In this article
Sewage, Getting to the Bottom of It...
When customers contact ERIKS for a quotation, they obviously know what their basic problem is that needs addressing. They often also have the solution in mind, even if they don't tell us as much.
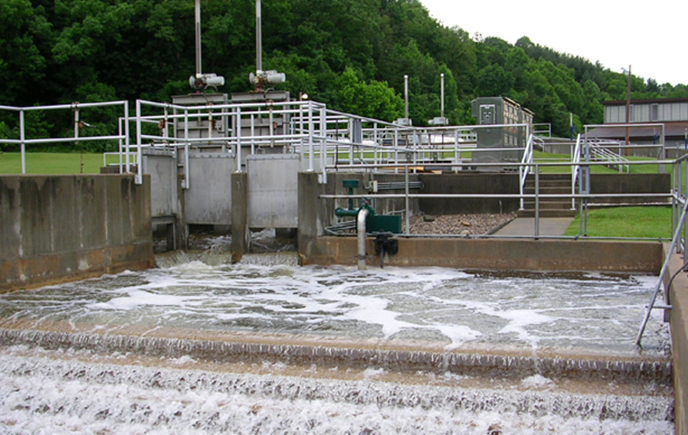
But our repair or replace approach to problems, coupled with comprehensive engineering and application experience, means that the ultimate solution the company delivers is often very different, very much better, and gets to the very bottom of the problem.
One such challenge began life as a request to refurbish an existing Picket Fence Thickener at Beckton Sewage treatment works in east London.
This is one of Europe’s largest sewage works, the fourth largest such works in the world, and currently serves 3.5 million people – though most of them will never even think about it. However, that’s exactly how its operators like it. Most people only think about sewage when something goes wrong with its removal.
Fortunately, the problem that got ERIKS called in wasn’t at that stage yet.
A Sinking Feeling
Anyone who has ever passed by a sewage works will have noticed their most prominent feature: the large circular tanks; however what you cannot see is the revolving picket fence suspended on a slewing ring in the middle of the tank driven by a gearbox, mounted on top.
As it rotates, this ‘fence’ creates vertical voids in the sewage sludge in the tank, which allow water and micro-bubbles to rise to the surface, so the sewage sludge thickens and sinks to the bottom. At Beckton works, this thickened sludge is then used to power an on-site Sludge Powered Generator.
The problem at the Beckton works was the repeated failure of the Picket Fence Thickeners (PFTs), caused by the tanks regularly over-filling with sludge. This sludge then contaminated the slewing rings, which in turn led to a complete seizure of the rolling element raceways.
Rather than simply refurbishing the Picket Fence so it could fail again, ERIKS’ engineers wanted to know what else lay behind the failure.
Only Human
As in many cases of machine failure, ERIKS’ discovered there was a human element involved.
Their initial assessment found that the existing drives had a worm gearbox installed, complete with a torque limiter. As well as the rolling element raceways, the torque limiters were also seizing in place, due to the atmospheric conditions. As soon as this occurred, the drives’ mechanical protection became non-opera, and the electronic overload limits were activated.
Cause and Effect
The first step for Andy Sillis, Technical Manager for ERIKS Dartford, was a detailed inspection and assessment to determine the best course of action – a course which would not simply postpone the problem until it happened again, but permanently cure the root cause.
Andy realised what was obvious but had not been considered: that by eliminating the contamination entirely, the slewing rings would no longer seize up. To do this meant raising the slewing rings clear of the sludge, which required the fabrication of two entirely new supporting spool pieces. His inspection also revealed that the driving gearbox was coming to the end of its service life, so a recommendation was made to replace this with a new planetary drive. This would mean many more service hours than the old unit would provide, and greater torque output and greater efficiency.
To prevent human error or misplaced intervention, the torque limiter was replaced with a new Mayr internally sealed FTL series, which has a manual resetting feature to prevent tampering by the operators. New slew rings – and an adaptor plate for mounting – were manufactured and fitted, and the existing greasing system was replaced with a positive displacement powered grease dispenser. Lastly, to incorporate the new design, the entire supporting structure needed to be raised and a newly-fabricated supporting frame installed.
Once the existing drive had been removed by crane, and the new equipment installed, a newly-fabricated walkways structure was placed on top, and the electrical connections and lubrication system set-up ready to go.
With the project completed, the PFT was set in motion once more. Production of the thickened sludge got under way again to the great relief of 3.5 million Londoners – if they’d ever known there had been a problem.
Discover how we can help your further by downloading our Water Industry brochure.
For more information on Engineering, Repair and Replace solutions please contact your local ERIKS Service Centre, who will be happy to discuss your options.
#ERIKS #LetsMakeIndustryWorkBetter #RepairAndReplace #WasteWater #BecktonSewage