In this article
Achieving your AMIS aims
For over 30 years, the MCP Consulting Group has been taking businesses on the Asset Maintenance Improvement System (AMIS) journey. Helping clients to move their maintenance organisation from “Chaos”, through “Control” to “World-Class”, it’s a journey recently undertaken by a large distillery, with the help and support of ERIKS Integrated Solutions.
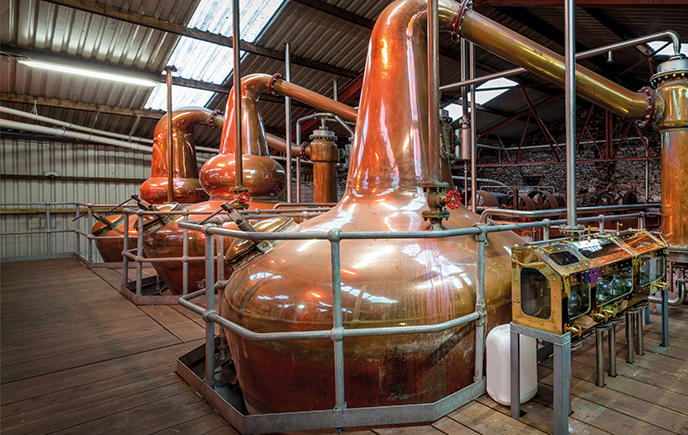
It’s been four years since the distillery decided to embark on their AMIS journey, with the aim of becoming a more streamlined maintenance organisation. This was partly driven by the fact that they wanted to be seen – and be – at the forefront of excellence.
AMIS is the industry standard for demonstrating the success of an organisation’s operations, through KPIs which measure maintenance and asset management performance on a consistent basis. It provides the largest database of benchmarks and key performance ratios of efficiency and effectiveness, worldwide.
To help ensure the best possible performance against these benchmarks, the distillers enlisted the support of ERIKS Integrated Solutions, who placed a team on site in 2018 to drive improvements in the MRO stores.
Parts are only part of it
Supplying the right parts at the right time and the right price should only be part of the story of successful support for Maintenance, Repair and Operations. If there are still issues in your storeroom, or recurring failures of your assets, throwing parts at the problem won’t help.
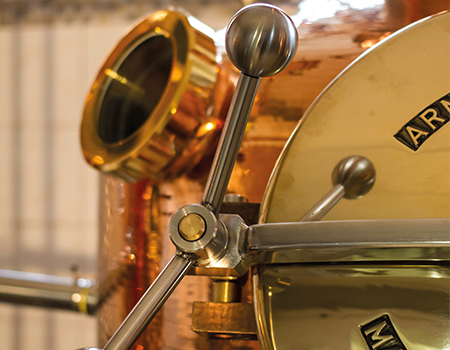
ERIKS’ approach recognises this and differs from competitors by looking beyond product supply and taking a view that’s wider than just the storeroom. In fact, ERIKS Integrated Solutions’ team becomes a fully integrated partner, playing a vital role not only in maintaining your assets, but also in improving and streamlining your processes to deliver optimum efficiency and performance.
For the customer, this involved ERIKS’ on-site team working together with them to undertake a number of initiatives in and around their product ordering and storeroom processes. These included:
- Entering all stocked asset parts onto IFS management system
- Creating a catalogue grouping all spares and showing their location in stores
- Undertaking an obsolescence exercise to remove parts no longer needed and archive any uncertain items
- Following obsolescence exercise, updating catalogue with pictures of parts and a Non-Stock catalogue
- Demarcating shelf contents on floor/ceiling
- Instituting a pump and motor turning regime
- Standardising valves, actuators and seals, to reduce number of vendors
- Creating a Bill of Materials against critical assets
- Creating a taxonomy of instrumentation, pumps, gearboxes, filters
- Rolling-out parts kitting and Drop Zone
Searching for parts. Finding savings
ERIKS research reveals that 50% of all MRO spend on carriage is avoidable, and 10% of store costs are tied up in obsolete items. 15% of downtime is caused by lack of spare parts, and 13 minutes is wasted searching for replacement parts.
By working closely with the customer, ERIKS Integrated Solutions was able to identify potential risks to efficient asset management, and establish safeguards to mitigate them: such as obsolescence management and standardisation. By adding this engineering know-how to the latest MRO methods, processes and technology, and combining this with maintenance supply chain and procurement functions, ERIKS have helped customers achieve cost savings of 3-15%.
For the distillery, ERIKS’ improvements to the stores and MRO parts processes helped the business to gain an AMIS score of over 75% – which equates to a “World-Class” rating. And when your MRO stores are performing at this level, the reliability, efficiency and productivity of your assets can’t help but follow suit.
Asset Maintenance Improvement System (AMIS)
Recognised as the industry standard, the AMIS journey begins with an assessment designed to identify gaps between an organisation’s current performance and industry best practice. It produces a set of effectiveness scores, as well as comparisons with similar or competitor organisations within the same sector.
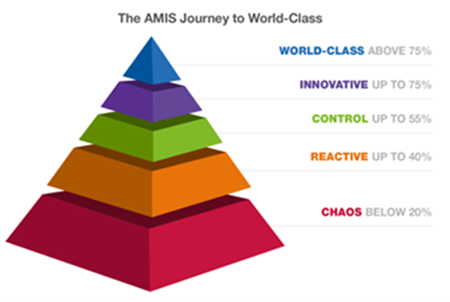
Using a standard system and defined maturity levels, the assessment enables its providers – MCP Consulting Group – to benchmark performance and generate KPIs, to be used as the basis for an improvement programme.
For more details about AMIS, contact your local ERIKS Service Centre, who will be happy to discuss your options with you.
#ERIKS #LetsMakeIndustryWorkBetter #AssestMaintenance #MCPConsultingGroup