In this article
Strengthening the industrial supply chain: The route to 100% pick accuracy
Pick accuracy – the ability to ensure that every part or product delivered is exactly as ordered by the customer – is a term that’s widely applied throughout the logistics sector.
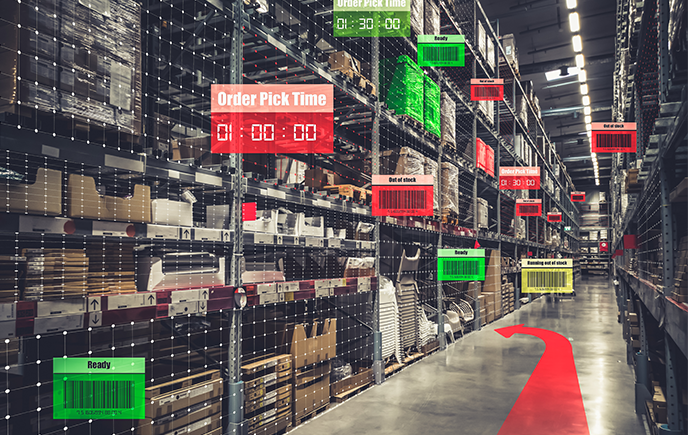
Although pick accuracy derives from retail logistics, it applies equally to the distribution of industrial goods, where it is arguably even more important. For example, an incorrect consumer delivery, frustrating as it may be to the individual, is unlikely to be as costly as failure to deliver the correct replacement bearings for a production system that has had to be taken out of commission and which may cost hundreds or thousands of pounds for each hour that it’s inoperative.
Order picking accuracy is one of the more complex procedures in any warehouse, especially those that depend on a high degree of staff involvement in selecting the correct products. Although industry statistics are difficult to obtain the general consensus is that best-in-class warehouse operations achieve a pick accuracy that is greater than 99%.
However, even if less that 1% of goods are incorrectly picked this can still potentially result in either a large number of disappointed customers or, if the error is identified prior to despatch, an inevitable delay in delivery.
The Oldbury Fulfilment Centre of Expertise
We’ve reviewed best practice across the sector, worked with independent industry experts and leading warehouse equipment suppliers, and analysed multiple data sets from our own logistics operation to help us develop an innovative approach that will transform many aspects of the industrial supply chain.
Key to this new approach has been significant investment – running into many millions of pounds – in the most advanced technology and fulfilment systems.
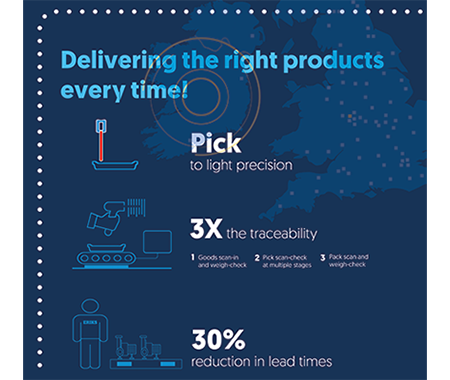
For example, the Oldbury Centre is being built around Industry 4.0 compliant technologies including 21 of the latest fully automated intelligent vertical lifts, with pick-to-light capability, over 400m of high-speed conveyors and an interconnected network of scanning and check-weighing systems.
Advanced technology, however, is just part of the solution. Equally important is our ability to integrate all our systems, from the simplest scanner and check-weigher, through a new and highly sophisticated Warehouse Management System (WMS), to our company-wide ERP platform; and then, in the future, to interface this with similar systems from our customers and suppliers, to develop a truly predictive and dynamic supply chain solution.

Optimising the industrial supply chain
A key aspect of our new industrial fulfilment model is to build an ongoing staff training and career development programme that touches every aspect of our business and its relationship with each customer. In particular, this includes our customer-facing, Fulfilment Centre and backroom teams, to ensure that they have the knowledge and skills to help us reach the highest levels of customer service while continuously improving key processes, such as pick accuracy.
Although achieving the highest levels of pick accuracy require a clear strategy and advanced goods handling and management systems, they also depend on a wide range of far simpler measures. For example, the design and layout of the new Fulfilment Centre has been optimised to enable picked parts to be automatically delivered to centralised receiving points, thereby minimising the distance that staff have to walk each day; this speeds up the order management process, eliminates the risk of errors from manual picking and improves working conditions.
Similarly, by implementing a carefully planned goods-in process we will be able to improve the speed with which goods are subsequently handled and thus our pick accuracy. We will therefore have full quality inspection of all parts before they are entered into our inventory, with each part being bar coded, scanned and check-weighed. This will be part of an end-to-end tracking process of all parts as they progress through the system, giving precise stock control and 100% stock availability, while final scanning and check-weighing prior to despatch will further enhance our ability to reach 100% pick accuracy.
30% faster picking
The combined impact of our investment in infrastructure, technology, systems and people will have a dramatic impact on both our picking speeds and precision. We anticipate that we will be able to increase pick speed by at least 30%, even with a far higher level of quality and inventory monitoring, while from day-one our pick accuracy will be better than 99%.
Ultimately, our goal is to be able to stock the products you need, to able to deliver them to you faster or on the date you specify and to the precise location you require, while ensuring you receive exactly the goods you ordered. As our systems develop, we’ll also be able to work with you to implement an even more dynamic platform, so that we’re able to predict your needs and have the products you require ready and delivered in advance, ensuring that your business operates even more successfully.
#ERIKS #LetsMakeIndustryWorkBetter #DigitalSupplyChain #DigitalWarehouse #FCE #FilfulmentCentre #Expertise #IndustrialSupplyChain