In this article
Upgraded manifolds are the cat’s whiskers
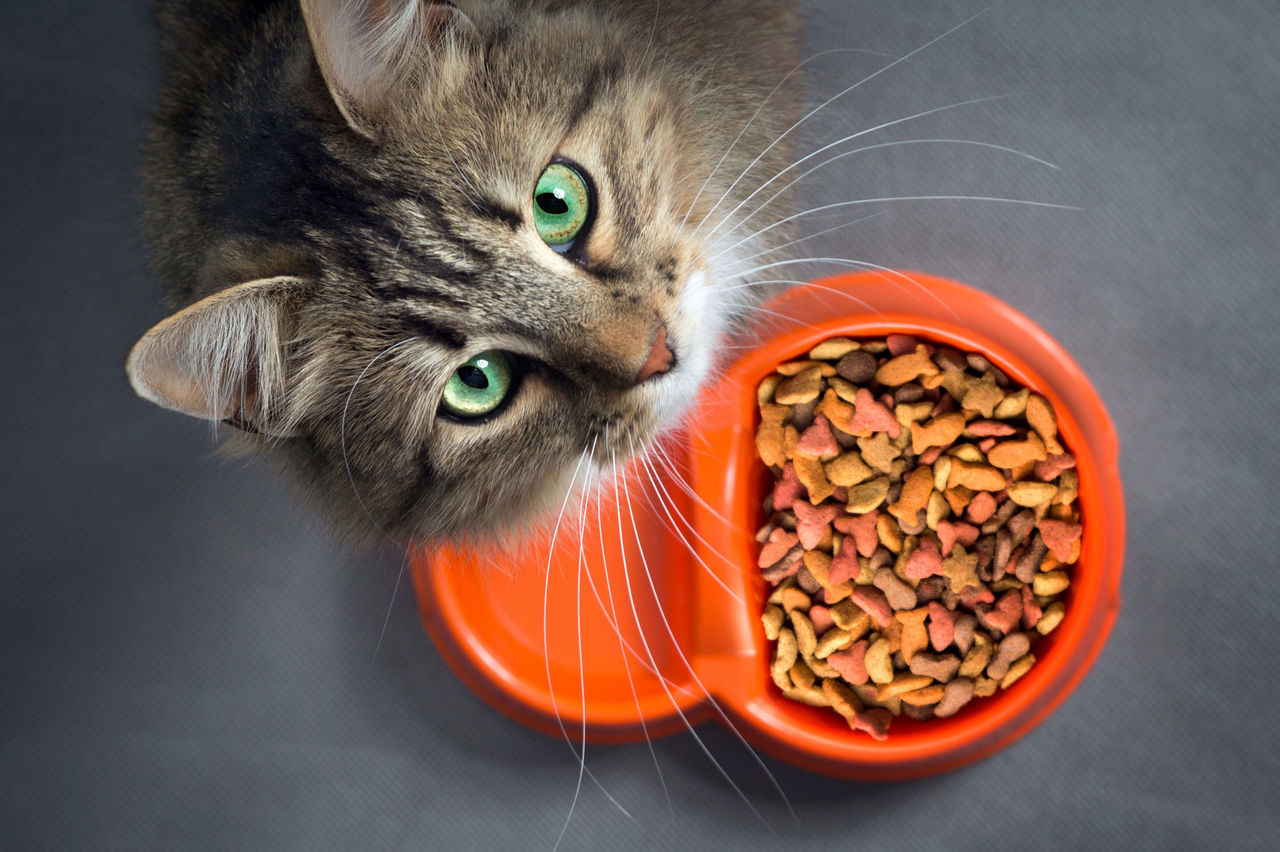
Industry Sector:
Food and Beverage
Application:
Volpak Filling and Wrapping Line
Actual Saving:
£4,800
Payback period:
3 Months
Product/Service:
- Fluid power, transfer & control
- Obsolescence support
- Design review
Customer Benefits:
- Increased uptime
- Increased efficiency
- Maintenance reduction
- Reduction of lead-time
- Productivity savings
Operating in a high-production environment, one large pet food manufacturer was experiencing issues during the phase-out of their current valve manifolds on the Volpak filling lines, opting to switch like-for-like during reactive maintenance activities, resulting in extended downtime when failures occurred, with costs exceeding £4,000.
Challenge
If an asset fails mid production run, it can cause serious problems. You may not have any spares in stock, or worst-case scenario, the product from the line must be completely scrapped. Either way, the end result is the same: lost production through unplanned downtime, lost time through sourcing alternative solutions, and lost money hitting the bottom line of the business.
Solution
The phase-out presented an opportunity for a design review of the filling line, with the aim of increasing reliability, optimising parts availability, and achieving savings on MRO spares. Working with Festo – the valve manifold OEM – an updated valve manifold solution was proposed.
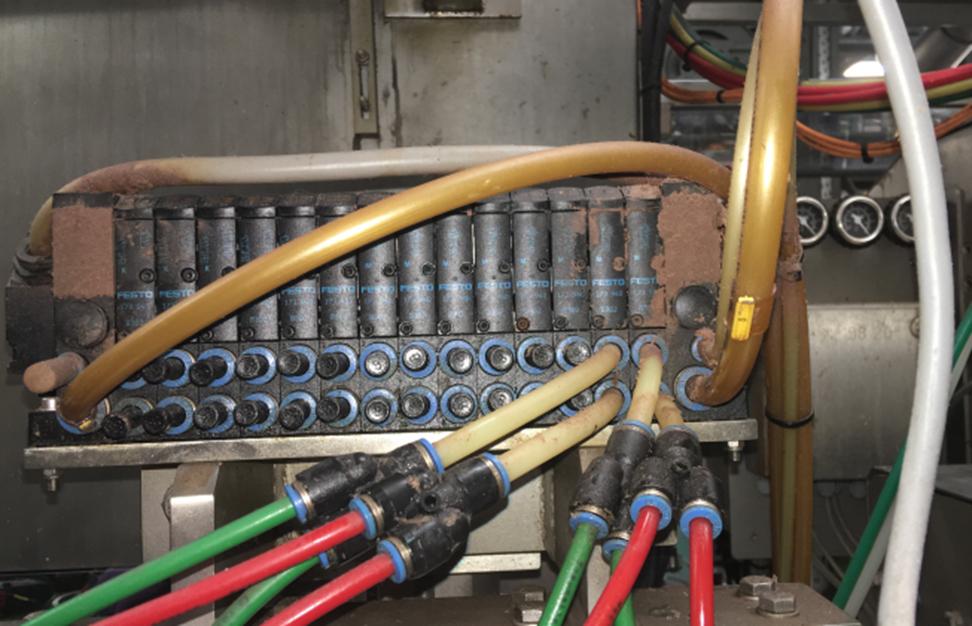
Obsolete manifold soltuion
ERIKS engineers took control of the project management, minimising the downtime needed for the changeover to the new manifolds, ensuring that any associated modifications were completed simultaneously. With the support of installation engineers, a pilot installation and commissioning was undertaken to allow for de-snagging, before rolling-out the new valve manifolds across all machines on site.
Result
The new upgraded valve manifold solution has not only future-proofed the assets, but now facilitates faster repairs, with replacement components easier to obtain. The replacement units have a higher B10 value (longer expected life), and will require less scheduled maintenance, meaning that the lines can run for longer, uninterrupted, freeing-up engineers’ time, while offering improved Overall Equipment Effectiveness.
Now, when maintenance is required, lead times are shorter, enabling stock reductions, and maintenance costs are driven down for the upgraded units compared to the previous manifold valves. The customer’s initial investment of £1,200 for the new units, was recouped within the first three month, resulting in savings of £4,800.