In this article
How thinking in circles saved steel, energy and CO2
The idea of the circular economy can look good on paper, but is it effective in reality? Who better to answer that question, and take it from paper-based theories to practical application, than one of Europe’s largest paper mills for recycled paper – probably one of the best known, best understood and most widely successful examples of the circular economy.

In the traditional linear economy, we take resources, make a product, then throw the product away when it is no longer usable or wanted. In paper manufacturing, that means cutting down trees to make wood pulp to turn into paper, and then throwing away the paper (whether it’s finished form was a newspaper or wrapping paper or wallpaper) once it was finished with.
But the three principles on which the circular economy operates are very different. Rather than ‘take, make, waste’, they are ‘reduce, reuse, recycle’.
‘Reduce’ means designing products to minimise the amount of resources used in the first place, and therefore the amount of waste generated at end-of-life. ‘Reuse’ means carefully maintaining products so they last longer, and also reusing them to avoid the need to manufacture new ones. And ‘Recycle’ means following good practice at the end of use, to salvage material from the old product to make new products.
For this recycled paper manufacturer, those principles are the foundation of their operation, using recycled materials to produce paper which can then be recycled again, and again.
But they have not limited the application of the principles just to their products. When four large replacement bearings were required after a roll refurbishment, the customer asked SKF to investigate the possibility and costs of remanufacturing all four.
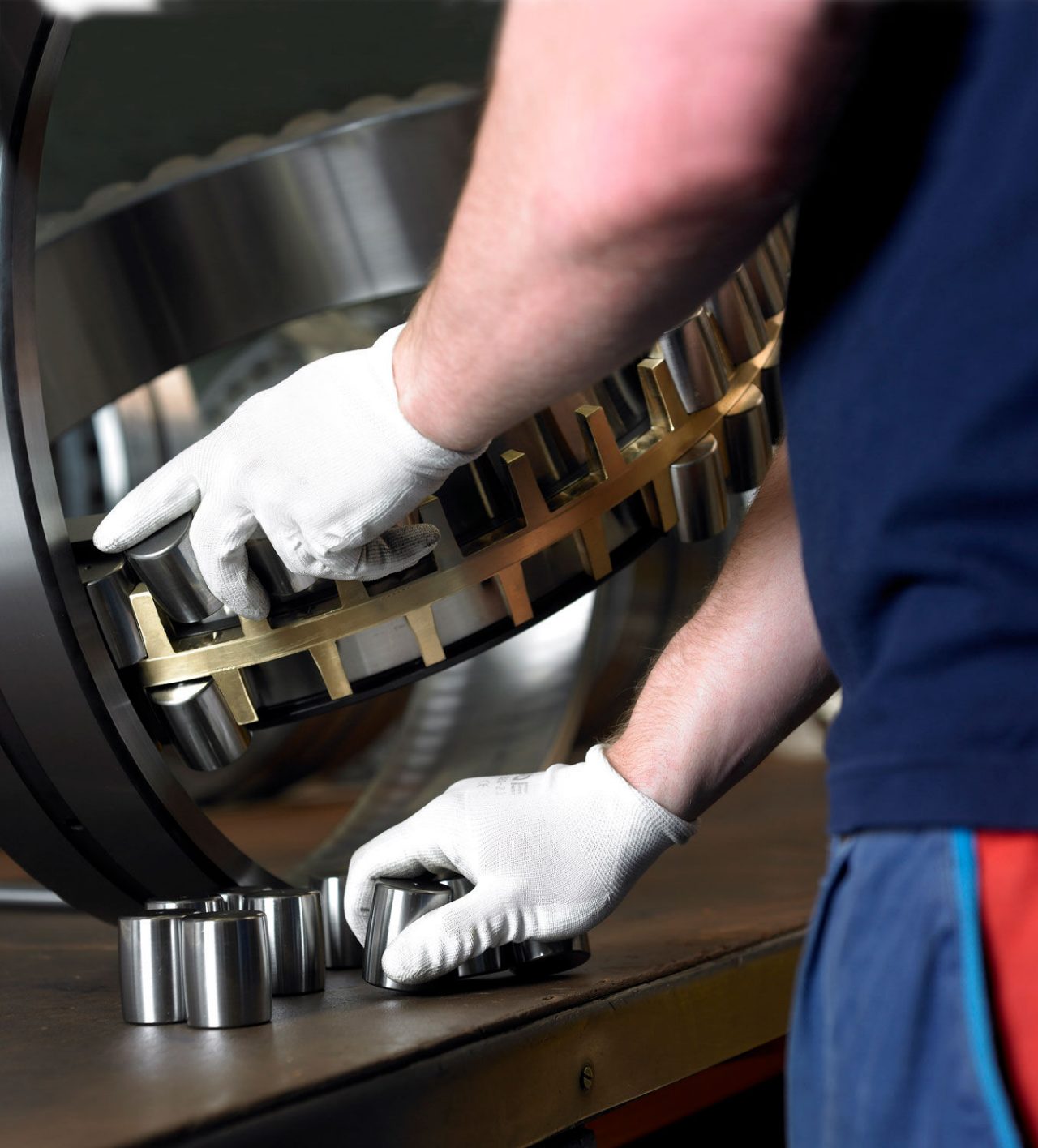
All-round impacts
Manufacturing a new bearing has environmental and economic effects in a number of areas.
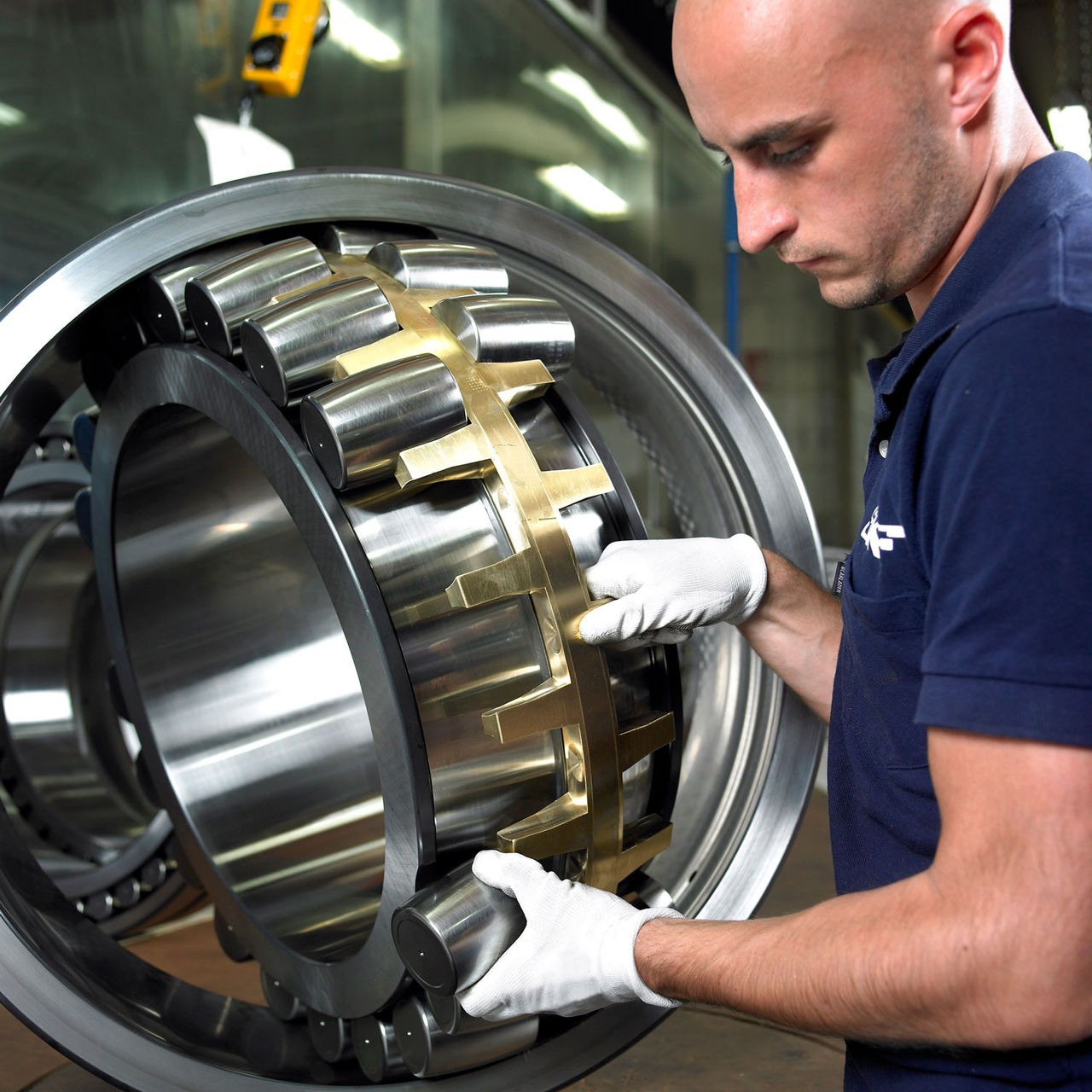
The raw material for the manufacture is steel, the production of which involves several finite resources. There are then further steps in the process from raw material to finished bearing – including forging, turning, heat treatment, grinding, honing and assembly.
Each one of these steps has an environmental impact, whether it relates to energy use, CO2 generation, material consumption or waste, or any combination of those.
Remanufacturing an existing bearing, on the other hand, involves far fewer steps. Which in turn means fewer negative environmental impacts: lower energy use, less CO2 generated, fewer materials consumed and therefore less waste produced.
As good as new – and better for the environment
The reduction in environmental impacts that result from remanufacturing is only one of the advantages compared with manufacturing a new bearing.
Remanufactured bearings have a shorter production lead time than new bearings. This can be critical if there is a risk of downtime and lost production should the original bearing catastrophically fail.
The carbon footprint of remanufacturing compared with making the same bearing from new is 90% smaller. And the cost of remanufacturing is also almost always lower – but without any compromise on quality.
For this particular SKF customer, as for many others, remanufacturing made perfect environmental and economic sense.
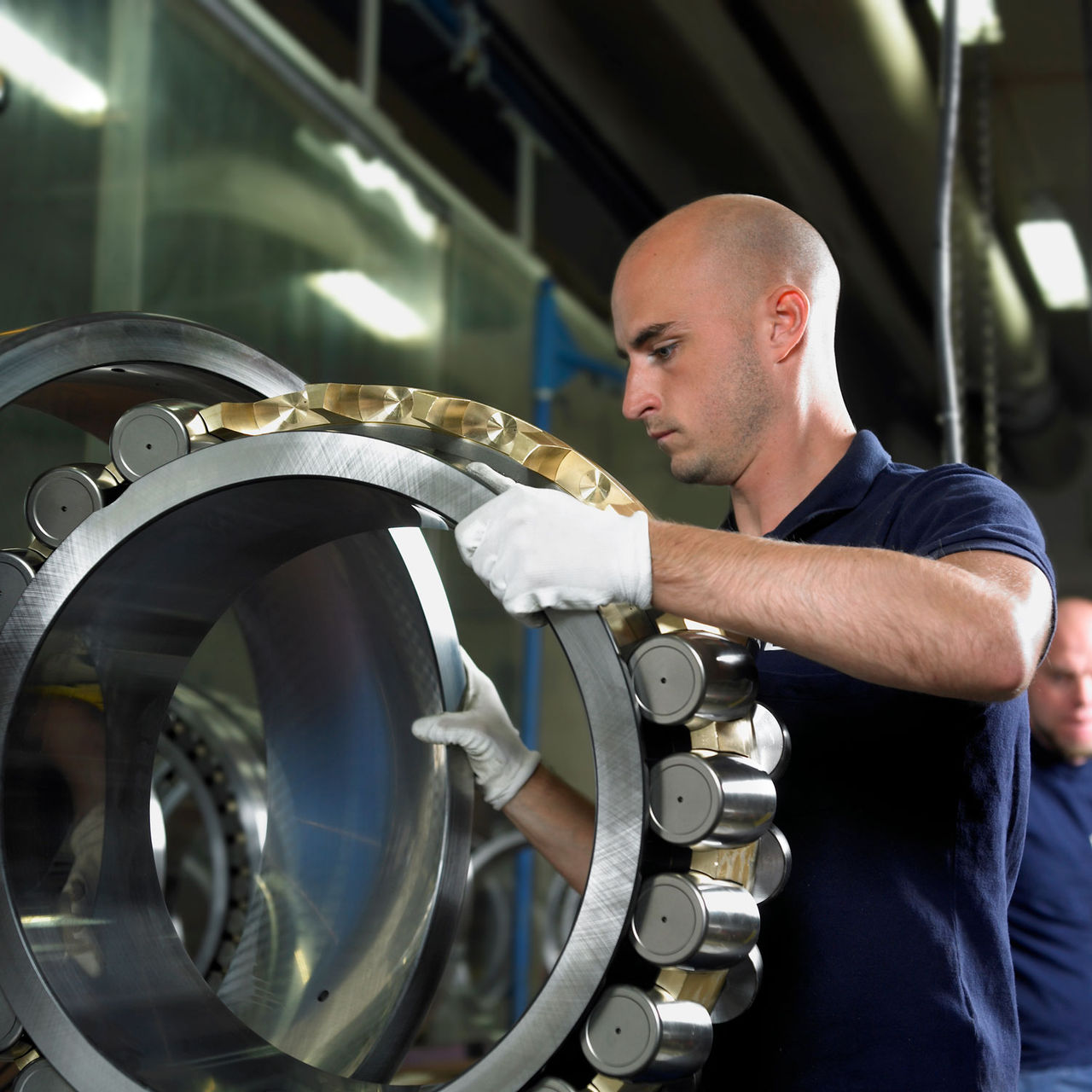
A perfect match
The bearings required were a large precision type, used in the customer’s press section in a paper machine. There were two of each type, with the C08 and VQ424 suffixes indicating that all four bearings have a reduced radial run-out.
SKF’s remanufacturing of the bearings maintained this particular feature, as well as restoring the bearings to as-new condition – for less than the cost of new manufacturing.
In addition, thanks to the SKF Avoided Emission Calculator, the customer could see exactly how much steel was re-used, how much energy use was avoided, and how many CO2 emissions were eliminated [see box-out below].
The figures were good on paper. And the bearings were good on recycled paper manufacturing too.
Reuse, recycle, result
The remanufacture of the bearings produced the following benefits for the customer and the environment.
2-off SKF 23096 CA/C08W77
- Steel reused – 340kg
- Energy use avoided – 2657kWH
- CO2 emissions avoided – 1204kg
2-off SKF 239/750 CA/W33VQ424
- Steel reused – 840kg
- Energy use avoided – 5191kWH
- CO2 emissions avoided – 2352kg
For more information on Bearing Solutions and to get in touch with one of our ERIKS Specialists, please contact your local ERIKS Service Centre, who will be happy to discuss your options.
#SKF #ERIKS #LetsMakeIndustryWorkBetter #Bearings #Remanufacturing #EnergySavings #CarbonEmissions