In this article
Energy savings are the cat's whiskers
New energy-efficient motor leaves engineers purring
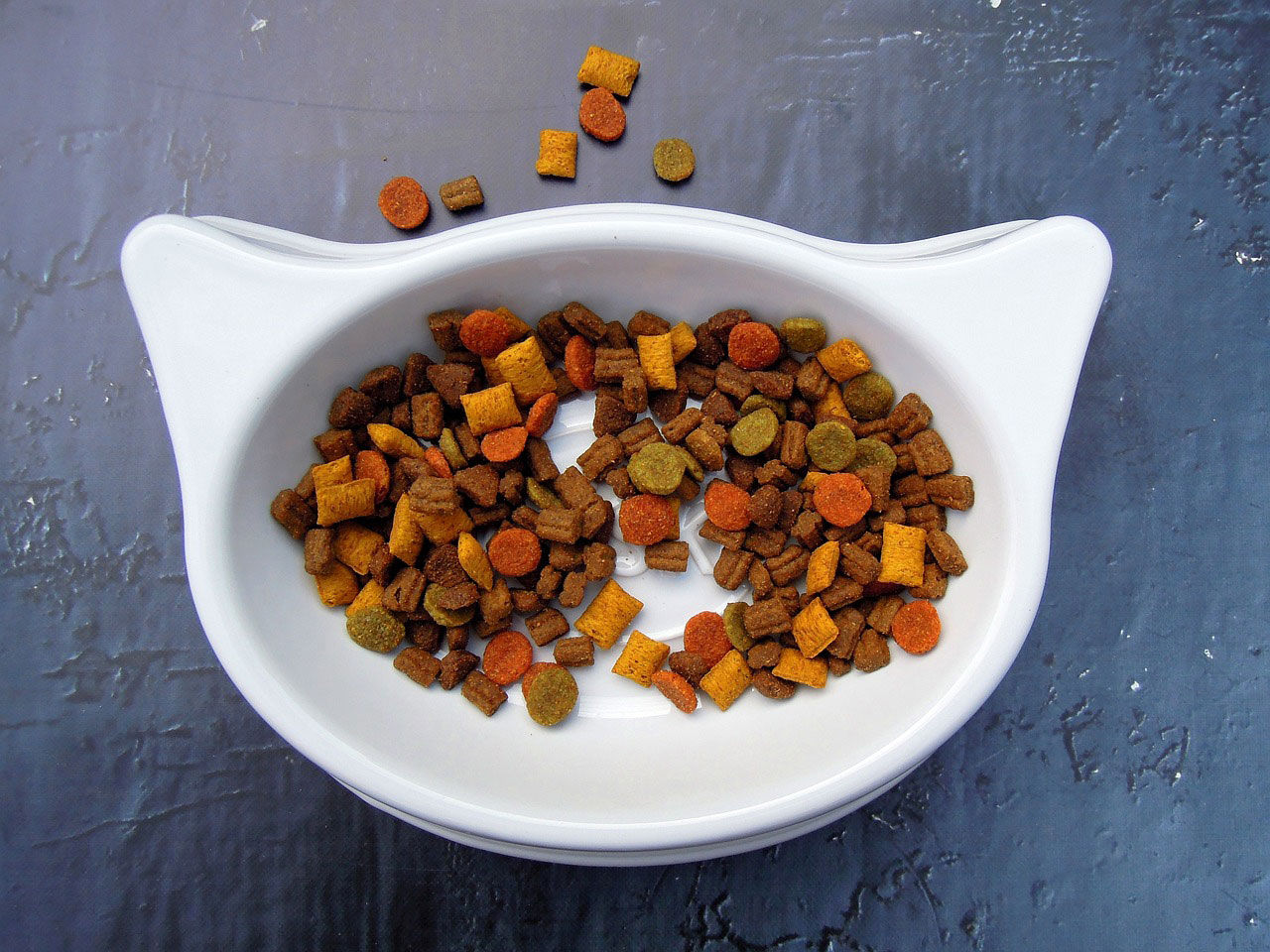
Industry Sector:
Food & Beverage
Application:
Emulsifier
Actual Saving:
£12,492 p.a.
Payback period:
2 Years

Product/Service:
- IE5 Motor
Customer Benefits:
- Cost saving
- Energy efficiency
- Seamless integration
- Environmental compliance
For a major manufacturer of cat foods, optimising production doesn’t just mean developing new recipes to keep Kitty happy. It also means a continual evaluation of processes and an ongoing assessment of efficiency, emissions and productivity, to identify opportunities for improvement.
It was during one of these regular reviews that the manufacturer’s engineers recognised the potential to increase the energy efficiency of a number of motors.
After the customer approached WEG – our motors partner – with their initial enquiry, WEG in turn approached ERIKS. A joint site visit was arranged to ensure the solutions proposed didn’t leave the customer having kittens.
Challenge
The customer operates 260kW IE2 motors to power emulsifiers, which are part of the pet food production process. IE2 is the second-lowest energy efficiency rating for electric motors, so there was a clear opportunity to upgrade to newer and more energy-efficient motor technology.
The customer’s target for the upgrade of a single motor was a 5% energy saving, producing a return on investment in 5 years. Although the customer wanted to upgrade the motor to a more efficient option, they still wanted to retain the 250W motor rating, to maintain the same frame size and footprint. In addition, the customer operates Rockwell drives as standard throughout the business, so the ideal motor solution would need to be completely compatible with the existing drives, to maintain standardisation and reduce installation costs.
In this particular application, there is the potential for heat transfer from the emulsifier, so any motor proposed needs to be able to cope with high temperatures. And there are regular high-pressure washdowns using aggressive cleaning chemicals, so the motor casing needs to be resistant to these.
Solution
A site visit by engineers from WEG – specialising in energy-saving motors technology – and ERIKS – providing unparalleled application know-how – produced a choice of two alternative solutions. After careful consideration, the customer chose the option of a WEG 260kW IE5 permanent magnet 6-pole motor, operating at 75Hz.
This integrates seamlessly with the current drive system, and matches the existing motor’s frame size and footprint. The permanent magnet technology also allows for the removal of the inverter from the configuration.
To meet the specific demands of the operating environment, the WEG motor bearings were filled with high-temperature grease, to resist any lubricant failure due to heat transference from the emulsifier. And the motor casing was treated with a special paint to resist high-pressure cleaning and aggressive chemicals.
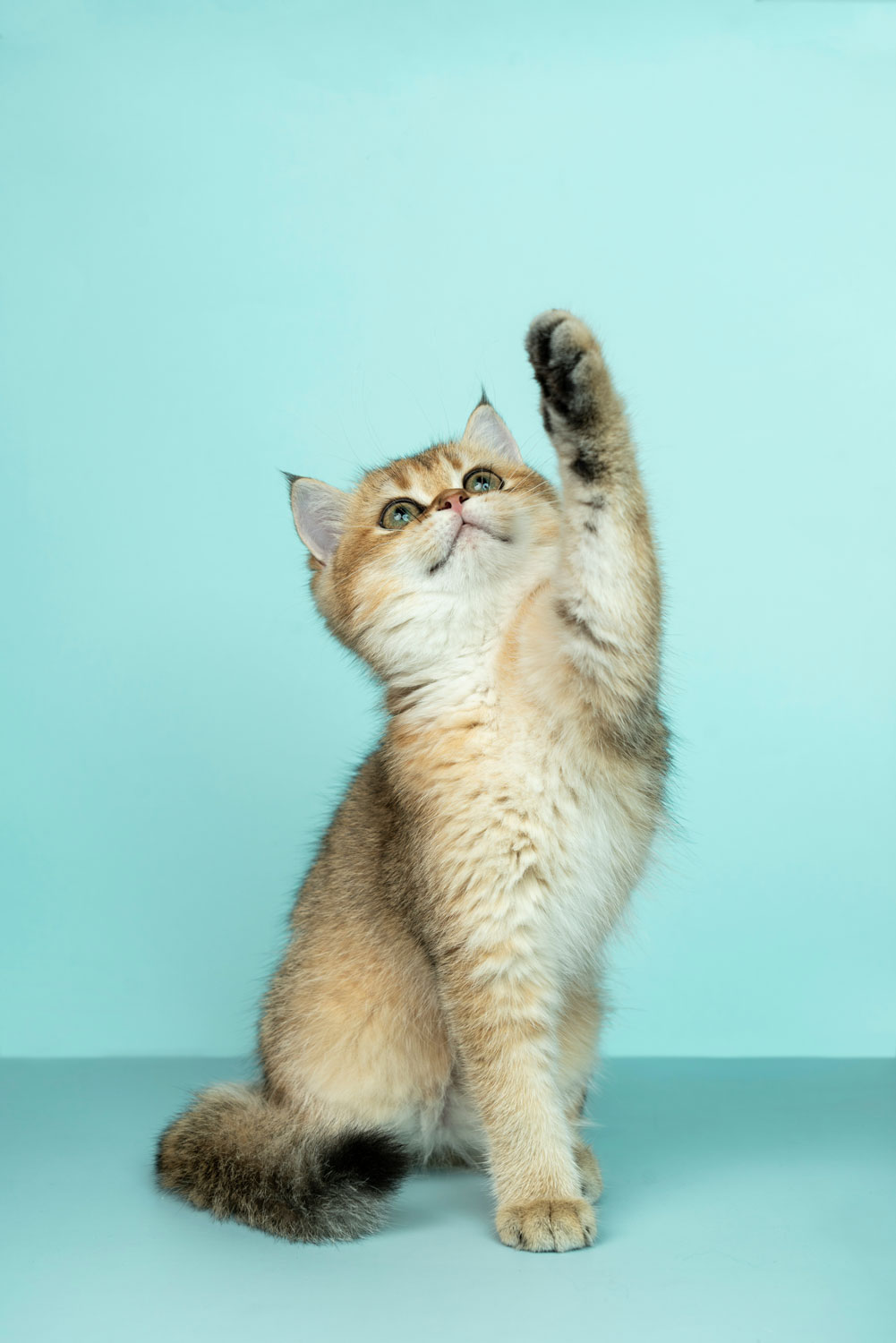
Cat pleading to be fed
Result
The customer had targeted a 5% energy-saving with a 5-year payback period. The ERIKS/WEG solution did even better. In fact, the energy-saving achieved is 8-9%. And with energy cost savings calculated by the customer at £12,492 p.a., payback will be achieved in just 2 years.
A competitor’s proposal would have required a complete change to the drive system to accommodate the new motor. By contrast, the new, higher-efficiency WEG motor integrated seamlessly with the customer’s existing drive system – meaning no additional installation costs.
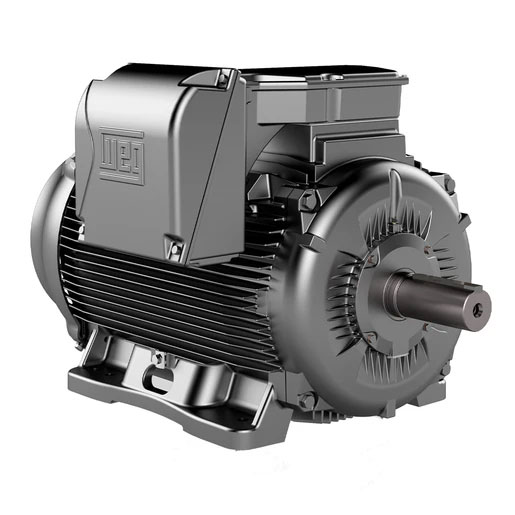
WEG IE5 Motor
As a major global manufacturer of pet foods, the customer has five more IE2 motors operating emulsifiers at the same UK site, and a total of 80 for the same application worldwide. Replacing them all with higher-efficiency IE5 WEG motors could leave their engineers grinning like a cheshire cat.