In this article
Should your seal be X-rated?
When is an X-ring seal better than an O-ring? Are they interchangeable? And which should you choose for your application? This brief ERIKS guide will help you to make a better informed, more cost-effective decision.
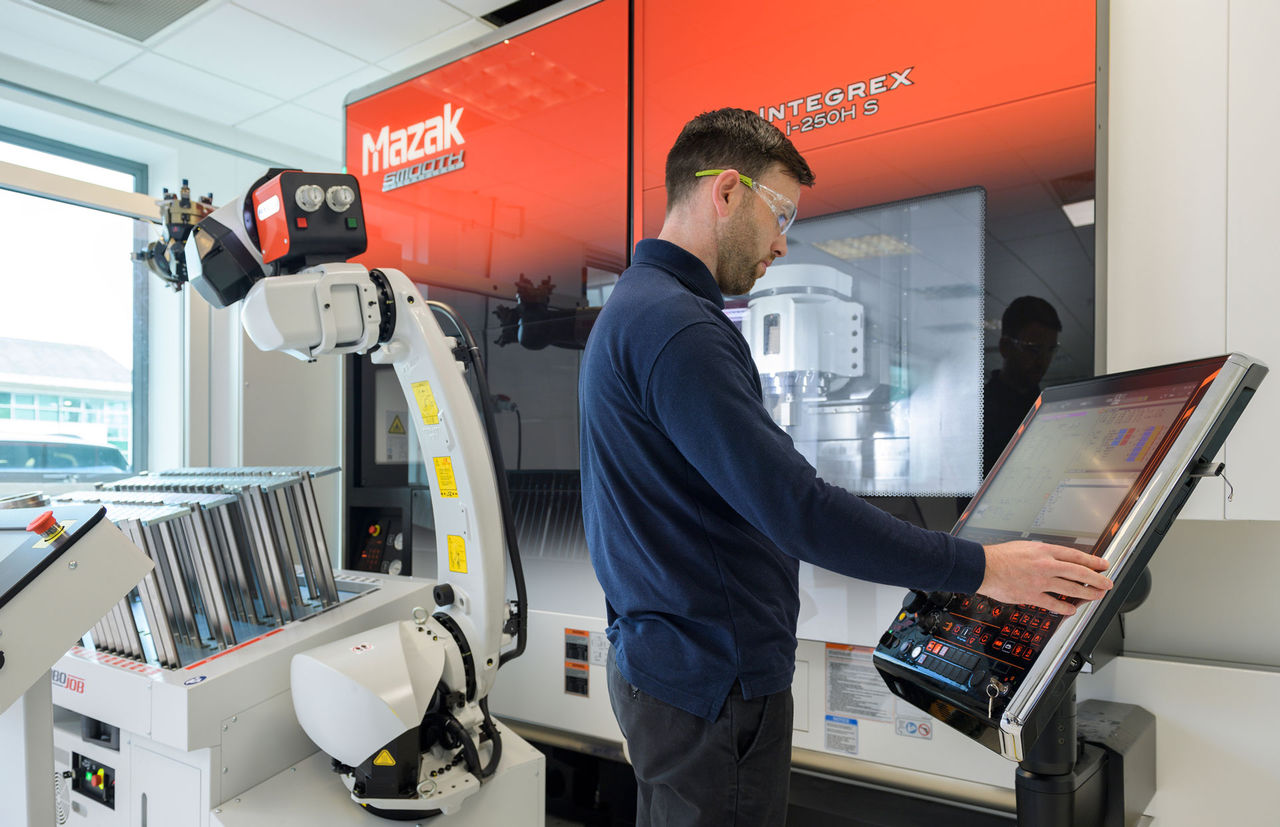
As the name suggests, the most obvious difference between X-rings and O-rings is their shape. An O-ring has a round cross-section, while an X-ring has an X-shaped cross-section. O-rings came first, with X-rings developed later to serve as enhancements to O-rings under certain conditions.
Both types are double-acting seals, meaning they can seal in both directions. But choosing an X-ring in preference to an O-ring can have real advantages in some static, dynamic, slow rotary and oscillatory applications.
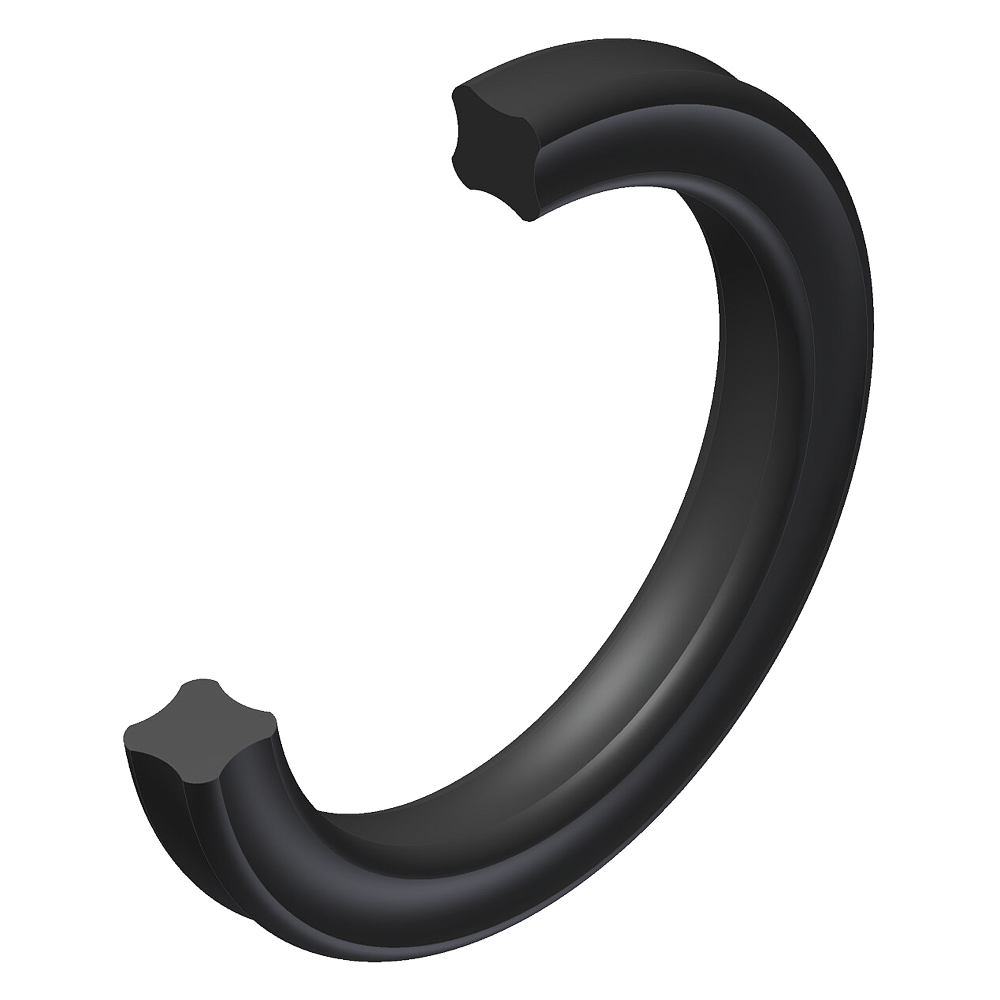
X-ring advantages
Preventing premature leakage in dynamic, sliding applications
One of the biggest issues with O-rings in dynamic, sliding applications (such as piston or rod sealing) is their tendency to twist. This can potentially create a leakage path, leading to premature failure. The X-shaped cross-section of X-rings makes them less likely to twist, providing enhanced stability which leads to better sealing performance.
Extended seal life
X-rings have a lower potential than O-rings for running and break-out friction. This is especially important in dynamic applications where the seal is constantly in motion. X-rings will wear less quickly and have a longer service life as a result.
Greater sealing efficiency
While O-rings have only two points of contact, X-rings have four. This means that X-rings have twice the sealing surface in contact with the part – making them more efficient at preventing leaks.
Resistance to spiral failure
Because X-rings have a larger surface area in contact with the hardware, they are more resistant to spiral failure. This can be an advantage in high-pressure applications.
Higher lubricant retention
The cross-sectional shape of X-rings allows them to retain pockets of lubricant, which helps to reduce friction and increase service life.
X-ring materials
X-rings can be manufactured from the same compounds as O-rings. However the standard X-ring range focuses mainly on compounds used in dynamic applications in contact with oil, where the X-ring’s shape already gives it an advantage.
The ERIKS range of X-rings, including their materials and applications, is outlined below.
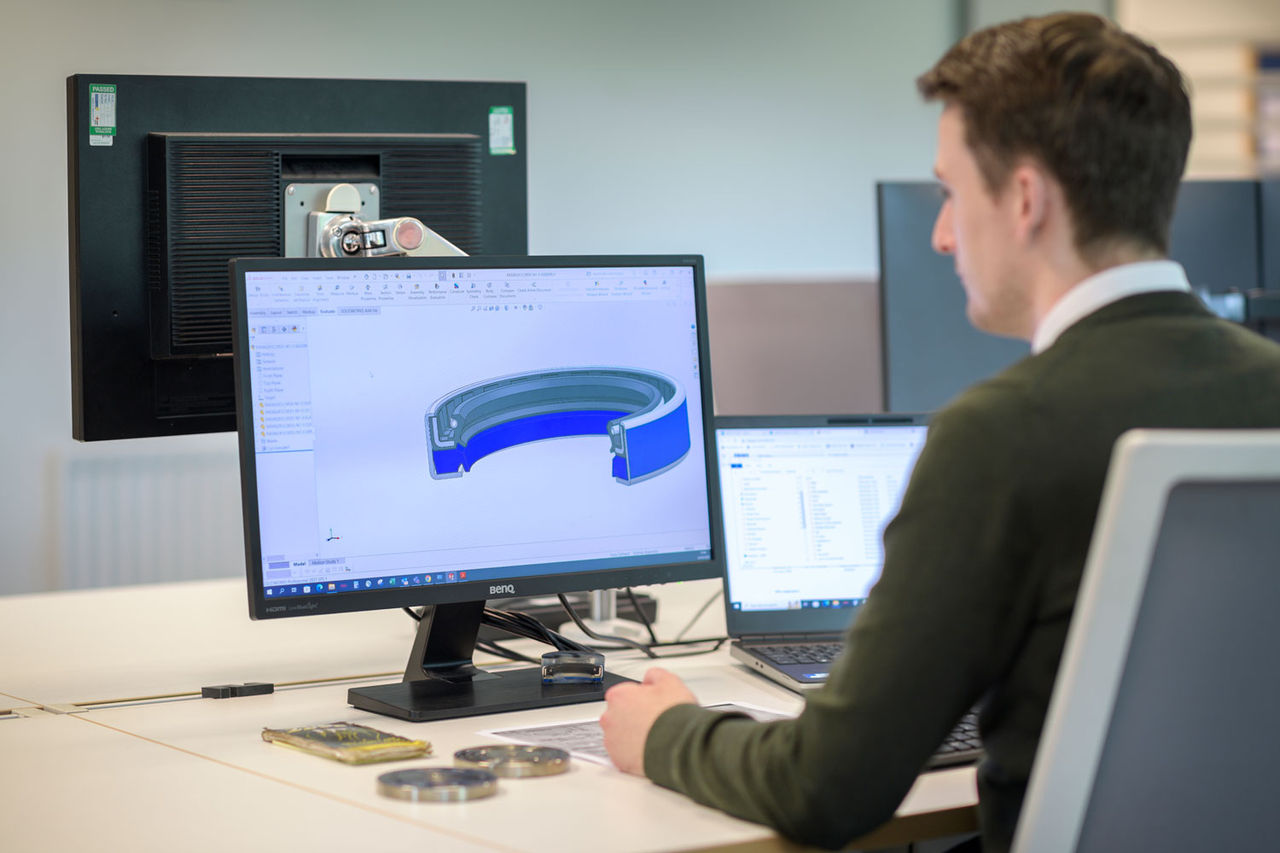
ERIKS NBR 36624
This is the most common material for applications with hydraulic and lubricating oils. NBR is not resistant to ozone or UV, so exposure to these can accelerate ageing.
ERIKS’ standard NBR Compound 36624 has a range of -30°C to +°120C, though in oil a maximum of 100°C is recommended.
ERIKS FKM 51414
FKM (Fluorine Kautschuk Material) is commonly called ‘Viton’, after Chemours’ Viton™ – one of the best-known FKM brand names. FKM is the ISO standard 1629 designator. There are many different types of X-ring within the FKM family. The basic co-polymer types are unsuitable for use in steam or hot water applications.
ERIKS 51414 is a high-quality black FKM, which is highly resistant to many chemicals, oil, grease and fuels. Due to its high density, it can also be used in vacuum applications.
ERIKS EPDM 55914
This black EPDM 70 seals acids, bases, hot water and low-pressure steam. In addition, it is ozone- and UV-resistant. Performing within a temperature range of -55°C to +130°C, the material is not suitable for applications with fats, or mineral and animal oils. If the temperature in your application is higher than +130°C, choose Compound 55915.
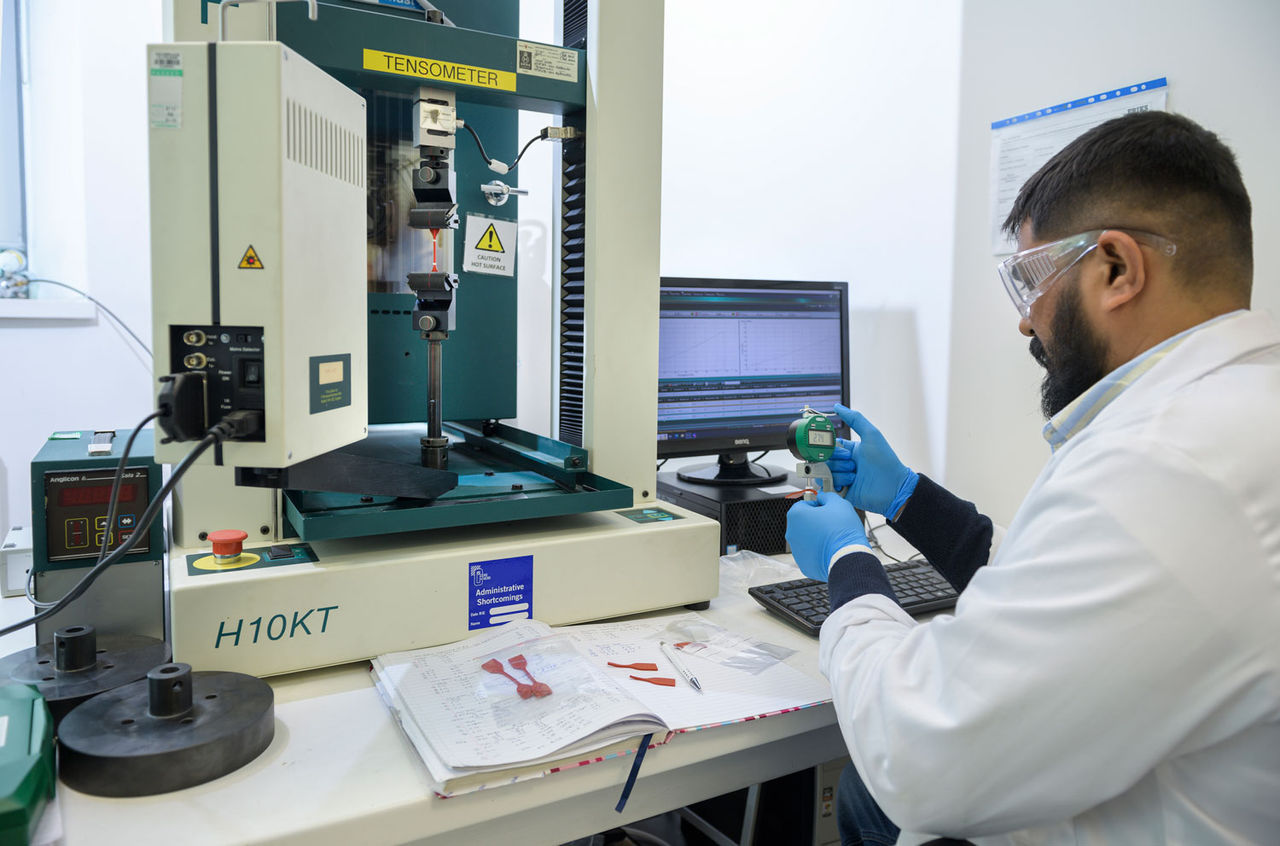
Choosing the correct X-ring size
A seal will only function properly if the right size X-ring is fitted. For dynamic use, the thickest possible X-ring is recommended. A thicker X-ring also compensates better for wear, has a more favourable compression set, a better dynamic sealing ability, and can better accommodate larger movement gaps. For static seals, an X-ring with a smaller crosssection will perform equally well.
More advice on choosing the correct X-ring size, the most effective rubber type for your application, and other technical information, is available from ERIKS online. Or talk to your usual ERIKS contact. Their advice won’t be X-rated, but is always highly rated.
For more information on Sealing and Polymer and to get in touch with one of our ERIKS specislists, please contact your local ERIKS Service Centre, who will be happy to discuss your options.
#ERIKS #LetsMakeIndustryWorkBetter #XRings #Seals