In this article
Who can you rely on when the chips are down?
Lost production is the problem no-one wants to have. Whatever the cause, it’s always essential to get your line back up-and-running as soon as possible. But what if your Reliability Partner turns out not to be reliable enough, and you find yourself looking at a complete shutdown? For this customer, the losses could have been almost a quarter of a million pounds. That’s why they asked ERIKS to chip in with urgent engineering support.
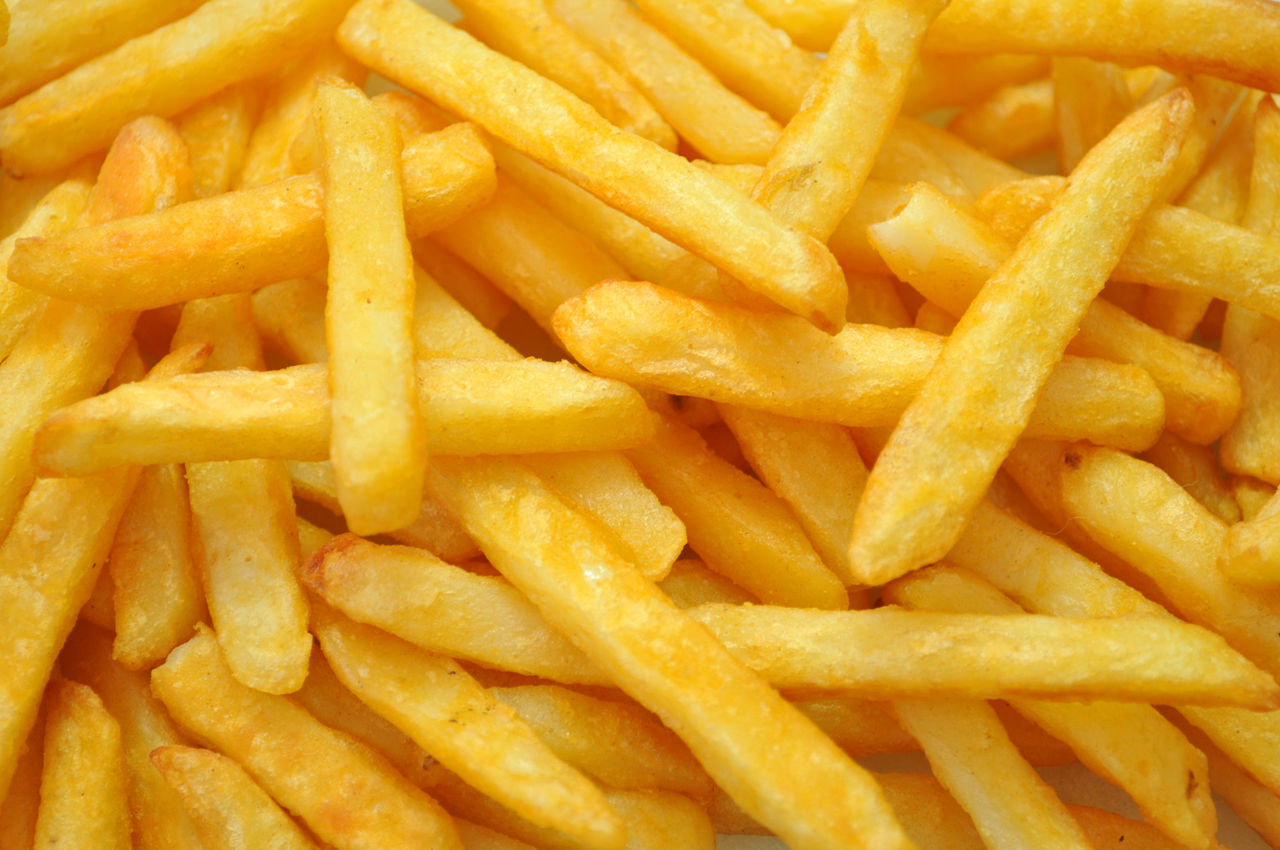
This particular customer is the biggest buyer of British potatoes. That’s a great deal of spud bashing to get the potatoes clean and ready for processing. Large quantities of silt and sand have to be removed, and a problem at this stage has a massive knock-on effect right down the line.
That was just what threatened to happen – before ERIKS turned up to save everyone’s favourite fries.
All washed up
The customers production line incorporates one duty and one standby pump, driven by Variable Speed Drives, which remove the harmless effluent from the potato washing and discharge it to sea. When the duty pump fails, it should be a simple matter to switch to the standby pump while the first pump is repaired.
Unfortunately this time, the standby pump failed too.
The customer’s Reliability Partner quickly identified the cause of the first pump’s failure as a split pipe. So it should have been a simple matter to swap-out the pipe for a new one and get production back online.
But even with the new pipe in place and the pump apparently working as normal, the waste water still wasn’t being pumped away in the necessary quantities. Instead of being up to their necks in clean potatoes, the production line workers were almost up to their ankles in dirty process water.
Worse still, this time the Reliability Partner couldn’t spot the cause of the problem.
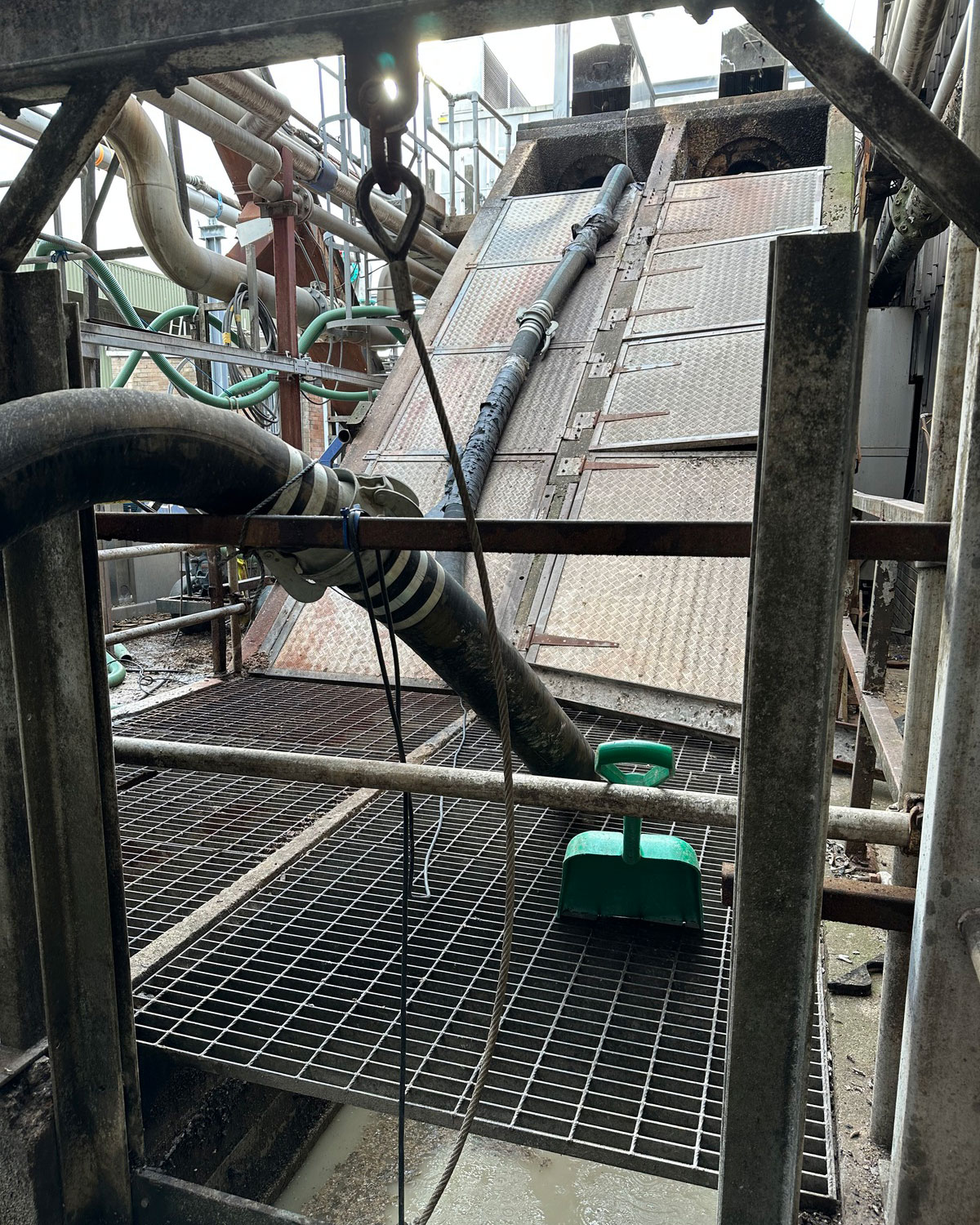
This left the customer with two options. One: shut down production on both lines for at least twelve hours, to allow for removal of the effluent by tanker, and enable access to the suction pipework to look for the cause. Or two: call ERIKS for a better solution.
Which do you think they did next?
Reliably reliable
The customer were sure they could rely on ERIKS in an emergency. And they were right. An ERIKS Pump Application Engineer quickly rearranged all his appointments, and arrived on-site the very next day.
His visual inspection didn’t reveal any new information, and even photographs and videos provided by the customer didn’t help to clear up the mystery. However, when the ERIKS engineer asked to view the customer’s Building Management System – which also recorded the pumps’ flow rates and pressures – he had a lightbulb moment.
The data showed a 90% drop in the pumps’ performance, even before the outlet pipe had split. With flows varying from 300m3/hr down to as little as 30-40m3/hr, it was clear that the pumps were drastically failing to keep up with the flow of effluent.
But why?
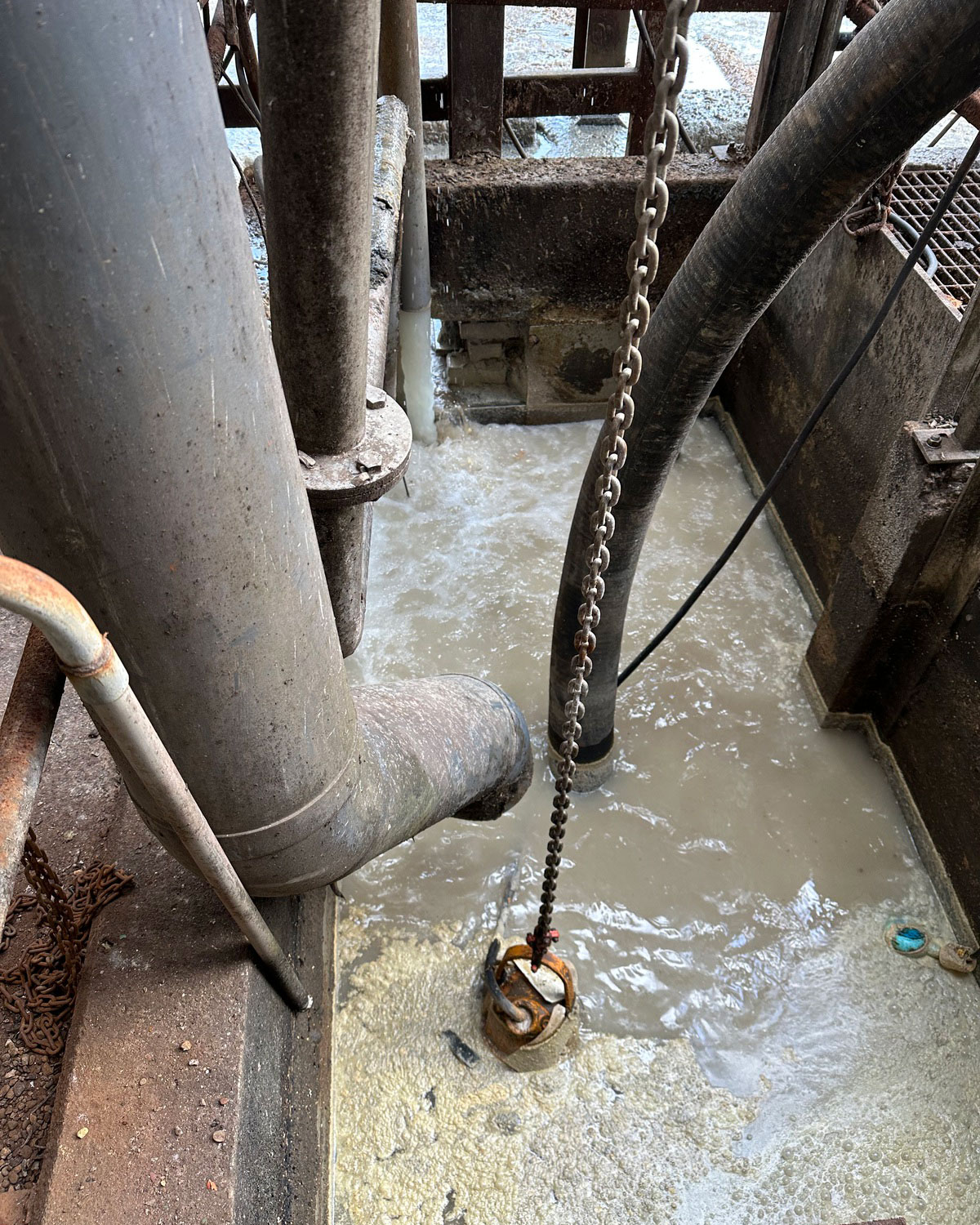
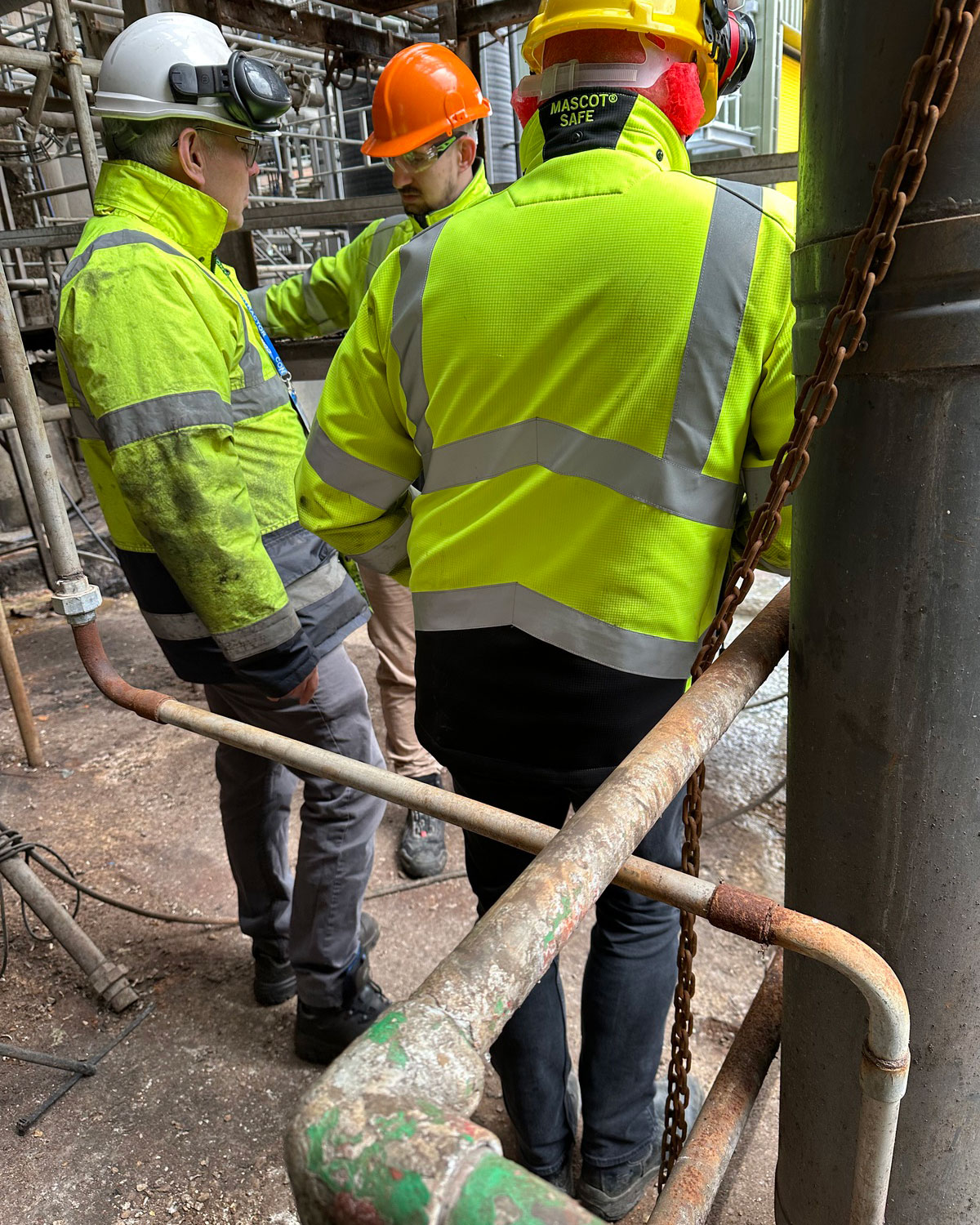
Keeping it clean
The ERIKS Pump Application Engineer knew that, connected as they were to 8” diameter pipework, pumps of this capacity should operate at 2.7 – 3.5m/sec velocity to be self- cleaning. He also knew that these particular pumps were operating at well below that rate.
The result was ever-increasing clogging of the suction apertures with silt and sand from the potato washing process, so that excess water overflowed into the surrounding area.
A quick calculation (quick for someone with ERIKS’ know-how, anyway) showed that if the pumps were run at 120% they would achieve 3m/sec velocity with a 330m3/hr flow rate, and self-cleaning would kick in.
So the VSD was adjusted, the duty pump was switched on – and within 90 seconds the pump was back to full flow. When the standby pump was run at the same rate, the same result occurred.
If ERIKS had failed to resolve the problem, the customer would have had to tanker away the effluent to enable access to the submersible pumps. That would have meant a twelve hour shutdown of two production lines, and a cost of lost production totalling £24,000. Which is big potatoes in anyone’s book.
For more on how we can help meet your Maintenance needs please contact your local ERIKS Service Centre, who will be happy to discuss your options.
#ERIKS #LetsMakeIndustryWorkBetter #Reliability #Pumps #Maintenance