In this article
Ultrasonic Cleaning eliminates the ‘strain’
Performance and efficiency through innovation
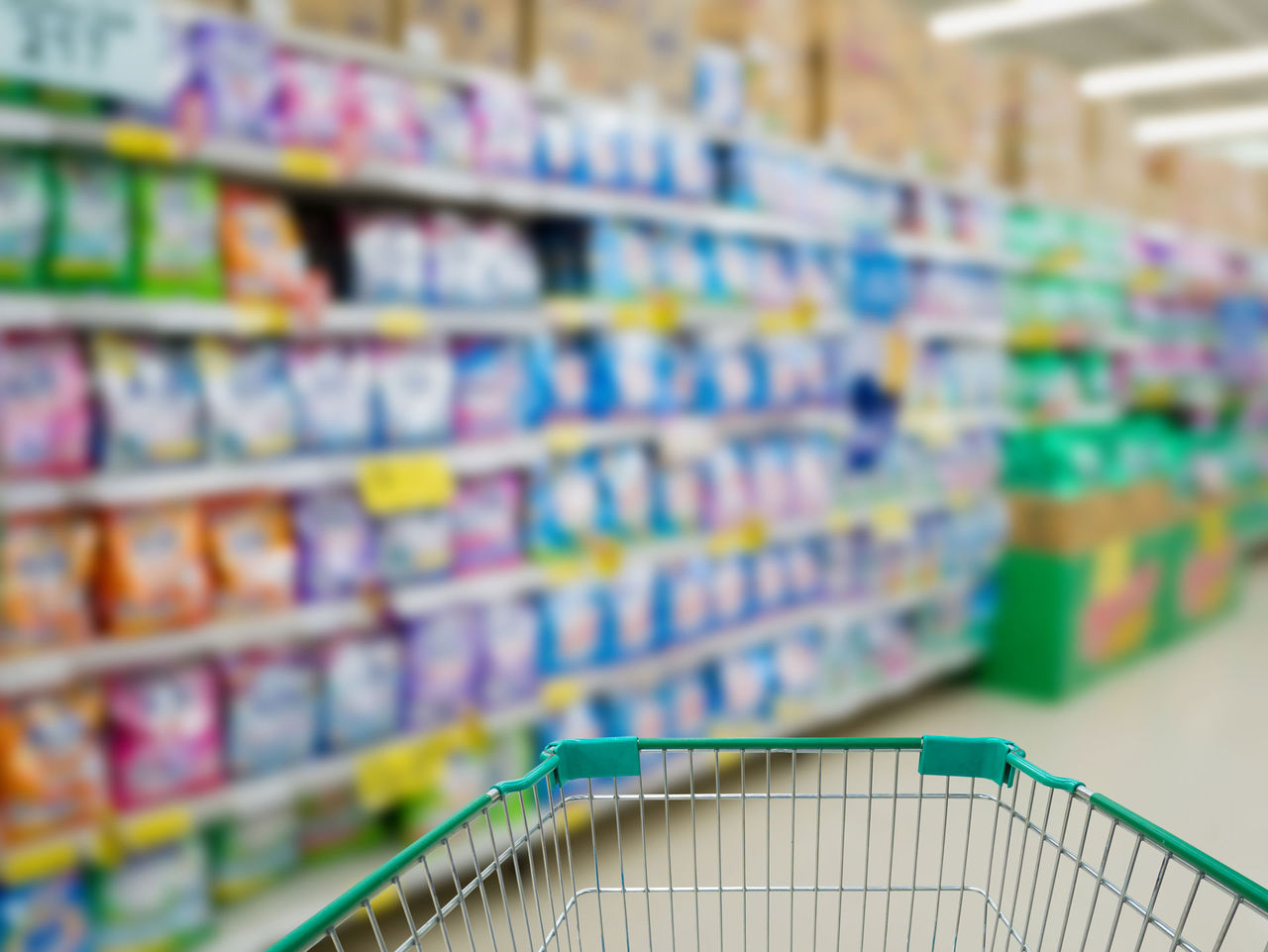
Industry Sector:
Consumer Goods
Application:
Falling Film Reactor
Actual Saving:
£64,989
Payback period:
Immediate Saving
Product/Service:
- Ultrasonic cleaning
- Industrial consumables
Customer Benefits:
- Increased productivity
- Reduced downtime
- Sustainable solution
- Faster maintenance and cleaning schedules
We all know that a clogged air filter under your car’s bonnet can zap performance, it can no longer keep out dirt and contaminants, crippling your fuel efficiency, and it can even damage your engine and its components.
Now translate that clogged filter to a production environment. A decrease in performance means losses in efficiency and productivity, possibly leading to product contamination, all of which hits your bottom line. After all, it’s not as if you can ignore it for a couple of weeks as we often do with our cars.
Challenge
The site Engineering Team of a large consumer goods manufacturer were experiencing ongoing issues with the stainless steel strainers on the falling film reactor, which plays a pivotal role throughout the filtration process in removing contaminants from the system. Sulphur passes through each strainer at a temperature of 150°C resulting inevitably in each strainer over time becoming clogged.
Requiring changing on a weekly basis and with a current lead time of 10 days this was becoming problematic for the customer. Frequent costs and ever increasing lead times on an integral component were simply not sustainable or cost-effective. A more practical solution to avoid contamination was required to reduce spares and maintenance revenue.
Solution
The ERIKS On-Site Team set to work investigating all available solutions to improve reliability and performance. Following consultation a decision was reached to invest in an Ultrasonic cleaning solution from (Sonic Solutions).
The Ultrasonic Cleaning process uses both liquid and high-frequency waves to remove even the toughest of contaminants, in this case the build up of sulphur. This simple switch would save the customer over £64k, eliminate timing waiting for components, ultimately speeding up maintenance and reducing downtime.
Furthermore, upon hearing of the Ultrasonic cleaning success other production departments within the customer infrastructure have contacted the ERIKS team for units to be installed in their areas so they too could ‘clean up’ productivity.
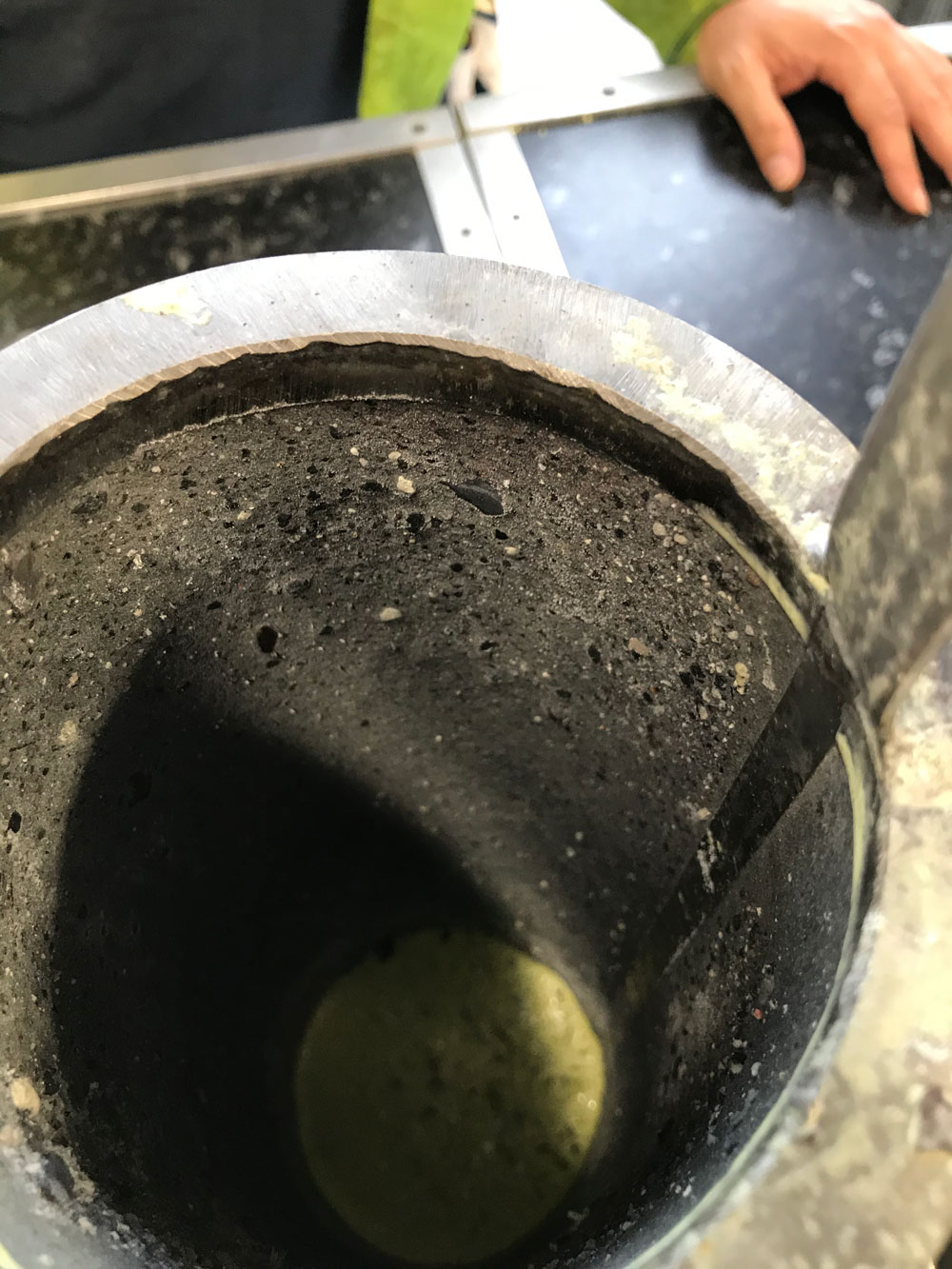
Strainer before Ultrasonic Cleaning process
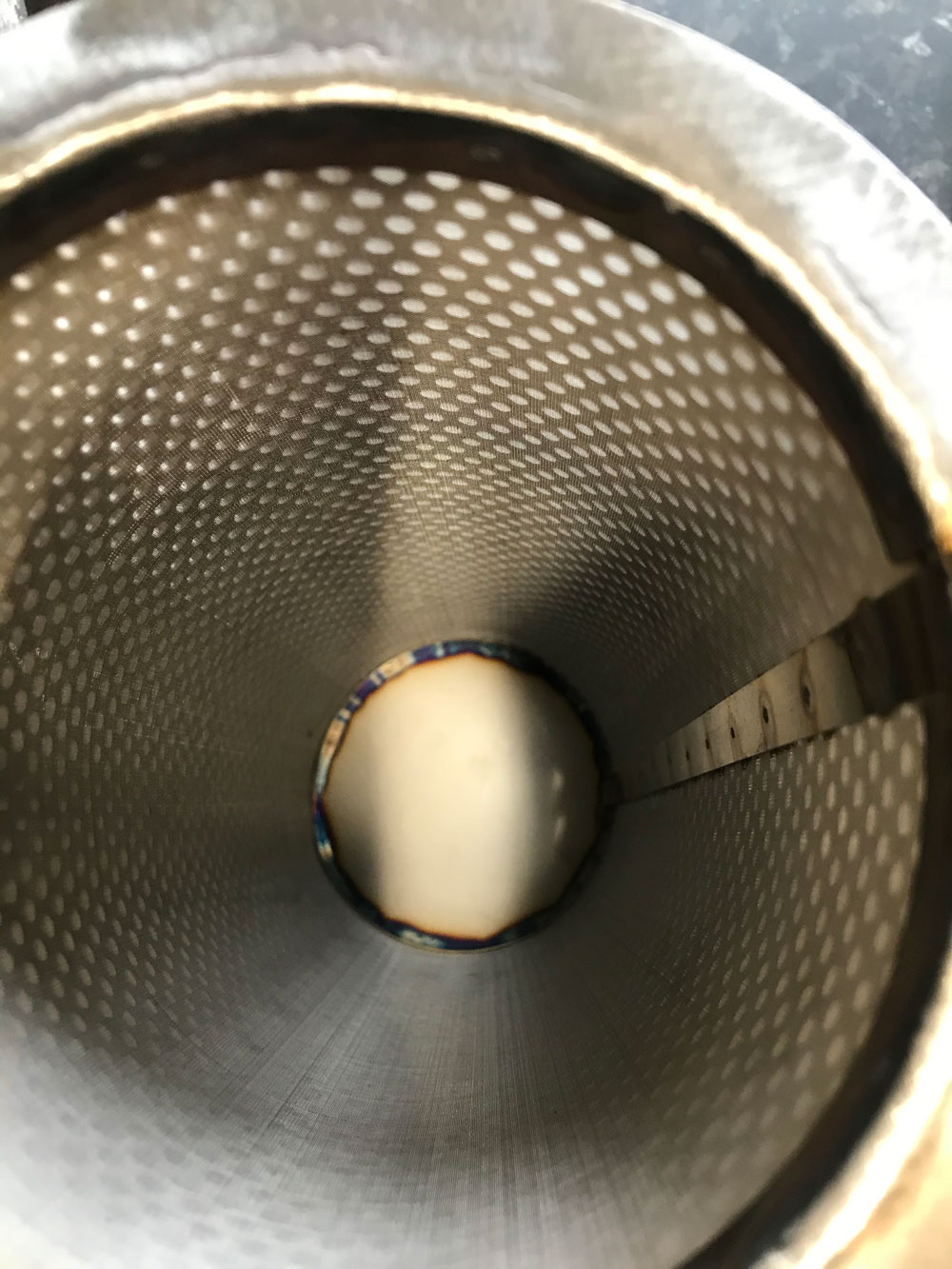