In this article
Need a fast, cost-effective belt repair? Unique Polymer Systems deliver...
A belt that holds up your trousers or skirt is a good thing. A belt that holds up production isn’t. Conveyor belt problems are common but – thanks to a unique rubber repair solution – lengthy downtime, lost productivity and expensive emergency belt replacements can be avoided.
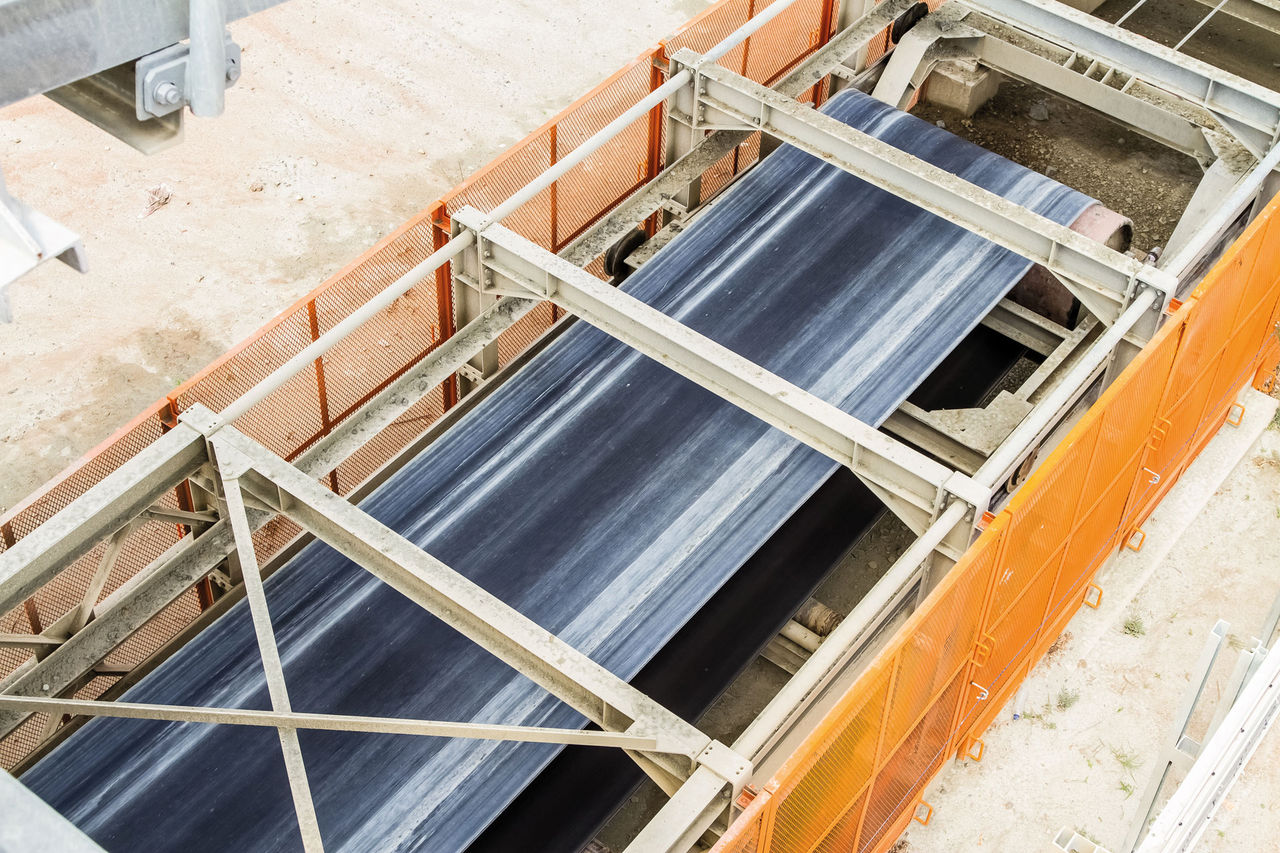
The list of things that can go wrong with a conveyor belt is almost as long as some conveyor belts themselves. From excessive wear damage at the edge of the belt, to hardened and cracked belts and cracked belt covers.
From longitudinal grooving of the bottom cover, to holes and cracks at the idler junction point. And from separation or delamination of the vulcanised joint, to belt breaks by the fasteners, or fasteners that tear loose or split.
Worst of all, when something does go wrong it means unscheduled downtime, often with the cost of a new belt to add to the cost of lost production. Or at least, it did.
Not any longer. Now there’s an alternative solution which not only makes it quicker to carry out emergency repairs, but also means you can easily make conveyor belt maintenance part of your regular maintenance routine.
Brush, toothpaste, smile.
Combining polyurethane resins, a base and an activator, an elastomeric paste from Unique Polymer Systems is as easy to apply as toothpaste.
So you can quickly repair worn or damaged conveyor belts and other flexible components.
First, the area to be treated should be cleaned with a mechanical wire brush – taking care not to melt the rubber or cause more damage to the belt. This ensures improved adherence of the rubber repair paste. Dust should also be cleaned from the area.
Solvent-free and non-polluting, the paste is supplied with the precise ratio of hardener to base, together with mixing tools and application equipment. The easy-to-use packaging allows the exact amount of product to be prepared for each stage of the repair.
So no product cures and is wasted while the belt is being cleaned and prepared. The product is also available as a fluid, which may be more suitable for some areas to be repaired.
The paste has the same viscosity as toothpaste, making it easy to apply on sloping or vertical surfaces – and even upside down – with no risk of runs. It also maintains the shape it’s given during the application, and is resistant to impact, abrasion, and chemicals. Excellent elongation of up to 190% means that even when the belt wraps around the pulley, the repair won’t pop out or be forced off.
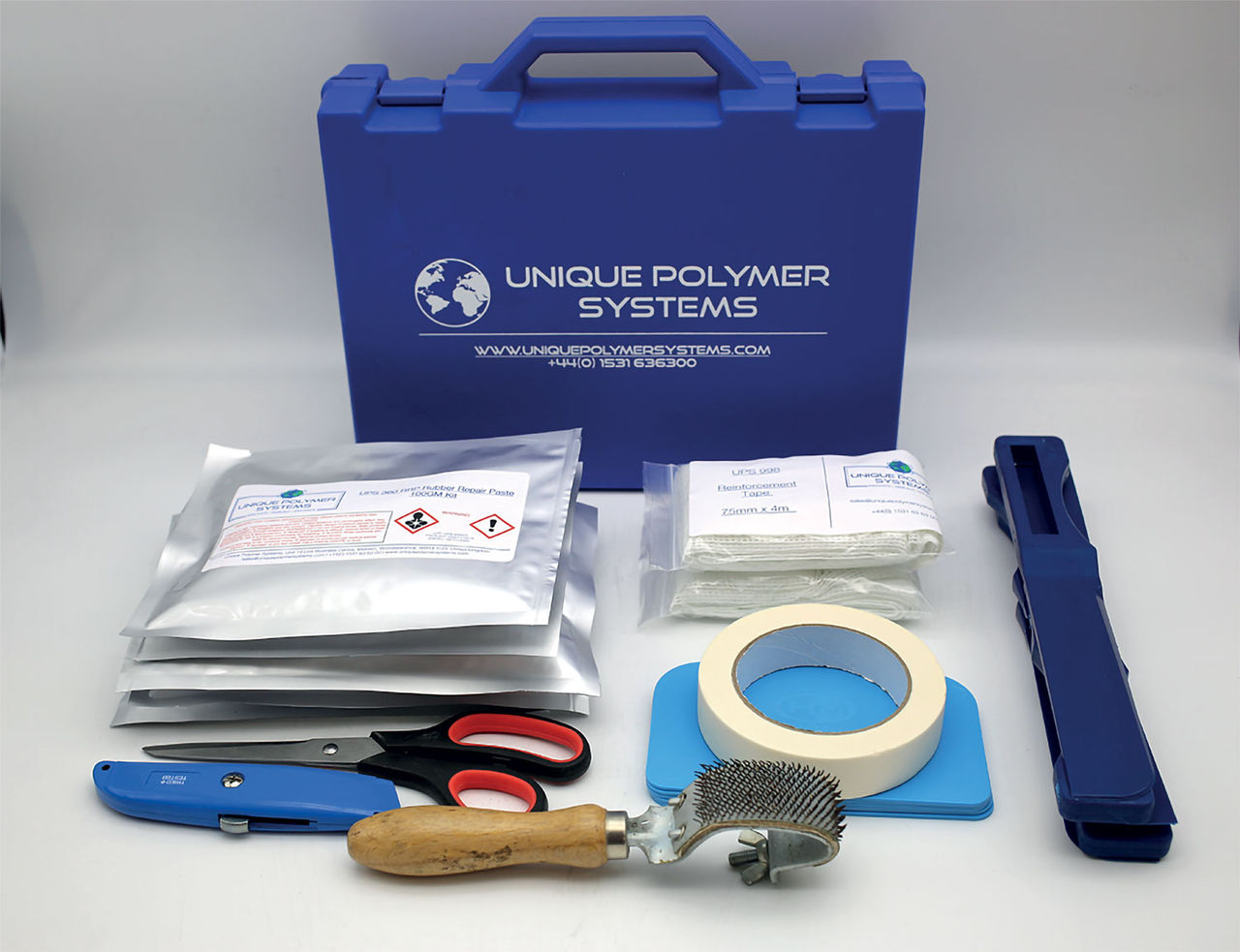
While a conveyor belt replacement can often mean days of downtime, the Unique Polymer Systems Complete Rapid Conveyor Belt Repair System takes as little as 30 minutes to dry and only an hour before the belt can be ready to start up once again.
With a rapid repair system that’s so easy to use, there’s no need to wait for a belt to fail before it’s repaired or replaced. Now all your conveyor belts can be maintained in optimum condition during scheduled downtime, to make sure production keeps rolling.
Rock and rolling
CASE STUDY
Just two days after installation, a belt conveying large aggregate was damaged when materials became jammed between the skirt and belt. A 14cm gouge along 140m of the belt’s length caused damage to a depth ranging from 1.5 - 6mm. The first two layers of fabric carcass were worn through, exposing the third layer to further wear.After cleaning with a wire brush attached to an industrial grinding machine, a solvent was used to clean dust from the area before application of the Unique Polymer Systems Complete Rapid Conveyor Belt Repair System paste.
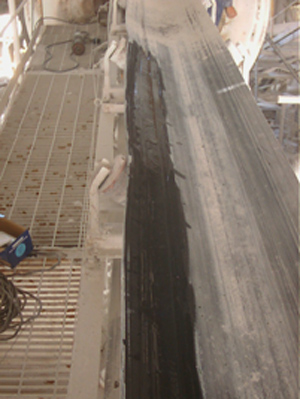
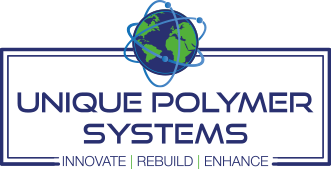
With pre-measured quantities for mixing, and no expansion or contraction after application, applying the correct amount was simple. No specialist contractors were required, and two of the customer’s own maintenance engineers carried out the repair: one applying and the other spreading the paste.
The UPS 360 RRP paste used for the repair took only two hours to cure for every 2mm depth. Measured on the Shore Scale it cures to a hardness of 60-65, depending on the ambient temperature.
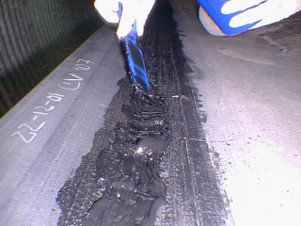
For more information, please contact your local ERIKS Service Centre, who will be happy to discuss your options.
#UniquePolymerSystems #RepairKit #CrackRepair #Polymer #Repair #BeltRepair #ERIKSUK #LetsMakeIndustryWorkBetter
ERIKS in the Quarrying Industry
ERIKS simplify business and processes in challenging environments