In this article
Going Spare Without a Strategy
Having spares available for your rotating equipment is only half the story. To reduce maintenance costs and downtime, you also need a spares strategy.
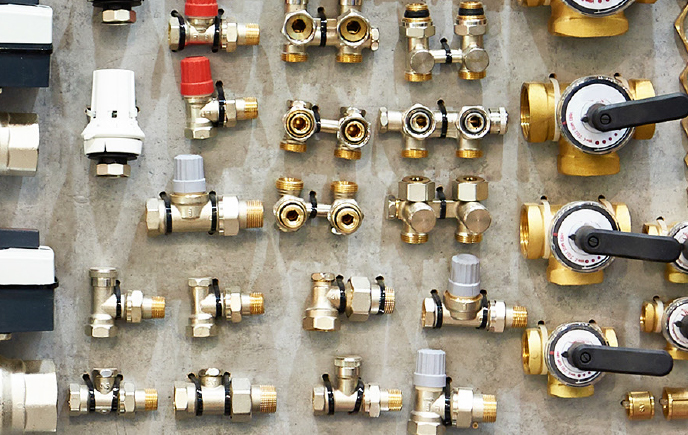
Reliability and maintenance costs are two key drivers of the unit cost of production. According to a study by Solomon Associates1 these should be targeted at 96% availability, with a maintenance cost of 1.4% of the plant replacement value.
A spares strategy for your rotating equipment, which identifies spares criticality and rationalises your engineering stores, is one way to achieve these targets. And it can even improve your Total Cost of Ownership.
All spares are not created equal
Are your engineering stores a pick and mix of spares for your rotating equipment, or an accurate reflection of the assets in your plant? Shelves filled with spares which are hardly ever needed aren’t a production resource but a waste of space. Especially if you lack enough of the critical spares which keep your plant running.
So clearly, your first step towards optimising plant availability should be to identify critical spares and their lead time for replacement. If you have only one standby replacement for a critical asset, and it has a six week lead time, for example, once you remove the asset from your stores you’re exposed to six weeks’ risk of a plant shutdown.
But that doesn’t mean you need a standby asset for your standby asset.
With the right experience and know-how applied to the task, you’ll know whether it’s possible, quicker and more cost-effective to repair, refurbish or replace. Knowledge of how equipment fails can also help you to maintain a stock of critical components (seals kit, bearings etc.) for critical assets. If your spares requirement is expertly assessed and carefully planned, the right components can provide the same risk mitigation as holding a replacement asset – but far more cost-effectively.
Longer, healthier life
An effective spares strategy should do more than help you keep your assets running. It should also help you keep them running more efficiently for longer. The equipment, industry and market knowledge and experience which ERIKS can bring to your spares strategy can do just that.
An ERIKS criticality assessment will not only identify which assets and spares are “plant stoppers”, but will also highlight equipment failure modes, to help with spares selection. After all, there’s no point in stocking a spare bearing if ERIKS’ experience shows it’s typically the seal that fails.
Better still, ERIKS’ spares knowledge means that if there’s a suitable seal out there which fails less frequently, we’ll know. And if there are two assets on your site which use the same seal, ERIKS will know that too: so you can avoid spares duplication and reduce your inventory.
By devising a lean but focussed spares strategy for your rotating assets, ERIKS can help you to hit the “sweet spot” between too few spares – preventing you from reaching that 96% availability target – and too many: which would increase your maintenance costs beyond the target of 1.4% of plant replacement value.
Storing-up trouble?
Even with the right spares strategy and inventory in place, you can’t forget about your spares until you need them. Just like assets on the plant floor, spares need maintenance.
Rotating parts in particular are susceptible to false brenelling if left in one position for too long, and should be rotated on a regular basis. Some component parts within rotating equipment also have a shelf life. An O-ring or seal, for example, will need replacing after 6-8 years, even if built-in to the asset.
So why not talk to ERIKS about your spares strategy and stores management? It will improve your asset reliability, lengthen asset life, improve your TCO – and mean all sorts of problems spared.
For more information on creating a spares strategy, contact your local ERIKS Service Centre, who will be happy to discuss your options.
#ERIKS #LetsMakeIndustryWorkBetter #RotatingEquipment #Strategy #Maintenance