In this article
Digitising the industrial supply chain
Industry 4.0 (I4.0) was first introduced as long ago as 2011 by a group of industrialists, business-people, politicians and academics with the goal of helping the German manufacturing sector become more competitive. The official launch of the concept was at Hannover Messe that same year.
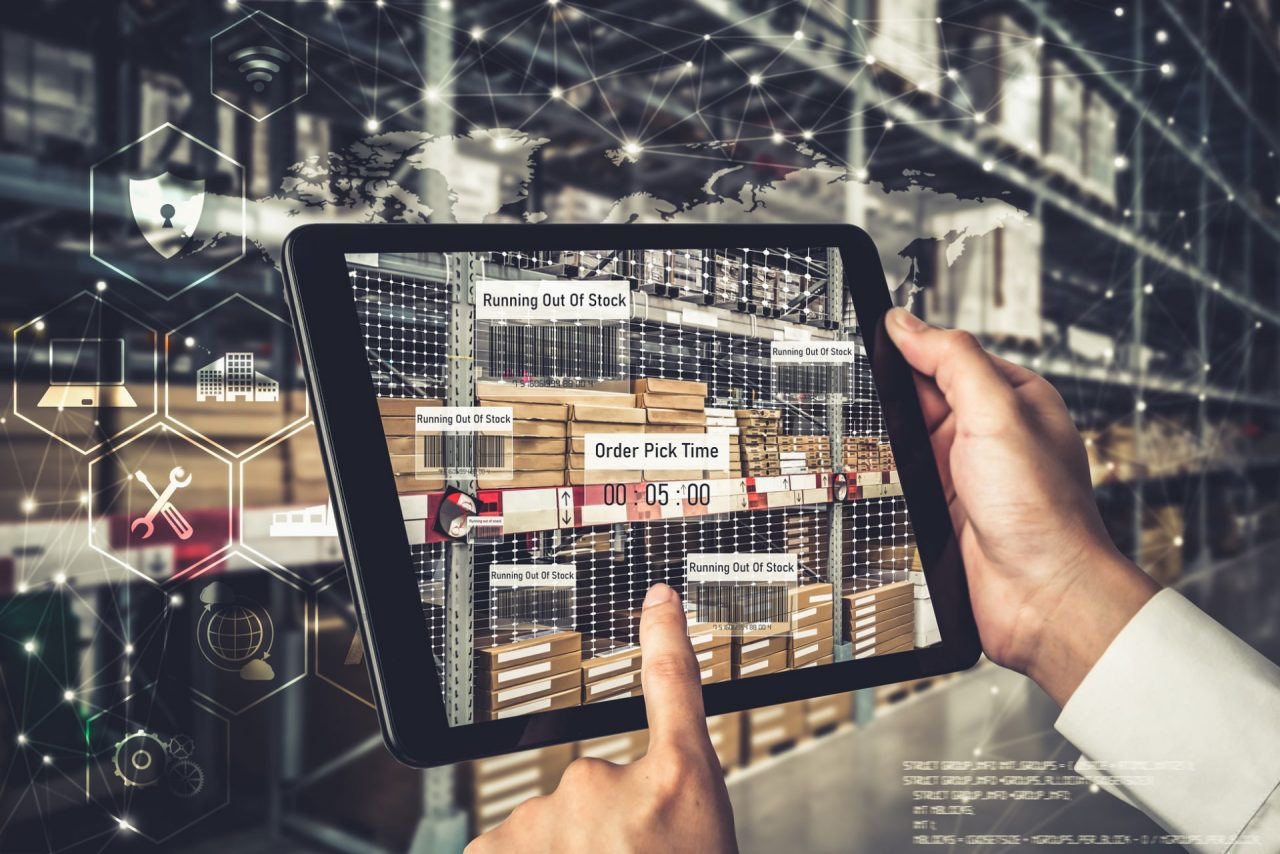
Since then, the term has been variously described as the Forth Industrial Revolution, Industrial Internet of Things (IIoT), Smart Factories and Smart Manufacturing. Regardless of the description you choose to use, it’s fundamentally about the digitalisation and inter-connection of systems and processes to create an environment where high quality data can be gathered in real time, analysed and used to make intelligent and automated decisions to improve the quality, consistency and flexibility of production operations within a broader, interconnected business.
The initial take-up of I4.0 was relatively slow, due primarily to factors such as a lack of suitable technology, the challenges of adapting existing production systems, availability of appropriate investment, and a natural resistance to adopting new technologies until they had been fully tried and tested. There was also, as is often the case with new ideas or technologies, a fair degree of hype, which in the early days inevitably deterred many companies from entering the I4.0 arena.
In recent years, however, the adoption of I4.0 technology has accelerated, with an increasing number of companies developing the vision to implement business-wide I4.0 strategies, together with the funding mechanisms, skills and physical resources. For many companies, the process often starts with a small or self-contained project – perhaps the upgrade of a particular production line – to test the process and act as a model from which to scale-up across the business.
Supply chain integration
In the industrial sector, the focus to date has predominately been on developing strategies and programmes that make each company or business unit I4.0 ready. Essentially, this has been inward-looking with minimal consideration of the vertical integration of the business with customers or suppliers.
This situation is now gradually changing, as manufacturing companies look for ways of improving the service they provide to their customers, while building more resilient supply chains, with greater visibility at all points in the supply, production and delivery process.
Our Fulfilment Centre of Expertise features:
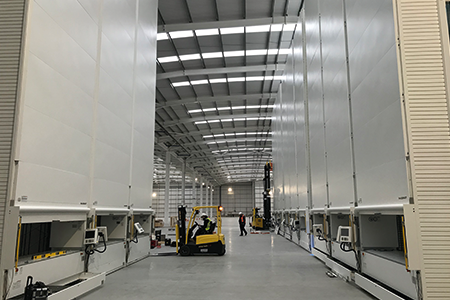
21 fully operational Hane Lean Lifts, with approximately 100 shelves per lift
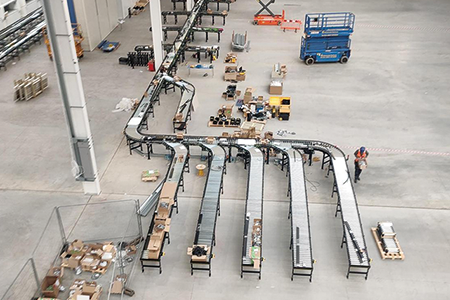
400 metres of intelligent conveyor system with automated scan points, using 50% less energy

Packing areas, 12 Goods-In stations and 20 lanes of dedicated racking
Building a 21st century industrial fulfilment solution
The opening this summer of our new Oldbury Headquarters and Fulfilment Centre of Expertise for the UK and Ireland will be the next stage in our business transformation programme. A key element in this programme is the adoption of I4.0 technologies with the twin goals of enhancing all aspects of our internal systems and procedures, to boost business efficiency still further, and to develop a completely transparent end-to-end fulfilment process for each customer.
We want to be able to ensure that we stock exactly the products you need, bring them to you faster than ever before and deliver the right products every time.
Additionally, we want to give you visibility of each order, from the point of enquiry through to delivery to your production site.
By adopting intelligent logistics technologies, with real time monitoring and reporting, giving interoperability with both our supplier and customers, we will be able to develop what we believe will be the most advanced and efficient industrial fulfilment service available.
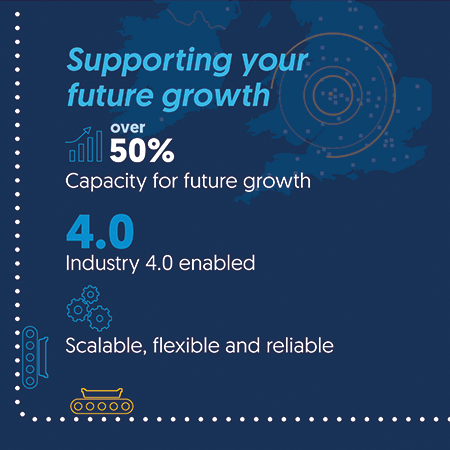
This will, for example, include the ability based on historical ordering to predict future requirements, the option automatically to offer alternative products if the parts you need are unavailable, plus intelligent integration with sophisticated economic and supply chain analytical models to enhance overall resilience.
We’re already taking important steps along this journey. For example, at our new Fulfilment Centre of Expertise all goods-in consignments will be fully inspected and quality checked on arrival. They will then be checked again when they are picked and receive a final scan and check-weigh before despatch, while data from these systems, along with that from our new I4.0 compliant vertical lifts and storage systems, will be transmitted in real time to a dedicated warehouse management system; in turn, this will be integrated with our company ERP systems.
Once the new Oldbury Fulfilment Centre of Expertise is fully operational we’ll be working closely with customers and suppliers to develop and implement a fully integrated, resilient, and agile supply chain solution that supports the future success and prosperity for all those involved.
For more information or to place an order please contact your local ERIKS Service Centre today or alternatively, CLICK HERE to buy directly from the ERIKS Webshop.
#ERIKS #LetsMakeIndustryWorkBetter #FCE #FulfilmentCentre #Investment #SupplyChains #DigitalSystems