In this article
Timken offer a time-saving new angle on roller bearings
Baking is essential for bricks – to make them solid, strong and hard-wearing. For bearings, it’s not so desirable. That’s why, with temperatures approaching 100°C and large amounts of fine dust in the atmosphere, split roller bearings in a brickworks’ hot air blower were frequently failing. With every bearing replacement causing a day’s lost production, the customer’s maintenance engineers had hit a brick wall.
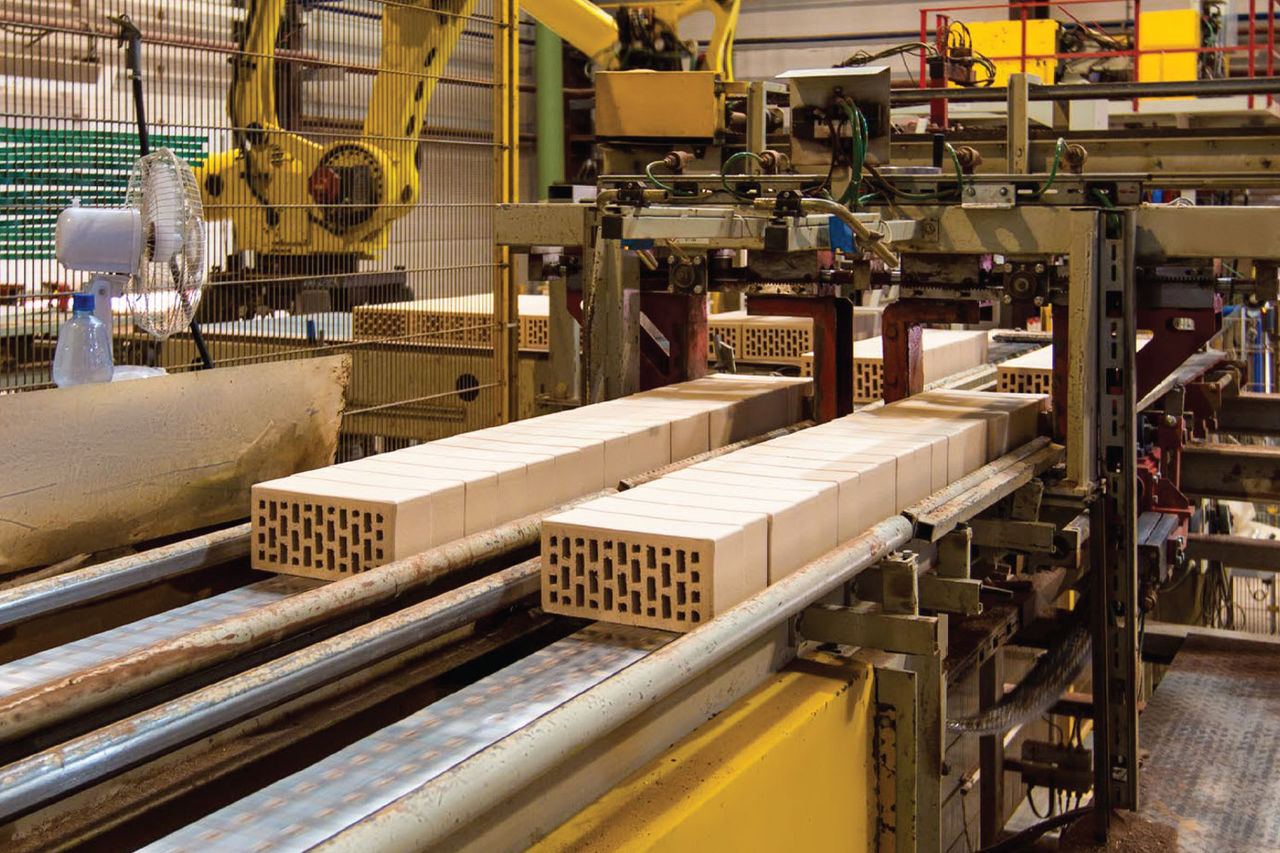
Before bricks can be baked, their moisture content has to be reduced – ideally to below 2%. This is achieved using a hot air blower which recirculates air from the brick kiln. However, while the hot air is good for the bricks it’s bad for the fan bearings. The seals quickly become hardened as a result of operating temperatures of 80-100°C. And the fine brick dust present in the operating environment soon bypasses the failed seals, and finds its way into the bearings themselves – leading inevitably to bearing failure.
In this particular application, replacing the bearings was a time-consuming task. Accessing the failed bearing and installing a new one meant dismounting the blower fan and the transmission, before the shaft could be lifted out of the way and the replacement installed.
A split decision
Even with a split roller bearing (SRB), replacing a failed bearing took the customer 10 hours and involved several maintenance engineers. That meant 10 hours of lost production, and several days’ worth of labour costs.
No wonder they immediately saw the benefits of a Timken angled SRB. The ‘classic’ SRB simplifies maintenance and saves time. But the drive shaft still has to be lifted so the bearing can be installed. A smaller and lighter asset may be suitable for manual lifting, but that’s a potential safety risk for the engineers involved. A larger drive may even require lifting equipment – which means more expense, and possible access issues if a crane is needed.
So when it comes to changing a bearing in this kind of ‘trapped’ application, the Timken angled SRB changes everything.
Look at it another way
A roller bearing with an angled split, like the Timken SNQ, makes it possible to swap out a bearing without lifting the shaft. The shaft does, though, still need support – so the base of the angled Timken SRB housing has been strengthened (using 250-grade cast
iron) to ensure there’s no compromise in performance.
The new Timken SNQ split roller bearings are currently available for shafts of up to 6” (150mm) diameter, in both metric and imperial sizes. The bearings in the new range have also been designed to be completely interchangeable with any existing SN and SD units. For all trapped applications where downtime for maintenance is a critical issue, switching to the time-saving angled SRB is easy.
However, for the customer with the brickworks, it wasn’t only downtime for replacing the bearings which was the issue. It was also the bearings’ repeated and frequent failure in the first place.
The Timken SNQ angled SRBs solved that problem too.
Bulletproof sealing
Fine dust entering the bearings was the main cause of the customer’s bearing failures.
The high operating temperatures in the brickworks caused the bearing seals to harden, giving the ever-present fine brisk dust an easy way into the bearings.
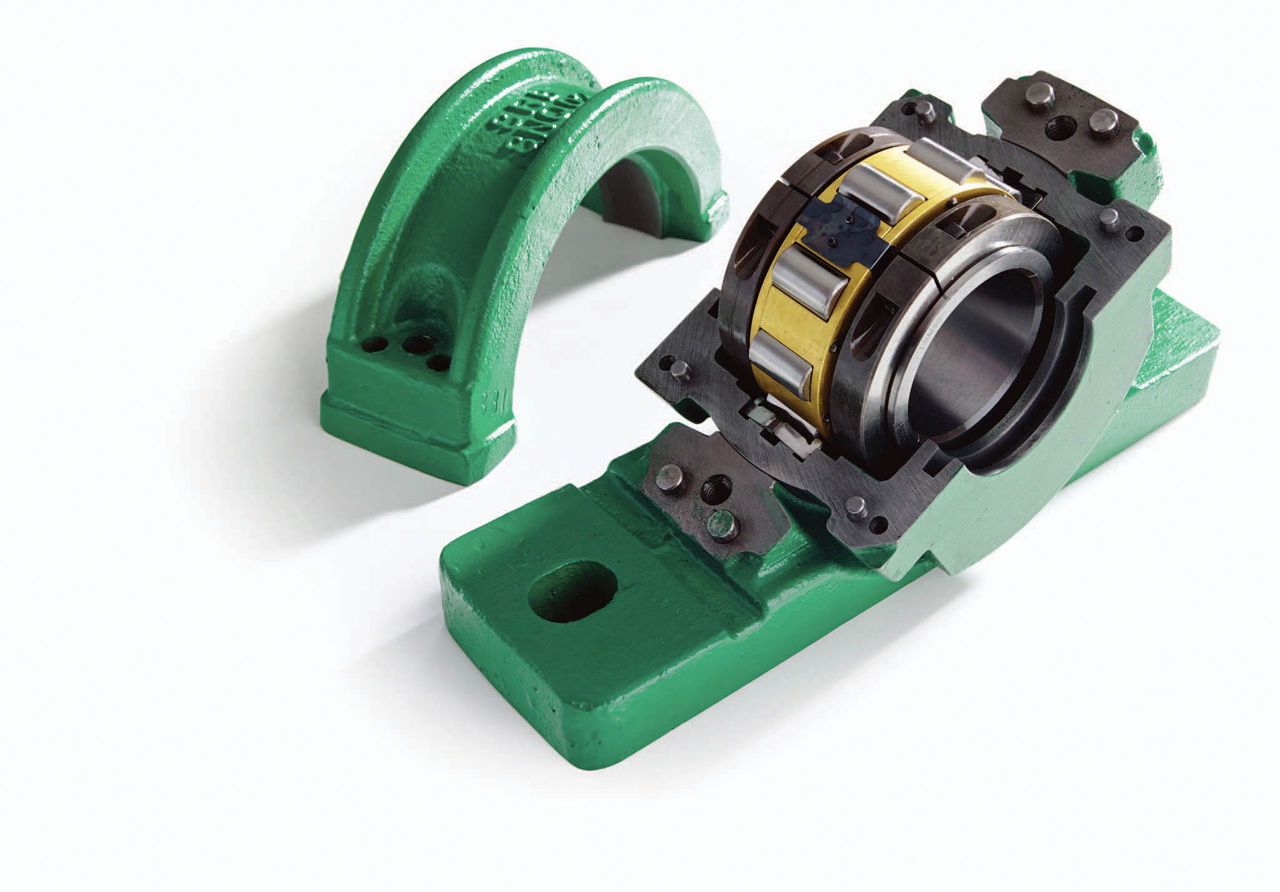
But the new SNQ bearings feature highperformance seals made from Kevlar: the same material used for bulletproof vests. These Kevlar KPS seals are highly resistant to high temperatures, so maintain their sealing qualities – and their protection against the ingress of dust – for far longer than conventional seals.
The KPS seals also run at the speed of the bearing. Which means despite their more effective sealing, they don’t reduce the speed of the shaft or compromise the asset’s performance.
Swings, roundabouts, and bearings
The Timken SNQ angled split SRBs are more expensive than standard SRBs. But the higher ticket price has to be weighed against the lower maintenance costs, increased uptime, and faster, easier bearing replacement.
For this particular application, replacing failed bearings had previously taken 10 hours. With the new angled split bearing solution, this was reduced to just two hours. Which looks like a significant saving from any angle.
For more information on Bearing Solutions and to get in touch with one of our ERIKS Specialists, please contact your local ERIKS Service Centre, who will be happy to discuss your options.
#Timken #ERIKS #LetsMakeIndustryWorkBetter #Bearings #Innovation #SplitRoller #Solutions