In this article
The future is now... with ERIKS Online Monitoring
Increase productivity, avoid unscheduled downtime
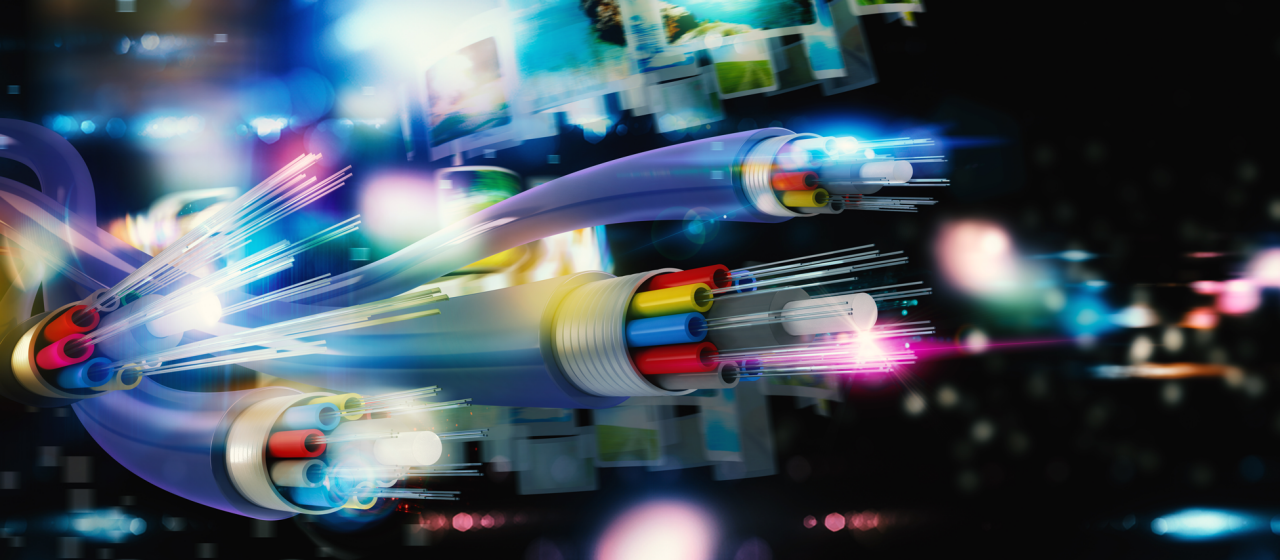
Industry Sector:
Electrical Manufacturing/Semicon
Application:
Twiner Main Drive Motor
Actual Saving:
£24,000 (cost avoidance)
Payback period:
1 day
Product/Service:
- Digital Reliability Services
- Online Condition Monitoring
- Re-Engineering
Customer Benefits:
- Increased uptime
- Reduced maintenance costs
- Improved lead times
- Future foresight and insight
- Prescriptive maintenance
Asset failures are one of the biggest burdens for engineering managers and manufacturing plants in their attempt to drive down costs and overheads. Failure to identify potential problems with complex machinery will only ever lead to catastrophic consequences.
In the case of one Network Solutions Provider, interruption of their production process would lead to scrapping an entire production run and starting again from step one.
Let the implications of a single asset failure sink in for one moment. An entire production run lost, excessive downtime, unscheduled maintenance, interruptions to the supply chain, or potential reputational damage could be just the start of losses spiralling out of control.
Challenge
Looking to avoid such catastrophic production losses, the customer turned to ERIKS Digital Reliability Services, which utilises state-of-the-art online monitoring through wireless sensors.

Digital Reliability Services dashboard analysis
Over a period of time, a warning alarm was triggered, highlighting that the Twiner Main Drive Motor was starting to fail.
Allowing this particular machine to run to failure would have cost the customer disproportionate amounts in lost production, and could easily be rectified with further investigation, avoiding a costly breakdown and the associated risks.
Solution
Investment in ERIKS Digital Reliability Services provided the customer with an early indication to an issue that otherwise would have remained undetected. From the data obtained, which comprised of tri-axis accelerometers logging velocity, acceleration and temperature, it was confirmed that the drive end bearing of the motor was in a serious state of deterioration and on a path to failure.
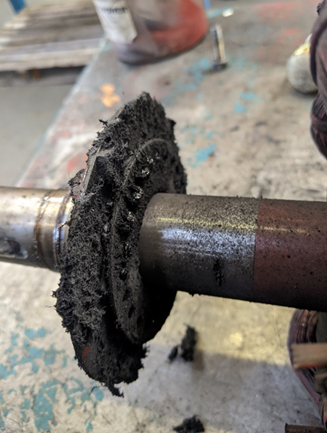
Deteriorated and contaminated Drive End
This was mainly due to lubricant contamination with the ingress of carbon from the natural design and construction of the machine forcing carbon dust through the vents causing issues over time.
Using the findings, and a remedial actions presented on the Strategic Asset Management dashboard the site engineers at the customer were able to make an informed decision on the best course of action to prevent a catastrophic breakdown.
In this case they contacted ERIKS to propose a corrective action plan to eliminate future contimination problems and manage the risk to their future production processs.