to drip onto the conveyor track below.
By switching to ROCOL Sapphire Ultra – a non-melting grease with no drop point – the problem of separation and dripping was eliminated. At the same time, the lubricant’s exceptionally long service life extended the lubrication intervals, and reduced labour costs as well as downtime.
The customer’s Head of Operations described the benefits to their production process of the new lubricant: ‘After 4 months, we found our grease to be in good and sticky condition, with the lubricating film already forming inside the balls of the trolley bearings. Since then we’ve had no dripping issue, thus giving us a cost saving of almost 50% – or around £1,500 a year.’
For more information on Bearing Solutions and to get in touch with one of our ERIKS Specialists, please contact your local ERIKS Service Centre, who will be happy to discuss your options.
#Rocol #ERIKS #LetsMakeIndustryWorkBetter #Bearings #Innovation #Optimisation #Solutions #PFPE #Sapphire #Endure #Ultra