In this article
Taking Control of Leaking Valves with Spira-trol™
Reducing food safety risks and extending life
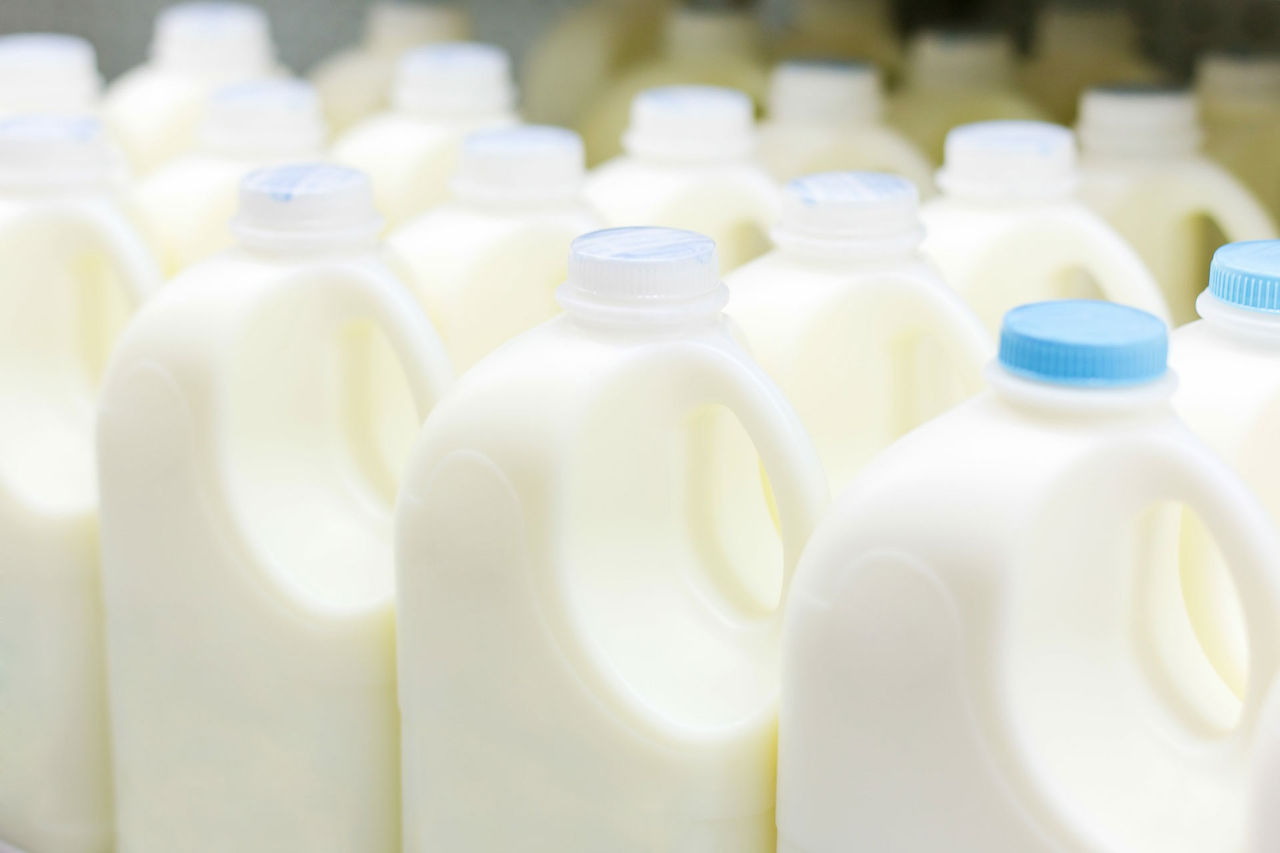
Industry Sector:
Food & Beverage
Application:
Heat exchange system
Actual Saving:
£50,000
Payback period:
1 year
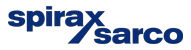
Product/Service:
- Control valve upgrade
- Re-engineering
- Application support
Customer Benefits:
- Improved process efficiency
- Reduced maintenance costs
- Increased uptime
Leaking control valves were leaving a dairy product manufacturer feeling pretty cheesed off. The control valves in question were part of a tubular heat exchange system, and had become worn over time. Because they were failing to close securely, there were knock-on effects on the system’s efficiency.
Without effective and reliable closure, the heat exchange system tended to operate outside its set parameters, and water hammer was also occurring.
Challenge
The customer’s idea was to install more valves: this time, actuated ball valves in front of the control valves. This would have helped the control valves to shut-off tightly, but it would also require reworked pipework to enable, additional control signals and also mean an increase in compressed air consumption. In this case more valves also meant more problems and more energy consumption.
Instead of trying to rectify the problem with the existing control valves, ERIKS recommended replacing them with a completely different type of valve: the Spira-trol™ valve with a soft seat.
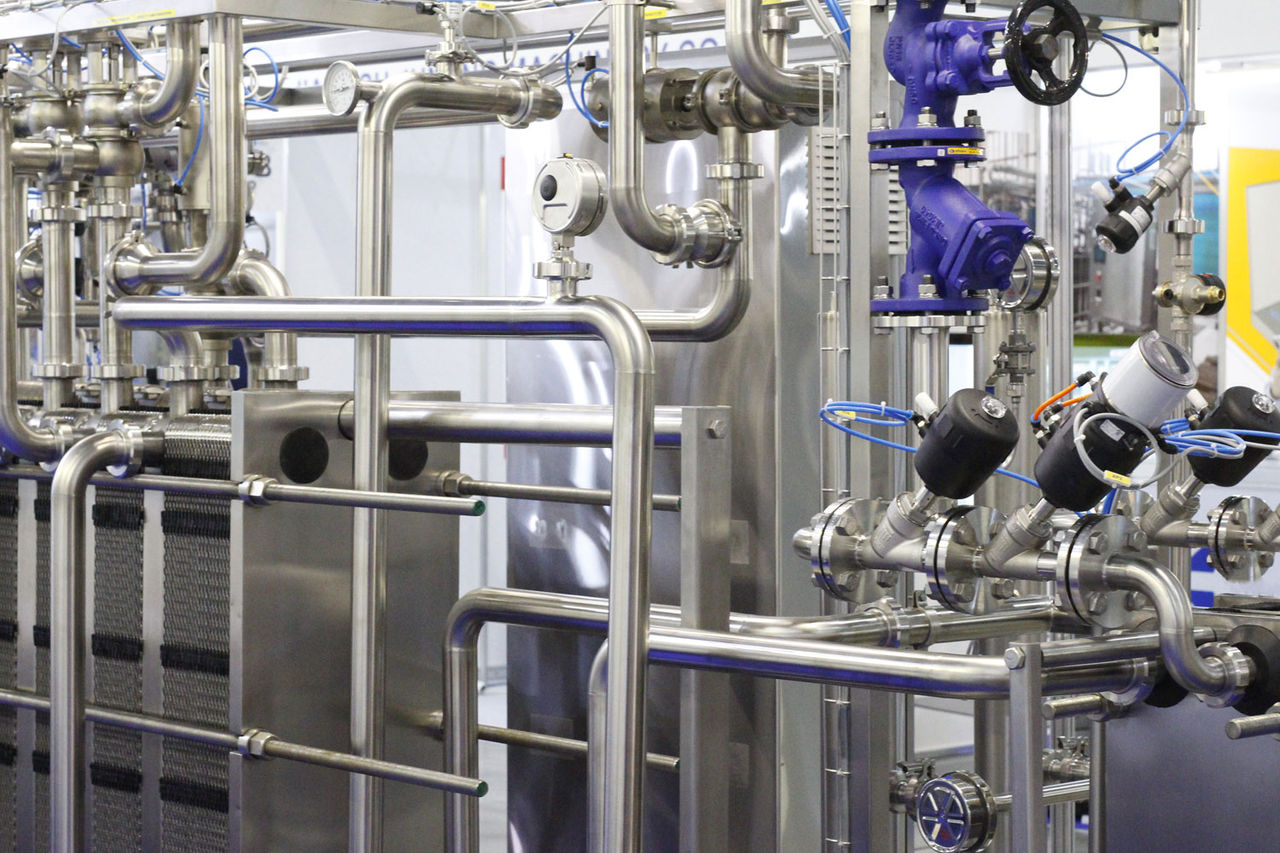
Dairy rubular heat exchanger
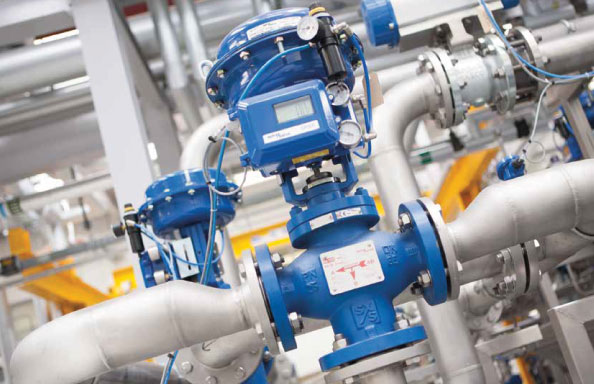
The Spira-trol™ valve from Spirax Sarco
Solution
The Spira-trol™ valve is part of a range of 2-port single seat globe valves with cage retained seats. Engineered to a highly flexible modular design, they are designed for steam and other industrial fluids, and can easily be adapted to most process requirements. Once installed, commissioned and set, they can be safely left to get on with the job, with minimum maintenance.
By replacing the worn control valves with the Spira-trol™ valve with a soft seat, the customer would not only have valves with modulating capability, but also a watertight closure with no leaks. Initially, the Spira-trol™ valves were installed at the two most critical points in the customer’s process, with a thermographic camera to monitor their operation.
Result
After nine months of monitoring, the valves were still showing no signs of leakage. The customer was so impressed they installed eight more Spira-trol™ valves, replacing the modulating valves that had caused so many problems. This solution offered a significant reduction in downtime and maintenance costs, along with improved process efficiency and reduced energy costs, and realised an actual cost saving of £50,000.