In this article
Halloween horror averted with ERIKS speedy response
Six day turnaround avoids six weeks' lost production
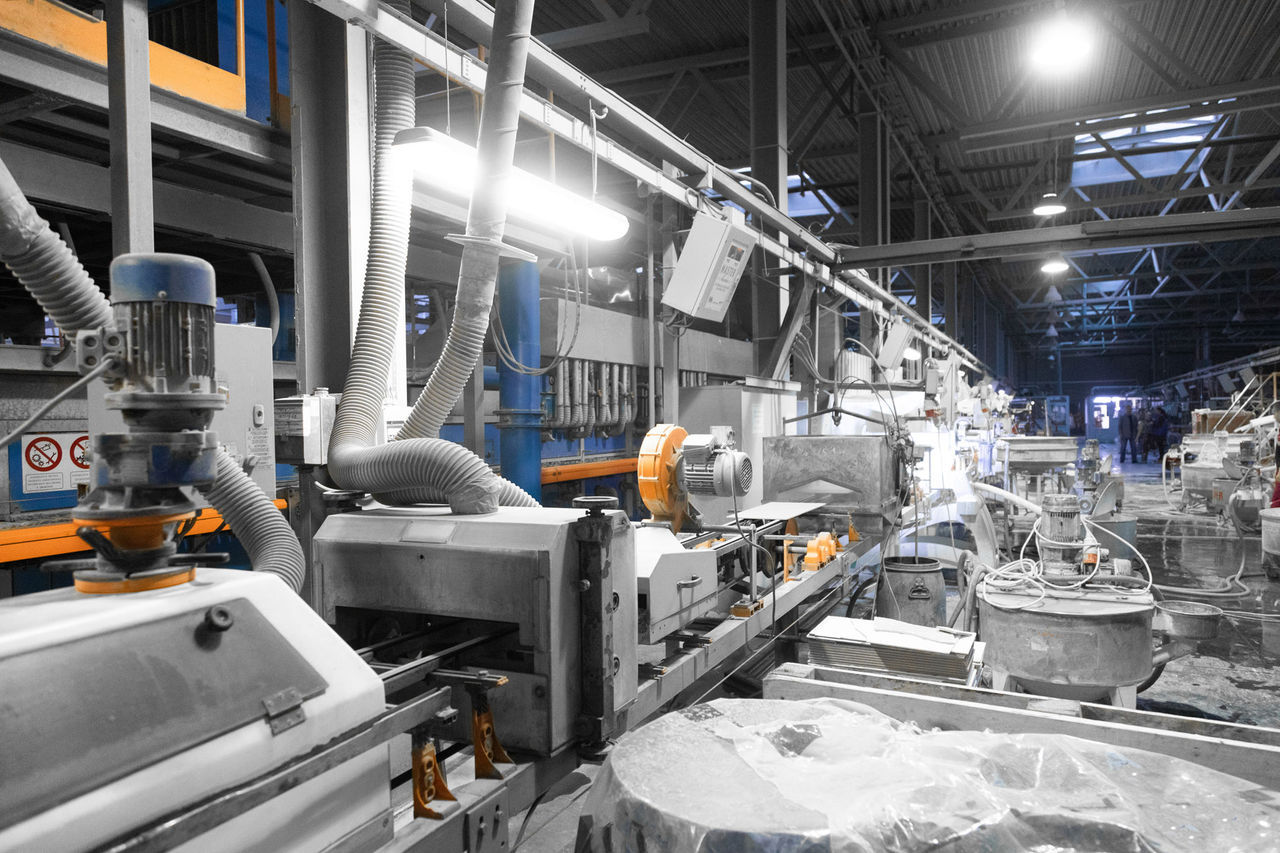
Industry Sector:
Primary Industries
Application:
Cement Raw Mill Motor
Actual Saving:
£560,000
Payback period:
N/A
Product/Service:
- Engineering services
- Inspection and testing
- Training and knowledge transfer
Customer Benefits:
- Increased uptime
- System improvement
- Maintenance reduction
- Increased Mean Time between Failures (IMTBF)
On Halloween morning, 31st October, ERIKS received a scary call from a customer about a problem with their raw mill motor. By bonfire night, six days later, the customer had avoided a six-week loss of production, thanks to ERIKS’ lightning-fast maintenance turnaround.
Challenge
The call, from a cement manufacturer, concerned a raw mill motor that turns quarried and crushed rock into meal, which in turn is used to produce clinker for the manufacture of cement. Without the meal, there’s no cement — so the customer was very keen to get the problem sorted ASAP.
ERIKS engineers were on site the same morning. Their initial investigations revealed damage to the motor’s brush assembly and slip ring contactor collection surface. They performed a Baker Surge Test in-situ - a test that is ideal for motors that are difficult to remove, or those that are critical to operations.
A Baker Surge Test, tests the insulation of the motor windings. The motor windings are disconnected from the power supply and the test determines the insulation condition, and in this case no additional damage to the rotor main winding was found.
Solution
Next, they removed the brush gear to gain full access to the slip rings. This very quickly showed heavy carbon contamination along with substantial burning and pitting of the slip ring contactor surface. With just two weeks supply of raw material stockpiled, salvaging the slip rings was essential.
Getting hold of new ones would take at least eight weeks, so the business could potentially lose six weeks of production — a huge operational and financial blow.
Even if they could be repaired, everything had to be completed within two weeks, before the existing supply of clinker ran out and production halted. Normally, such an operation would take between six and eight weeks, so this was quite a challenge.
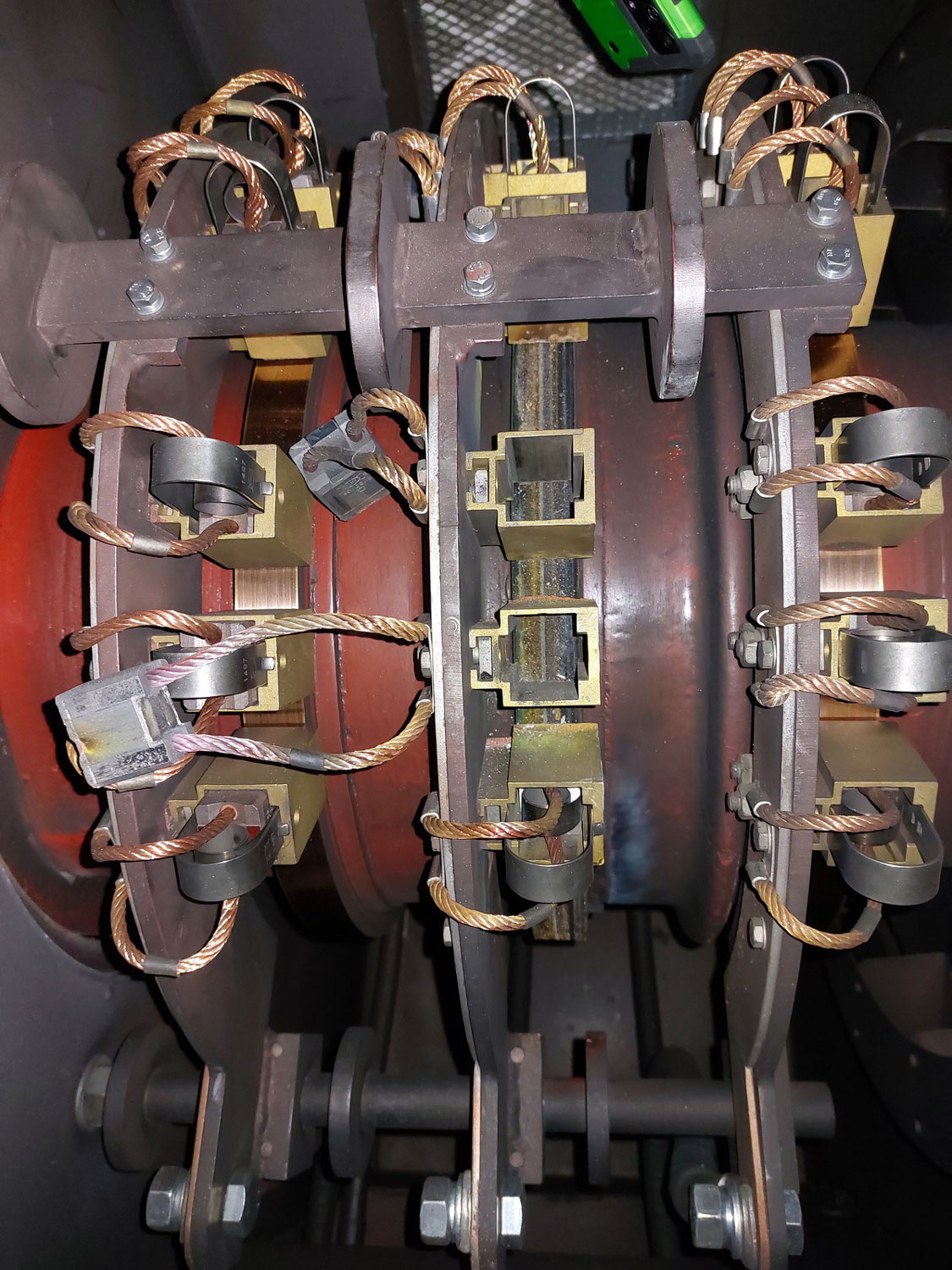
Raw mill motor slip rings
The ERIKS engineers quickly got to work cleaning and repairing the rings in-situ, carrying on the next morning, 1st November. The motor was tested that afternoon, but the engineers decided further investigation was needed. For optimum safety for all parties, this was to be carried out offsite, at ERIKS’ Chesterfield workshop.
ERIKS collected the motor from the customer’s site while arrangements were made to maximise the number of people available to work on the problem day and night on 2nd and 3rd November. Because of the huge potential loss to the customer, the motor was prioritised.
Result
Thanks to good planning and the expertise and know-how of ERIKS engineers, the slip rings were repaired in double quick time. A successful test run was carried out on 4th November and by Bonfire Night — six days later and three days ahead of estimate —the motor was back in place and the raw mill ready to roll again.
The slip ring repair and motor rebuild comprised cleaning, polishing, and skimming the slip rings. In all, it took 343 working hours, including engineers’ time on site, working through the day and night at the workshop, and reinstalling the motor back on site once the work was done.
And because the customer had the motor back three days sooner than anticipated, a further 8,000 tonnes of production was saved, worth a total of £560,000.
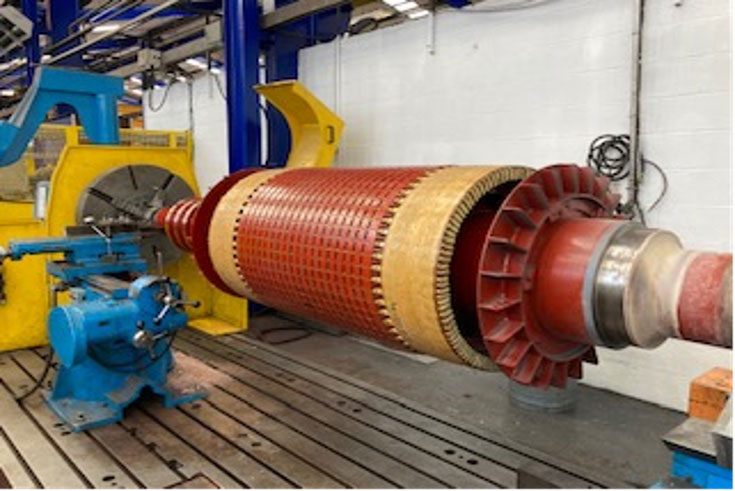
Raw mill motor in-situ
To avoid similar problems in the future, ERIKS recommended a new slip rings assembly, and a specialist visited the site to monitor the brush gear, bearings, and alignment – all general in-situ health checks while the motor is on the application. They also reviewed the maintenance schedule, proposed improvements and offered additional best practice training.
In the next scheduled shut-down, ERIKS are looking to improve and upgrade the brush gear on the motor, which has seen some deterioration in service and due to previous third-party repairs, and also to reverse engineer a new set of slip rings which the customer can use as a spare set in the future.
ERIKS went above and beyond with this repair — but that didn’t mean other customers with jobs in the workshop were affected. Once the motor had been returned to the customer, ERIKS engineers continued to work overtime and extra night shifts to ensure all the other jobs were completed on schedule.
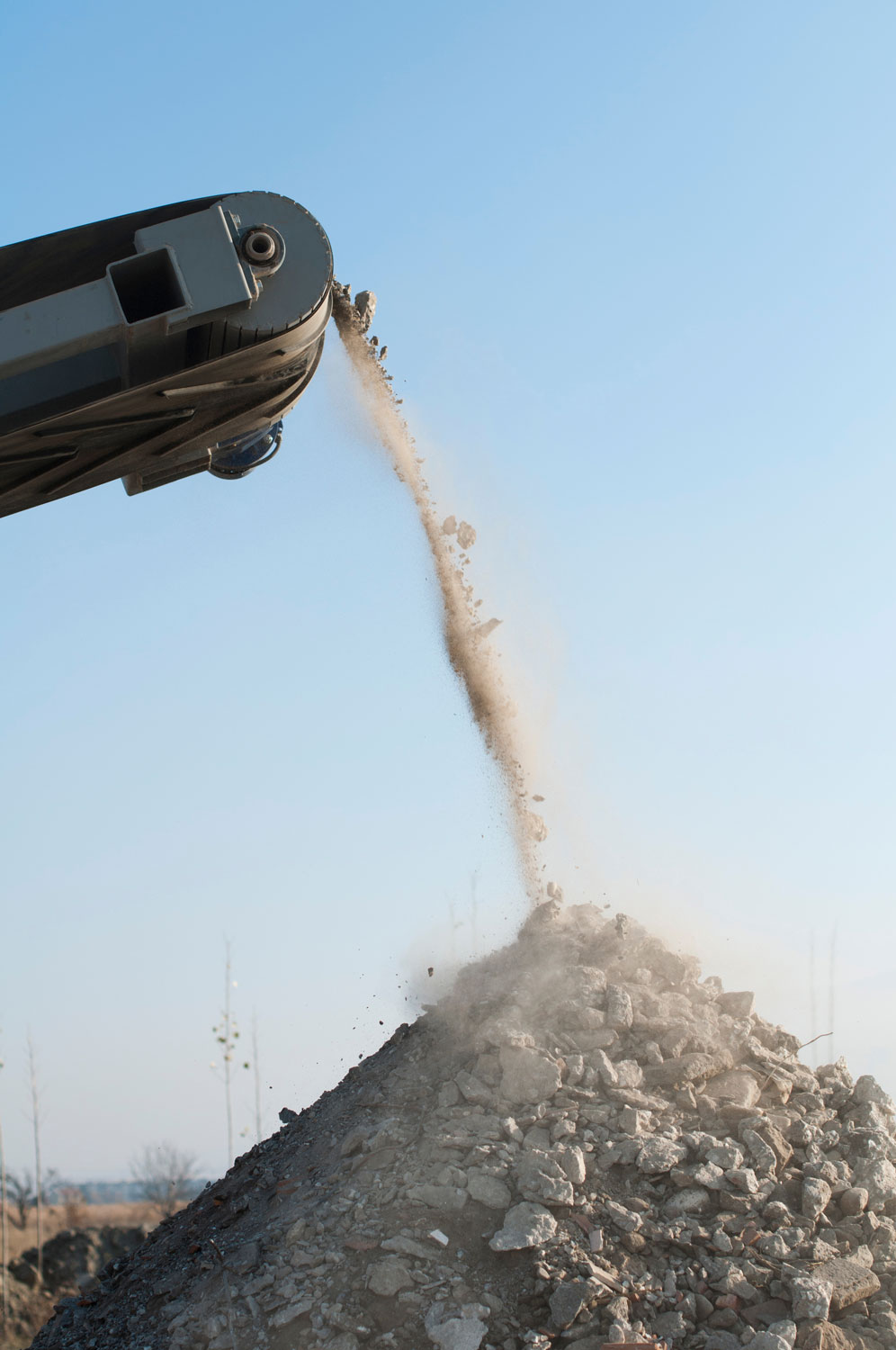
Crushed rock ready to be turned into meal
The ability to flex to deal with emergencies without jeopardising regular maintenance work means that every ERIKS customer can rely on speedy turnaround and on-schedule maintenance and repair.
An unrivalled nationwide network of workshops around the UK provides local engineering solutions to customers, either within in the workshops or via qualified and trained ERIKS engineers attending on site. In addition, ERIKS has specialist workshops for larger, heavier, and more complicated repairs – such as Chesterfield, which specialises in high voltage motor and generator repairs. Thanks to ERIKS, even a Halloween horror story can have a happy ending.
In Summary
A customer risked losing six weeks’ production because their raw mill motor’s slip rings were heavily damaged, needing replacement or repair. ERIKS prioritised the repair and managed to get the motor up and running again, three days earlier than anticipated, along with planning improvements for the future maintenance schedule.
- 8000 tonnes production saved at a cost of £560,000.
- Costly six-week downtime avoided.
- Prioritised repair with no impact on other customers’ work
- Rapid response and overnight repairs kept disruption to a minimum.
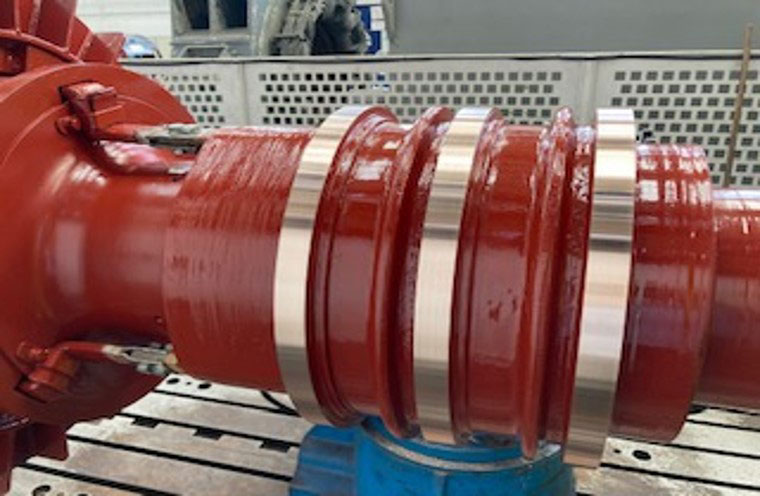