In this article
Spin riveting for maximum conveyor chain plate security... The benefits of Renold
Although most conveyor chains these days are wedge riveted as standard, the option to specify spin riveting is an important one and should be considered for critical applications both by designers of original equipment and maintenance engineers alike.

It’s an important consideration and an effective solution on applications where attachments have been fitted to the side plates of conveyor chain that could be carrying heavy loads. In fact, Alec Annand, the manager of Renold Chain’s Customer Service Centre, recommends that all engineers specifying custom designed conveyor chain, with attachments, should consider the benefits of spin riveting as an option, due to the extra side plate security it provides.
The recommendation comes after one manufacturer using a large amount of conveyor chain, at one of its plants, sent an inspection team to Renold Chain’s Bredbury Service Centre, which also produces both transmission and conveyor chain to exact specifications to a wide range of industries including OEMs, theme parks, packaging, printing and food, to check on the quality of its spin riveting process.
Conveyor chain operated by the manufacturer was fitted with attachments that had to carry very heavy loads through underground chambers that were inherently dirty and foul smelling.
The load on the chain side plates was causing them to work loose over time and eventually they would come off. An engineer would then have to descend into these dark, unpleasant chambers to carry out repairs.
The maintenance team at the manufacturer took the decision to specify replacement conveyor chain with spin riveted side plates as a solution. Not only would this virtually eliminate the need for engineers to enter the unpleasant environment to carry out repairs, but the spin riveted chain would also cut maintenance and increase productivity.
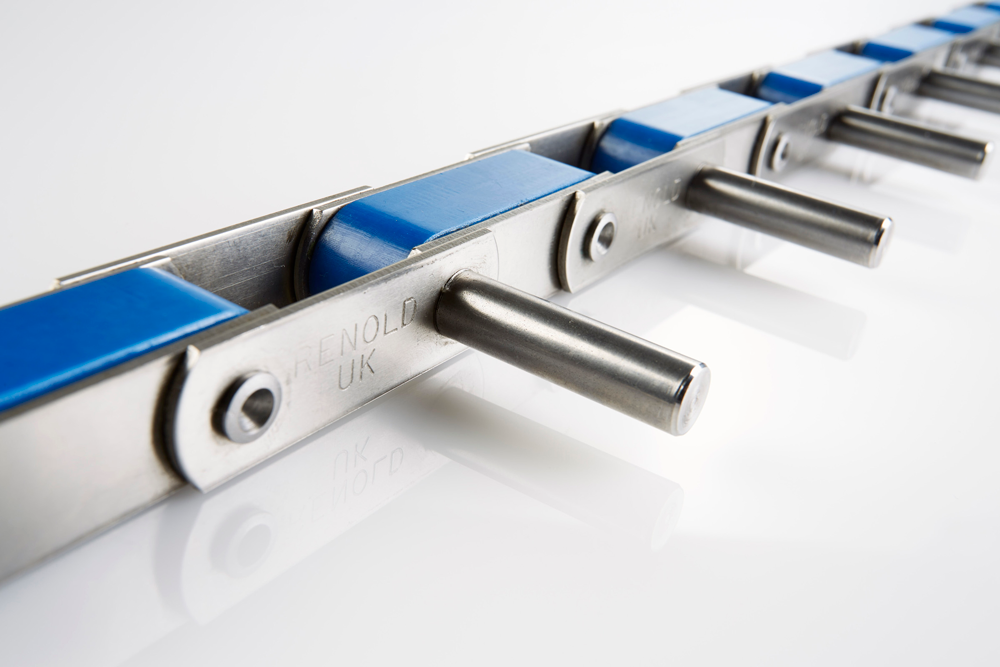
Cheaper alternative
Wedge riveting is cheaper and quicker than spin riveting, which is why most conveyor chain manufacturers have adopted this process as standard. It’s fine on most applications, especially where the side plates are not fitted with load carrying attachments, but spin riveted conveyor chain provides enhanced side plate security, and as Annand recommends, it should be considered for all critical applications.
During the spin riveting process, at Renold’s customer Service Centre, the pins are end softened to prevent cracking during riveting, and to provide easier onsite installation, riveting and dismantling for customers. The spin rivet itself has a mushroom-like head and provides much greater surface area contact with the side plate. It is this feature that provides the required enhanced security of the chain’s side plates.
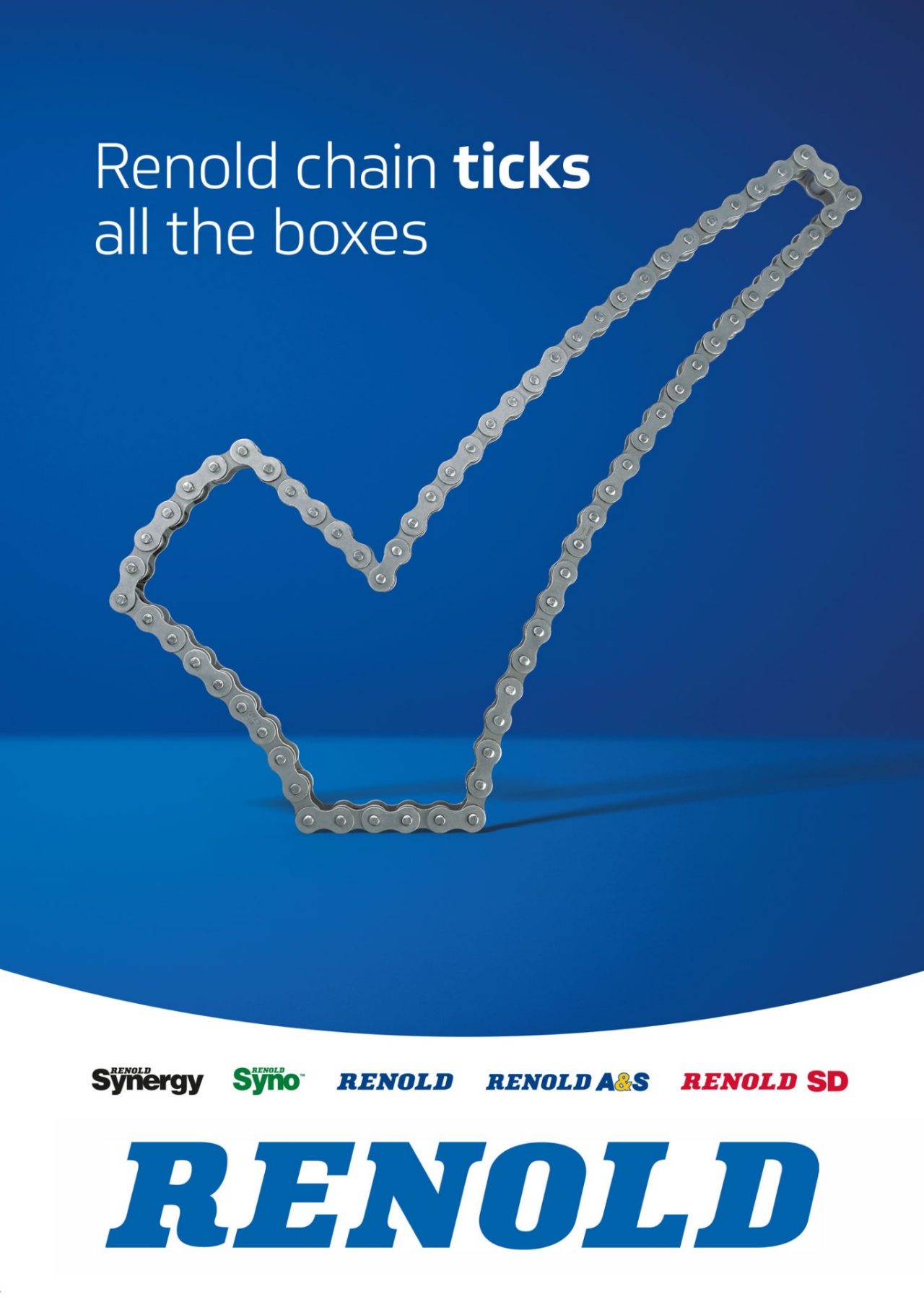
For more information on Power Transmission solutions and to get in touch with one of our ERIKS Chain Specialists or Power Transmission Engineers, please contact your local ERIKS Service Centre, who will be happy to discuss your options.
#Renold #ERIKS #LetsMakeIndustryWorkBetter #SpinRiveting #Printing #Packaging #Food #Conveyor #Chain #Plates #Engineering