In this article
Teamwork makes a crushing victory
It’s not always what you know, but sometimes who you know. And although ERIKS know-how is comprehensive across industry sectors and applications, mechanical assets and components, occasionally even more specialist expertise is required. That’s when knowing who to call is as important as knowing what to do.

So when the operator of a major mineral mine contacted ERIKS about the scheduled replacement of some unusually large and heavy bearings in their ore-crushing machines, ERIKS got in touch with a bearing specialist with all the necessary experience.
For bearings this size, the more hands on the job, the better.
Avoiding deep trouble
The customer operates the UK’s deepest mine, extracting mineral ores from a mile below ground. These ores are then processed and refined to produce fertiliser and road de-icing salt. As part of the process, the mined ore is crushed in two compacting machines which operate slow-running rotors under heavy loads.
The compacting machines – made in Germany and France – incorporate huge rotor bearings (two per rotor), each with an exterior diameter of 830m and weighing 700kg.
As a crucial part of the production process, the machines operate 24/7 except during the mine’s annual two-week shutdown. This is when the bearings are replaced every 2-3 years, as part of the regular planned maintenance schedule.
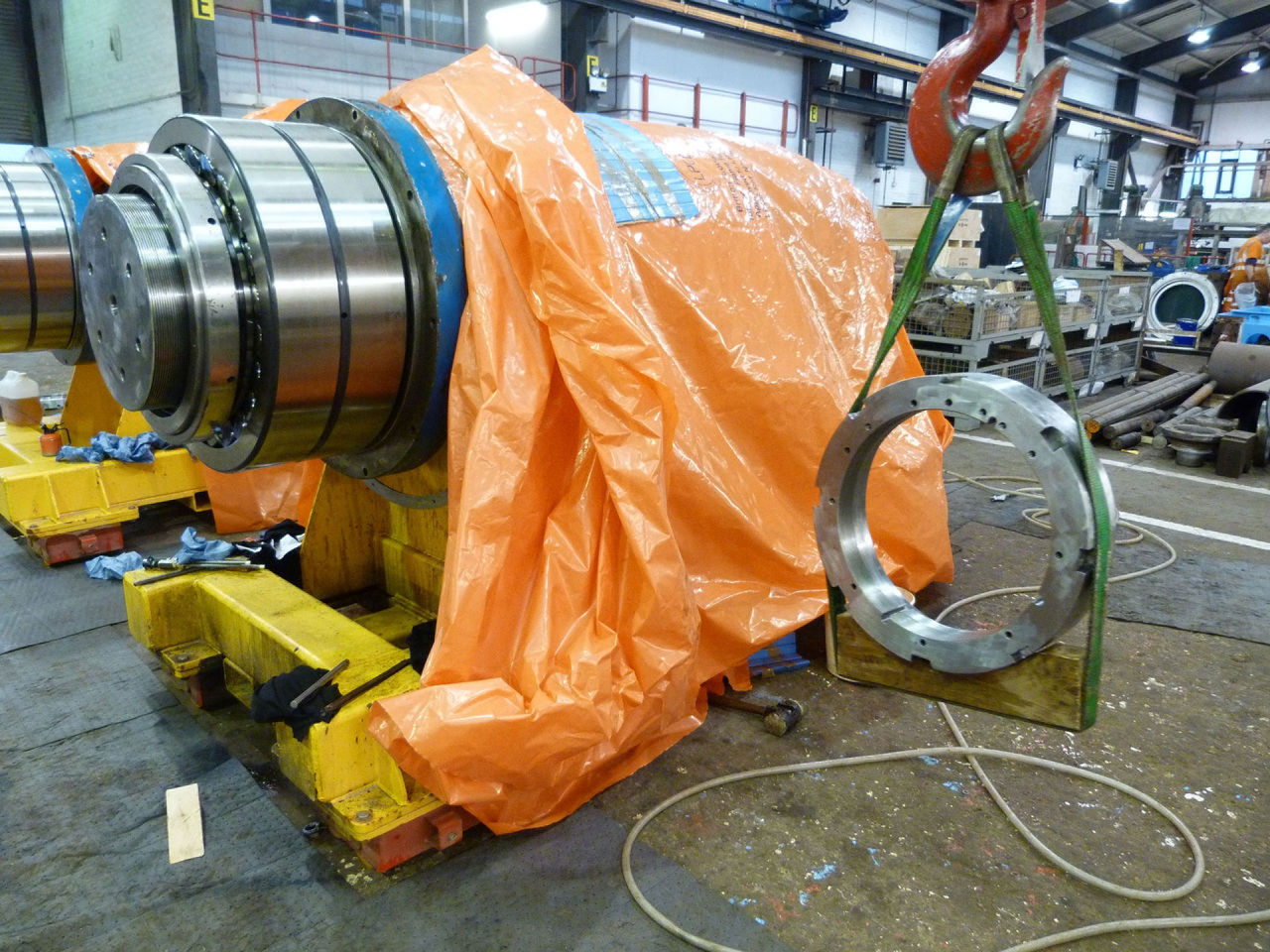
Fitter for purpose
The size of the main crusher rotor bearings means they have a manufacturing lead time of up to 12 months. The difficulty of handling, manoeuvring and correctly mounting them also means that specialist fitters are required to supervise their replacement – and they are few and far between.
By liaising from the moment the customer contacted them, ERIKS and Schaeffler were able to ensure the components, equipment and expertise were available in the right place at the right time, for a quick, efficient and trouble-free bearing replacement.
This meant not only specifying the bearings in good time for them to be delivered, but also arranging for a specialist Schaeffler fitter to fly in from Germany – and co-ordinating another to arrive from Birmingham – thus making both available on-site for a full three days.
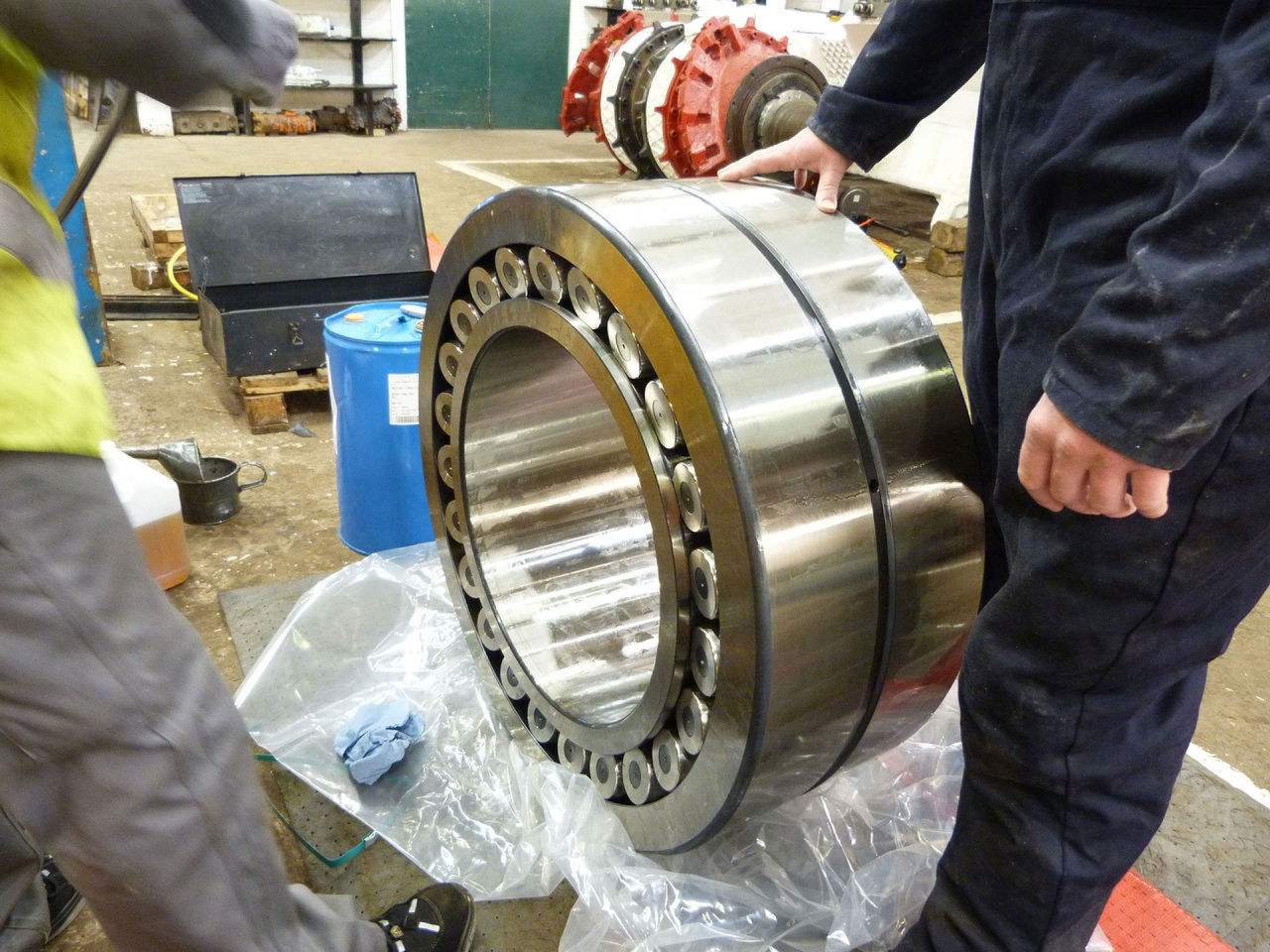
Planned to perfection
To ensure the whole exercise ran smoothly, Schaeffler prepared a detailed method statement specifying the tools, lifting and other equipment required.
The replacement process involved:
- construction of a special rig for the bearing shaft to sit in
- inspection, measuring and cleaning of the shaft
- a high-powered hydraulic annular piston press to push the adaptor sleeves into the bearing during the mounting process
- a specialist fitter to supervise the operation and check the radial internal clearance
- careful checking of the locking nuts to ensure they are tightened to the correct torque
Mounting pressure
In the case of such large and heavy bearings, even a small discrepancy in the clearances or error in the mounting would lead to a high risk of bearing failure and production stoppage. There could also be extensive collateral damage to associated components – all adding to the potential length of downtime and cost of repair.
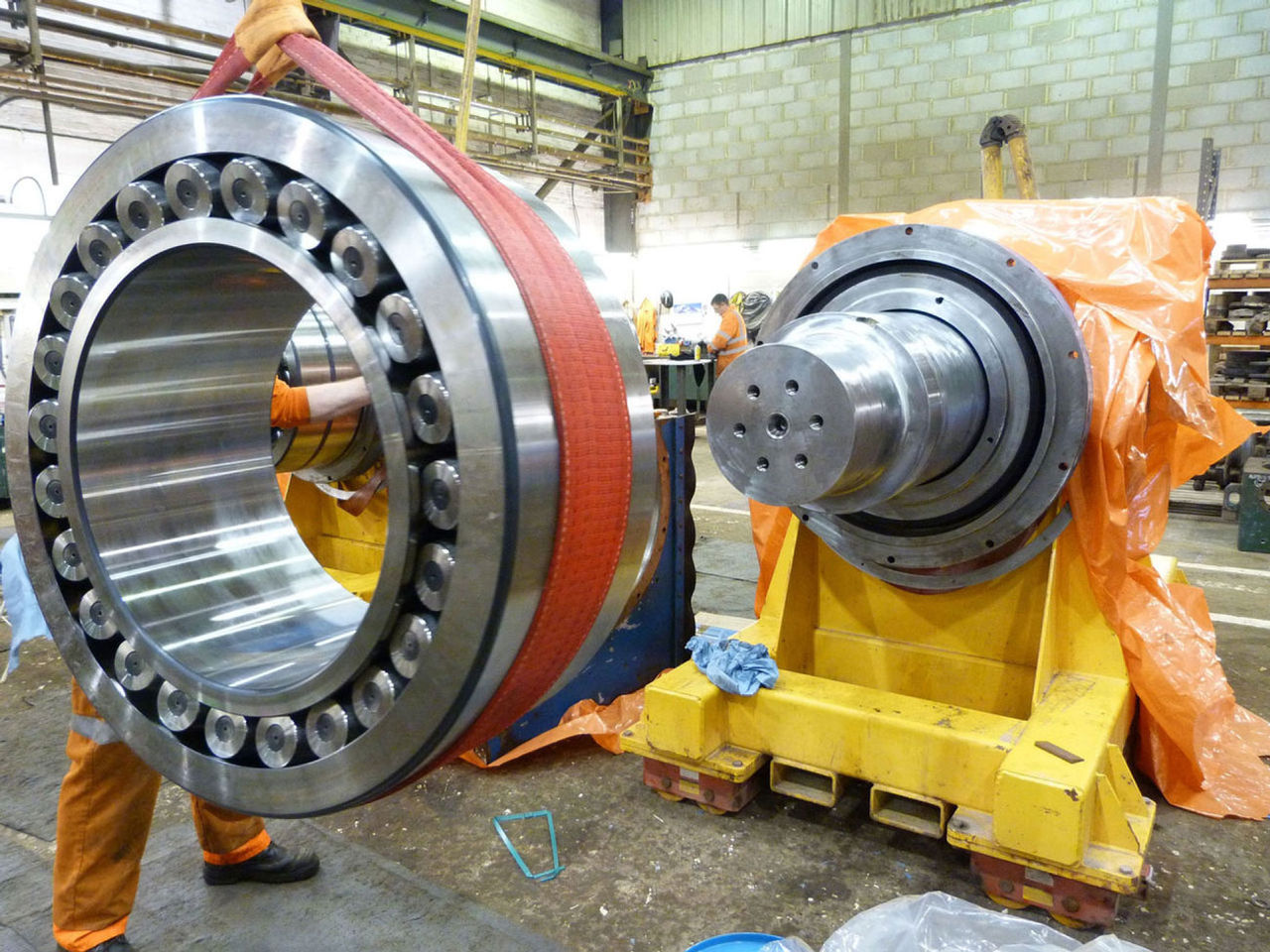
However, by utilising the expertise of Schaeffler’s engineers, ERIKS were able to ensure a trouble-free installation of four new bearings with no disruption to production.
This meant that together, ERIKS and Schaeffler were able to help the customer avoid a potential £30,000 stoppage, maximise the bearings’ life, and – through reconditioning of the bearings which remained viable – lower their total cost of ownership and improve their sustainability.
A victory for expertise, experience, efficiency – and teamwork.
For more information on Bearing Solutions and to get in touch with one of our ERIKS Specialists, please contact your local ERIKS Service Centre, who will be happy to discuss your options.
#ERIKS #LetsMakeIndustryWorkBetter #Schaeffler #Bearings #Specialism