In this article
Escaping the energy costs trap
Steam trap survey sees costs evaporate
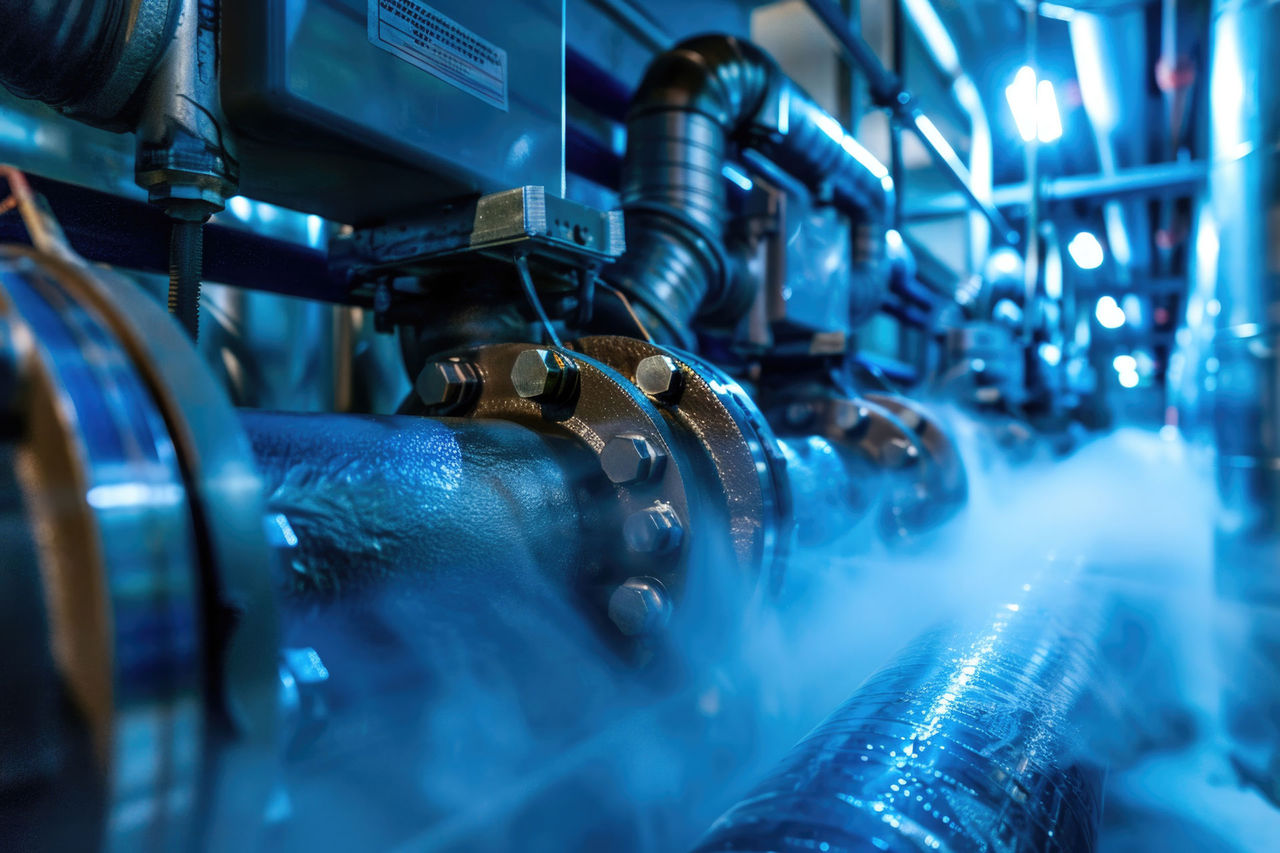
Industry Sector:
Food & Beverage
Application:
Site-wide steam system
Actual Saving:
£56,282
Payback period:
2 Months
Product/Service:
- Steam trap survey
Customer Benefits:
- Increased safety
- Energy efficiency
- Enhanced sustainability
- Environmental compliance
Sometimes energy savings can be discovered in the most unlikely places. And often, shrinking the energy bills is only part of the story. There can be wider positive implications for efficiency, productivity – and even safety. What’s needed is the know-how to identify the issue and the experience to see the bigger picture.
When an ERIKS Application Engineer visited the site of a major cereals manufacturer, he not only had the in-depth knowledge necessary to suggest energy-efficiency improvements, but also the expert partner supplier to help deliver them.
Challenge
Like most manufacturers facing ever-increasing energy costs, this customer was hoping to identify energy efficiencies. With so many energy-consuming assets on site – from motors to pumps and drives to fans – singling out the area where savings could be easiest to achieve required comprehensive know-how.
Together, the ERIKS Application Engineer and ERIKS Value Delivery Team were able to pinpoint the quickest win with the most favourable ratio of initial outlay to potential saving.
Solution
After inviting the Application Engineer on a tour of the site, followed by discussions with the Value Delivery Team, the customer had a range of savings opportunities to choose from, each with different potential benefits. The decision was made to accept ERIKS’ offer of a Steam Trap Survey, to be conducted by Spirax Sarco: an ERIKS Preferred Partner Supplier.
It is recommended that a Steam Trap Survey should be carried out every 12 months – or even more frequently if system pressure is over 30psi. However a longer period had elapsed since the customer’s most recent survey. It was clear that energy savings, efficiency improvements and safety enhancements were likely to be readily available.
The survey took six days, involving a total of 271 steam traps across the site.
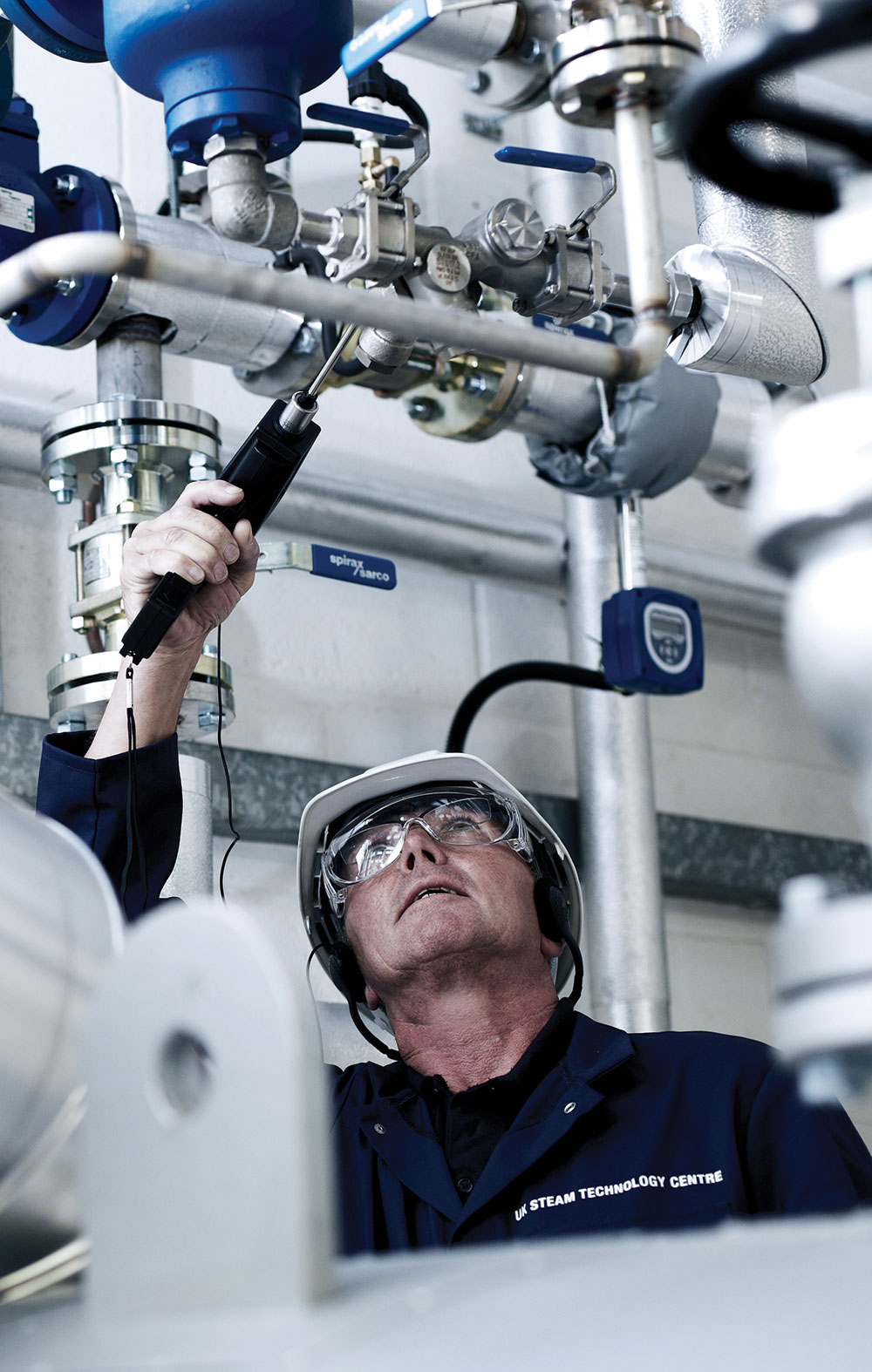
An engineer carrying out steam system audit
Heat measurement guns were used to measure the temperature in the steam traps and connected pipework. Any temperature anomaly indicated that steam was not passing freely through the system at that point, and / or that the condensate was not being efficiently recovered.
In either case, incorrect working could lead to excess water in the steam system. Initially this would mean the system would be operating inefficiently, with more energy required to generate more steam, and greater pressure required to achieve the same performance. Ultimately, potential knock-on effects would be:
- Increased corrosion
- Possible safety complications
- Water hammer, with the potential to damage other assets
- Water contamination (of equipment or even end-products)
Result
Of the 271 traps surveyed, representing the whole of the customer’s steam system, 147 (54%) were classed as operating correctly. 71 were not in use or redundant. This left 13% of the total traps classified as either failed open, failed closed, or cold.
The financial implications, identified in the survey, were annual energy losses through leaking traps of £84,250.07. Annual CO2 emissions from the failed open traps amounted to 335.83 tonnes.
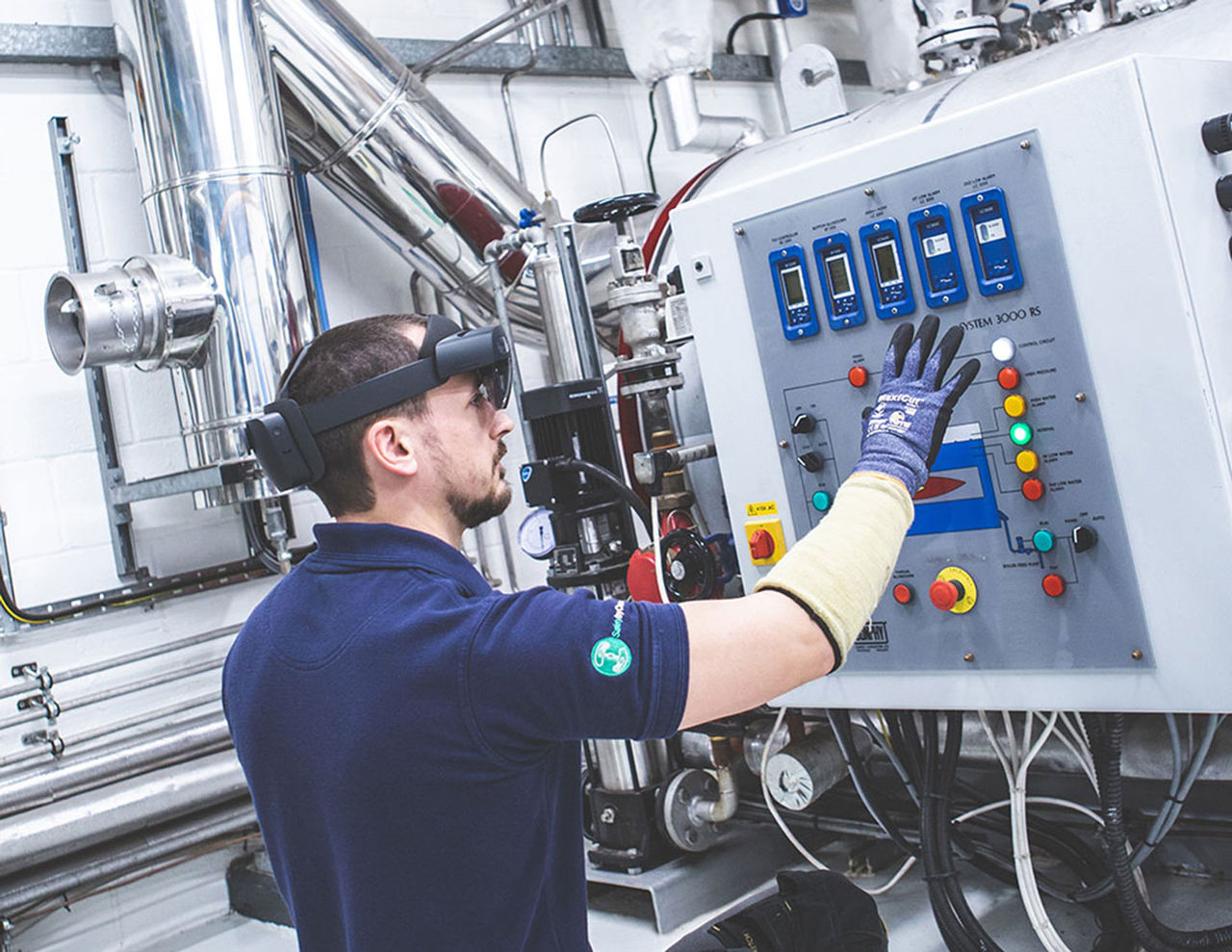
Additional Engineer carrying out steam system audit
With an investment of just £13,486.67 in replacement steam traps to remedy the losses, payback would take just two months. Understandably, the customer proceeded to replace or repair the failed and faulty traps identified in the survey.
12 months later, the total cost savings were calculated at £56,282, and the customer was on track to achieve sustainability targets.
Adopting Best Practice of an annual Steam Trap Survey would mean full steam ahead to repeat those kind of savings every year.