In this article
When Archimedes was screwed
The Archimedes screw has been doing a great job of lifting and transporting fluids and powders since the time of, well, Archimedes (around 24 centuries ago, give or take). So when a cement manufacturer began having problems with theirs, they called in the experts with experience. Though not quite that much experience.
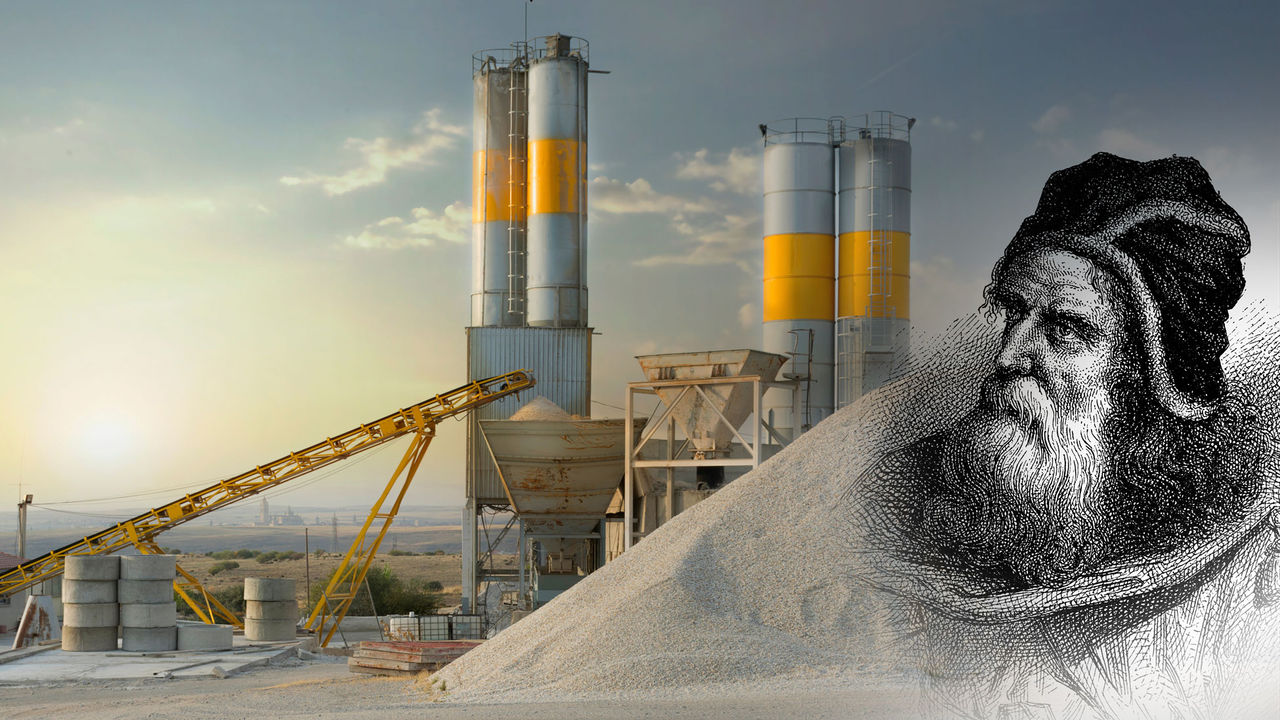
The manufacturing plant uses a total of eight plain bearing assemblies to support Archimedes screws which lift cement in a powder form vertically. Each Archimedes screw and bearing assembly would rotate at a speed of approximately 1,400rpm. Or at least it does when things are going well.
For three months or so at a time the system would work perfectly. But then, time and time again, the bearing would fail and the screw would stop turning. The whole asset would have to be taken out of service for at least a day, to replace the whole bearing assembly i.e, connecting flanged shaft, plain bearing, labyrinth, and housing too and a completely new assembly would need to be installed.
The cause of the problems was fairly obvious. Cement dust is an aggressive, intrusive substance and – as the name suggests – it’s not something a cement works is short of.
Despite the phosphor-bronze bush bearing being protected by a labyrinth seal, the dust still found its way in and soon caused the bush to fail.
The ingress of dust was also steadily damaging the main shaft, which was another replacement or failure just waiting to happen.
The customer had tried regular purging of the grease to try to remove the contaminant, but this not only increased the maintenance burden and – obviously – the bill for grease. It also failed to resolve the issue.
Since Archimedes is no longer available, the customer called in ERIKS.
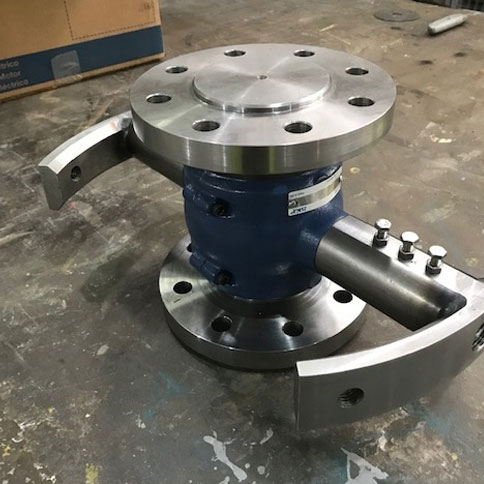
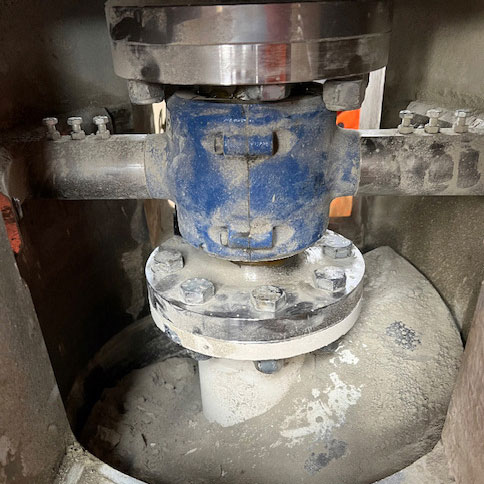
Taking Einstein’s advice
Einstein wasn’t an engineer himself, but he did have some useful advice for engineers. ‘Insanity’, he said, ‘is doing the same thing over and over and expecting a different result.’
So instead of replacing the old bearing with an identical one, ERIKS’ engineers brought some fresh pairs of eyes and new ways of thinking to the problem.
They began by observing the application, continued by identifying the root cause of the problem, and finished up by designing an entirely new bearing housing assembly.
The new assembly doesn’t just offer greater protection against cement dust ingress, thanks to its special H-Ecoupur seals. If the bearing ever needs to be removed, the new design also makes this far quicker and easier, because there’s no need to remove the shaft to remove the bearing.
Hard and fast
The shaft has also benefited from ERIKS’ attention.
The original through hardened steel design suffered scoring from the dust – and although the shaft hadn’t failed as a result, it could only be a matter of time.
So ERIKS replaced the original shaft with a case-hardened and ground version: providing more resistance to any small quantities of the aggressive dust that still gained ingress.
And if and when the bearing or seals need attention, the new Split Roller Bearing (SRB) in its SRB housing can simply be opened up into two halves and lifted off the shaft, which stays securely in place.
This shortens bearing removal and replacement, if required, to a quick two-hour sprint rather than a whole day marathon.
The cost of replacing the bearing or seal is also reduced, as both are standard items available from stock.
Wear? What wear?
Previously, the Archimedes screw and bearing assembly was failing roughly every three months. With the new bearing in place, and no sign of failure after the same period, the assembly was dismantled for inspection.
What was revealed were bearings that were still fully greased and in excellent condition, and seals which were virtually immaculate. So the new SRB solution is already delivering on its promise of easier, less frequent maintenance and a longer life.
Hardly surprising, then, that ERIKS has been asked to quote for replacing bearings and seals on the remaining seven Archimedes screws. And the customer still has less downtime and lower replacement costs to look forward to.
For more information or to get in touch with one of our ERIKS Specialists, please contact your local ERIKS Service Centre, who will be happy to discuss your options.
#ERIKS #LetsMakeIndustryWorkBetter #Engineering #Bearings #Expertise #Cement #AggressiveEnvironments