In this article
Saving £0.5m is no small potatoes
ERIKS expertise delivers value when the chips are down
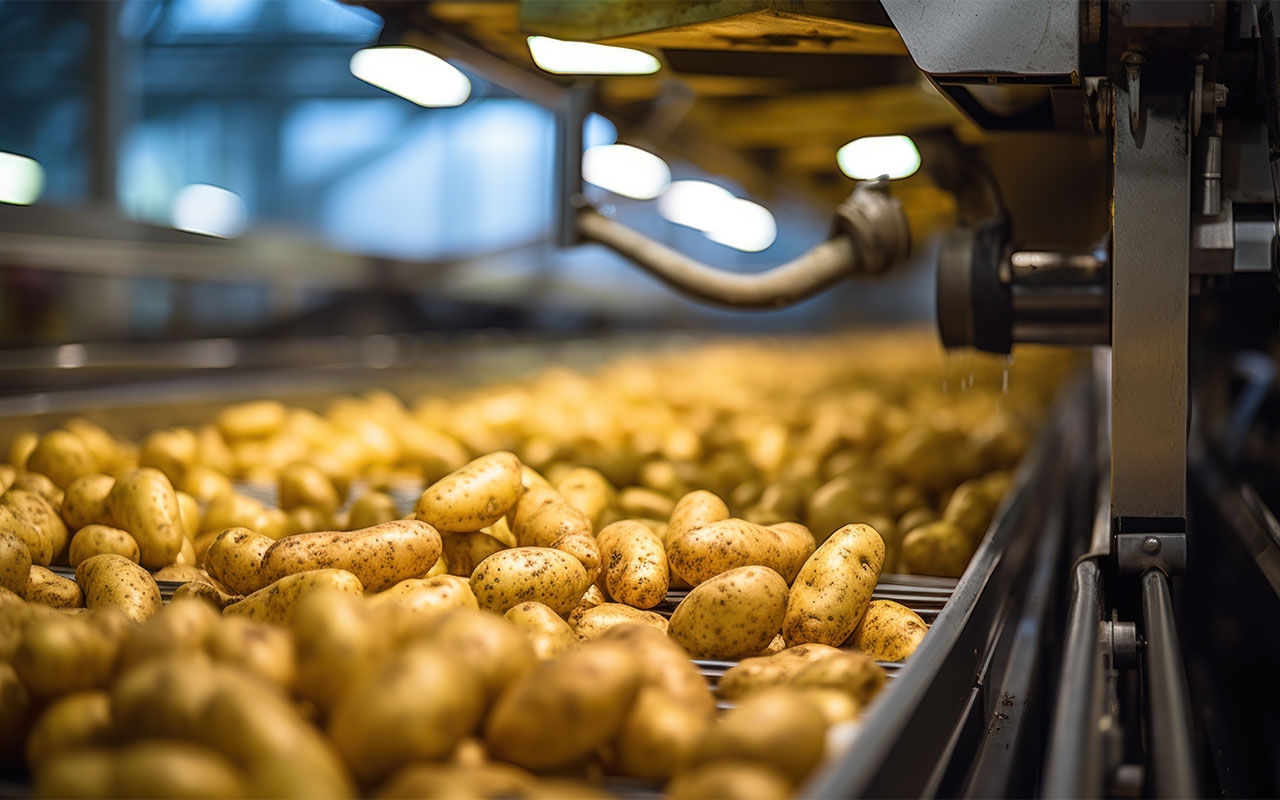
Industry Sector:
Food & Beverage
Application:
General industrial
Actual Saving:
£510,748
Payback period:
N/A
Product/Service:
- Pumps
Customer Benefits:
- Risk mitigation
- Increased safety
- Increased uptime
- Reduced maintenance time
A plate of Britain’s favourite may be ‘as cheap as chips’, but for one potato processor the manufacturing of the frozen dish was proving expensive. With failing pumps, poorly performing effluent screws, emergency pump hire, and tankering away waste water, problems – and potential costs – were piling up.
Processing potatoes into frozen chips sounds simple: peel, chop, freeze. But the product in the packet is a long way from the potato in the field. For one thing, it’s not covered in dirt. Washing the potatoes is a significant part of the process, and removing the resulting effluent – soil, sand, silt and waste water – requires a variety of machinery.
When this aspect of the customer’s potato preparation began to have issues, it was clearly time to call on ERIKS know-how – before the production line had its chips.
Challenge
The customer utilises two submersible pumps to remove the effluent and pump it out for disposal. When the first pump failed, the cause was traced to a split outlet pipe. Until this was repaired, the customer relied on their standby pump, but this subsequently also failed due to a seized bearing.
Even when the split pipe was replaced, the amount of effluent being removed by pump one was still far below the norm – leaving the site with standing dirty process water.
The customer’s Reliability Partner had been unable to identify the root cause of the problem. Closing the lines for a more in-depth investigation would have incurred costs to tanker away the water, as well as lost production costs.
So the customer contacted the ERIKS Customer Operations Manager, who arranged for an ERIKS Pump Application Engineer to attend. After rearranging less urgent appointments, the engineer arrived next day.
Solution
The ERIKS engineer inspected the application but found nothing obvious to indicate the reason for the pumps’ failure to remove the effluent. The customer shared photographs and videos of the application which also failed to reveal the cause.
The engineer then viewed the customer’s Building Management System which recorded – amongst other data – the flow rates and pressures for the pumps. It was immediately clear to the engineer that there had been as much as a 90% drop in the pumps’ performance – with flows varying from 300m3/hr down to 30-40 m3/hr. This explained why so much effluent was remaining on the site and failing to be pumped away.
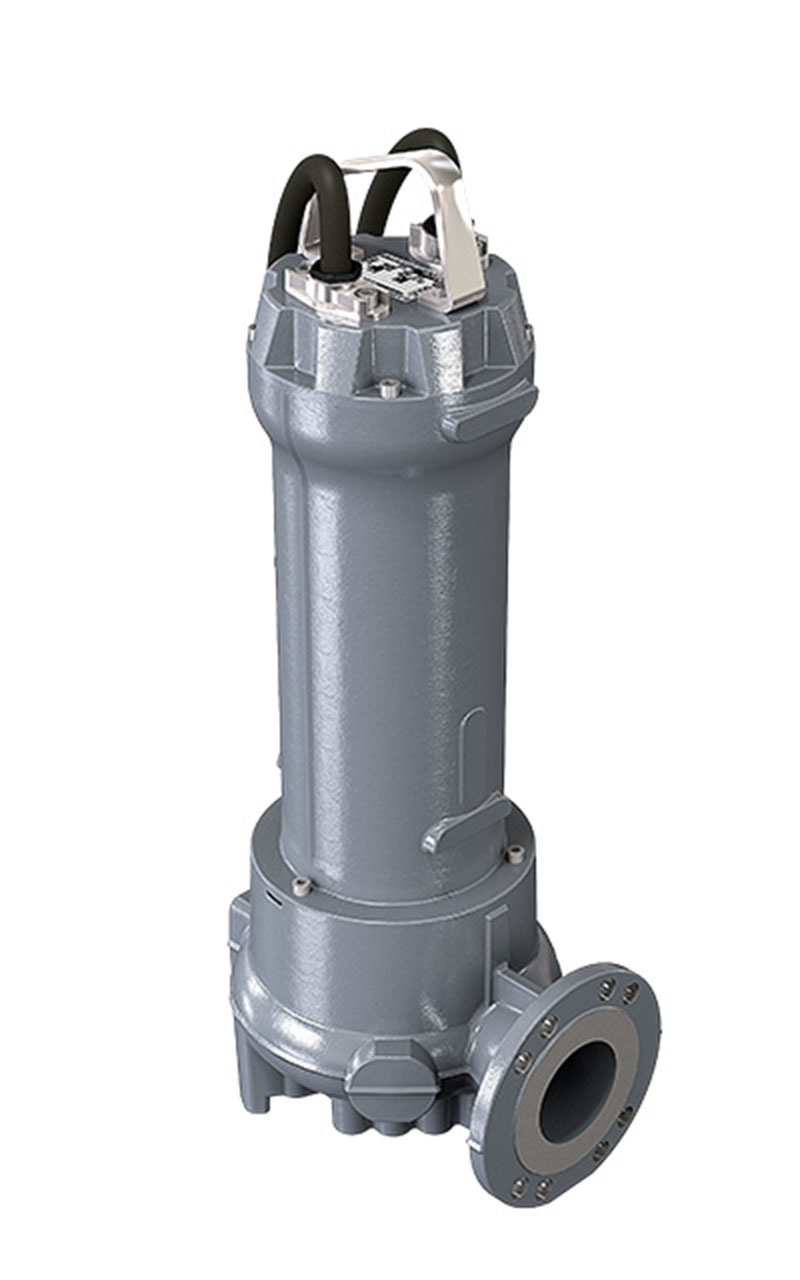
Submersible pump used within the application
But why were the pumps underperforming?
When connected to 8” diameter pipework, the industry standard for a pump’s self-cleaning velocity – without causing excessive increased wear – is between 2.7m/sec and 3.5m/sec. As the ERIKS pump engineer realised, the customer’s pumps were operating below the self-cleaning velocity for the size of pump and pipework. As a result, the suction apertures were becoming increasingly clogged with silt and sand.
Because the pumps were being operated with a Variable Speed Drive, they could be driven at overspeed. ERIKS know-how enabled the engineer to quickly calculate the required velocity to effectively clear the sediment from the units. His workings showed that by operating the pumps at 120%, a velocity of 3m/sec with a flow rate of 330m3/hr would be achieved – which would have the desired self-cleaning effect.
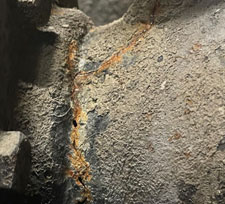
Split in the outlet pipe
The VSD was adjusted to the required speed and the first pump was switched on.
Result
Within just 90 seconds, the pump was back to full flow. The same procedure was carried out on the standby pump, and this also showed a marked improvement in performance.
Without the ERIKS Pump Application Engineer’s know-how, the customer would have had to remove the effluent by tanker to access the suction pipework and look for the root cause of the problem.
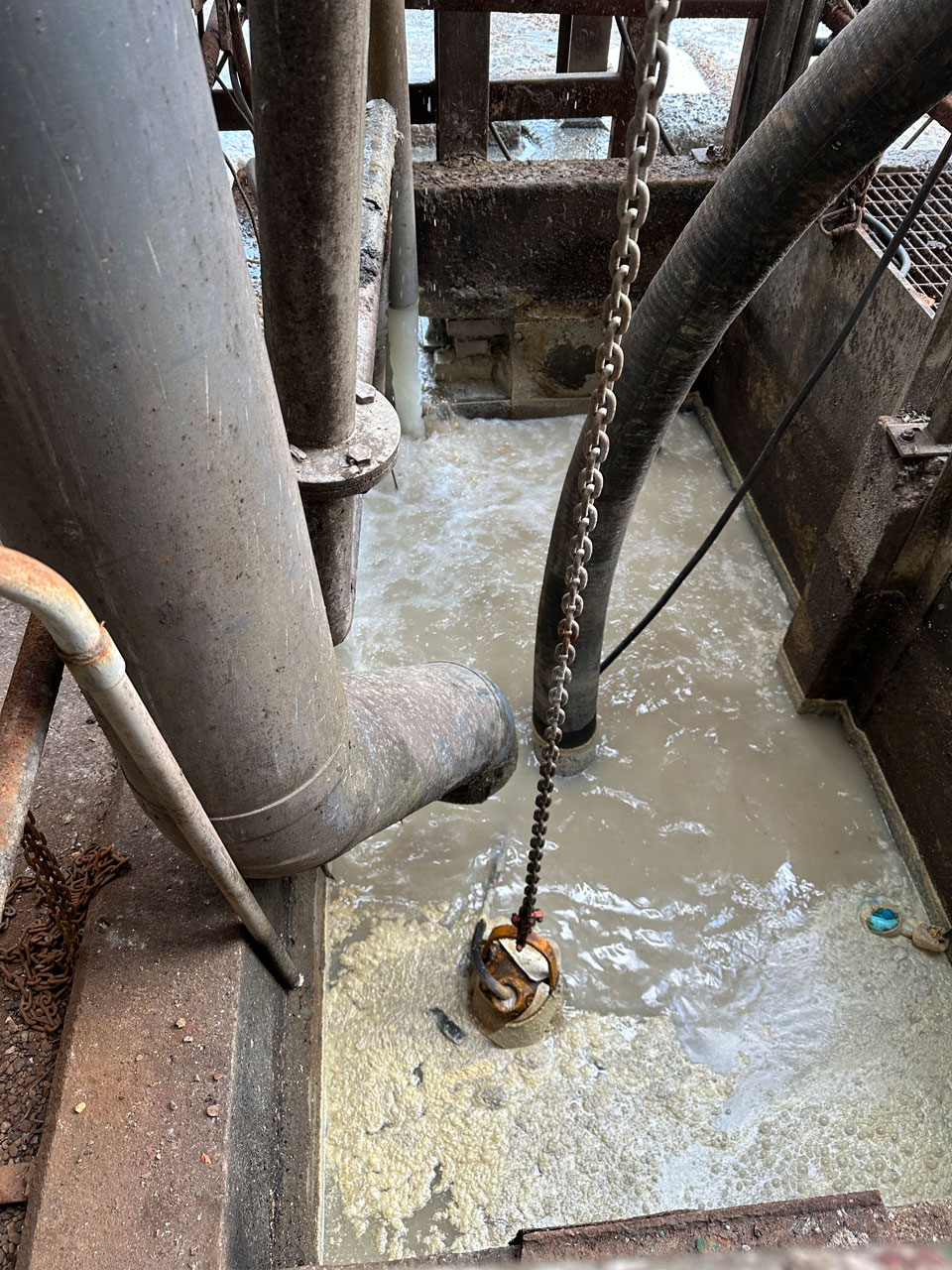
Submersible pump in-situ
This could have shut down production on both the lines involved for at least twelve hours, at a lost production cost of £10,000 per hour, per line.
To avoid any recurrence, ERIKS’ engineer advised the customer to include a short burst of faster running every 2-3 months as part of their Preventive Maintenance Program.
The Site Manager was so impressed by the speed of response and the quick solution to the problem, he has promised to put ERIKS’ Pump Application Engineer on his Christmas card list!
The second helping...
Further upstream in the process, the customer utilised two Archimedes’ screws to remove water from the effluent pit. These were failing, and ERIKS arranged two emergency hire pumps to enable the production process to stay operational.
Meanwhile, the overhaul of the screws was costed at £172,800. In addition, the screws would be out of action for up to 24 months, requiring two replacement pumps on long-term hire, at a cost of £129,259.
ERIKS were tasked with finding a more cost-effective solution.
Although the Xylem Flygt submersible hire pumps were keeping production going, they did have an unwanted side effect. Their design meant that they were chopping the soft solid potato waste into small pieces. These were then passing through the filter system into the export sump, and subsequently to the effluent outfall. As a result, the site’s allowance for export of material of this type was being exceeded.
At the same time, the quantity of sand, silt and foreign objects passing into the system had the potential to cause significant unwanted wear.
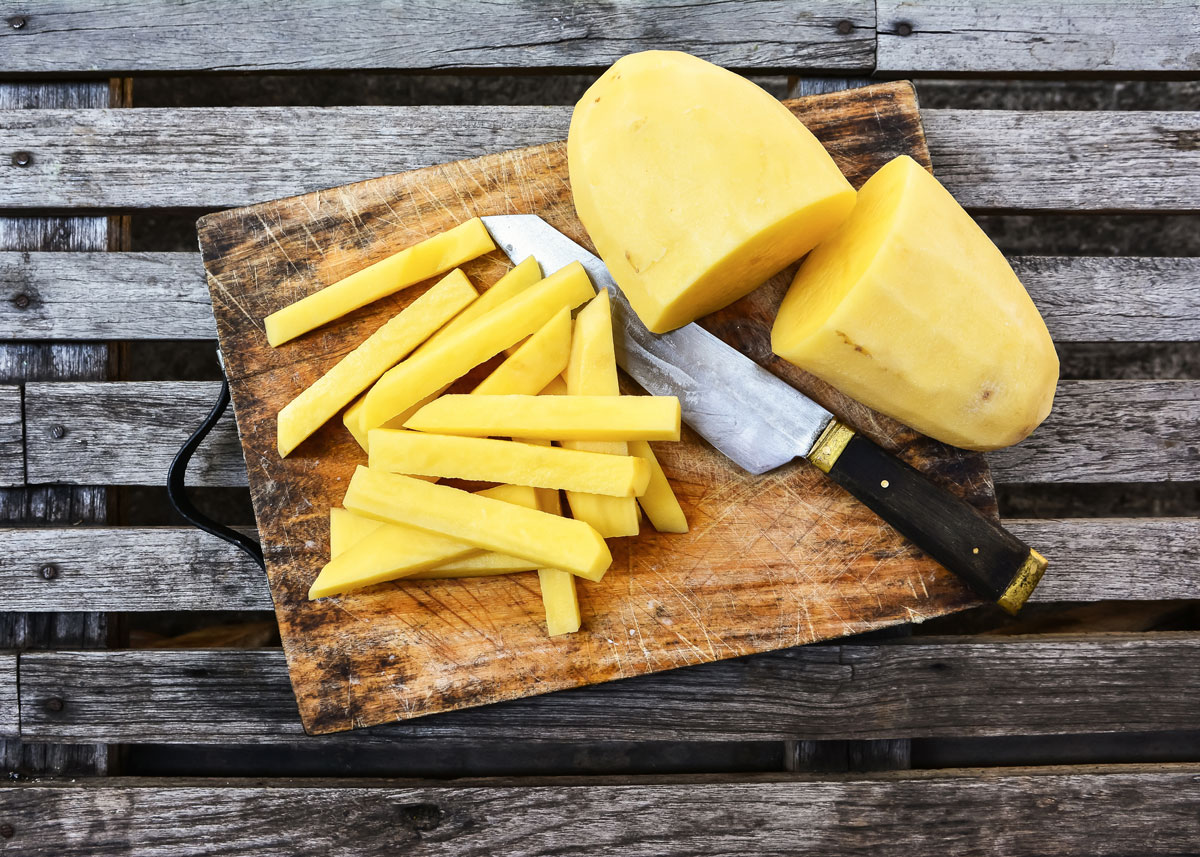
The tasty solution...
The ERIKS Pump Application Engineer plotted the performance of the units into a performance curve.
This showed that the pumps were running at 63% speed with a liquid flow velocity of 130m3/hr at 2m3/sec. The power requirement was approximately 3kW for the 13.5kW pump unit.
Using his pumps know-how, the ERIKS engineer recommended replacing the Xylem pumps with two vortex pumps. These allow larger solids to pass without being chopped up and without damaging the pumps. Since the solids remain the same size, they are then screened out at the next stage of the filter system, and prevented from being discharged into the sea.
Result
Not only do the new pumps keep the site within its effluent export limit. They also provide a permanent and more effective alternative to the Archimedes’ screws. And they reduced the pump hire costs that would have been incurred if the screws had been repaired rather than substituted.
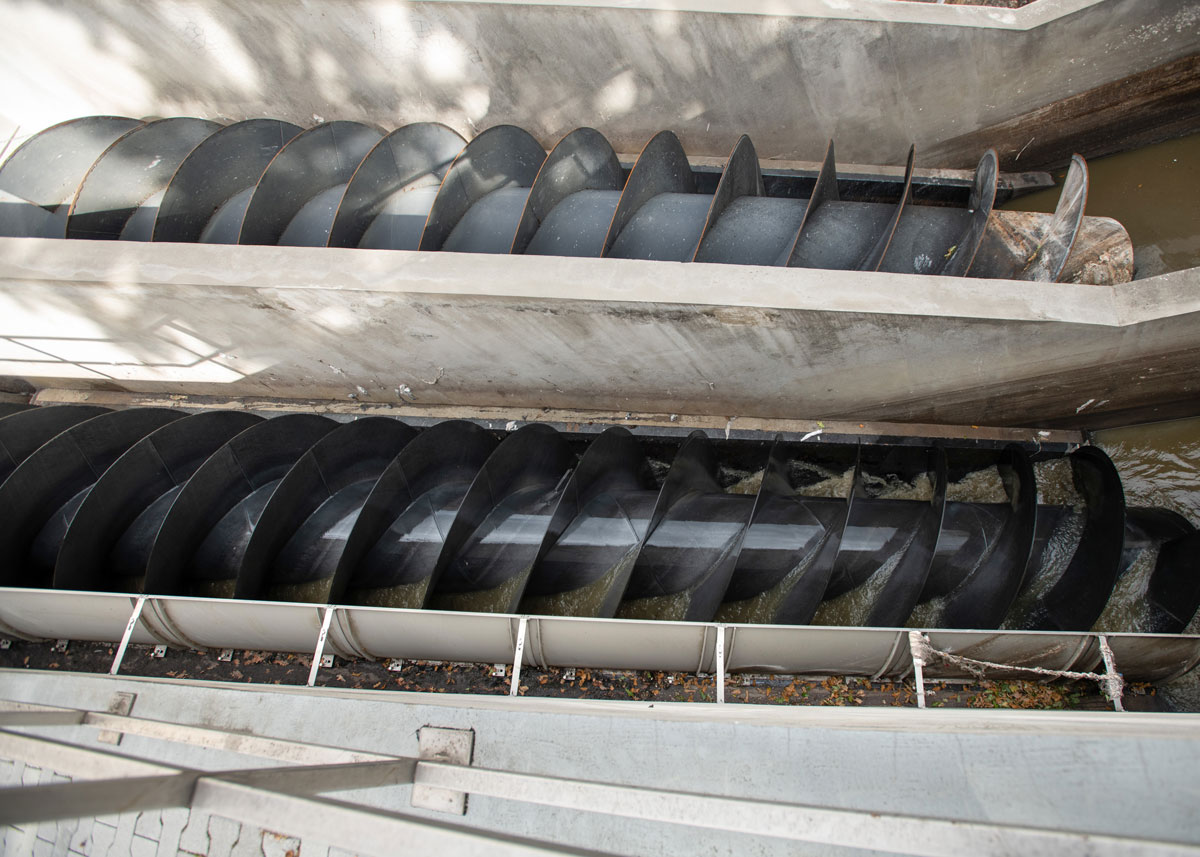
Two archimedes screws tasked to remove water from the effluent pit
Cheaper than chips
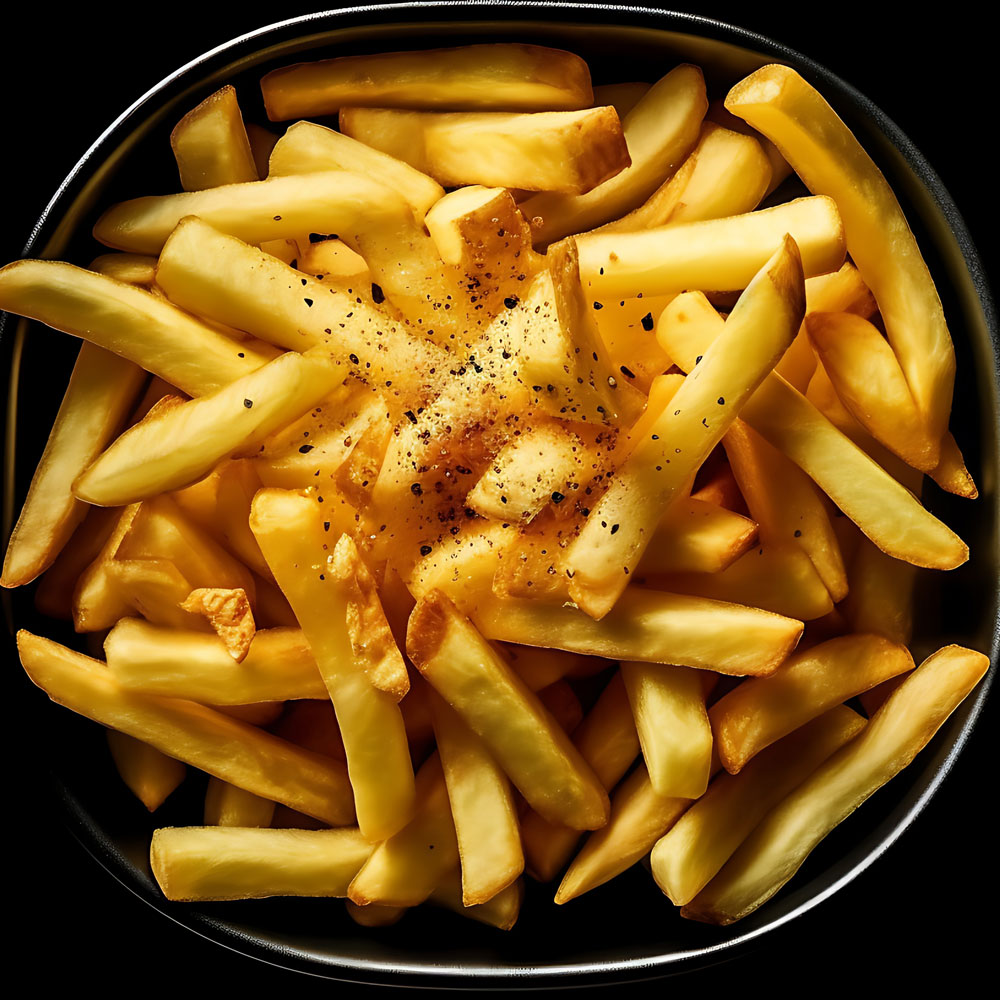
The finished product cooked and served ready to eat
Without ERIKS’ know-how, the customer would have incurred the following costs for the two major challenges described above:
- £240,000 lost production during submersible pump inspection
- £172,800 Archimedes screws overhaul
- £129,259 replacement pumps hire
Instead, the lost production was totally avoided, and replacing the Archimedes’ screwswith vortex pumps cost just £31,311.