In this article
Meet the new kid on the plummer block
It’s been 20 years at least since the design of plummer block housings was last improved. Meanwhile dust, dirt and other contaminants haven’t changed either. But the pressure to reduce plant downtime and improve efficiency has. That’s why Schaeffler has developed a completely new generation of innovative, high-quality housing, engineered to perform in even the most aggressive operating environments.
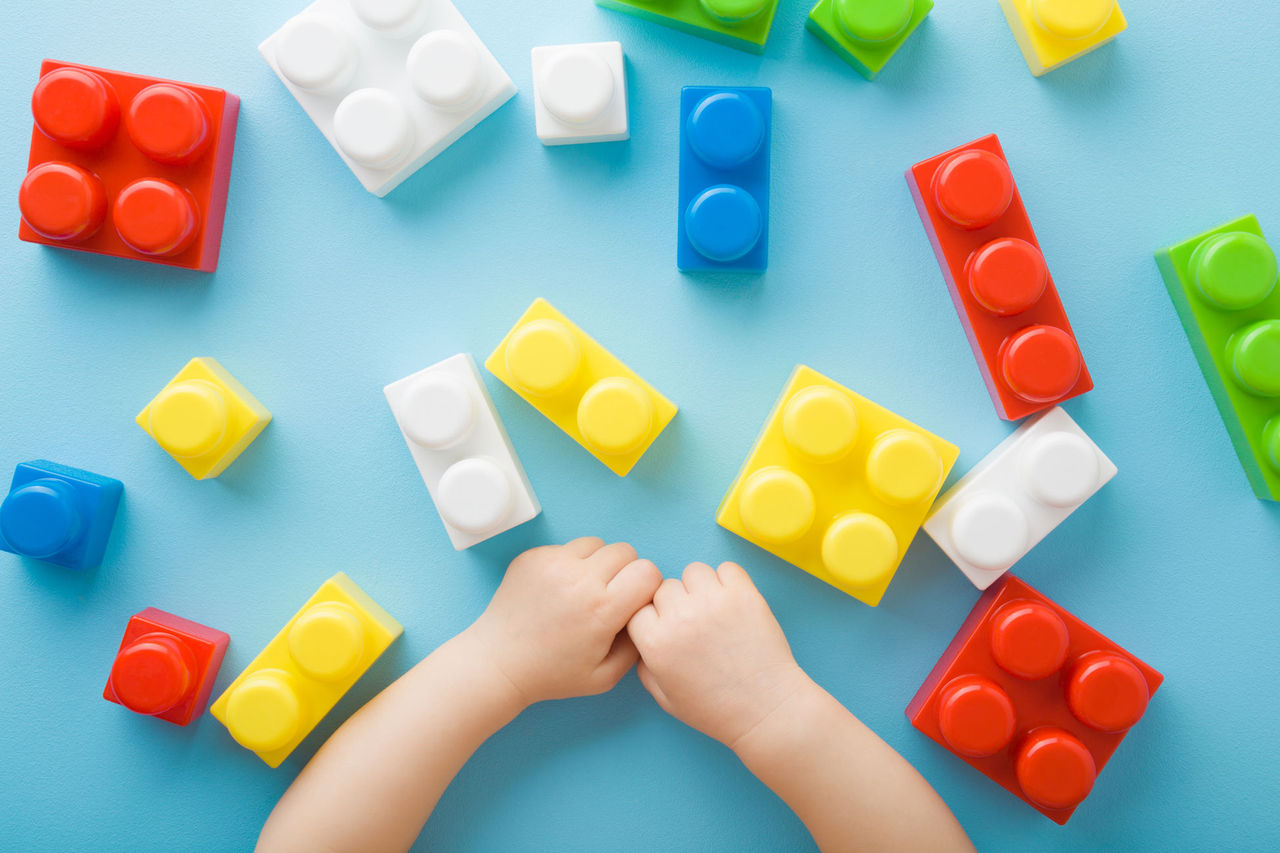
The purpose of a plummer block housing is to increase the service life of the bearing inside. But what about the housing itself? If that can be designed and engineered to last longer too, then the bearing automatically benefits. It’s a win-win situation for the customer.
So the starting point for designing Schaeffler’s FAG SES plummer block housing was to make it more robust, easier to maintain, and more resistant to ingress of contaminants – all so that the bearing inside can carry on performing better, for longer.
Improved – as standard
The new SES plummer block housings are changed and improved, but not beyond all recognition. It’s still built to the same dimensions as current standard housings, so that it’s quick and easy to switch to the new design.
Whether you’re replacing standard housings in conveyor systems, crushers, mills, drive drums, fans & turbines, you can swap for the new, improved solution with minimum fuss.
Added to which, with the new housing installed, things get easier still.
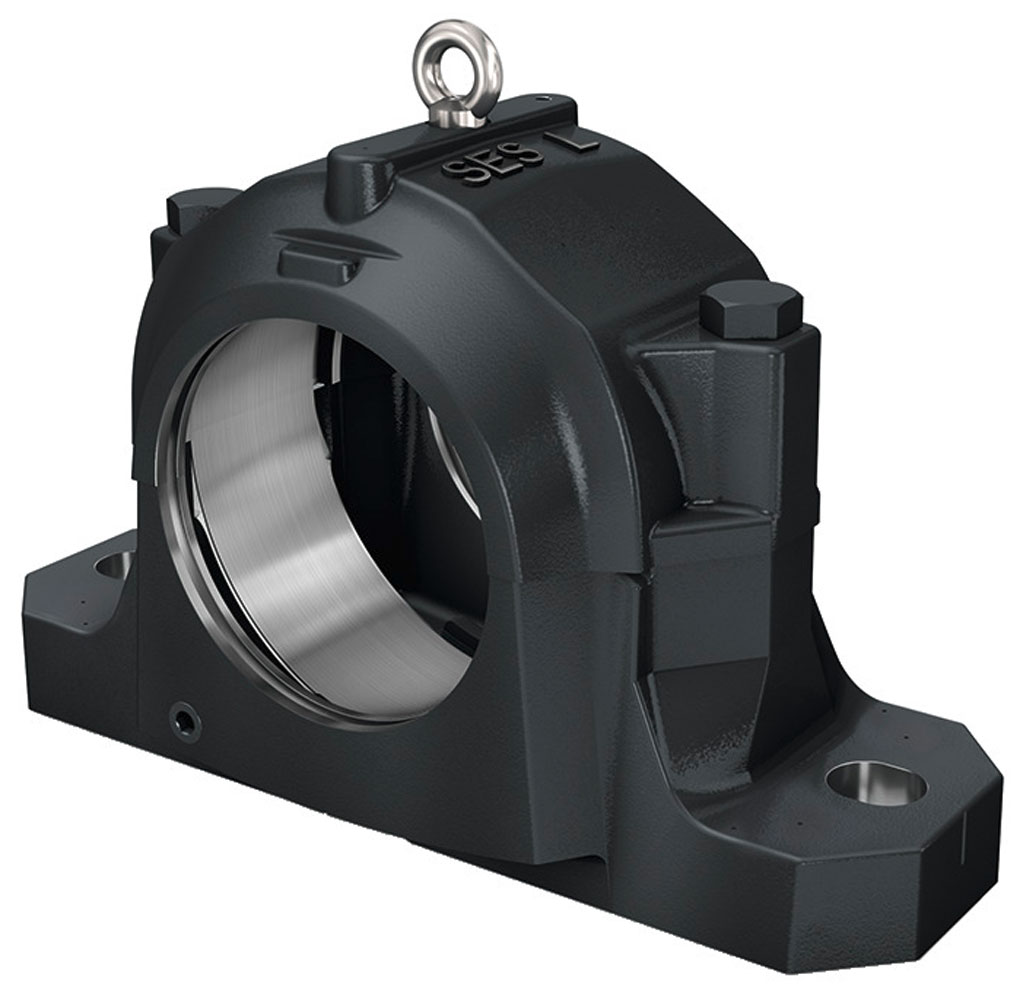
Ready to go
With older versions of plummer block housings, the housing is just the start. If you want to install condition monitoring or mount automatic lubricators, you have to locate and drill them yourself.
But with the FAG SES, half the job’s done for you.
Blind mounting holes for monitors and lubricators are already tapped into the housing, and they’re engineered for optimum effectiveness.
Firstly, they’re drilled to the perfect size so dust, dirt and other contaminants have less chance of finding their way into the bearing. Secondly, they’re quick and easy to align due to markings on the housing that indicate the shaft and bearing centre.
A standardised outlet hole is also provided, to control egress of lubricant and help to reduce wastage and costs.
Easing the load
The optimised design of the SES housing gives it a 25% higher rupture load compared with standard housings – with no increase in weight.
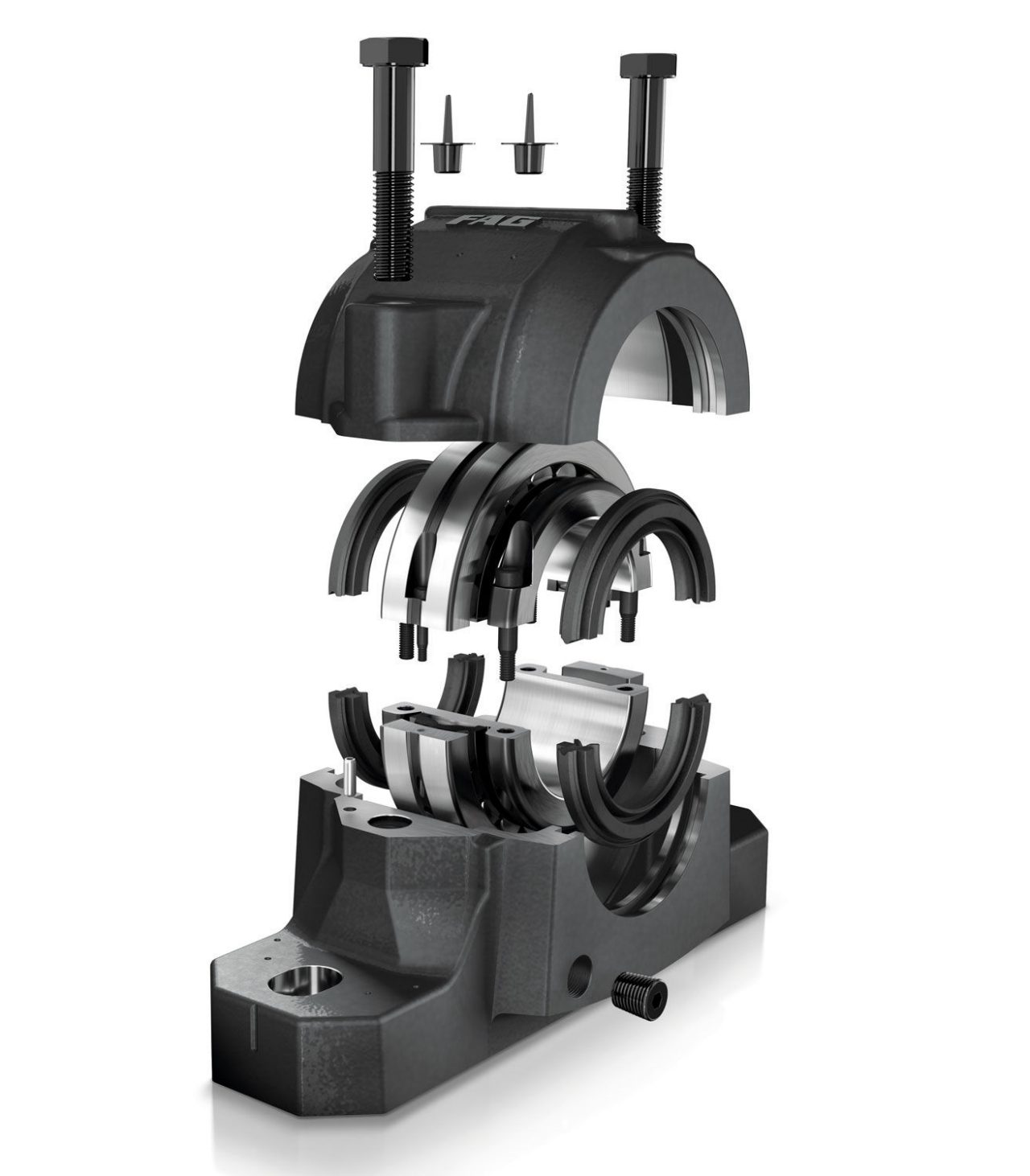
The housing is also available in a choice of two materials. Flake graphite cast iron is standard, but a spheroidal graphite cast iron option will bear even heavier loads.
Any outer surfaces which are not machined by chip-forming methods have a universal paint coating. For even greater protection against corrosion, this can be finished using a choice of finishes: synthetic resin, polyurethane, acrylic, epoxy resin, chlorinated rubber, nitrocellulose, or acid-hardening hammer tone.
Sealing the deal
However tough the housing, it’s still essential to keep out contaminants to protect the bearing within.
The FAG SES plummer block housing incorporates a labyrinth-type Taconite seal to keep the bearing free from contamination in the dirtiest, most aggressive operating environments. In fact this seal is so effective, it even protects against water ingress.
Designed so that split SRBs will fit easily into the housing, the SES means bearing replacement can happen more quickly. Though with the higher level of protection it offers, it means it happens less often.
Case Study: Gold mine finds cash
Gold mining operations at a pair of mines in Western Australia run 24/7, through extremes of high daytime and low night-time temperatures. The tough conditions were causing the bearings on the tube mills to fail annually, disrupting production for two days each time.
Schaeffler’s solution was to replace the sliding base housing at the floating bearing location with sliding sleeve housings and spherical roller bearings. The floating bearing displacement now takes place between the sliding sleeve and the housing bore – constantly fed with lubricant – rather than between the housing and sliding plate.
The results are:
- a low coefficient of friction when thermal expansion takes place inside the tube mill
- no more annual bearing failures
- no more two-day shutdowns
- cost savings of approximately €30,000/hour of saved downtime.
For more information on Bearing Solutions and to get in touch with one of our ERIKS Specialists, please contact your local ERIKS Service Centre, who will be happy to discuss your options.
#Schaeffler #ERIKS #LetsMakeIndustryWorkBetter #Bearings #PlummerBlocks #Innovation