In this article
When Father Christmas wore a boiler suit
ERIKS' engineering doing what Santa's elves couldn't
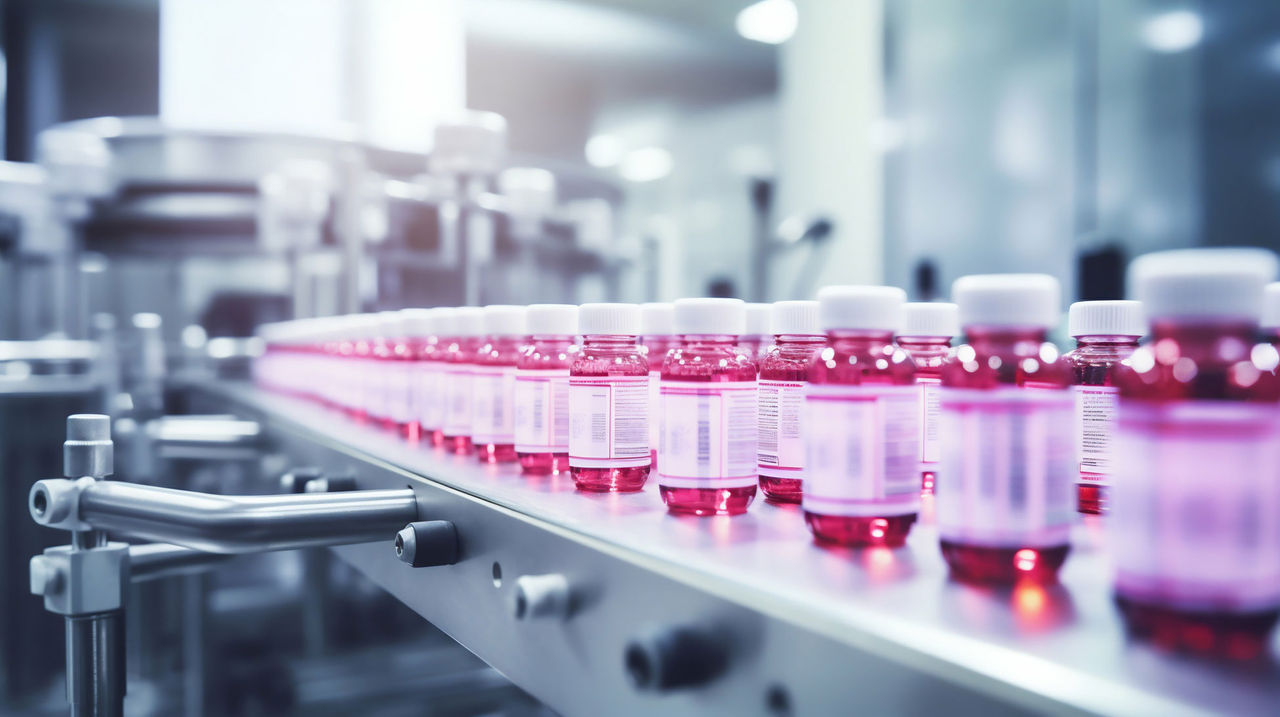
Industry Sector:
Pharmaceutical
Application:
Printing and Labelling machine
Actual Saving:
£165,000
Payback period:
3 Weeks
Product/Service:
- Gearbox
- Re-designing
- Re-engineering
Customer Benefits:
- Reduced lead time
- Reduced downtime
- Lost production avoided
- Improved asset performance
Sometimes it doesn’t matter if you’ve been naughty or nice. If a critical asset decides it’s going to fail, it will fail – even if it threatens to ruin your Christmas.
And there’s a well-known saying about presents: that the best things come in small packages. But the fact is, the worst things can do too. So even though the gearbox of this customer’s printing and labelling machine is relatively small, the impact on production if it fails will be significant.
Fortunately there was no need for ERIKS’ engineers to come down the chimney. With ERIKS OnSite team already on-hand at the customer’s facility, a brief jingle of telephone bells brought next-day support to the door.
Challenge
The customer manufactures and packages pharmaceutical products. The packages are individually labelled, with an average of 318,000 packs per week passing through the printing and labelling machine, which operates 24/7.
The machine includes a small but critical non-standard gearbox. Like most gearboxes this has one output shaft. But unusually, it features two input shafts – one of which is connected to a tachometer.
A local supplier had previously removed, stripped down, inspected and assessed the gearbox as being worn but operational, before reassembling and reinstalling it. Meanwhile, with no spare in stock, the customer had placed an order for a replacement, but the OEM’s lead time meant delivery was not due for around 4 months.
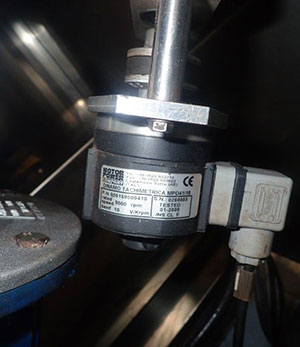
Tachometer fitted to input shaft
Subsequent monitoring and observations by the customer’s own maintenance engineers convinced them that there were developing issues with the existing gearbox which needed further investigation. With the customer’s Christmas shutdown only a week away, there was no time to lose.
Solution
ERIKS OnSite team contacted the ERIKS Drives and Rotating Equipment Product Business Unit (PBU), which deployed an Engineering Manager to the customer’s site the very next day.
His expert inspection confirmed that extensive wear to the gearbox internals would inevitably soon lead to catastrophic failure. With no chance of the replacement OEM gearbox being delivered before the asset failed, some suppliers would have struggled to come up with even one answer to the problem. ERIKS presented the customer with three possible options to save the day.
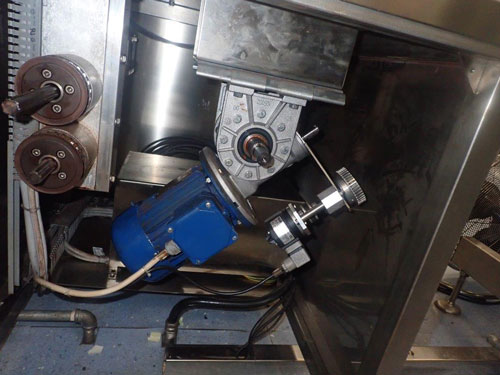
Critical non-standard gearbox in-situ
The first was to modify the input shaft to accommodate the tachometer connection. The second was to manufacture an entirely new double worm output shaft. And the third was to reposition the tachometer onto the non-drive end of the motor.
The customer carefully considered all three alternatives, before deciding that the first solution – a gearbox modified to enable the input shaft to connect to the tachometer – was the preferred choice. There was, however, one important caveat. To minimise downtime and avoid excessive lost production, ERIKS was tasked with completing the modification over the customer’s Christmas shutdown period, so the replacement gearbox would be ready for installation immediately before production restarted after the holidays.
With no Christmas elves to lend a hand, ERIKS engineers at the PBU put their own Christmas plans on hold, and began work on assessing the quickest and most effective way to deliver the result the customer wanted.
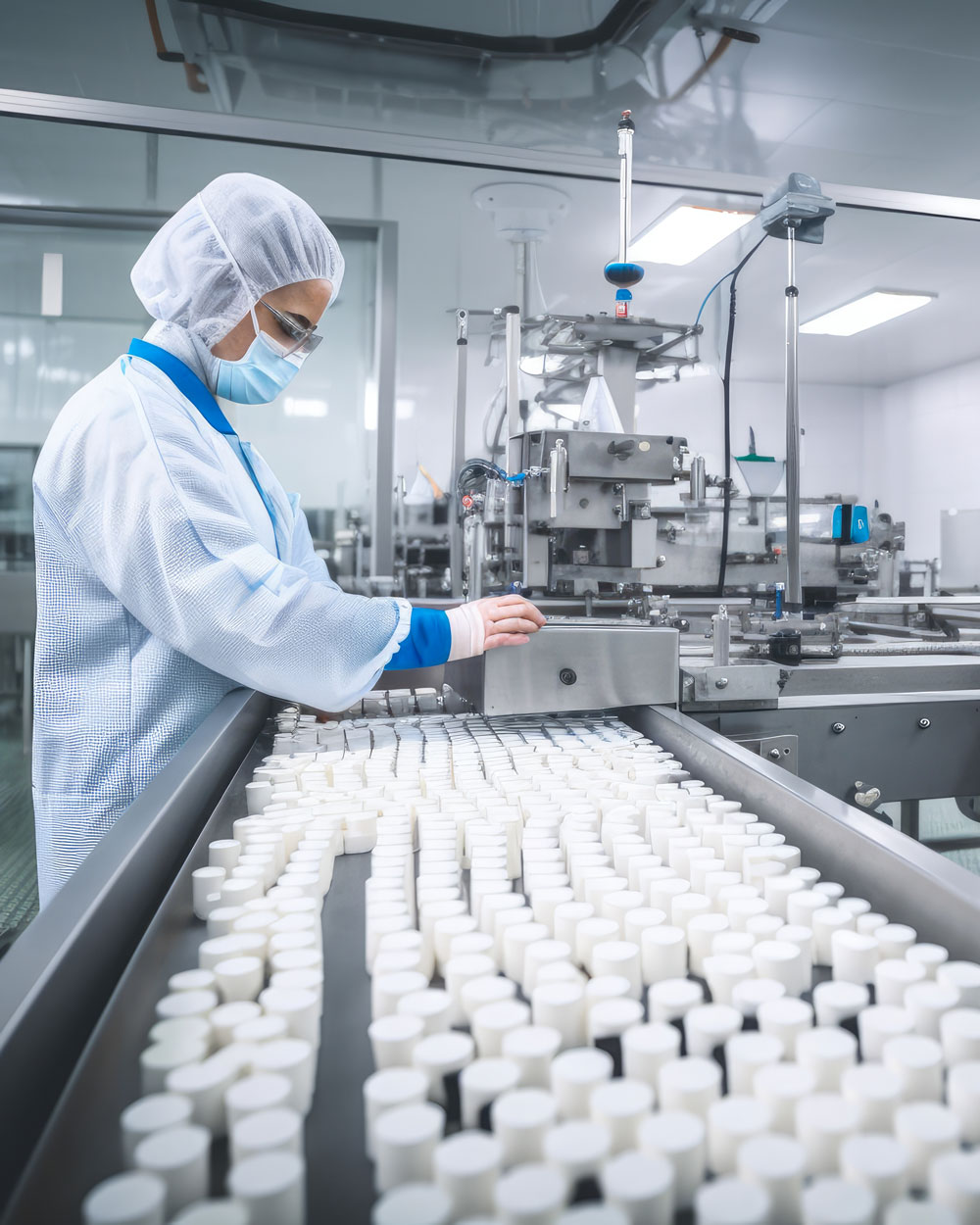
Pharmaceutical production process
The first time-saving step was to decide to carry out an adaptation of a standard gearbox rather than starting from scratch to build a special unit. The adaptation required was to accommodate a double input: one for the motor and one for the tachometer. However this wasn’t as simple as merely modifying the worm shaft. Complicated calculations were required in advance of specifying the modifications, to ensure the proposed changes didn’t affect transmission of the correct amount of torque.
If they did, there was a risk of unacceptable torsional stresses, leading to shearing of the shaft and catastrophic failure of the adapted gearbox.
With the calculations worked out to the satisfaction of the engineers, and the manufacturing drawings completed, the adaptation of the standard gearbox could begin. Firstly, the gearbox had to be dismantled ready for the changes to be made. Then the worm shafts had to be modified to suit the new design. And of course the gearbox casing also required adaptation and re-engineering, to accommodate the double output worm shaft.
With ERIKS’ engineers putting their Christmas plans on hold, all this was taking place at top speed, to ensure the customer got a gearbox which not only met their requirements and their budget, but also their tight and far from festive timescale.
Result
The finished gearbox was delivered by ERIKS to the customer’s site on 30th December. The customer then tasked a local installer with the job of installation – in just one day – so the labelling line could be ready to roll as soon as the seasonal shutdown ended.
By working through this shutdown ERIKS was able to help the customer avoid disruption to their printing and labelling line, minimise downtime, and prevent a certain loss of almost £8,000 a day should the original gearbox have failed. The total potential production losses, based on the OEM’s predicted lead time for the new gearbox, have been calculated by the customer as no less than £165,000.
In addition, by engineering the new gearbox ready for installation while the customer was still awaiting delivery from the OEM, ERIKS has helped avert the risk of further disruption in the future. The new gearbox – when it finally does arrive – will go straight into the customer’s parts store. So if or when the same situation arises, there will be a ready-made replacement on hand for a swift swap-out.
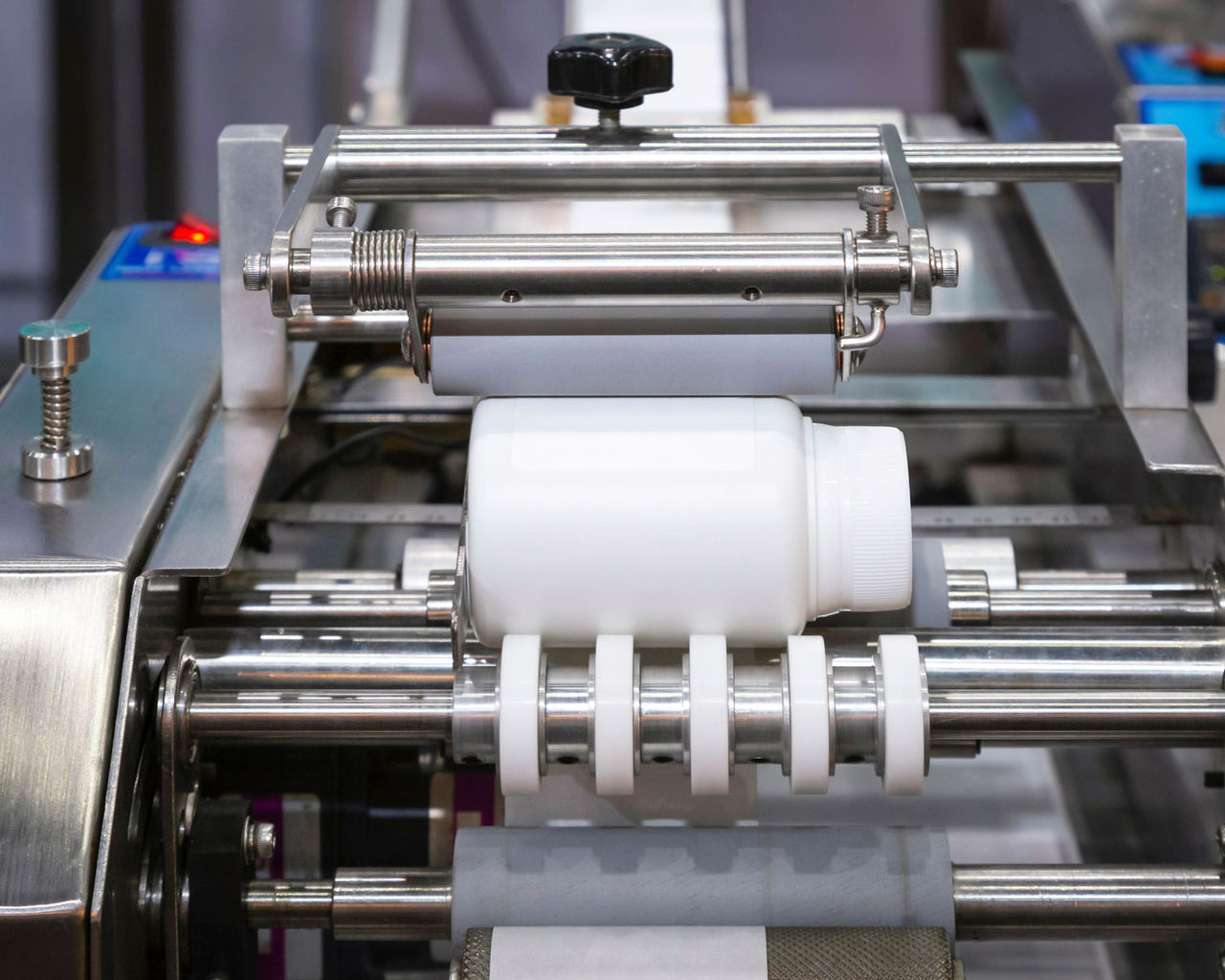
Individual labelling process
Twelve months on from the installation the new gearbox is still operating smoothly. In fact the customer’s own engineers have reported that it is running better than ever. Perhaps that’s a result of ERIKS’ engineering know-how and attention to detail in producing a one-off, non-standard item, compared with a relatively mass-produced OEM-engineered asset.