In this article
Money Down the Tube?
You’re probably confident you’re doing all you can to cut back your energy use. But if you have manifold-mounted, plug-in pneumatic valves, you could be using energy you don’t need, and wasting money you can’t afford to waste.
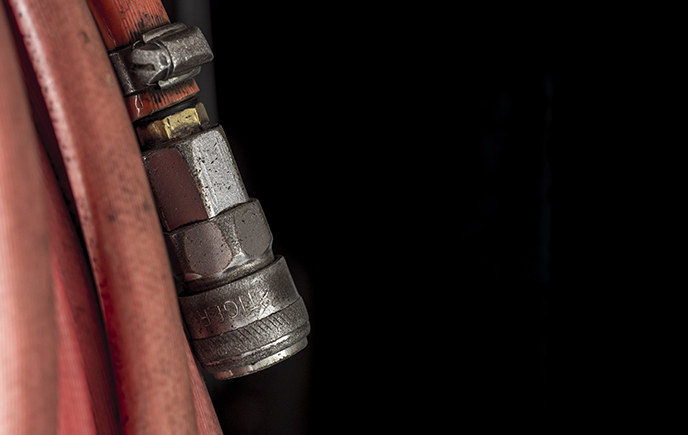
The problem is that most circuits have two air lines from valve to actuator: one for extend and one for retract. For each valve cycle the actuator is pressurized on one side or the other. This means the tube that connects the valve and actuator also has to be pressurised. Yet the tubing isn’t doing any work at all – just transferring the compressed air energy to the actuator.
And what seems like an insignificant tubing volume can add up to quite a significant energy use, and cost.
Pneumatics experts SMC provide an example, in a recent White Paper, of a packaging facility dropping corrugated boxes from a mezzanine down to ground level. The drop-down uses gravity, with mechanical stops to sequence the box delivery. Each stop comprises a pair of 2” bore x 1” stroke air cylinders to operate a brake to stop and release the box. There are four stops on each drop-down, requiring a total of eight actuators and four valves to control them.
Taking the long view
The directional control valves are centrally located on a single manifold, which is anything from 10-25ft from the actuator. That’s 10-25ft of tubing, one length of which has to be exhausted and one filled, every time a valve shifts.
Insignificant? Maybe not.
In fact, assuming 10ft of ¼” OD tubing with an ID of approximately .180”, the volume is 3.05 cubic inches. With two lines from the valve to each actuator pair, the total tubing volume is 6.10 cubic inches per complete cycle. Each of the 2”x1” cylinders has a total volume (extend and retract sides) of 5.5 cubic inches, or a total cylinder volume of 11 cubic inches.
That means the tubing volume is over half that of the actuators. So over half the energy being developed at the compressor is being used just to fill the tubing lines, which do no actual “work” at all.
What does that wasted energy actually cost?
Paying under pressure
A working pressure of 80 psi and a compression ratio of 6.33, multiplied by the volume, provides a normalized volume of 38.6 standard cubic inches. If the cylinders are actuated five times a minute, compressed air consumption is 193 standard cubic inches per minute – or 0.11 SCFM. And that’s only for filling the tubing to the closest station on the drop-down.
There are 3 other more distant stops to consider too, as the chart below shows.
Tubing Length (inch)
Tubing Volume (in³ x 2)
Tubing Volume x Compression Ratio (in³)
Time 5 Cycles per minute (scim)
SCFM
Station 1
120
6.1
38.6
193
0.11
Station 2
180
9.16
58.0
290
0.17
Station 3
240
12.2
77.2
386
0.22
Station 4
300
15.3
96.8
484
0.28
Total
840
42.8
270.6
1353
0.78
As you can see, the total volume of the airlines from valves to actuators is 42.8 in³, compared with a total volume of 44 in³ for all eight cylinders. So virtually half the compressed air produced is consumed for filling air lines.
The factory in SMC’s example is in the USA, with electricity at around 8p ($0.10) per KWh. Operating 24/7, a single drop-down would consume around £85 ($110) of electricity per annum just to fill those air lines. As the factory has 50 drop-downs, that’s approximately £4,250 ($5,500) of wasted energy every year.
Shortcut to cost-cutting
This may seem an extreme example. But have you never used long air feed lines to provide a clean valve package? Or oversize tubing just because it was handy? Or larger tubing because you considered it more efficient?
If you have, then you’ve been producing compressed air just to fill tube volume. Not to mention risking liquid moisture build-up in over-long lines, that will eventually work its way into the actuator and shorten its life.
Fortunately, as SMC explain, the solution is simple: mount valves on or nearer to the actuators. This also means fewer connections, which means fewer potential leaks.
In the example above, that one simple energy-saving step would save £4,250 a year from – literally – going down the tube.
For more information on Fluid Power, Transfer and Control Solutions and to get in touch with one of our ERIKS Specialists, please contact your local ERIKS Service Centre, who will be happy to discuss your options.
#FMC #ERIKS #LetsMakeIndustryWorkBetter #Pneumatics #Valves #Actuators #CostSaving