In this article
Supply chain disruption is driving reshoring. But are we ready?
The trend towards reshoring has been growing for some time. It was initially prompted by Brexit, combined with a decline in the value of the pound, tariff disputes, geopolitical uncertainty and climate change. The Covid-19 pandemic, however, which has caused major disruption to global supply chains, has forced many manufacturing companies to take a long hard look at how and where they produce products and systems.
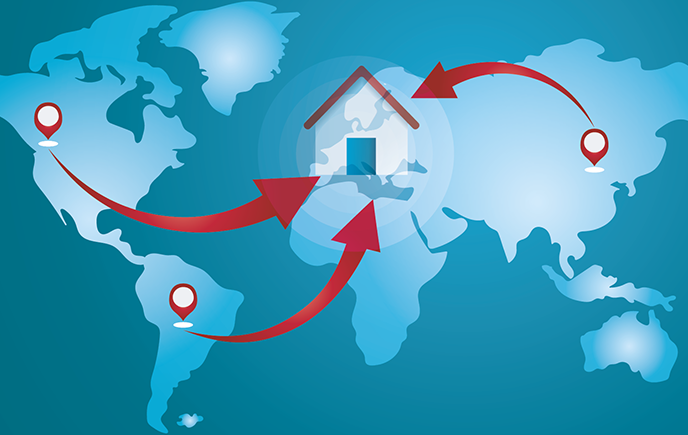
A poll published by The Engineer magazine a few months ago, at the height of the Covid-19 crisis, found that 59% of readers believed that there should be a wholesale, UK-wide policy of reshoring manufacturing operations, with a further 32% stating that as a minimum the production of critical supplies should be brought back to the UK. Just 9% felt that existing arrangements were adequate or that the only option was to use low cost economies as a way of remaining competitive.
Perhaps the key question is ‘can UK reshore manufacturing at scale, sustainably and over both the short and long-term?’
The reshoring challenges
Reshoring is clearly a key strategic decision, especially for those manufacturing companies that have offshored all or most of their supply chain and production operation. The decision will be a central factor in a wider business strategy and will be driven by many different factors, from cost and operating margins, to market demand and customer expectations. As the authors of a report from Warwick University 'Realities of reshoring' pointed out, ‘Why to reshore is a blend of internal competitive priorities, external incentives and risk mitigation’.
It’s worth noting that reshoring part or all of a manufacturing operation is unlikely to be the same as the activities that were originally offshored. Products, processes and markets will inevitably have changed since the original offshoring decision; activities that return to the UK may therefore look completely different.
In part, this will be because the manufacturing world is continuing to change rapidly. With the rise of I4.0 and the Industrial Internet of Things (IIoT), the growth in automation, greater connectivity and smarter factories, the way in which we now produce products and systems revolutionising our approach to supply chains.
Other factors that are influencing decisions to reshore include the growth in additive manufacturing technologies. These have now reached a point where high quality, volume parts can be produced in a wide range of metals, from conventional engineering steels, to titanium and exotic materials such as Cobalt Chrome. These parts are suitable for the most demanding production applications and can be manufactured quickly, at the point of use and at competitive cost; clearly, this is something that cannot be achieved using a traditional supply chain model.
Perhaps as importantly, additive manufacturing techniques also allow new product variants or modifications to be prototyped and then moved into production extremely quickly. This complements another emerging trend: the demand for low volume custom manufactured products available on demand. A classic example of this was the response of many UK companies to the Covid-19 crisis, where PPE was being produced at scale by many different businesses within days or weeks of the market need becoming evident.
Skills and recruitment
Perhaps one of the greatest challenges for manufacturers in reshoring is to ability to recruit skilled employees to staff any reshored UK facilities. In the last two decades we’ve lost a wide range of highly experienced design and manufacturing engineers, machinists and tooling specialists. For example, a survey by the GMB Union highlighted the fact that the UK has lost around 500,000 manufacturing jobs in the last ten years, many of these were skilled workers with many years of collective knowledge. As we emerge from the Covid-19 pandemic the likelihood is that in the short term many more manufacturing jobs are likely to be lost.
Clearly, this is going to present a major challenge for manufacturing businesses. One option for a reshored operation is to find local partners that are capable of providing the required skills and support capabilities.
Download a copy of our whitepaper
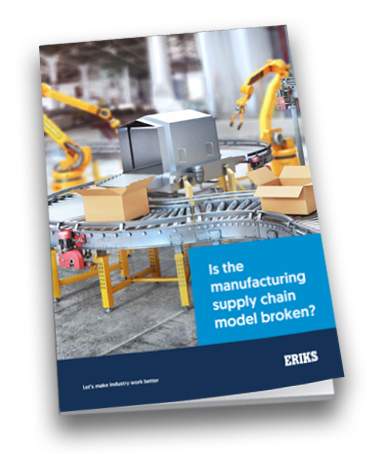
In essence, this is an outsourced model, almost identical to the traditional offshoring supply chain relationships that currently exist. The difference being, of course, that the supply chain – or at least a large proportion of it – becomes almost self-contained within the UK.
Suppliers such as ERIKS, for example, are well versed in both the local stockholding and supply of critical components, often on a JIT basis, and in providing dedicated manufacturing or assembly services that integrate with the supply chains of different customers. These services typically include the design, development and manufacture of sealing solutions, product design or re-engineering and sub-system assembly or build.
Protecting quality, margins and reputation
It’s become evident in recent years that, especially compared with the boom in offshoring in the last two decades, manufacturers are no longer led solely on price and labour costs. Today, the capacity and skills to manufacture locally in the UK, with the ability to hold inventory and meet short lead times, while mitigating risk from volatile overseas trade conditions, are of far greater importance. So too are factors such as corporate reputation, sustainable environmental policies and customer satisfaction; all of these criteria can be more easily achieved by moving production back to domestic soil.
To find out more, talk to one of our logistics experts today or contact your local ERIKS Service Centre. Alternatively, you can download our latest white paper on supply chain disruption above.
#ERIKS #LetsMakeIndustryWorkBetter #IndustrialSupplyChain #SupplyChainManagement #COVID19 #Brexit