In this article
Improving electrical safety - and maintenance - in seconds
Absence of voltage testing offers a pleasant shock
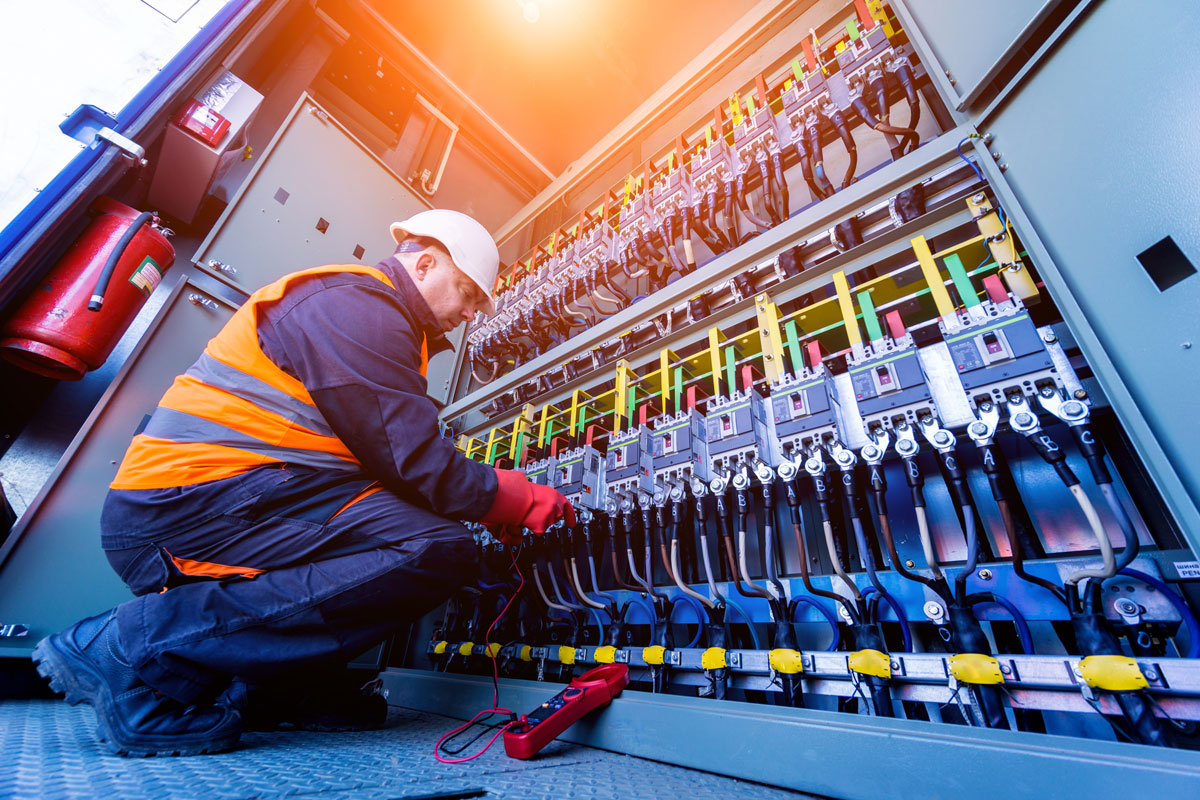
Industry Sector:
Construction
Application:
Electrical control panels
Actual Saving:
£121,298
Payback period:
4 Months
Product/Service:
- Panduit VeriSafe™ Absence of Voltage Tester
Customer Benefits:
- Risk mitigation
- Increased safety
- increased uptime
- Reduced mainteance time
Electrical safety isn’t a place to cut corners. There are strict procedures to follow to ensure the safety of everyone inspecting, maintaining or repairing electrical equipment, and they cannot be ignored. However, if there’s an equally safe but unbelievably faster way to achieve the same level of safety, who wouldn’t want to adopt it?
Industrial Injuries resulting from contact with live exposed wiring, transformers or electrical components are far too frequent, serious and costly. So like most employers, British Gypsum takes the safety of its employees seriously – including its maintenance engineers, who are likely to have the most frequent and repeated exposure to the risk of electric shock.
But the real shock came with advice from ERIKS and Panduit, which revealed how they could reduce the risk, increase safety, and also free up hours of engineers’ time for other maintenance tasks.
Challenge
British Gypsum has dozens of electrical panels associated with a wide variety of assets across its two sites in East Leake, Notts., and Robertsbridge, East Sussex, where it produces plaster and plasterboard for the construction industry.
To maintain the manufacturing equipment at its optimum efficiency, the company’s maintenance engineers carry out regular and frequent predictive maintenance tests, such as thermographic testing. These require safe access to the electrical panels to ensure the absence of voltage can be reliably verified.
This is a time-consuming, complex procedure, open to error, complacency and risk.
Usually involving a portable, handheld, voltage test instrument, the process requires the instument user to don PPE before proceeding. This takes time even before starting the testing. There is also the risk that the instrument itself has a mechanical or electrical failure, or is incorrectly used and gives a false result. Then the testing exposes the user to risk of shock if voltage is present. And once the test has been completed, removing and storing the PPE takes up more valuable time.
This is all time which could be better used for the actual maintenance task. It is also time during which the asset is out of action, resulting in lost production. Even so, a responsible employer such as British Gypsum would never contemplate shortcuts to save time at the risk of reducing electrical safety.
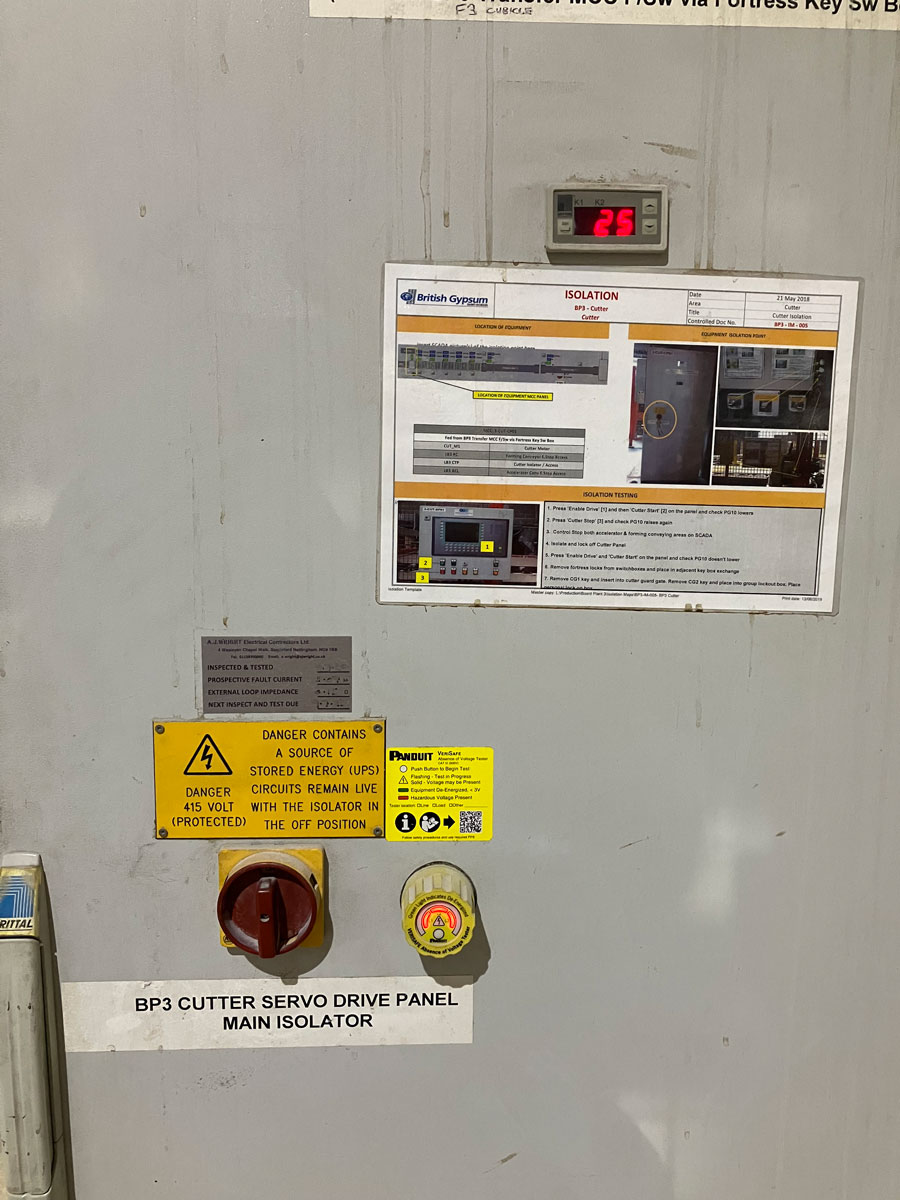
VeriSafe™ Absence of Voltage Tester in-situ
What’s needed is a method of verifying absence of voltage in less time, but with no less safety or reliability.
Solution
After British Gypsum contacted their local ERIKS Branch Manager, an ERIKS electrical safety expert and a Panduit representative approached the customer with information about the automated Panduit VeriSafe™ Absence of Voltage Tester (AVT).
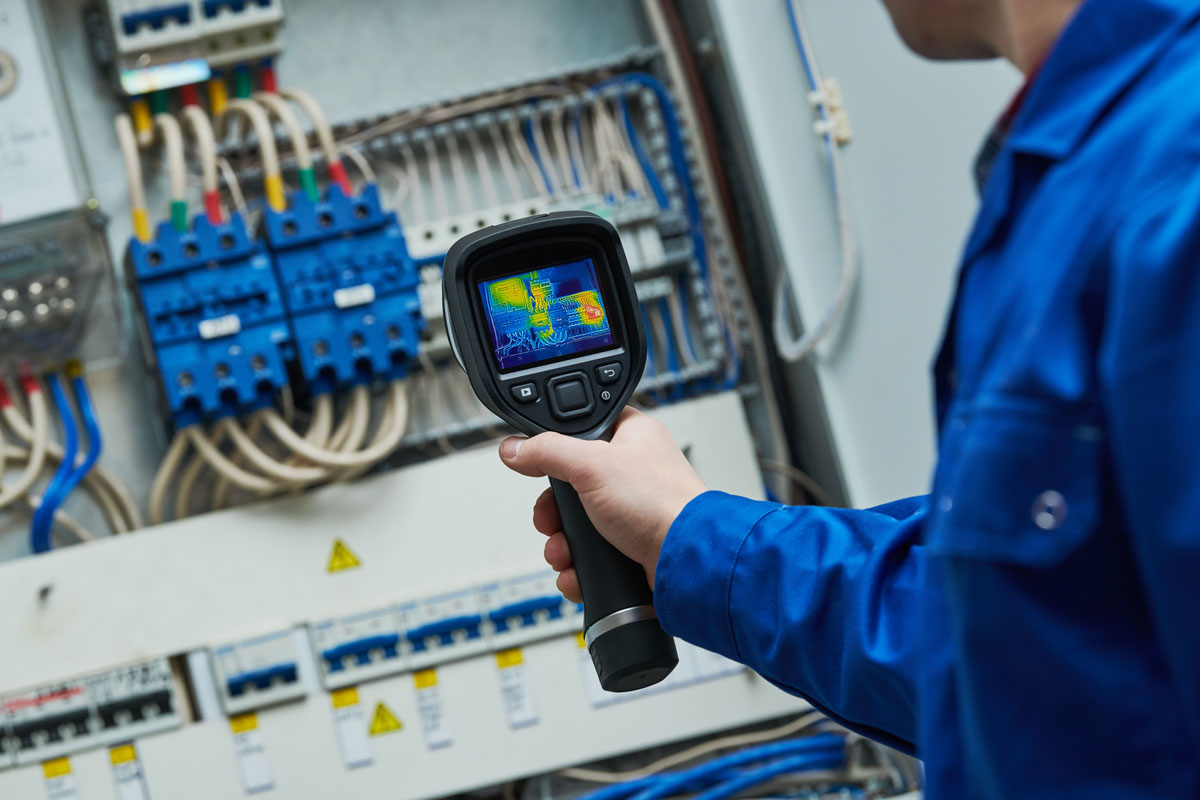
Thermographic testing
As a new technology for electrical testing, the VeriSafe™ AVT is the first AVT tailored for electrical enclosures. By simplifying and automating the voltage verification process, it not only eliminates the need for direct exposure to electrical hazards, but also determines the voltage status before equipment is accessed. So it reduces risk, cuts maintenance time and increases uptime.
In fact, automated verification with the VeriSafe™ AVT shortens the procedure to a matter of seconds, while maintaining absolute operator safety.
Using a portable tester, the operator needs to don PPE, test the tester, check for voltage, and retest the tester, before being able to start the actual maintenance or repair. And all the time during the testing of the tester, the voltage checking and the retesting, the operator is potentially exposed to electrical hazards.
Using the VeriSafe™ AVT, all the engineer needs to do is activate the automated tester, note the indicator status and – if a green indicator is illuminated – open the enclosure to start work. At no time throughout the sequence of events – which in any case takes just seconds – is the engineer exposed to any electrical hazard.
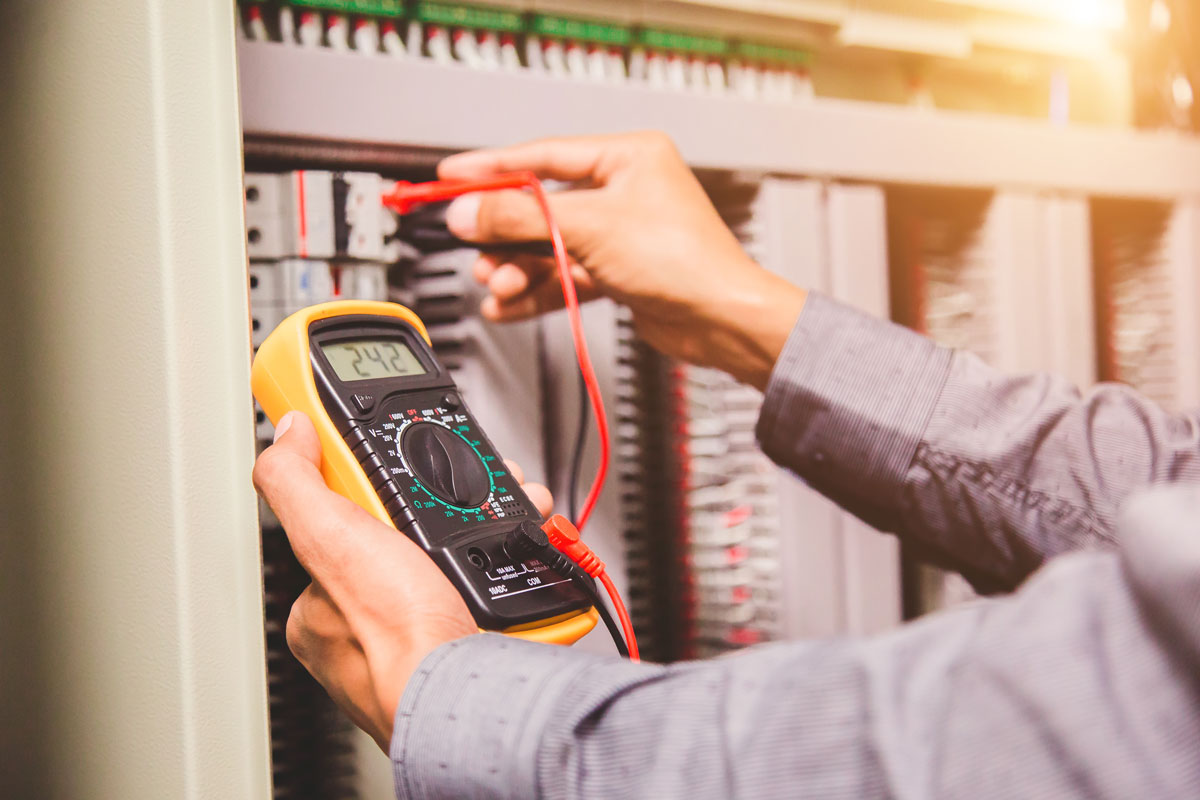
Electrical panel undergoing testing
The amount of time which can be saved on testing is so significant that at first the customer couldn’t believe it. So ERIKS and Panduit not only provided an initial demostration using a test rig, but followed it up with a VeriSafe™ installation on a number of electrical panels in a trial area at one of the British Gypsum sites.
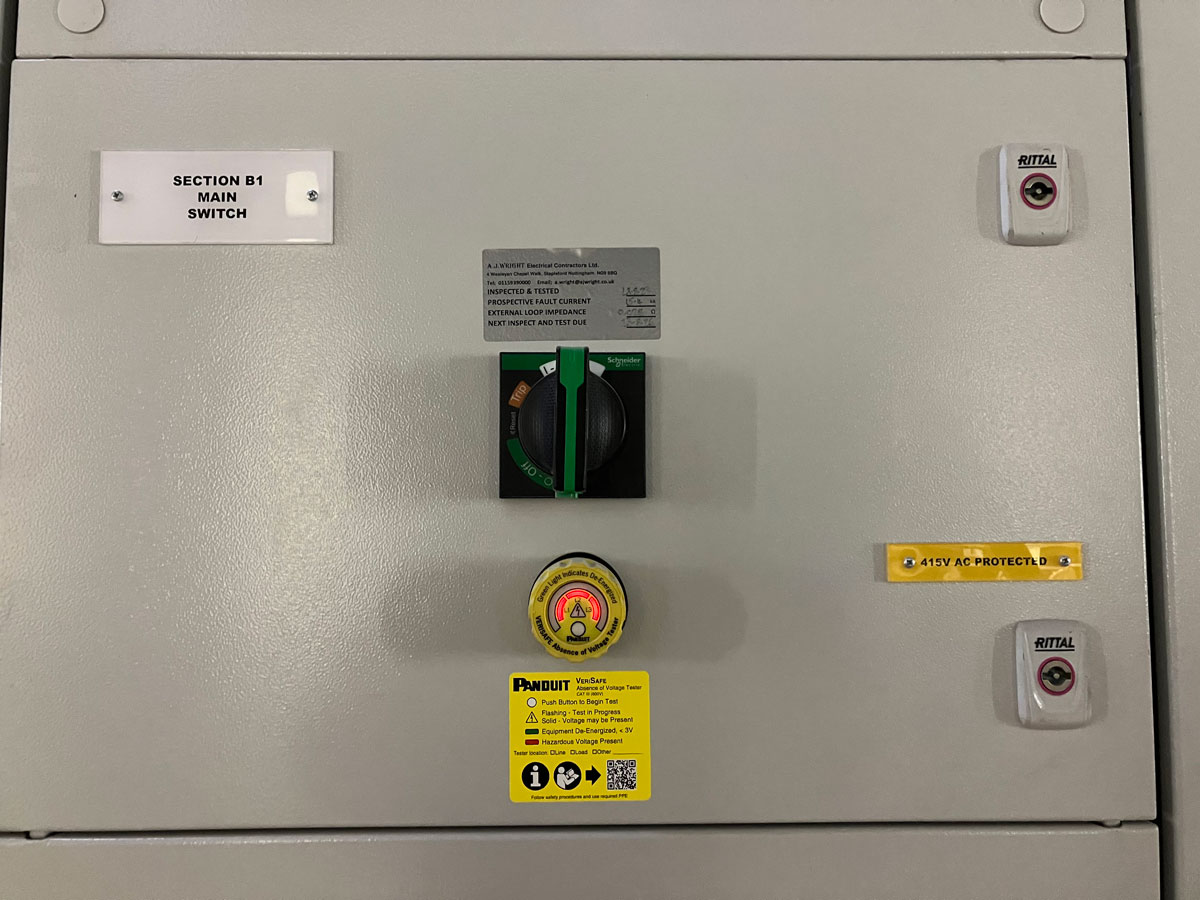
Result
The results, in terms of time saved for maintenance engineers with no compromise on safety, were impressive. So impressive that British Gypsum proceeded to install 103 Panduit VeriSafe™ AVTs at their Nottinghamshire site, 50 at their East Sussex site and another 20 at their site in Leeds.
And the customer’s maintenance engineers not only have the reassurance of enhanced electrical safety. They have also recouped around 50% of the time previously spent on voltage testing and LOTO procedures, to dedicate to more productive maintenance tasks to enhance operational efficiency and productivity.