In this article
Seals, designed, delivered: they're yours
Not as catchy as the lyrics to Stevie Wonder’s original song, maybe. But as a service from the ERIKS Technical Campus in Warrington, they’re just as much of a hit. Because when a customer has a unique bearing sealing problem, an off-the-shelf seal won’t cure it. But a unique seal designed by ERIKS will deliver the ideal solution.
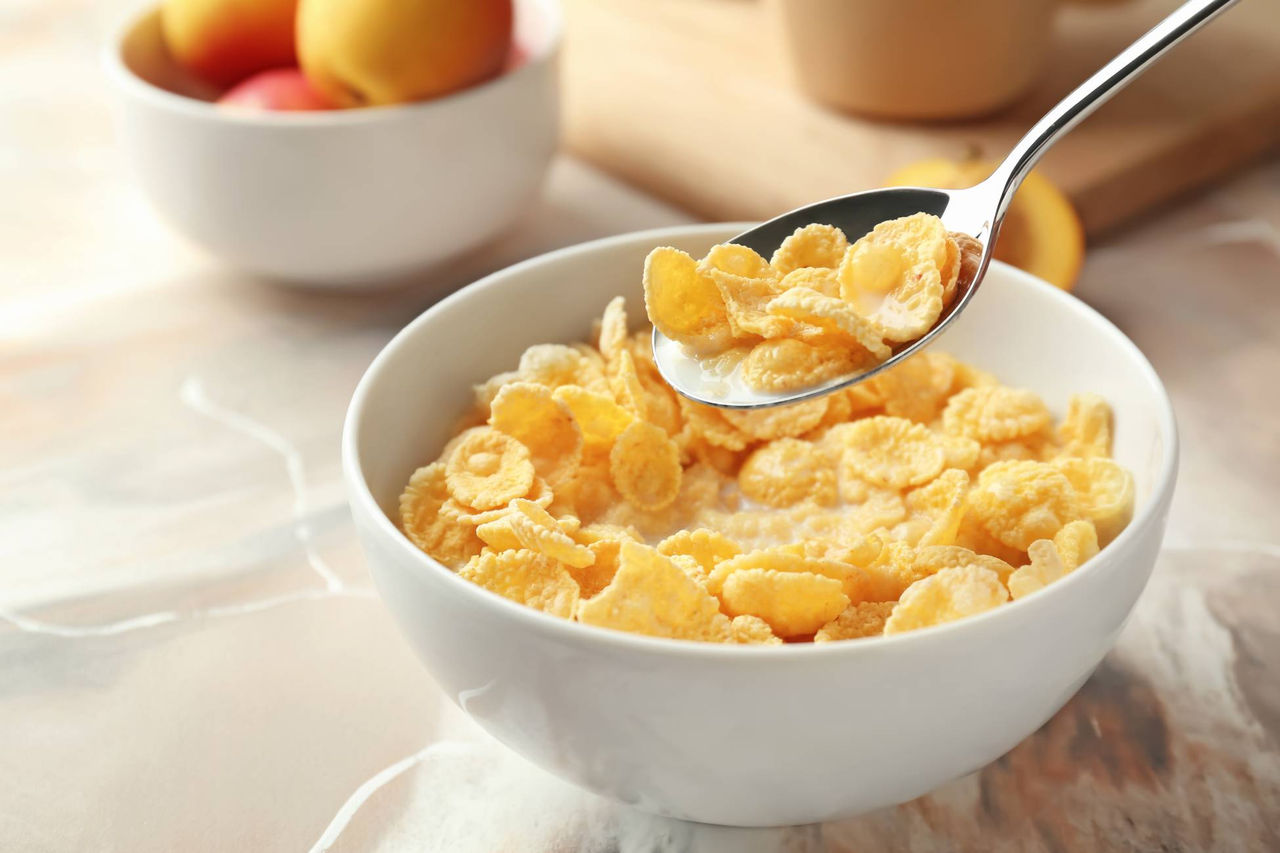
All bearing seals are designed to do something basically similar: keep the good stuff – lubricant – within the bearing where it can do its job. And keep the bad stuff – dust, dirt and fluids – outside the bearing, where it can’t do any damage. Obviously, the seal has to be matched to the bearing in terms of size. But it also has to be matched to the operating environment, to ensure it’s up to any challenges it presents.
That’s where the ERIKS Technical Campus comes in.
The science of seals
If you need help with finding the best seal for your application, you’d expect to have engineers involved. What you might not expect are scientists. At the Warrington campus, you get both.
ERIKS engineers have the know-how to understand the application requirements across a huge range of client’s assets. ERIKS materials scientists know how to identify or develop the polymers which will create the most effective sealing material for a specific operating environment.
They use advanced analytical equipment and techniques – including ThermoGraphic Analysis and Differential Scanning Calorimetry. And they combine this with extensive practical industrial experience, to provide recommendations of more effective alternatives and unique solutions.
On-site CAD modelling is then used to confirm their findings, followed by engineering, manufacturing, and testing of samples. So, by the time a new seal is installed, not only the scientists and engineers, but also – and most importantly – the customer, will be absolutely sure it’s the right seal for the job.
Cereal killer of bearings
One customer who benefited from the know-how available from the ERIKS Technical Campus is a major cereal producer.
An early stage of their production process involves crushing corn kernels using a 4mtr-long roller. Although this is effective at crushing corn, at the same time the corn’s hardness, brittleness and abrasiveness make it very effective at giving the roller’s bearings a battering.
When small pieces of corn split off, and dust and debris were produced, they were finding their way into the bearing. Meanwhile, frequent washdowns were not only succeeding in removing that dirt and debris, but also in removing grease from the bearing housing. Not surprisingly, seal and bearing damage and failure soon followed.
Repair or replacement of failed seals was made even more difficult due to the nature of their construction. As one-piece seals, they could only be removed once the gearbox, housing and bearings had also been removed. And the size of the bearings made that a job for heavy-lifting equipment, with all the associated problems of access and additional cost.
ERIKS devised a seal solution which cut the problems down to size and cut the time for replacing a seal from one day (with two engineers) to one hour.
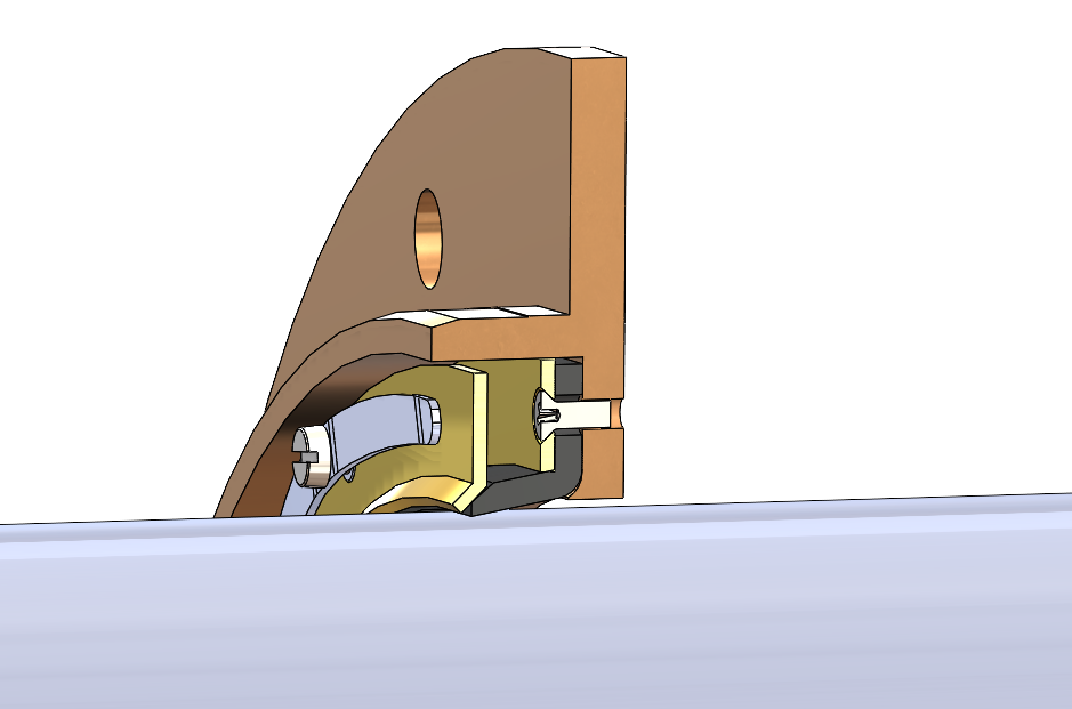
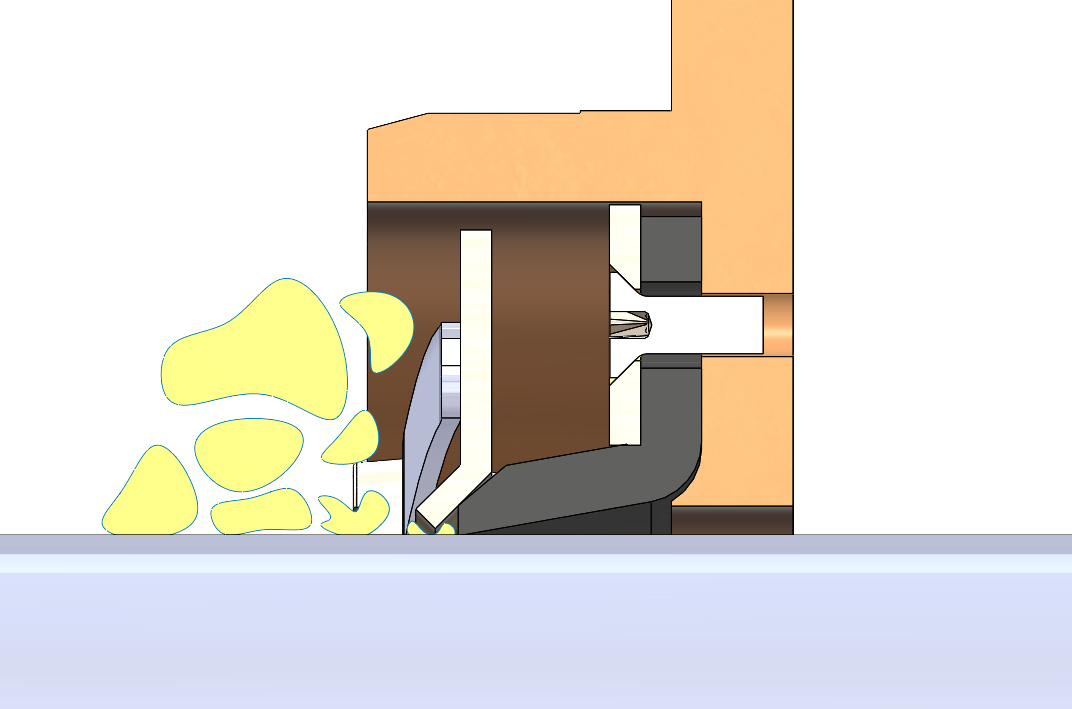
A split decision
The most radical aspect of the ERIKS solution was the decision to utilise a split seal. This eliminates the need to remove connected assets providing easier access to remove and replace the seal.
The seal is also designed to absorb the inevitable damage caused by the aggressive operating conditions. So instead of the bearing taking the battering, the seal takes the strain. And that means a far easier and less costly replacement when the time comes.
The seal also effectively prevents washdown wash-out of the bearing grease, which again helps to prolong bearing life.
Now when seal replacement is required, it’s quick and easy. Every seal designed and manufactured at the Warrington site is allocated a unique part number and recorded in an ERP database. When the customer requests a replacement and gives the relevant part number, a quick database search will provide all the information required to quote for a replacement.
The Benefits continue…
Upon inspection at ERIKS Warrington Campus it is often identified that the multi-component seal can in fact be refurbished by replacing any compromised components which facilitates a quicker and more cost effect solution for the customer.
So, when the customer wants to get back to crushing corn, we don’t let the grass grow under our feet.
For more information on Sealing and Polymer and to get in touch with one of our ERIKS specislists, please contact your local ERIKS Service Centre, who will be happy to discuss your options.
#ERIKS #LetsMakeIndustryWorkBetter #Seals #Solutions #Warrington