In this article
Saying 'hear hear' to better noise protection from 3M
From the obvious culprits such as construction and heavy manufacturing, to automated production lines in the food and pharmaceutical sectors, noisy workplaces are common in industry. And noise isn’t just a nuisance. At best it can reduce productivity. At worst it can be a long-term health hazard or a critical safety risk.
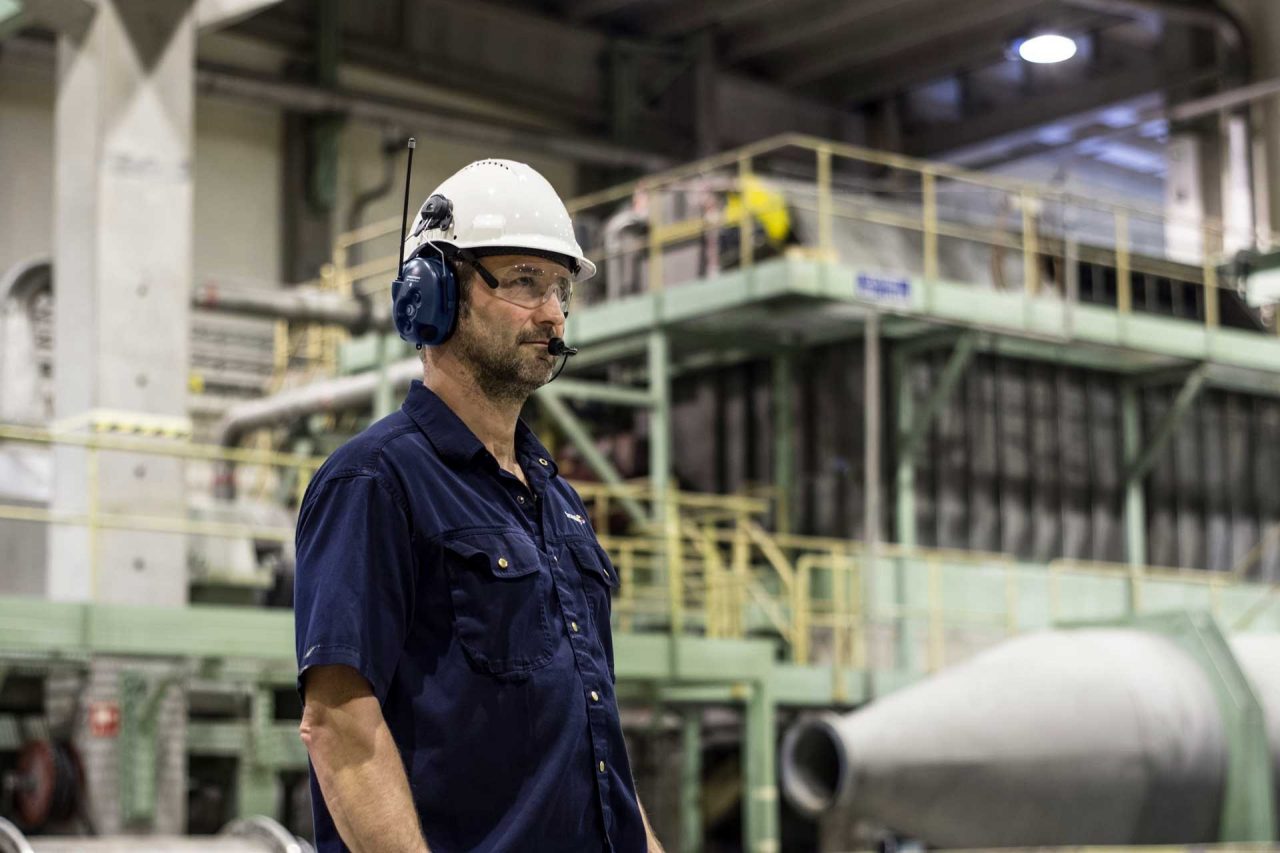
Hearing protection reduces the impact of noise on the wearer’s hearing, but only solves half the problem – and can cause even more. For example, simply blocking out the noise can make it difficult to communicate, and makes it harder to hear instructions, conversations, and even warning signals.
A large UK glass manufacturer was struggling with all these issues when they contacted ERIKS – who listened carefully before coming up with the solution.
Hearing loss or lost production?
The choice between risking damage to hearing or reducing productivity is not one any business or any employee should have to make. Yet every time an employee removes their ear protection to talk to a colleague, or leaves a noisy production area to be able to hold a conversation, either their hearing or their productivity will suffer.
When the glass manufacturer got in touch, ERIKS Industrial MRO & Safety specialists considered the problem, and suggested a 3M product which would resolve both issues in one piece of protective equipment.
The 3M™ PELTOR™ WS™ Litecom Plus is an innovative headset which combines hearing protection with:
- an integrated pre-programmed analogue two-way radio
- Bluetooth® multipoint connectivity
- noise cancelling microphone
- level-dependent function for ambient listening
Even in the noisiest industrial environments, a worker wearing this headset has compliant protection from hazardous noise – while still being able to communicate with colleagues and remain aware of ambient noise such as machine sounds and warning signals.
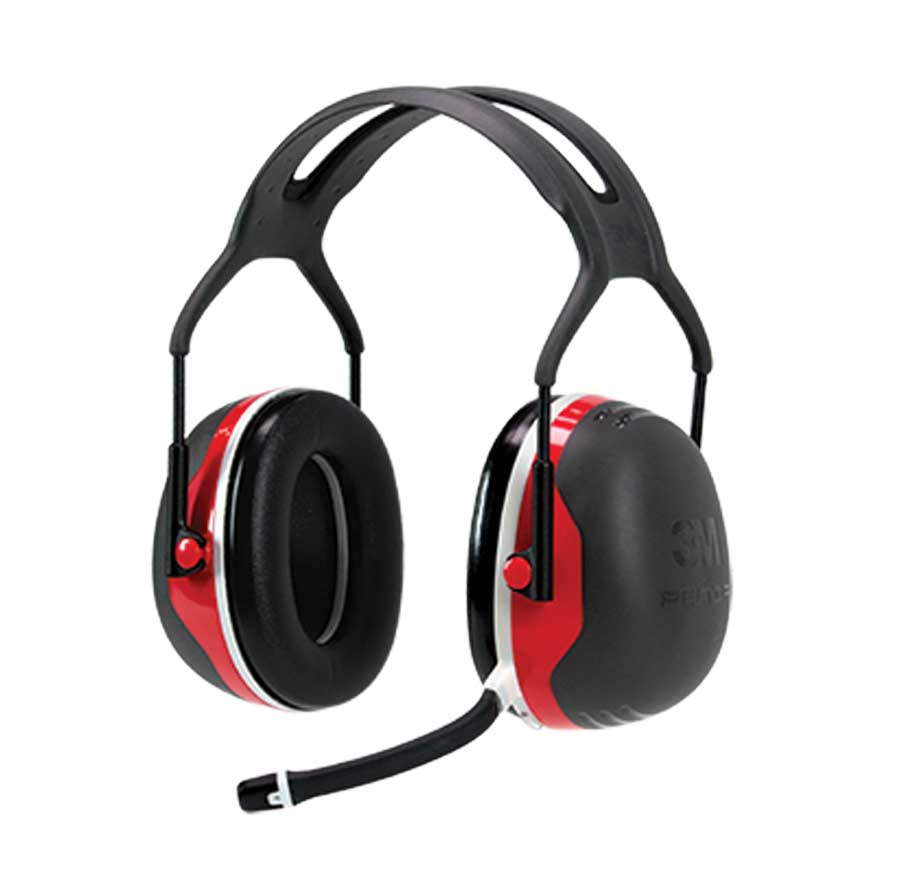
Not just hearsay
The productivity benefits of the 3M™ PELTOR™ headsets have been scientifically proven in a study by researchers at Lund University in Sweden.
They supplied one team of construction workers with the headsets, while an identical team carried on working without. Both teams were working on construction-related tasks such as excavating, pipe laying and tube welding. The researchers recorded the time that members of both teams spent working, and ‘downtime’ when they were – for instance – walking about the site or stopping work to talk to colleagues.
The results showed that the workers without headsets had a total of just under 10 hours’ downtime during the survey period, whereas the workers with headsets had under 5½ hours. That meant there was an increase in productive time of more than 15% as a result of wearing the headsets.
Integrated and integral
ERIKS’ glass manufacturing customer didn’t carry out a scientific survey. But they did report that 3M’s hearing protection with integrated communication had ‘become an integral part of our day-to-day operations.’
They went on to explain that they ‘operate in a very noisy environment, and find that these headsets significantly improve our communication. Our site is on the larger scale, and they allow us to clearly speak with other engineers in any part of the factory, which not only increases our level of communication, but also mitigates many other risks associated with health and safety.’
For more information on Safety solutions and to get in touch with one of our ERIKS Safety Specialists, please contact your local ERIKS Service Centre, who will be happy to discuss your options.
#3M #ERIKS #LetsMakeIndustryWorkBetter #Welding #Hearing #Headset #Innovation #Peltor #PPE