In this article
Let's talk dirty
Dirty is the one thing that food, pharmaceutical and semi-conductor manufacturers can’t afford to be. Dirty means wasted production. Dirty can mean product recalls. And in the worst cases, dirty can mean customers harmed by contaminated food or drugs, or semi-conductors failing or igniting fires. This service from ERIKS Sealing Technology helps to make sure your seals and gaskets are kept completely clean from one end of the manufacturing process to the other. So if your production relies on clean gaskets or seals, you can wash your hands of worrying about it.
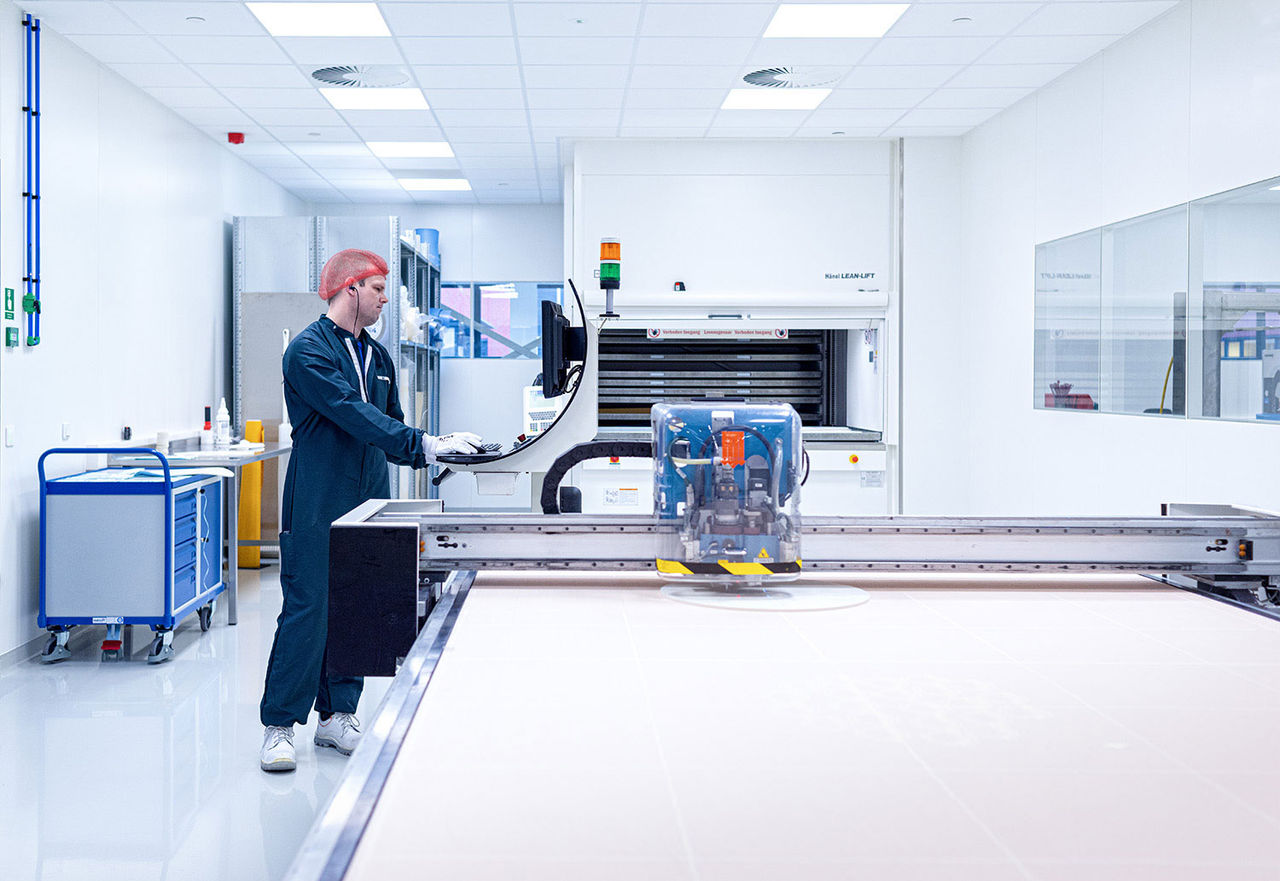
With a new gasket dedicated Oxygen clean room recently opened at Leader Gaskets in Slovakia (an ERIKS company), ERIKS now offer three European located facilities for contamination-free seals and gaskets production, with the existing two sites being located at ERIKS premises in the Netherlands and Belgium, with the dutch site having a special focus on the semi-conductor industry. Having these three sites gives ERIKS the advantage on being able to direct orders to where has the most capacity and best meet the customers, or indeed the intended industries, requirements for the manufacture and cleaning of their gasket and sealing needs.
So as requirements for preventing contamination become increasingly stringent, and demand for clean sealing technology grows, having these three specialist sites you can rely on ERIKS for the capacity and capability to meet your sealing needs.
Send dust packing
Due to an ever-increasing awareness of cleanliness, the industry is focusing more and more on optimal control of production processes. Efforts are made to prevent technical components from causing contamination in the processes and systems. Pollution can be caused, among other things, by particles floating in the air, which are both visible and invisible to the eye. These particles are called aerosols. Preventing this type of pollution is especially important in the pharmaceutical, semiconductor and food industries.
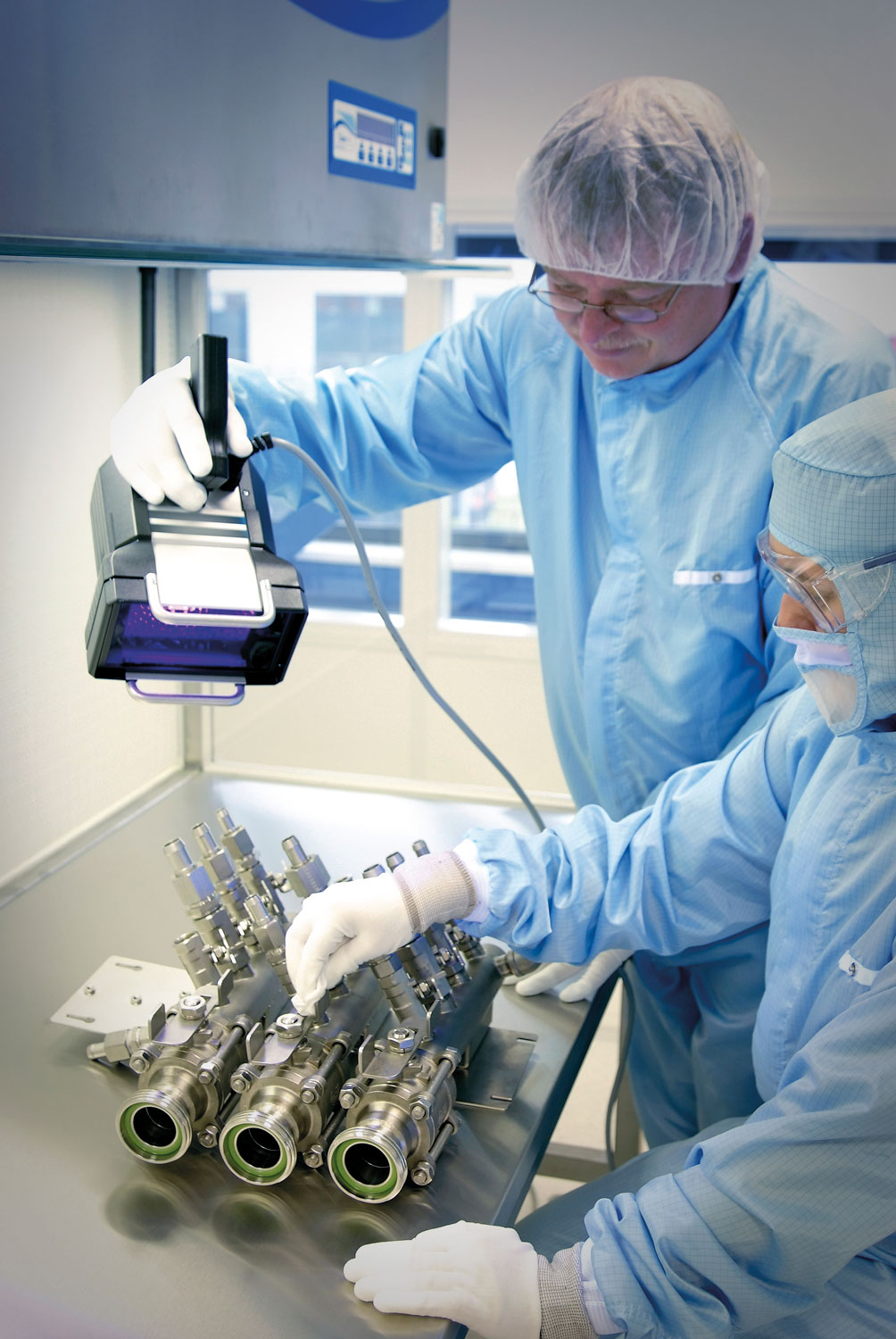
Manufacturers of food and pharmaceuticals don’t pick and choose where to operate clean production, it is often a necessary requirement. From raw materials to finished and packed product, every centimetre of the production line must be hygienically clean.
Raw materials brought into the ERIKS clean rooms can be oxygen or ultrasonic cleansed, cut, moulded or extruded, assembled, inspected, double-bagged and labelled, all within the same hygienically clean space.
Labelling and special packaging
Cleaned products can be specially labelled at the request of the customer. Positioning stickers and labels so that they are legible can be crucial when installing components — that’s why we provide tailor-made solutions on request.
All products are placed in special transparent or pink plastic clean bags with labels providing customer-specific product information. When the components are sent out to customers, the components are clean, clearly marked and ready to use.
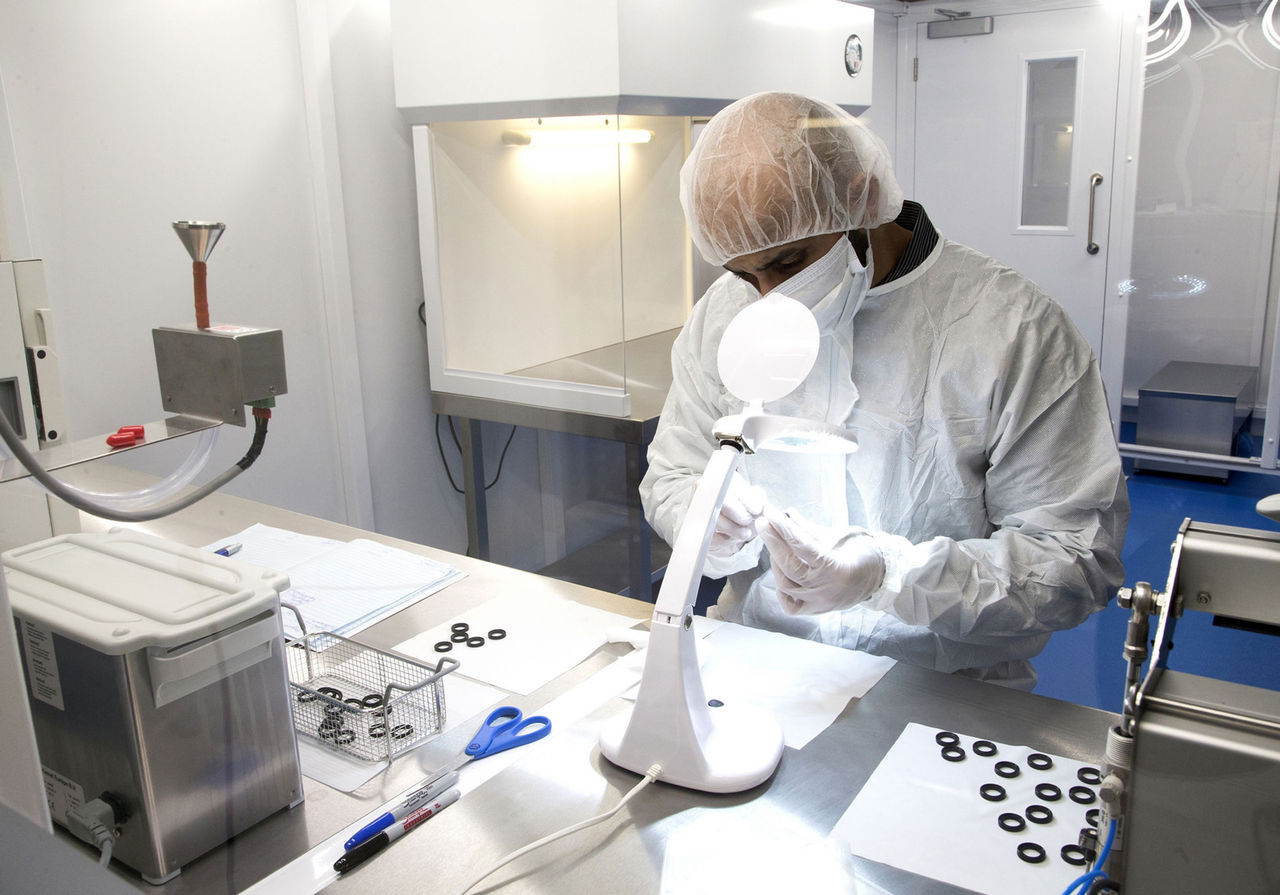
How clean is clean?
The ISO sets standards for clean rooms, based on the number and size of particulate contaminants allowed to be present in the room’s atmosphere.
The requirements for hygienic manufacturing and packaging processes are becoming increasingly stringent. One of the biggest challenges is preventing contamination. Tiny particles—so small they are measured in nanometres—can seriously disrupt critical industrial processes.
The CMF (Clean Manufacturing Facility) in Alkmaar covers two floors and more than 1,000 square metres. The facility consists of clean manufacturing areas and a 320-squaremetre ISO Class 6/Class 1000-certified, cleanroom, which means it contains a maximum of 35,200 particles per cubic meter of a size greater than 0.5 microns, and no more than 293 particles per cubic meter of a size larger than 5 microns.
Clean Manufacturing Facility activities
- Clean manufacturing and assembly
- Cleaning products (cleaning baths)
- Clean packaging and labelling (clean packaging areas)
Positive pressurising of the ERIKS clean rooms helps to prevent any ingress of airborne particles, and all technicians working within the rooms change into clean hygienic coveralls and footwear before entering.
Clean rooms meeting the ISO 6 standard, include an airlock, so that people coming into the rooms don’t enter directly from the outside environment. Which means the easiest way to get access to the facilities – and the clean sealing technology products and assemblies they produce – is to contact your usual ERIKS representative and ask where we can help you ensure you are receiving the quality of product and cleaning services expected.
Lean in clean: complete care
ERIKS has designed its clean manufacturing services to be fully lean. “Lean” means creating value and eliminating waste. “Clean” refers to the cleanliness of the products, both in terms of food safety and particulate matter. Being ‘lean in clean’, means taking care of the entire clean manufacturing process for a growing number of customers in the food, pharmaceutical and semiconductor industries.
Fewer links in the supply chain - all under one roof
In the past, customers had to buy products from ERIKS and send them elsewhere for clean manufacturing — now we are able to offer all of these services under one roof. This makes your processes more efficient and production lines shorter, while ensuring maximum quality. Having fewer links in the supply chain results in cost savings and faster deliveries. Complete care from start to finish. That’s what we provide. That’s ERIKS. That’s lean in clean.
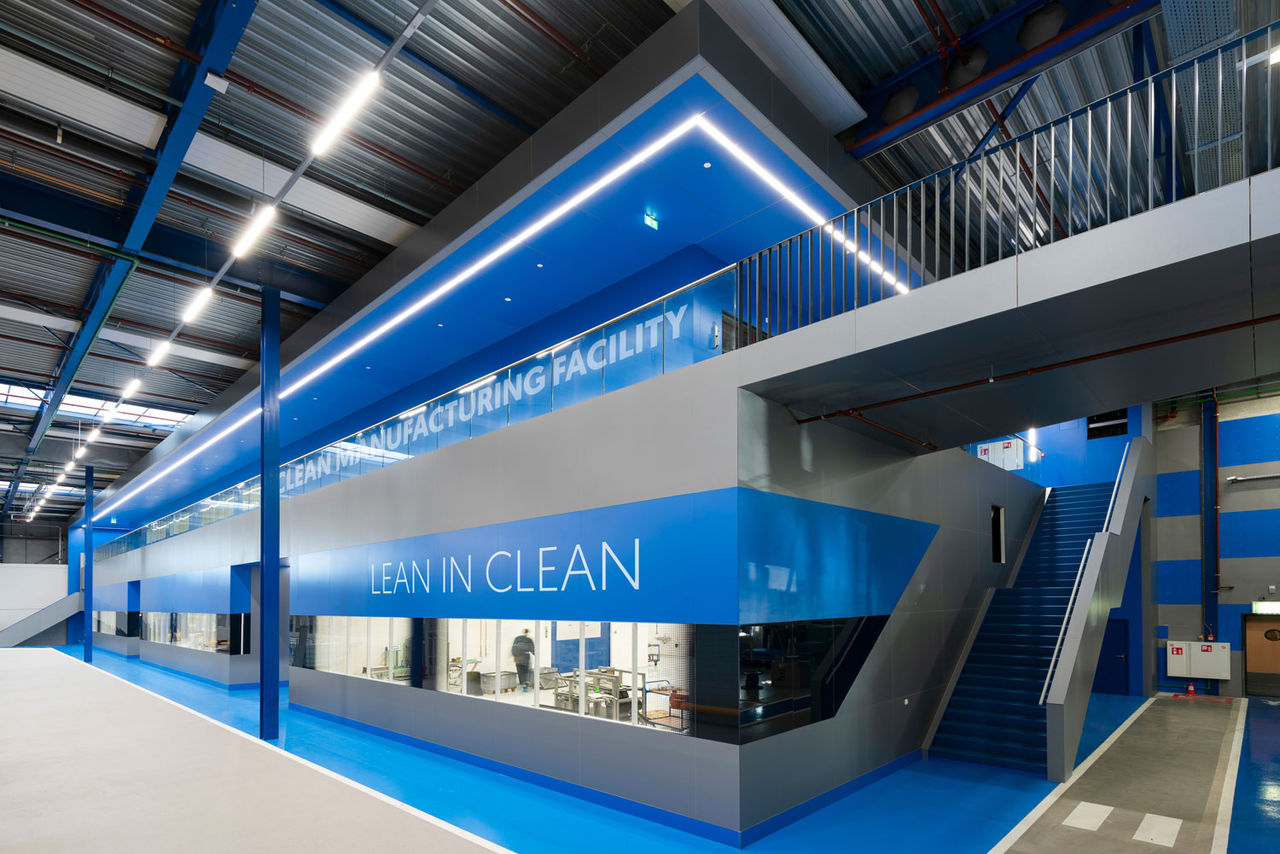
For more information on Sealing and Polymer and to get in touch with one of our ERIKS specislists, please contact your local ERIKS Service Centre, who will be happy to discuss your options.
#ERIKS #LetsMakeIndustryWorkBetter #Seals #Gaskets #CleanManufacturing #Cleanroom