In this article
How to manage hose management
Hydraulic hoses are the critical component within most production systems. They’re also the component which can be completely compromised by something as seemingly insignificant as a pinprick. So it’s essential that maintenance engineers know the hoses they have, what they do, the condition they’re in, and when they should be replaced. But knowing the importance of your hydraulic hose systems is one thing. Managing them is another.
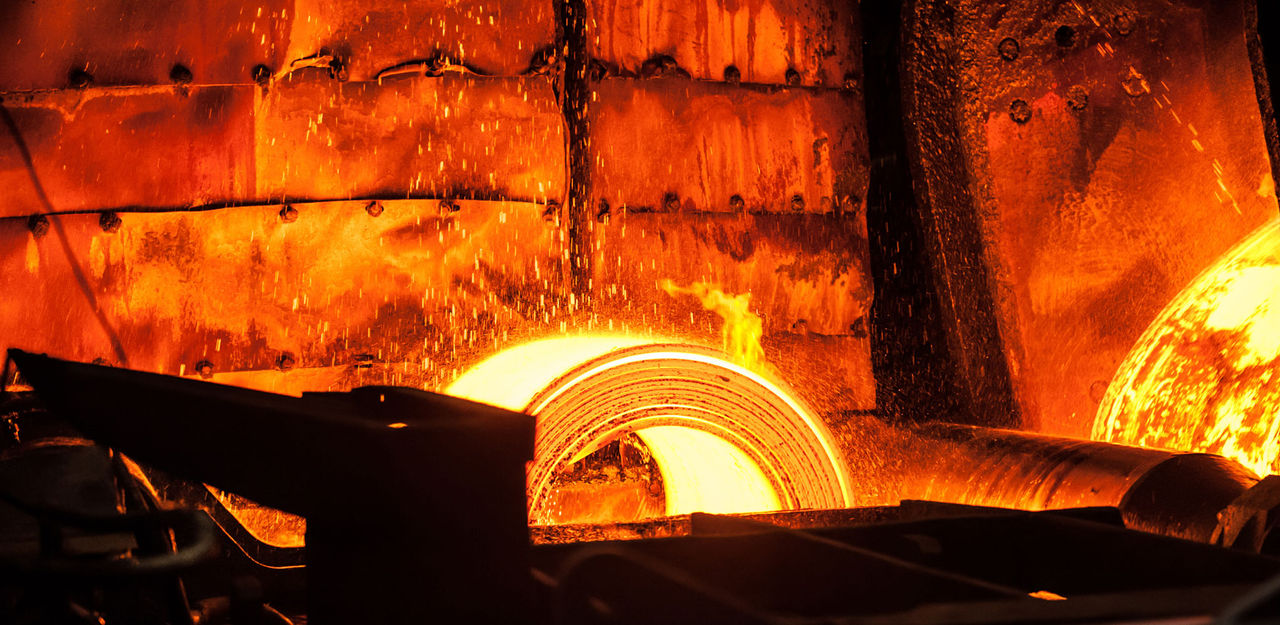
One business in the steel industry has around 2,500 hydraulic hoses to manage. Realising this isn’t a job for one person with a spreadsheet, their Reliability Engineer Manager turned to ERIKS Flow Division for their hose management expertise.
ERIKS’ response was to initiate a 4-step Hose Management System (HMS) to help save the customer up to £35,000/hr on unplanned downtime.
Where’s my hose?
Before you can manage your hoses, you need to know what hoses you have, and where.
For this steel sector customer, the first stage of the ERIKS HMS meant locating and surveying all their hydraulic hoses. At an optimum rate of 80 hoses a day, that was around 10 days’ work for three people – and in this case access for surveys was limited to planned shutdown days only.
The work was made even more difficult by the exceptionally dirty working environment. Not only new PPE but also new measuring equipment was needed for every working day.
Many of the hoses had been previously identified and tagged, but the information recorded on silicone tags quickly became illegible – or completely erased – due to the operating environment. ERIKS’ first proposal was to replace all silicone tags with more hardwearing and long-lasting metal alternatives.
The right hose for the job?
Once a hose has been located and identified, the next step in an effective HMS is to assess if it’s the right hose for the job. Does its specification and pressure rating meet the requirements of the application?
In the event of a hose failure, an emergency ‘Hose Doctor’ will often make a quick-fix, short-term repair using whatever similar hose is available. This hose is likely to fail in less time than the original but – because there’s no record of the original and it’s correct specification – it will be replaced again and again with a like-for-like hose or with another readily available alternative.
The result is not only reduced Mean Time Between Failures of the hose itself, but also an increased risk of failure for the valves, pumps and other associated equipment, thanks to undue stresses resulting from using an underspecified hose.
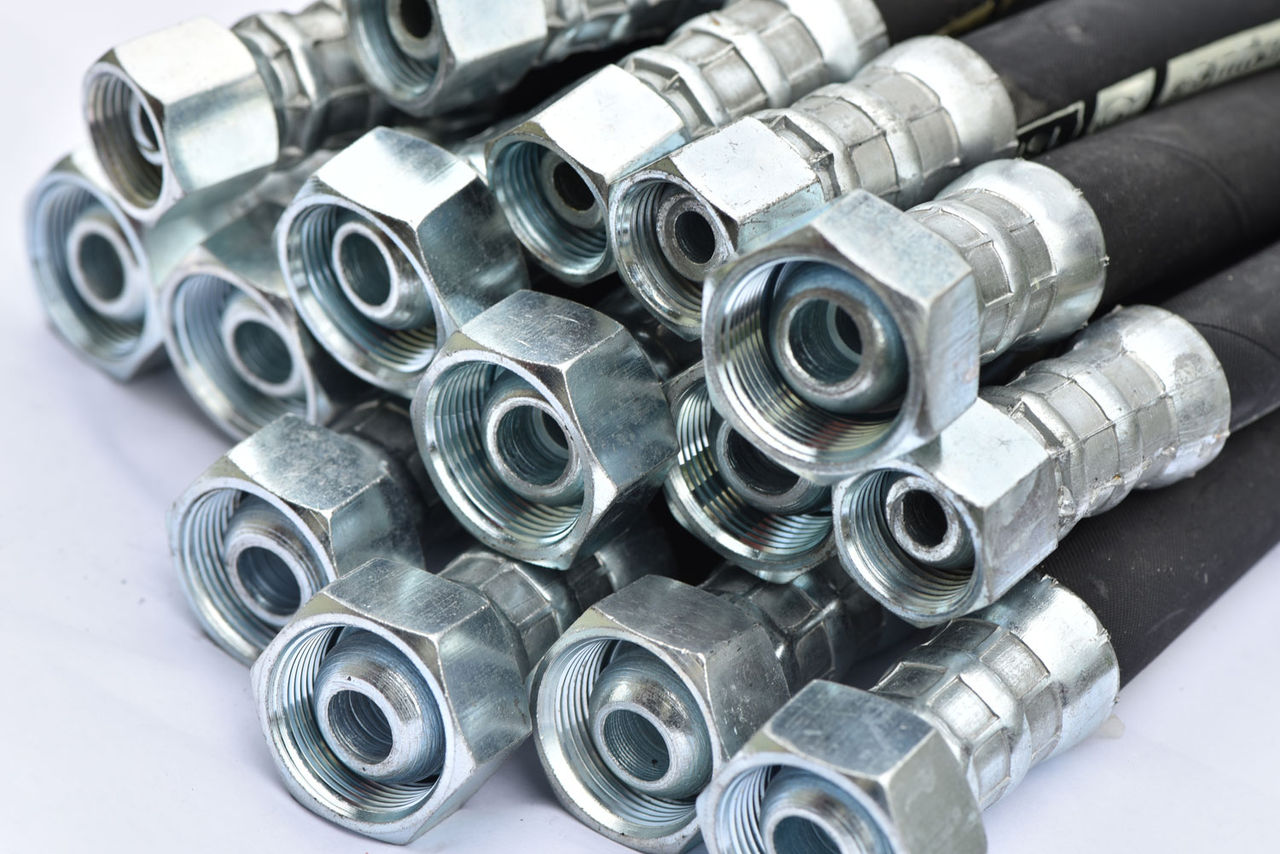
Time for a change?
Rubber hoses perish and degrade. The pressures and stresses of the particular application, and the number of cycles the system goes through, also help to dictate how often a hose should be changed. So identifying and recording this is the third stage of the ERIKS Hose Management System.
For hydraulic hoses in a high-pressure system, the recommended service life is five years. But to be sure each hose is replaced when due, it’s necessary to know when it was installed. And to have a properly maintained database where those dates can be logged and flagged-up.
Fit to burst
Preventing hose failure is more efficient than repairing or replacing failed hoses. Given the pressures in hydraulic systems, it’s also a great deal safer.
ERIKS Flow Division’s initial Hose Management System survey for the steel sector customer – undertaken during shutdowns – spotted several hose issues which would have created significant problems on restart. With the HMS now in place, the knock-on effect of similar issues is greatly reduced.
Without an HMS, the hose could only be identified on removal, meaning a long shutdown because manufacturing the new hose can’t even begin until the old hose has been removed. Now all hoses are logged on the system’s database, the information required to manufacture a replacement hose is quickly accessible. The system need only be shut down for a brief 20 minutes for swapping-out the hose.
With regular hose inspection as the fourth stage of the ERIKS HMS, potential failures can be identified and prevented before they cause problems, shutdowns, and possibly even injury.
An average of 70% of the cost of an emergency hose repair is for the call-out alone. So it makes sense and saves money to manage your hose management more efficiently, with the ERIKS Hose Management System.
For more information on Flow Control solutions and to get in touch with one of our ERIKS Pumps Specialists or Valve/Flow Control Engineers, please contact your local ERIKS Service Centre, who will be happy to discuss your options.
#ERIKS #LetsMakeIndustryWorkBetter #Innovation #FlowControl #Hose #HoseManagement #Inventory