In this article
Expertise That Goes Deeper
Supporting Royal Navy Submarine Simulator Maintenance
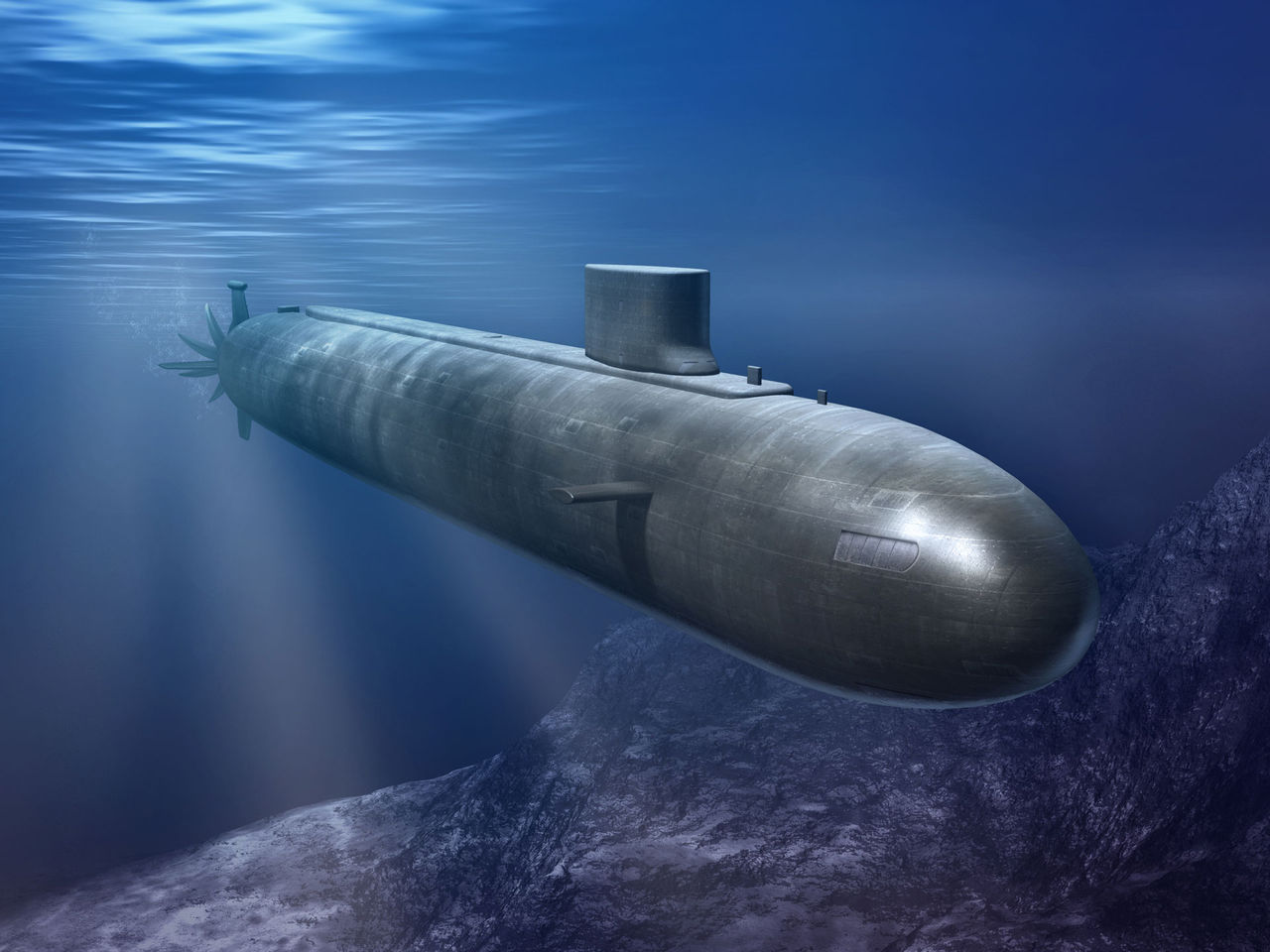
Industry Sector:
Defence
Application:
Submarine Simulator
Actual Saving:
N/A
Payback period:
N/A
Product/Service:
- Industrial Hose
- Hydraulic Hose
Customer Benefits:
- Improved equipment performance
- Enhance traceability
- Increased operational readiness
- Proactive lifecycle management
- Risk mitigation
- Supply chain resilience
- Proven defence sector partner
When maintaining a Royal Navy submarine simulator — a vital training asset valued at over £1 billion — there is no margin for error.
Strict security, confined working spaces, critical timelines, and high compliance standards meant that carrying out a 10-year hydraulic hose overhaul would require exceptional expertise, planning, and precision.
Challenge
Before even setting foot on-site, ERIKS’ Hose Technicians had to undergo extensive background checks and were required to work under escort within the Naval base. The physical environment presented its own challenges: cramped, scaffolded spaces, limited access, and a non-negotiable deadline — if the overhaul was not completed on time, service would be delayed for an entire year, potentially impacting the Royal Navy’s operational readiness.
Adding to the complexity, the overhaul involved replacing 63 hydraulic hoses and a hydraulic power pack, alongside the safe management of hydraulic oil removal and disposal. When supply chain issues threatened to delay critical components, the risk of project disruption loomed large.
The Royal Navy, through their partner Thales, needed a supply and service partner with the agility, technical knowledge, and resilience to overcome these obstacles — without compromising safety, quality, or deadlines.
Solution
Drawing on over 40 years of hydraulics experience, ERIKS’ team from the Northampton Centre of Excellence for Hose Technology took full ownership of the project.
A full site-specific risk assessment was carried out by ERIKS’ Health & Safety experts to ensure safety compliance in the hazardous working environment. A comprehensive tag-out safety system was implemented before any work commenced.
To manage the hydraulic oil safely, ERIKS coordinated a specialist contractor to drain, remove, and dispose of the oil according to environmental regulations, and to replace all filtration units before hose work began.
Despite an unforeseen supply issue with the original hose supplier, ERIKS’ extensive industry network allowed a rapid pivot to an alternative approved supplier, ensuring that the project timeline remained intact.
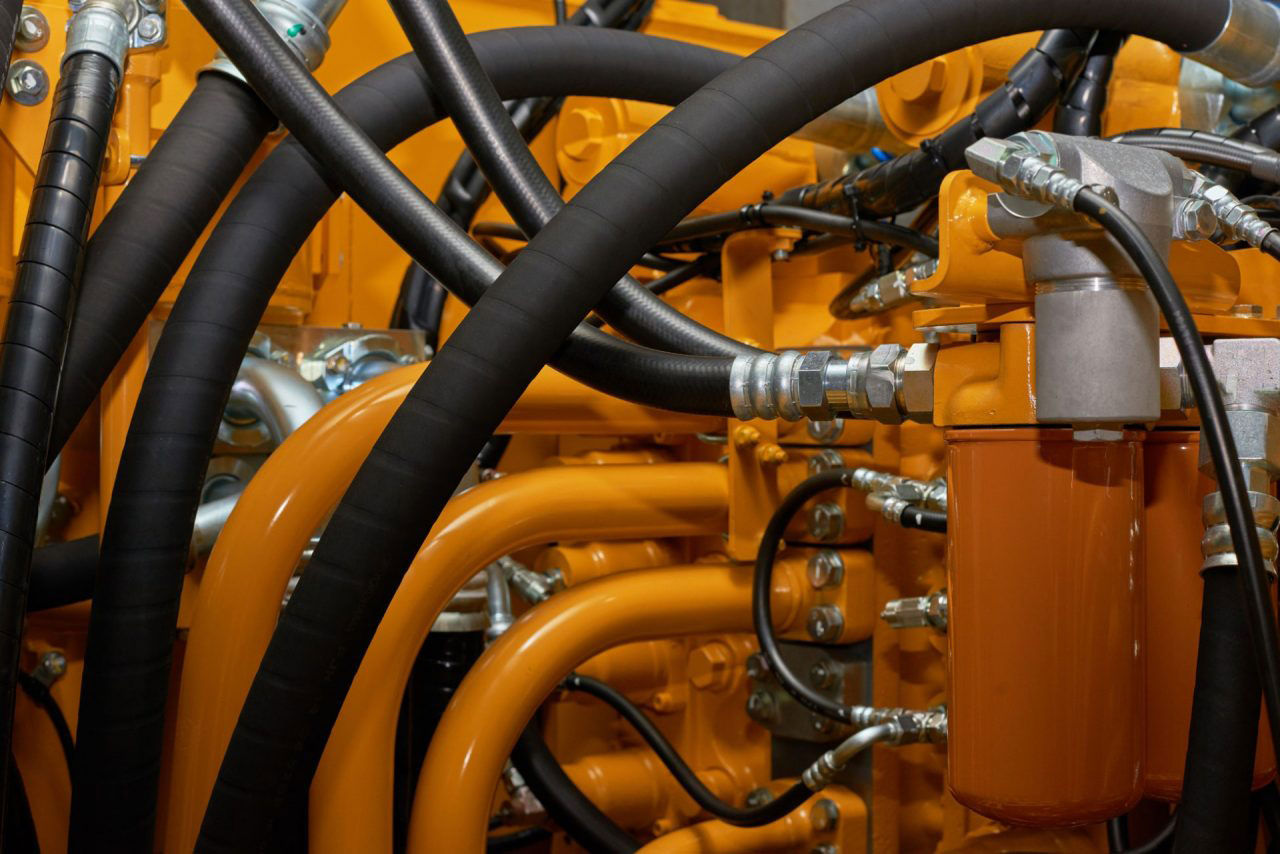
Rather than simply replacing like-for-like, ERIKS’ technicians used the opportunity to upgrade components where improved hose technologies were available. New hoses with better flow and pressure ratings were specified and installed, enhancing the simulator’s hydraulic performance.
Each newly installed hose was tagged with a unique barcode linked to the ERIKS Hose Asset Management app. This innovation enables complete traceability, immediate access to service records, and automated tracking of compliance with updated legislation. It also facilitates proactive lifecycle management, supporting annual inspections, pressure cycle testing, and timely replacements.
Result
Despite the site restrictions, tight deadlines, and mid-project supply challenges, ERIKS completed the entire hose and power pack overhaul with a full week to spare.
The result was a fully upgraded, fully traceable hydraulic system, delivering enhanced efficiency, improved performance, and future-proofed maintenance capability — all critical to the Royal Navy’s ongoing operational readiness.
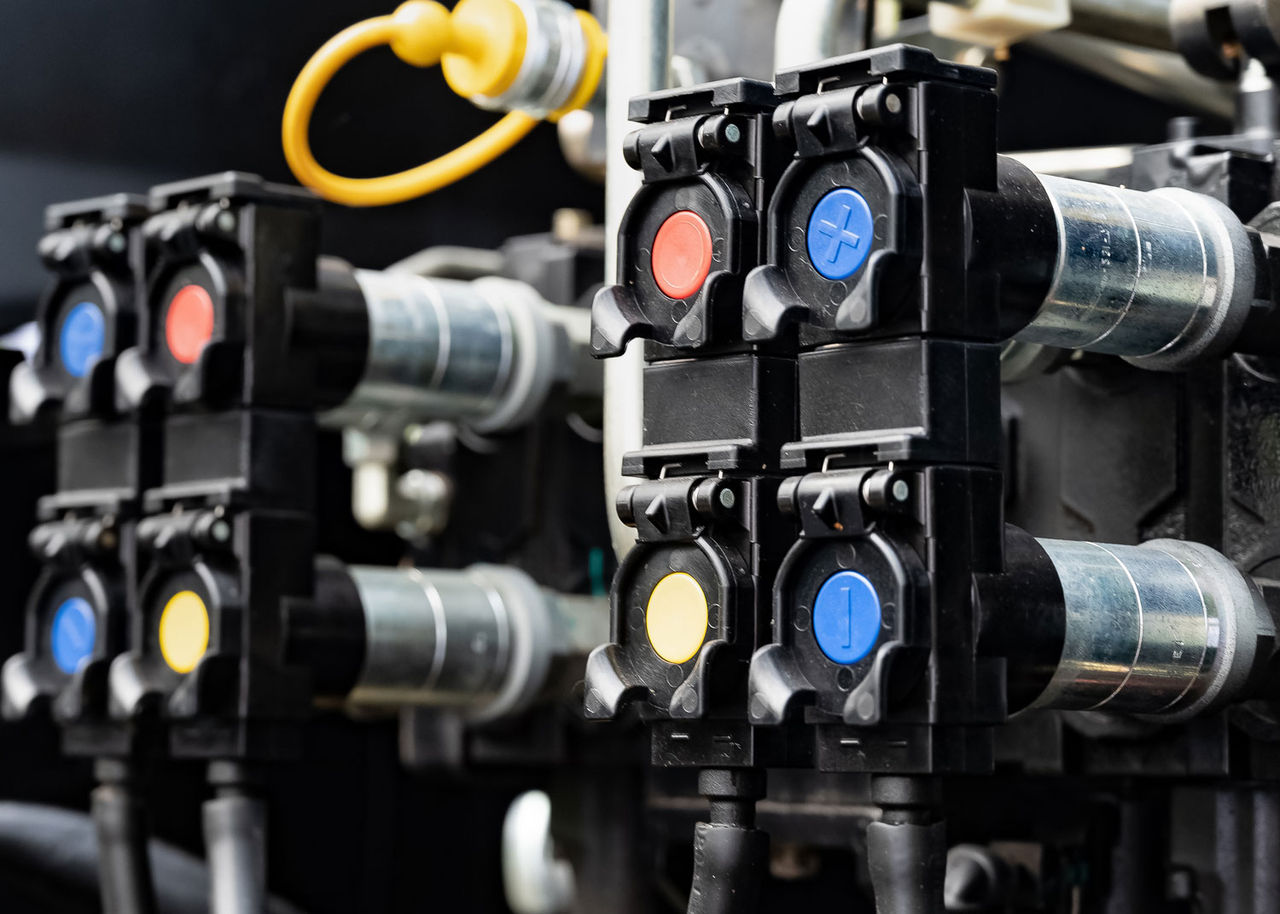
The success of the project not only reinforced the trust placed by Thales in ERIKS (following a previous successful overhaul of an RAF Airbus A400M Atlas flight simulator) but also cemented ERIKS’ reputation as a reliable partner for high-specification Defence sector projects.
Operating from the Northampton Centre of Excellence for Hose Technology, ERIKS once again demonstrated the value of combining deep technical know-how, proactive risk management, agile project execution, and commitment to customer outcomes.
Customer Benefits
- Improved Equipment Performance: Upgraded hoses deliver better flow rates and pressure resilience.
- Enhanced Traceability: Unique barcoded hose asset tracking supports ongoing compliance and maintenance.
- Increased Operational Readiness: Work completed ahead of schedule, avoiding service delays.
- Proactive Lifecycle Management: Automated service alerts and full compliance visibility via ERIKS Hose Asset Management app.
- Risk Mitigation: Full Health & Safety risk assessments and secure working practices ensured project success in a high-security environment.
- Supply Chain Resilience: Rapid resolution of supply issues protected critical project timelines.
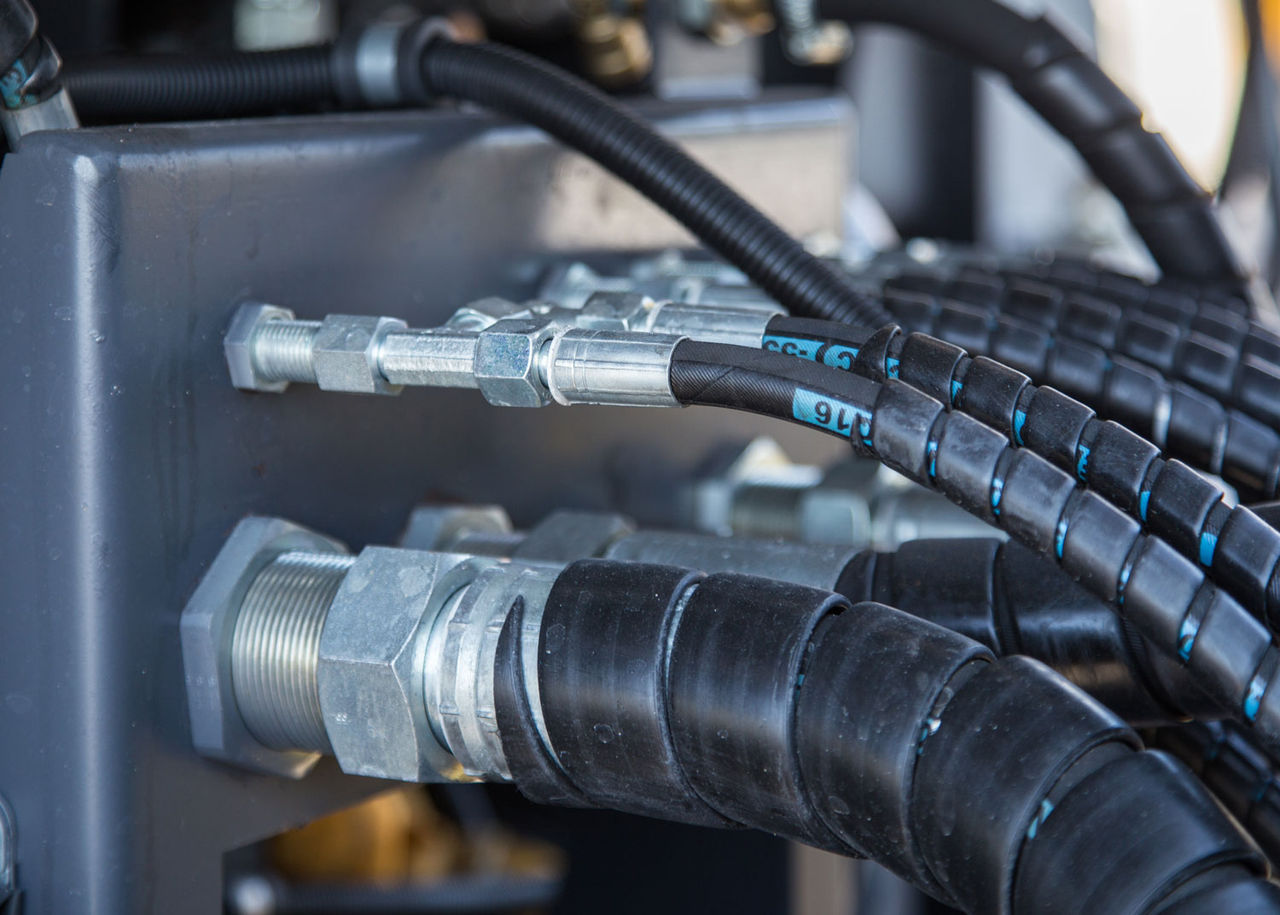
- Proven Defence Sector Partner: Demonstrated expertise in complex, secure site operations across multiple military platforms.