In this article
Oiling the wheels of industry
A system upgrade helps restore reliability
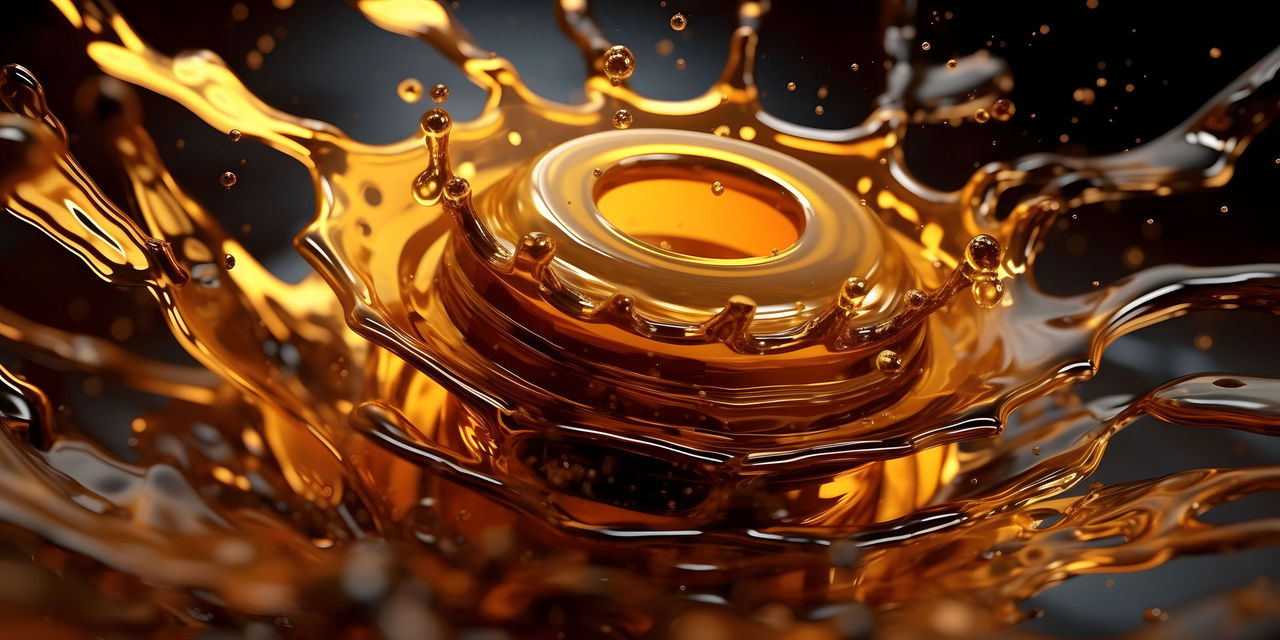
Industry Sector:
Automotive
Application:
Hydraulic Oil Contamination Programme
Actual Saving:
£107,806
Payback period:
2 months
Product/Service:
- Systems inspection and upgrade
- Filter supply and installation
- Training and knowledge transfer
Customer Benefits:
- System improvement
- Reduced maintenance
- Increased productivity
- Improved reliability
It’s not always the most high-tech and complicated machinery that causes the most expensive and time consuming breakdowns. Sometimes, it’s as simple as failing to change the oil.
A major manufacturer and supplier of engineered joining technology was losing thousands of pounds several times a year due to failure of two of its hydraulic presses. And because its maintenance programme was reactive, not proactive, machine failure was something that could stop production in its tracks.
The customer called in ERIKS to solve the problem and establish a preventative maintenance programme to ensure future disruption from contaminated oil was kept to an absolute minimum.
Challenge
The hydraulic oil had been in the two presses for 18 months, had never been changed, and both were breaking down every two to three months, resulting in repairs costing around £30,000 each time.
Costs were mounting up. One press had already been written off at the end of 2021 due to problems resulting from contaminated oil, leaving the business £300,000 out of pocket. The two faulty presses — a 63 tonne and 80 tonne — couldn’t reach the necessary pressing capacity.
The business was losing out both financially and in unnecessary downtime, so the engineering team got in touch with ERIKS on-site support for help.
Solution
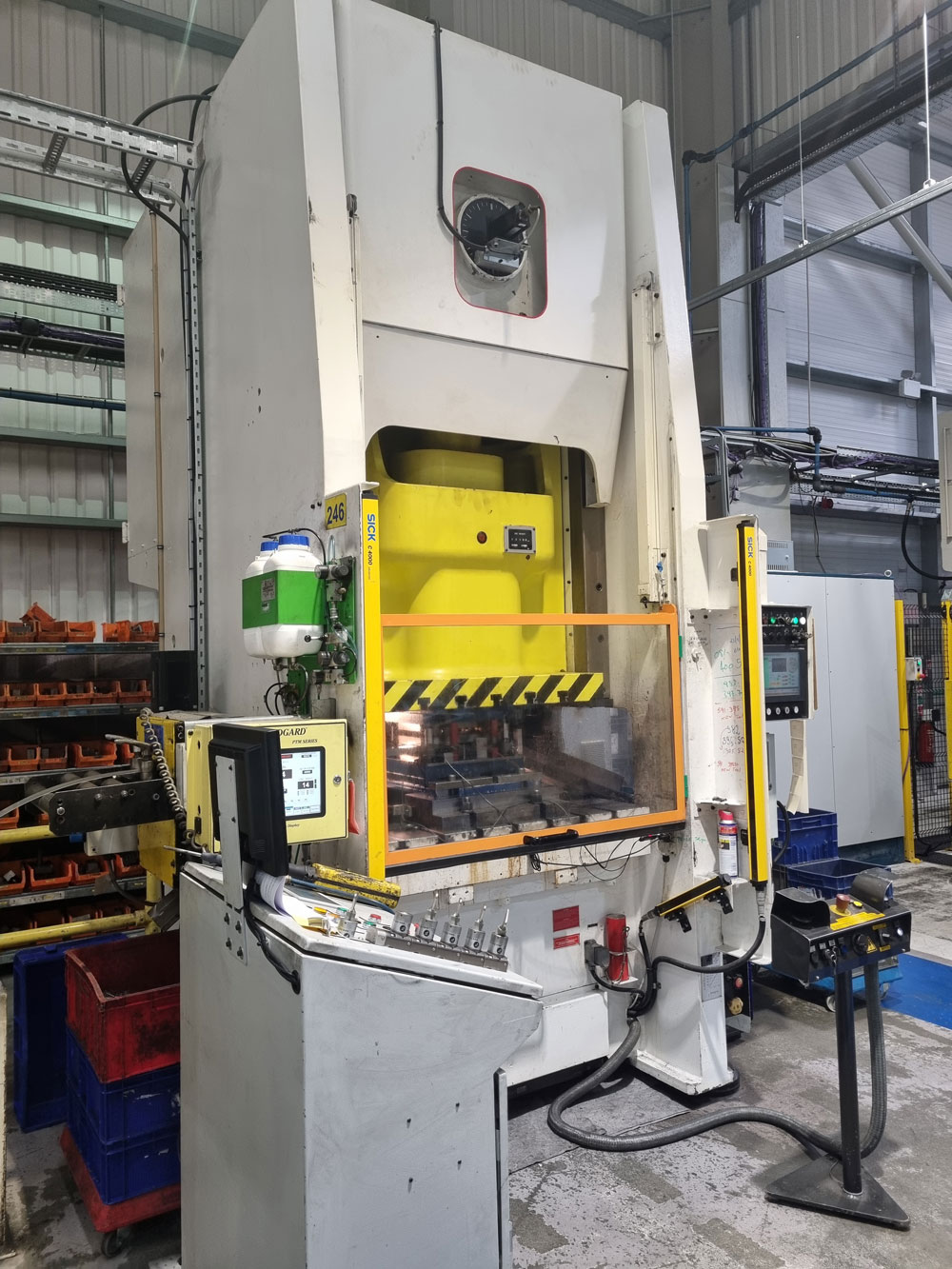
Upgraded press with mobile filtration unit (MFU) in situ
ERIKS undertook a full inspection of all the presses on site, with a technical specialist carrying out a full site walkaround, visually inspecting all presses — 170 hydraulic six tonne hare presses, four 63 tonne presses and two 80 tonne presses — and extracting oil samples for testing.
The inspection revealed that two presses showed high contamination and water content levels. One press had a water content of 15 ppm and a gravimetric result of 35mg/t, and the other a water content of 21.3 ppm and a gravimetric result of 15mg/t. The base oil showed a water content of 102.8 ppm and a gravimetric result of 5mg/t.
No contamination level here is acceptable. With neither press having a filter fitted, the oil entering the system was already contaminated, before it had even started working.
This needed fixing before the oil was changed, to stop any further particulates entering the system. Our application engineer recommended the use of a mobile filtration unit (MFU) at the oil ingress, to filter solid particle contamination, remove free water and help increase the life expectancy of both the machine components and the oil.
Once the MFU was installed, the presses were drained, filled with clean oil and recommissioned.
Result
Thanks to the installation of the MFU which paid for itself within two months, the customer saved £76,640 in the first year and £35,116 in the following year — £107,806 in total, including parts and general maintenance costs. Downtime has been significantly reduced, with over 500 hours saved, since the MFU was installed.
Before ERIKS’ intervention, maintenance had been carried out on the presses on a reactive basis, responding to problems rather than trying to avoid them in the first place. ERIKS suggested a maintenance plan incorporating sensors to monitor the hydraulic fluid on an ongoing basis. We also trained the company’s engineers to carry out their own preventative maintenance plan, ensuring future cost savings on oil changes, longer machine life and less downtime.
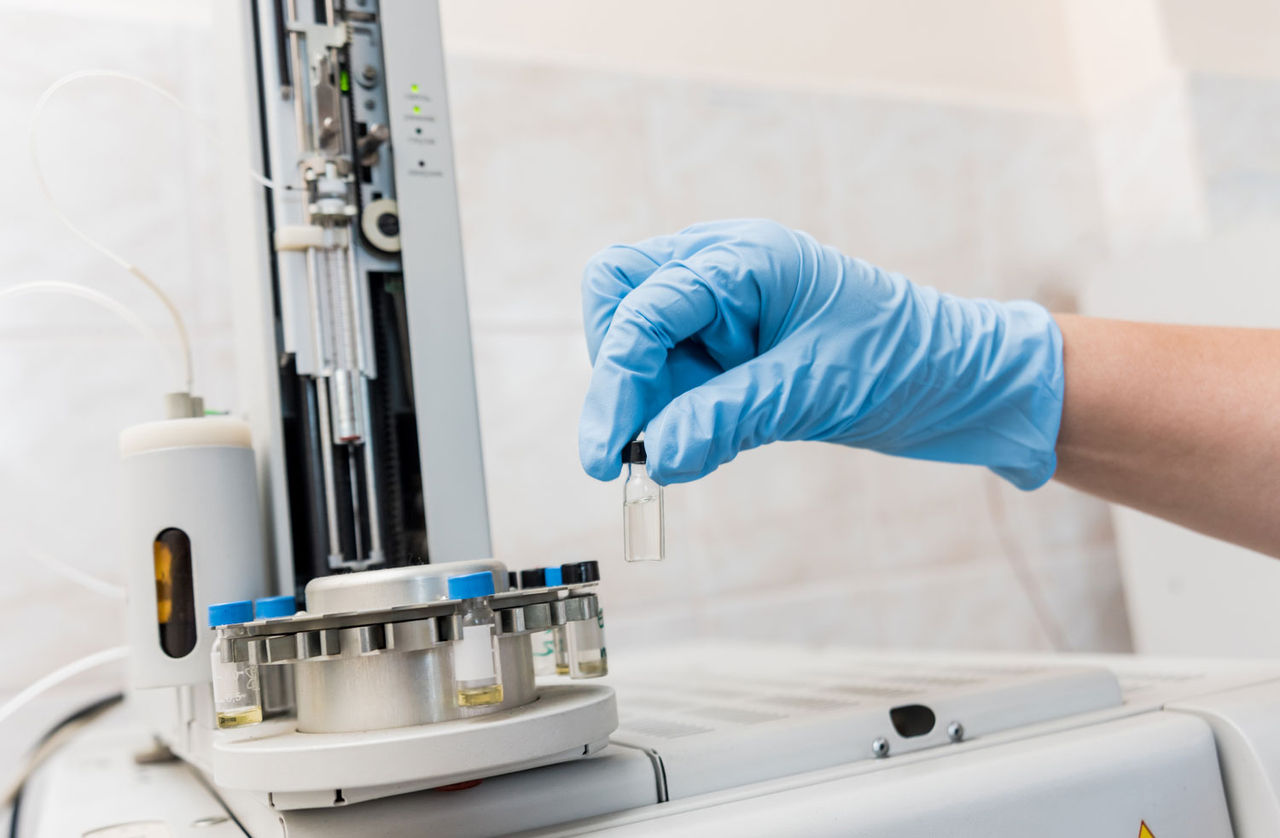