In this article
Unidentified production problems can't hide from ERIKS Digital Reliability Services
There are many factors that can determine the efficient running of your production line. But when inefficiencies arise, it’s not always straight forward to identify the root cause. Unless you're able to monitor online... Welcome to ERIKS Digital Reliability Services.
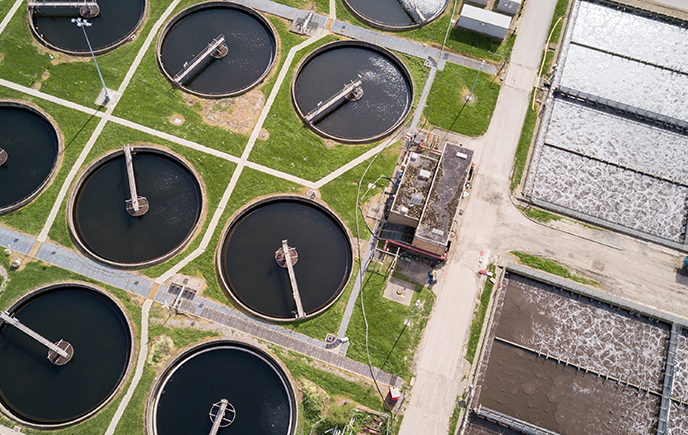
Failures have a variety of root causes – incorrect maintenance activities, lack of regular maintenance schedules, the common issues surrounding ageing and obsolete assets, as well as infant mortality due to improper installation.
But what we can tell you is, no matter how trivial the problem, the longer it remains unidentified, the more catastrophic and costly it becomes.
So, when one large water treatment works was experiencing unidentified repeated failures on a crucial low lift pump, they called on ERIKS’ expertise to discover the root cause and provide a solution that would empower them with insight and foresight into managing future problems.
Enough was enough
Over the past five years, the customer had invested millions of pounds following repeated failures of their assets, many of which dated back to the mid-1970s - not unusual within the water and wastewater industry.
But with costs constantly rising with each repair, as parts were having to be reverse engineered, and SEPA ready to intervene due to serious environmental threats, enough was enough. Now was the time to understand the real root cause.
Sens(or)ing the problem
The ERIKS Digital Reliability Services team attended site to inspect the critical low lift pumps in question, before proposing online vibration monitoring as a method to identify the root cause of these recurring production stoppages.
12 wirefree Bluetooth sensors were installed across three problematic machines, which would enable the team to monitor the condition of the pumps.
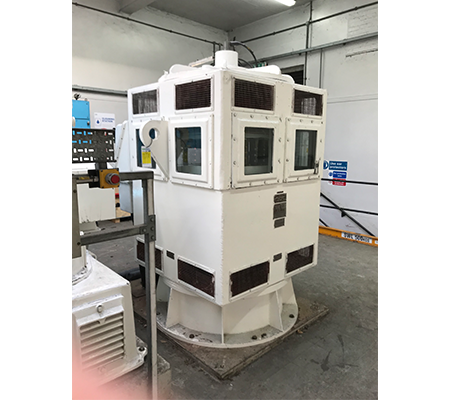
After only a few weeks of testing, measuring attributes including temperature, velocity, acceleration peak to peak and rms, the condition of one of the assets was deemed critical, with automated analysis identified the root cause as looseness within the machine structure due to improper installation. A site team was scrambled, and shockingly, the simplicity of a loose flange mounting bolt was causing excessive vibration, leading the asset down a path of certain failure.
What should be pointed out is that due to the variable speed nature of the asset, vibration was not present at all times and highly directional, making it doubtful that a portable monitoring strategy would have identified the root cause and a wired online needed ‘luck’ to have placed the sensor in the right place, therefore only through the correct selection of the appropriate ERIKS online monitoring solution was the true issue established.
Costs hard to comprehend
To put this problem into a pound note perspective, best case scenario a bill of £80,000 for the removal and overhaul of the asset would have resulted, while if left unattended, costs would have hit a staggering £240,000 with potentially serious damage to the civil infrastructure, motor, commutator, seals, pumps and internal, with many of the components requiring reverse engineering due to obsolescence.
With the problem now identified, the customer was able to rectify the issue, simply by tightening the rear bolts by half a turn, and the front bolts by two full rotations. It’s hard to comprehend that something as simple as a loose mounting bolt could have such a disastrous impact on the customer’s capital, but that was the reality.
The future is online monitoring
Many systems providers often talk about predicting ‘end of life’ to plan intervention, but at ERIKS we talk about extending life by timely intervention and hence safe, calm, rational, total cost of ownership-led decisions can be made.
The introduction of online monitoring has allowed for the implementation of a condition-based maintenance strategy, so now, when any issues arise, the customer has access to real-time data to determine the cause, and thereby a solution, at the earliest indication of any changes in condition, along with immediate affirmation that a change has occurred.
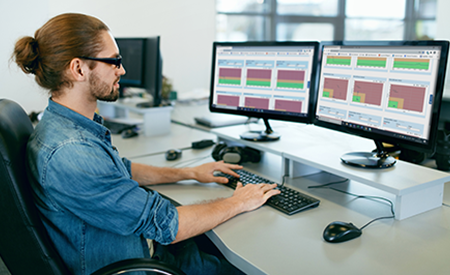
The standard set-up of sensors means that data is acquired continuously, with summary information sent via an on-board signal processing edge-calculation programme every two minutes – equating to over 700 data sets per parameter per day.
The ERIKS Digital Reliability Services interface is easy to navigate, with all data and parameter displayed clearly. Data is narrowed down to individual assets, with thresholds shown with severity scores – from 1 to 10 – for each chosen parament. The list of asset data is displayed as individual trends for a more in-depth analytical view. The power is in your hands.
Managed assets. Long-term benefits
Through the introduction of ERIKS Digital Reliability Services and online monitoring capabilities, the customer now has the support they need when it comes to managing their assets. Energy and cost savings, increased uptime, high productivity, true reliability, and improved efficiency can be achieved not only now, but in the long-term.
Read more about Online Vibration Monitoring
#ERIKS #LetsMakeIndustryWorkBetter #ConditionMonitoring #IoT #DigitalServices #DigitalReliabilityServices #OnlineMonitoring