In this article
The split decision everyone agreed on
It wasn’t the conveyor chains which shackled one customer to costly downtime. It was the sprockets. So they turned to ERIKS to see if there was a better way to keep their conveyors moving, their process running, and their production rolling.
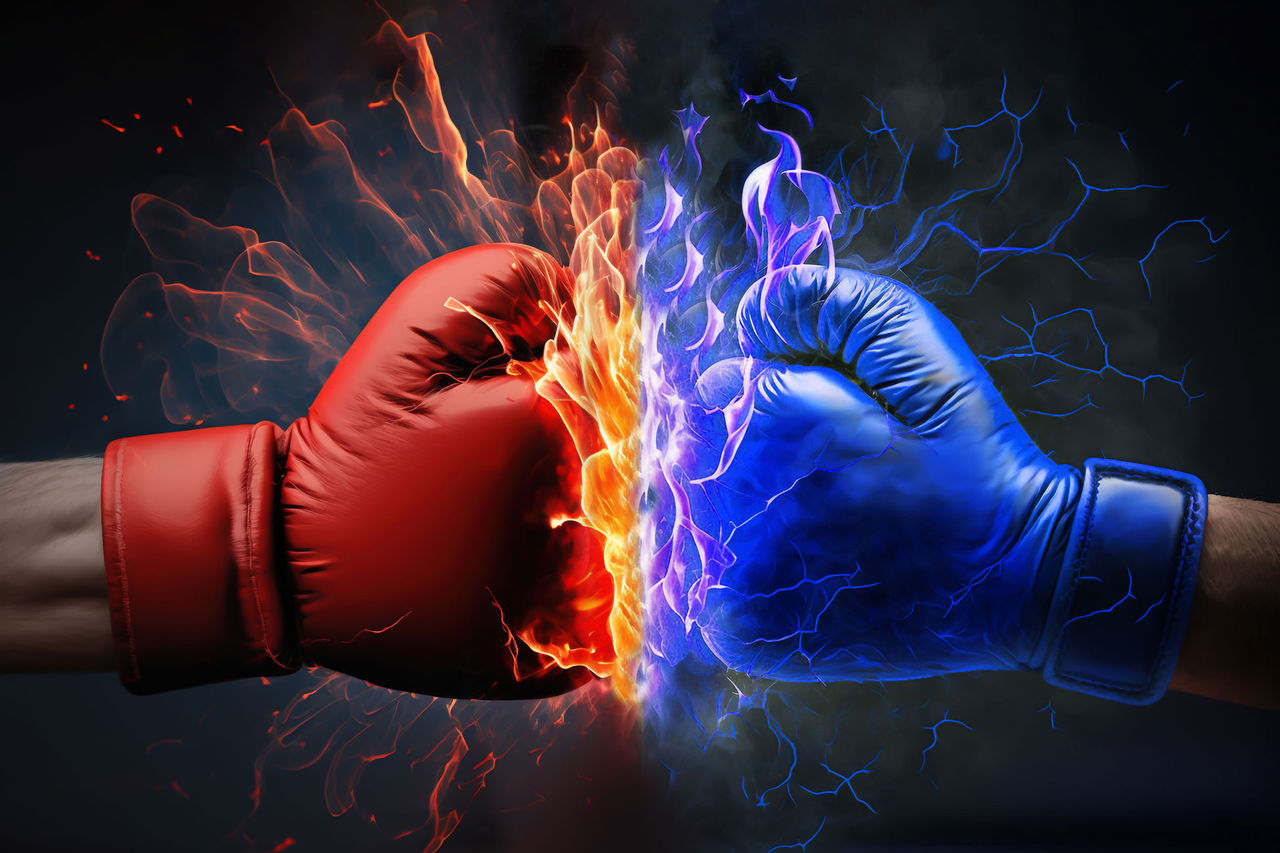
The cement manufacturing process is a tough environment for machinery. Even the conveyors carrying fuel to the kilns operate in less than ideal conditions. And for this leading cement manufacturer, there is an added reason why their conveyors need to keep moving 24/7. It’s because, whenever a conveyor is offline, the process running costs increase by no less than 50%, thanks to the need to switch from their sustainable fuel source back to coal [see box-out below].
So when chains and sprockets need repair or replacement, there’s no time to waste. But removing a 1.5m diameter heavyweight sprocket from a driveshaft, in a difficult-to-access location inside a 180ft-long piece of equipment, is a tough and time-consuming business.
That’s why the sprockets were normally run to fail, and not even the chains had been serviced or replaced for several years.
Wondering whether, to make life easier, it would be possible to use a split sprocket, the customer turned naturally to ERIKS for the answer.
Not rocket science: sprocket science
Split sprockets are not new, but they are unusual. Even for a standard application they’re not generally available off-the-shelf– and this customer’s application is far from standard.
The sprockets carry steel conveyor chains of 6in. pitch – 85ft. long and 4in. wide – with attachments for cross-flights approximately every 5ft.
One conveyor runs above and one below, with the cross-flights scouring and flattening the material carried on the lower conveyor, turning it into a 3in. thick layer. This material is then conveyed to a chute from where it is loaded into the kiln.
So designing and engineering a suitable solution demanded experience of sprockets, conveyors, and rotating equipment, together with expertise in aggressive environments.
Or to put it simply: it needed ERIKS know-how.
ERIKS’ Rotating Equipment Product Business Unit got down to work, using CAD to design a split-sprocket solution.
One crucial consideration was the size of the hubs: they had to be big enough to withstand the torque necessary to tighten the bolts which keep the two halves of the split sprocket together.
With a suitable CAD design completed, ERIKS approached an experienced supplier partner to manufacture the sprockets, ready to install at the customer’s next scheduled shutdown.
The chain gang
The ERIKS Project Drives Team was drafted in to remove the original one-piece sprockets from the shafts. Firstly, the conveyor chains had to be undone. Next, the bearings had to be stripped from the shaft and the shaft removed. Finally, the sprockets had to be pulled out using a heavy-duty 70-80 tonne puller.
The team then polished the shafts to good-as-new condition, installed the new split sprockets, replaced the conveyor chains, and had the refurbished conveyors back up and running to meet the customer’s end-of-shutdown deadline.
In the past, removing and replacing the one-piece sprockets was a three-day task.
Now, the new split sprockets can be taken out of the machine without stripping the bearings or removing the shaft.
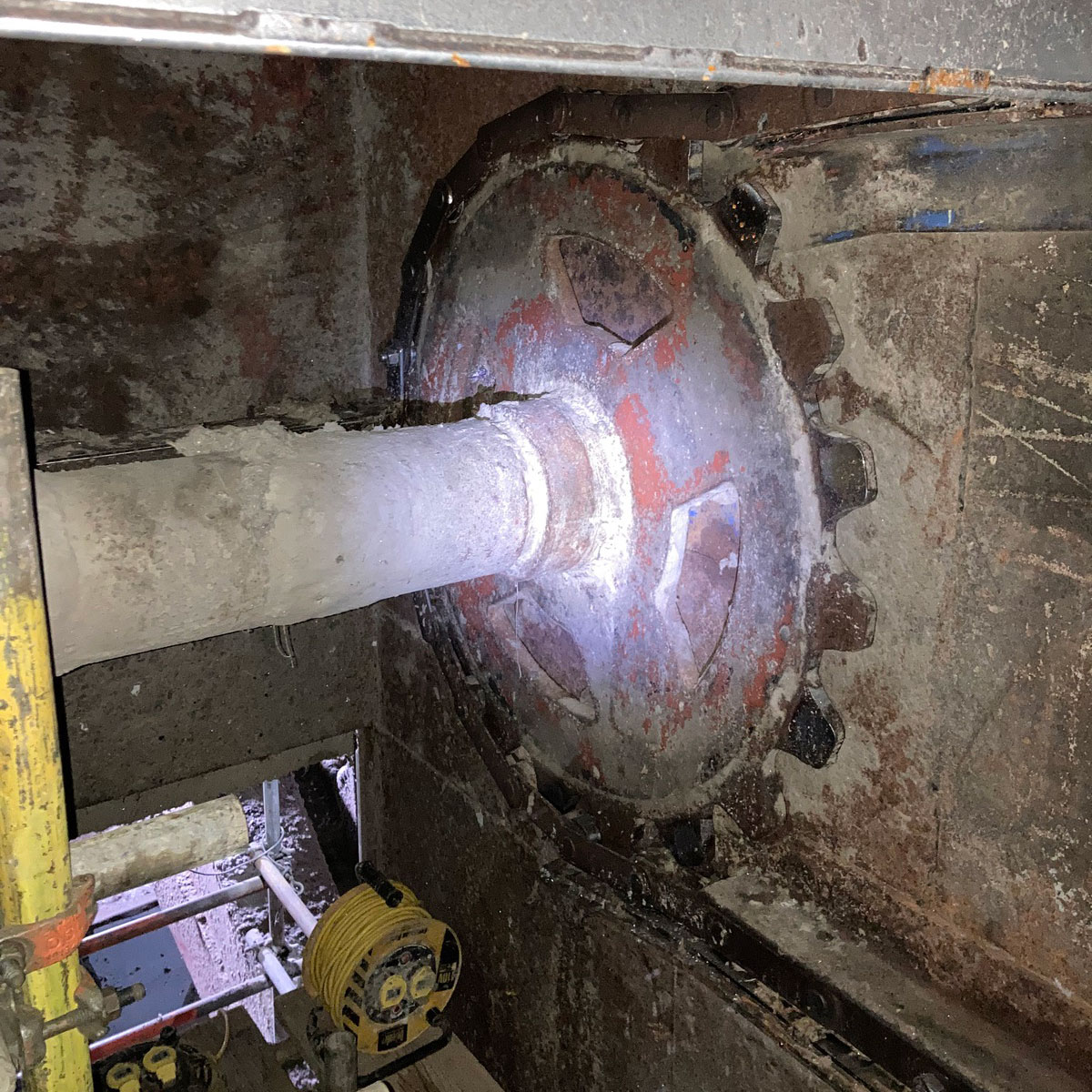
After undoing the bolts joining the two halves, all it takes is a few blows with a heavy hammer to separate the halves for removal. Any repairs can then be carried out on site, the sprockets replaced in the machine, and the conveyors be back in action – all in one day.
No wonder when people discuss the benefits of split sprockets, opinions aren’t divided.
Cutting costs and carbon
The customer’s conveyors carry a critical fuel source to the kiln for the cement-making process.
Sustainable and renewable, the fuel is manufactured from paper, plastic and fibrous wastes that are uneconomic or impossible to recycle. This fuel helps to reduce reliance on burning coal, which reduces the customer’s energy bill for the process by 50%. At the same time, burning a non-fossil fuel helps to shrink the customer’s carbon footprint.
The need to sustain these savings makes the continuous running of the conveyors crucial. Which is why the customer relied on ERIKS to provide a solution for removing the sprockets that keeps downtime, costs and carbon emissions to a minimum.
For more information or to get in touch with one of our ERIKS Specialists, please contact your local ERIKS Service Centre, who will be happy to discuss your options.
#ERIKS #LetsMakeIndustryWorkBetter #Engineering #Sprockets #RotatingEquipment