In this article
Simalube help give this distiller a reason to celebrate!
If you enjoy a whisky now and again, you probably also enjoy a top-up. But when you’re responsible for lubricating your mechanical assets, topping-up is just one more time-consuming, costly, and sometimes potentially dangerous task. So let’s raise a glass to one of Scotland’s leading distilleries, who – with ERIKS’ help – found a way to simplify their lubrication regime.
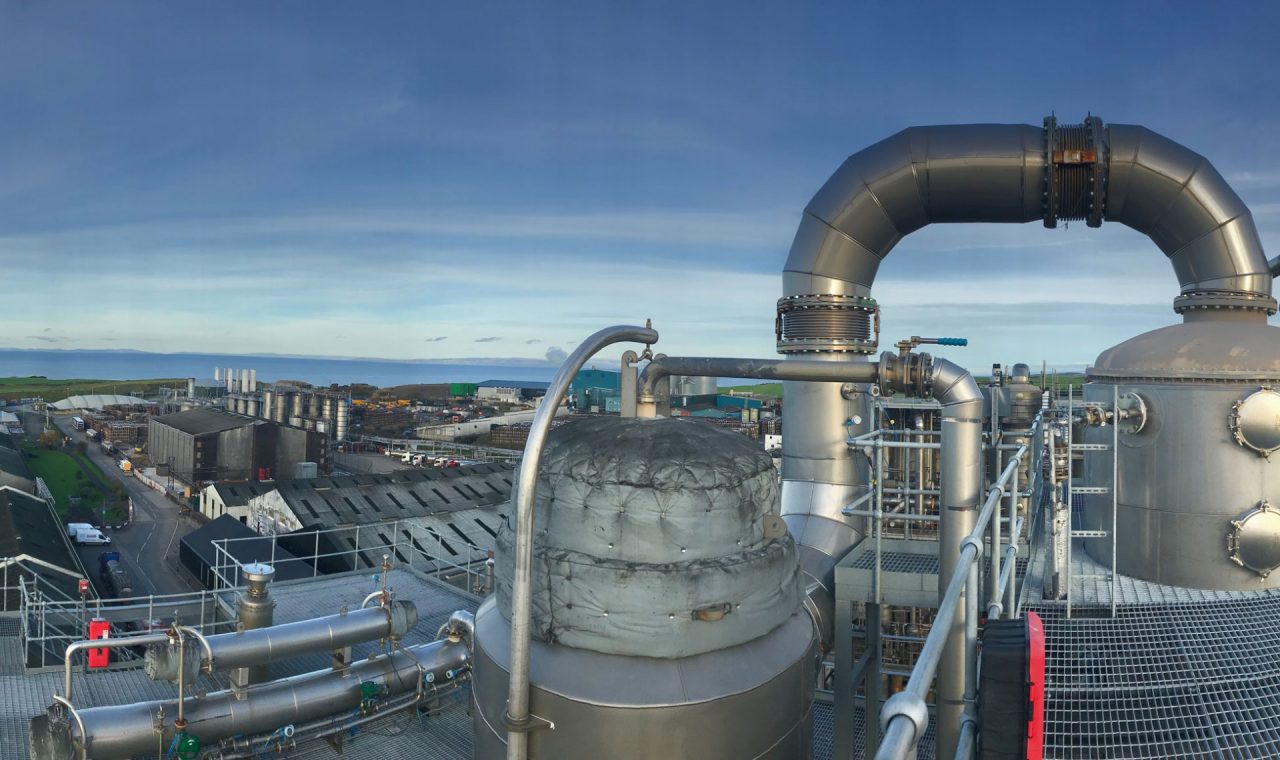
With an on-site presence at the distillery, ERIKS are always on hand to provide support, advice and know-how. Which meant that when the customer asked them to review their lubrication regime, it didn’t take long for ERIKS’ engineers to propose an improvement.
In a location as remote as the site of the distillery, spare parts – and engineers – can take a long time to arrive. So the reliability of assets is enormously important. But whether you are located in the Highlands or the Midlands, and whether you’re distilling whisky, producing food or manufacturing equipment, a key part of maintaining reliability is efficient and effective lubrication.
Lubrication by luck
Although most maintenance engineers will claim to have a lubrication timetable in place, it’s inevitable that practicalities can sometimes see the timetable forgotten or ignored. For reasons of resources and timing, often an asset will be lubricated only monthly, or during scheduled maintenance, or when the asset isn’t running – or not at all. An asset with a lubrication point that’s difficult or dangerous to access may actually be overlooked more often than it’s oiled or greased.
And all the time an engineer spends making lubrication rounds is time not spent carrying out other tasks which could improve efficiency, further enhance reliability, or reduce costs. ERIKS’ inspection of the distillery’s mechanical assets identified all these kinds of problems. But it also identified the most critical applications, and enabled ERIKS to propose a more efficient lubrication solution.
A lubrication expert for every asset
Lubrication done properly is a skill. Not too much grease, not too little, at just the right time and in just the right place. For a busy maintenance engineer, it’s one more job they may lack the time to carry out to the necessary standard.
But it’s possible to assign a ‘lubrication expert’ to the lubrication points of every critical asset, to ensure optimum lubrication for peak performance, maximum reliability and a longer service life.
The simalube automatic lubricator is that lubrication expert: a staggeringly simple solution which replaces lubrication by luck with the perfect lubrication regime.
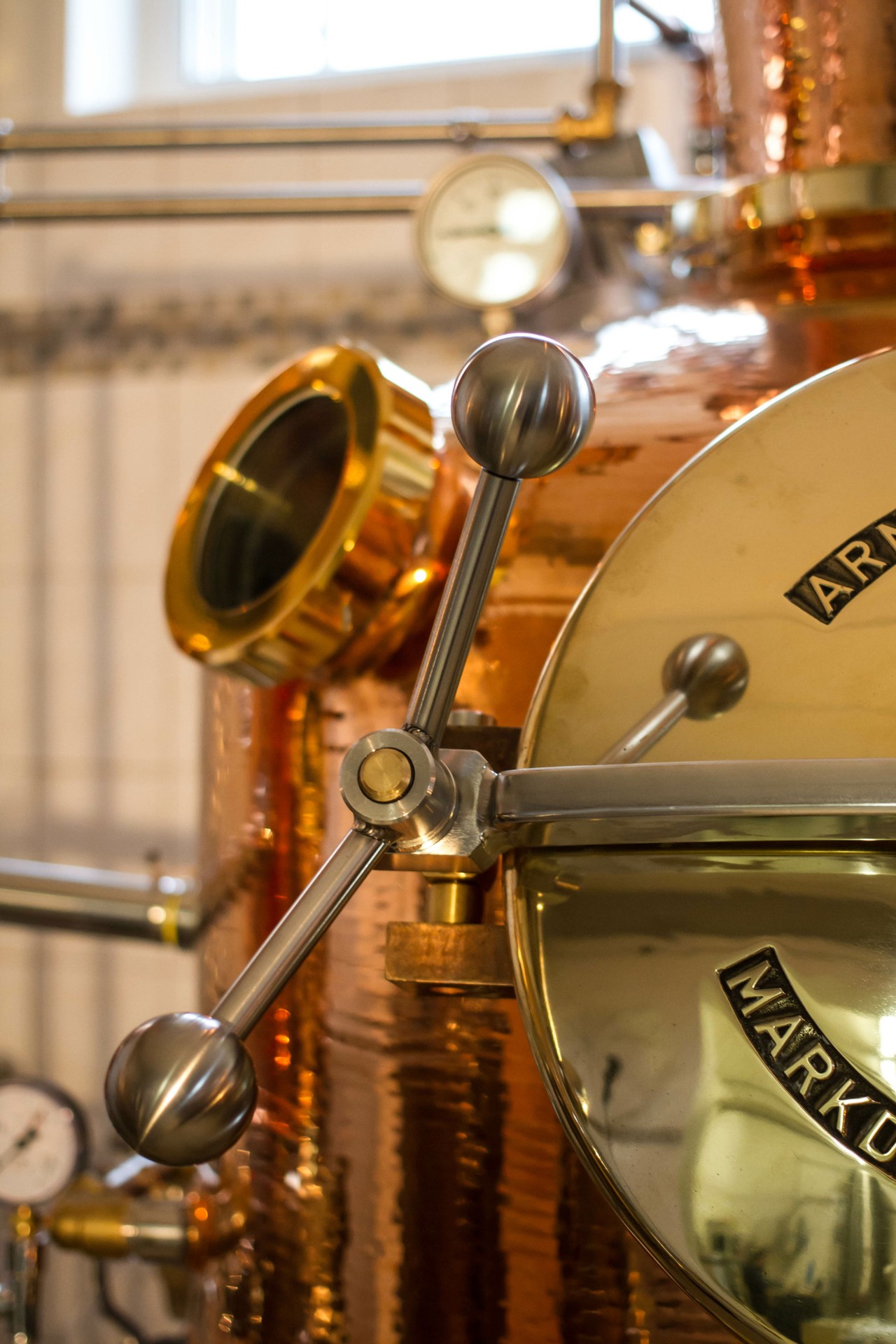
Quickly and easily fitted to the grease line of the asset – even if the machine is running – the simalube lubricator can be set to dispense grease for 3, 6, 9, or 12 months before it needs checking and refilling if necessary. So fit and forget – for up to a year.
Lubrication on demand
A simalube lubricator never dispenses too much grease, or too little. That’s because grease is effectively drawn down from the lubricant reservoir only as the asset consumes the grease already supplied.
As a result, lubricant costs can be reduced by as much as 30%.
At the same time, asset reliability is increased because the equipment is always optimally lubricated. Maintenance costs are reduced as the risk of breakdown is reduced. And maintenance engineers, released from regular lubrication rounds, are free to focus on more productive tasks.
Automatic lubrication with simalube can also improve site safety. At the distillery, for example, some lubrication points on top of silos and stills are the equivalent of 20 storeys above ground. Gaining access annually to refill the grease reservoir is obviously safer than lubricating every month.
Matured to perfection
Following the lubrication survey, ERIKS spent a day and a half installing simalube automatic lubricators on all the distillery’s critical assets. Now, three years on, the only requirement is to refill the reservoirs every November. To be classified as ‘Scotch’, a whisky has to be matured in oak casks for a minimum of three years.
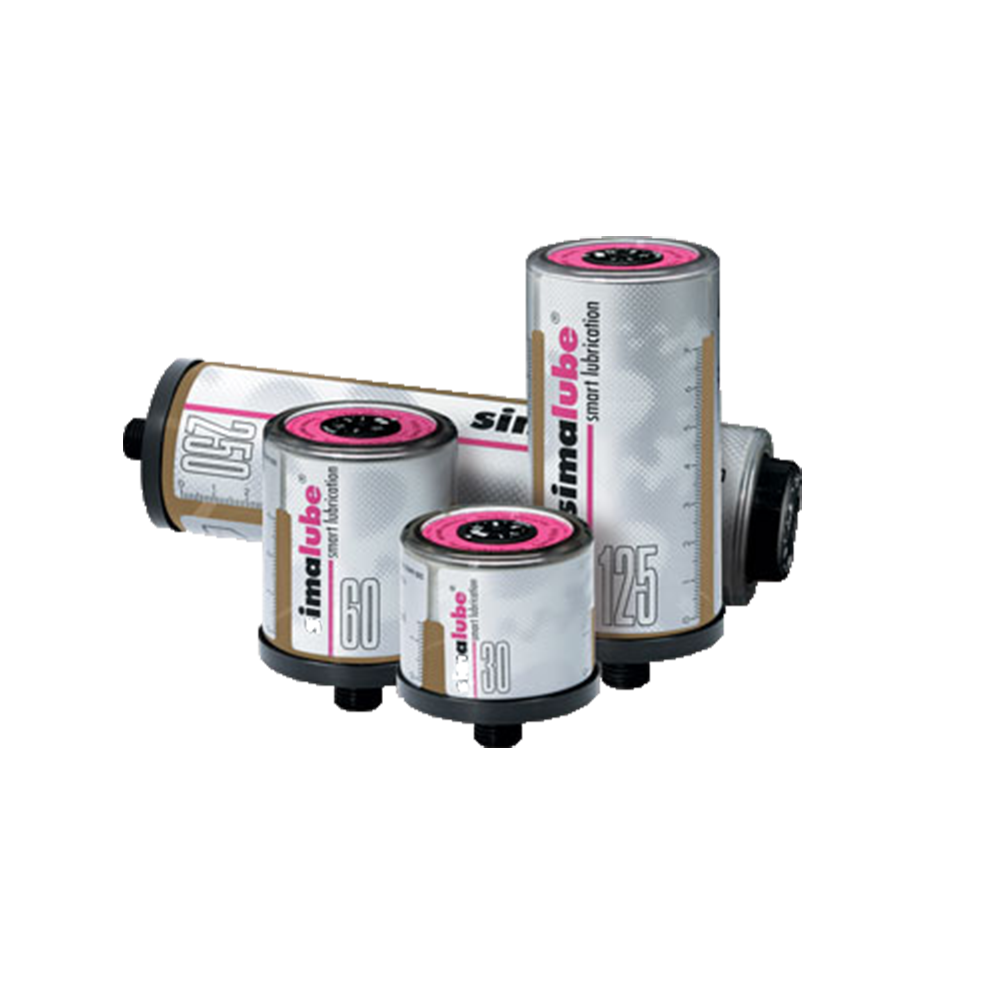
So some of the spirit distilled when ERIKS first carried out its lubrication survey is now ready to bottle. It would be the ideal drink to celebrate more reliable and more effective lubrication throughout the customer’s site.
For more information on Lubrication solutions and to get in touch with one of our ERIKS Specialists, please contact your local ERIKS Service Centre, who will be happy to discuss your options.
#Simalube #ERIKS #LetsMakeIndustryWorkBetter #Lubrication #Innovation #Distillery #Whisky